Was ist medizinisches Spritzgießen?
Medical injection molding is the manufacturing process of producing plastic medical devices and components by injecting molten plastic material into a mold. It enables the mass production of sterile, precise parts for various medical applications while meeting rigorous industry standards.
As technology continues advancing in the medical field, manufacturers utilize innovative techniques like injection molding to create complex devices that save lives. The precision offered by this automated process allows the production of intricately designed, flawlessly fabricated components that play critical roles in surgical procedures, implants, diagnostics, and more.
So how exactly does medizinisches Spritzgießen work? What materials and techniques are used? Let’s explore the intricate world of this transformative manufacturing process.
