Schrumpfung. Der Fluch des Lebens eines jeden Spritzgießers.
Sie entwerfen ein Teil mit perfekten Abmessungen. Programmieren Sie die Formmaschine entsprechend. Führen Sie einige Muster durch. Und dann - bumm - kommen die Teile mit Untermaß heraus.
Nicht das Ende der Welt. Aber niemand mag Überraschungen... vor allem, wenn es um hochpräzise Teile geht.
Die gute Nachricht? Die Schrumpfung muss Ihnen nicht den Tag verderben. Mit etwas Planung und Fingerspitzengefühl lässt sich das Problem in den Griff bekommen.
Als Fachmann Kunststoff-Spritzguss Ich zeige Ihnen, wie Sie die Schrumpfung unter Kontrolle bekommen, damit Sie Teile nach genauen Spezifikationen formen können.
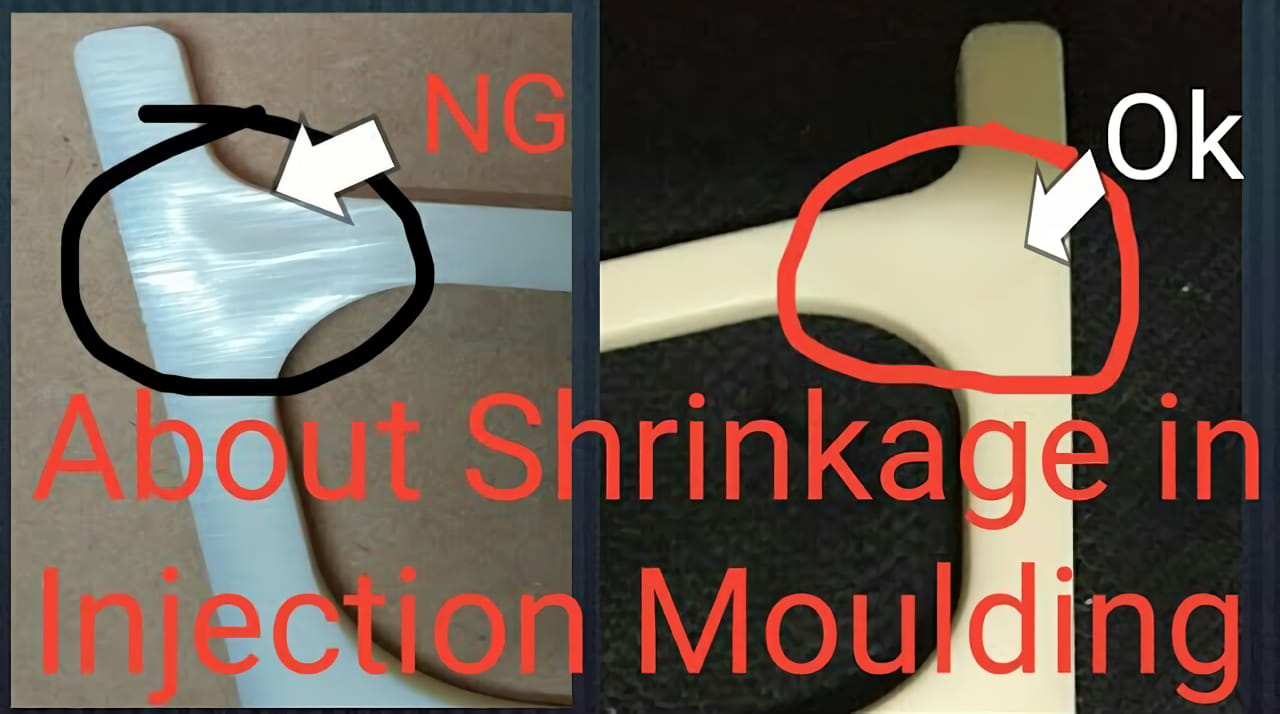
Was verursacht die Schwindung beim Spritzgießen?
Bevor wir Lösungen in Angriff nehmen, müssen wir verstehen, was das Problem überhaupt verursacht.
Alle Kunststoffe schrumpfen beim Abkühlen von geschmolzenem Glibber zu festen Teilen. Je heißer der Kunststoff ist, desto mehr dehnen sich die Polymerketten aus. Wenn die Dinge abkühlen, setzt die thermische Kontraktion ein. (Sie wissen schon: "Heiße Luft steigt auf", wie Sie es aus dem Naturkundeunterricht in der Grundschule kennen).
Das Ausmaß der Schrumpfung hängt von einigen Faktoren ab:
- Material: Amorphe Harze wie ABS neigen dazu, stärker zu schrumpfen als kristalline Harze wie Nylon. Und warum? Die Polymerketten in amorphen Materialien sind nicht so dicht gepackt, so dass sie beim Abkühlen mehr Platz zum Zusammenziehen haben.
- Formenbau: Dickere Teile oder Teile mit ungleichmäßigen Wandstärken neigen zu ungleichmäßiger Schrumpfung. Die dickeren Bereiche kühlen langsamer ab - und schrumpfen daher langsamer - als dünnere Abschnitte.
- Verarbeitungsbedingungen: Hohe Einspritzgeschwindigkeiten gepaart mit niedrigem Nachdruck führen dazu, dass sich das Material im Formhohlraum nur locker zusammenfügt. Dies ermöglicht eine größere Schwindung beim Abkühlen.
Da wir nun wissen, warum Schrumpfung auftritt, sollten wir darüber sprechen, wie man sie verhindern kann.
Wie lässt sich die Schwindung beim Spritzgießen reduzieren?
Um die Schrumpfung in den Griff zu bekommen, gibt es drei Hauptansätze:
- Optimieren Sie Ihren Formenbau
- Wählen Sie das richtige Material
- Passen Sie Ihre Prozessparameter an
Schauen wir uns diese an.
1. Optimieren Sie Ihr Formdesign
Wenn es nach dem Willen der Werkzeugmaschine ginge, würde jedes Teil in allen Abschnitten mit der exakt gleichen Geschwindigkeit abkühlen. Keine ungleichmäßige Abkühlung = keine ungleichmäßige Schrumpfung oder Verzug.
Aber wir leben nicht in einer perfekten Welt. Und eine völlig gleichmäßige Kühlung über komplexe 3D-Geometrien hinweg ist leichter gesagt als getan.
Dennoch können wir einige Designstrategien anwenden, um dem Ziel so nahe wie möglich zu kommen:
- Abrupte Änderungen der Wanddicke werden vermieden: Versuchen Sie, den Übergang zwischen dünnen und dicken Abschnitten allmählich zu gestalten (Filets sind hier Ihre Freunde). Dies hilft, "heiße Stellen" zu vermeiden und eine ungleichmäßige Schrumpfung zu minimieren.
- Achten Sie auf die Ecken: Scharfe Ecken wirken als Spannungskonzentratoren und verstärken die Materialschrumpfung. Abgerundete Ecken verteilen die Spannung gleichmäßiger.
- Strategische Platzierung der Rippen: Rippen und Zwickel verstärken Teile, ohne die Wandstärke wesentlich zu verändern. Achten Sie jedoch darauf, keine neuen heißen Stellen zu schaffen.
- Wählen Sie Ihre Gates ein: Die Platzierung des Anschnitts bestimmt, wie das Material in die Form fließt. Achten Sie darauf, dass sich die Form schön gleichmäßig füllt. Keine Schwachstellen, an denen sich das Material nicht vollständig füllen kann.
Profi-Tipp: Mit einer Simulationssoftware können Sie die Temperaturverteilung und die Schwindung vor dem Schneiden des Stahls vorhersehen. Auf diese Weise können Sie den Formenentwurf digital optimieren, anstatt ihn durch kostspieliges Ausprobieren in der Produktion zu verändern.
2. Wählen Sie das richtige Material
Wenn extreme Maßgenauigkeit erforderlich ist, sollten Sie mit dem richtigen Rohmaterial beginnen.
Es gibt einige Dinge zu beachten, wenn es um Schrumpfung geht:
- Amorphe vs. kristalline Harze: Wie bereits erwähnt, sind amorphe Materialien wie ABS oder Polycarbonat (PC) neigen dazu, stärker zu schrumpfen als kristalline Harze. Acetal und Nylon sind die bessere Wahl, wenn die Schrumpfung begrenzt werden soll.
- Verstärkte Kunststoffe: Die Zugabe von Glasfasern, Kohlefasern oder Talkum in die Materialmischung erhöht die Formstabilität. Der Nachteil ist, dass diese Füllstoffe oder Verstärkungen den Kunststoff zähflüssiger machen können, was zu Problemen beim Formen führen kann.
- Kennen Sie Ihre PVT-Daten: Jeder Materiallieferant stellt detaillierte Informationen über die Schrumpfungseigenschaften seines Harzes in verschiedenen Temperatur- und Druckbereichen zur Verfügung (PVT-Daten). Prüfen Sie diese Informationen, um die beste Option auszuwählen.
Unterm Strich: Arbeiten Sie mit Ihrem Materiallieferanten zusammen, um das Harz auszuwählen, das sowohl die Anwendungsanforderungen erfüllt als auch eine minimale Schrumpfung aufweist.
3. Verfeinern Sie diese Prozessparameter
Und nicht zuletzt sollten Sie die Flexibilität von Spritzgießmaschinen nutzen, um den Gießprozess selbst zu verfeinern.
Das Ziel ist es, so viel Material wie möglich in die Form zu packen, BEVOR die Dinge zu erstarren beginnen. Dadurch bleibt weniger Platz für die natürliche Schrumpfung, die beim Abkühlen auftritt.
Hier sind einige Prozessoptimierungen, die einen Versuch wert sind:
- Drehen Sie den Druck auf: Durch die Anwendung eines höheren Einspritzdrucks werden die Polymerketten enger zusammengedrückt. Das Erhöhen des Pack- und Nachdrucks wirkt der Schrumpfung nach der ersten Injektion entgegen, indem die Moleküle noch stärker verdichtet werden.
- Verlangsamen Sie die Befüllung: Schnelle Füllraten können Schwachstellen im Materialprofil hinterlassen. Durch die Verringerung der Einspritzgeschwindigkeit wird das Material dichter zusammengefügt.
- Verlängern Sie die Kühlzeit: Ich weiß, ich weiß... längere Zykluszeiten beeinträchtigen die Produktivität. Aber wenn man die Teile vor dem Auswerfen vollständig abkühlen lässt, wird vermieden, dass sie in einem "erstarrten, aber noch schrumpfenden" Zustand entnommen werden.
Profi-Tipp: Erhöhen Sie den Druck nicht von Anfang an in den Himmel. Beginnen Sie konservativ und erhöhen Sie den Druck schrittweise, während Sie die Qualität der Teile beurteilen. Ein zu hoher Druck kann auch Probleme wie Einfallstellen, Lücken oder Grate verursachen.
Wie viel "Übergröße" für Schrumpfung?
Jetzt kommt der Moment der Wahrheit.
Um all diese Erkenntnisse in die Praxis umzusetzen, ist letztlich ein weiterer Schritt erforderlich - die Kompensation der Schwindung durch eine absichtliche Überdimensionierung des Formnests.
Aber um wie viel?
Wie immer gibt es keine festen und schnellen Regeln. Die Schrumpfung hängt von allen oben genannten Faktoren ab. Die beste Antwort erhalten Sie, wenn Sie Muster herstellen, die Ihre Produktionsform bzw. Ihren Produktionsprozess so genau wie möglich nachbilden.
Hier sind jedoch einige Richtwerte für die Überdimensionierung, je nachdem, mit welchem Harz Sie arbeiten:
- Polyethylen (PE): 2-5%
- Polypropylen (PP): 1.5-3%
- Acrylnitril-Butadien-Styrol (ABS): 2-4%
- Nylon: 2-4%
Diese Prozentsätze müssen durch Stichproben validiert werden, aber sie sind ein guter Ausgangspunkt für die anfängliche Dimensionierung der Form.
Der Schlüssel liegt darin, die Abmessungen von dort aus auf der Grundlage realer Messdaten von Formteilen zu optimieren. Es ist eine gewisse iterative Optimierung erforderlich, aber es lohnt sich, das exakte Aufmaß zu finden, das für die Herstellung maßgenauer, formstabiler Teile erforderlich ist.
Niemand hat behauptet, Spritzgießen sei einfach! Aber mit ein wenig Wissen und einer strategischen Prozessoptimierung lässt sich die Schrumpfung auf ein Minimum reduzieren.
Und wenn dann das schöne Teil aus der Form kommt, hat sich alles gelohnt!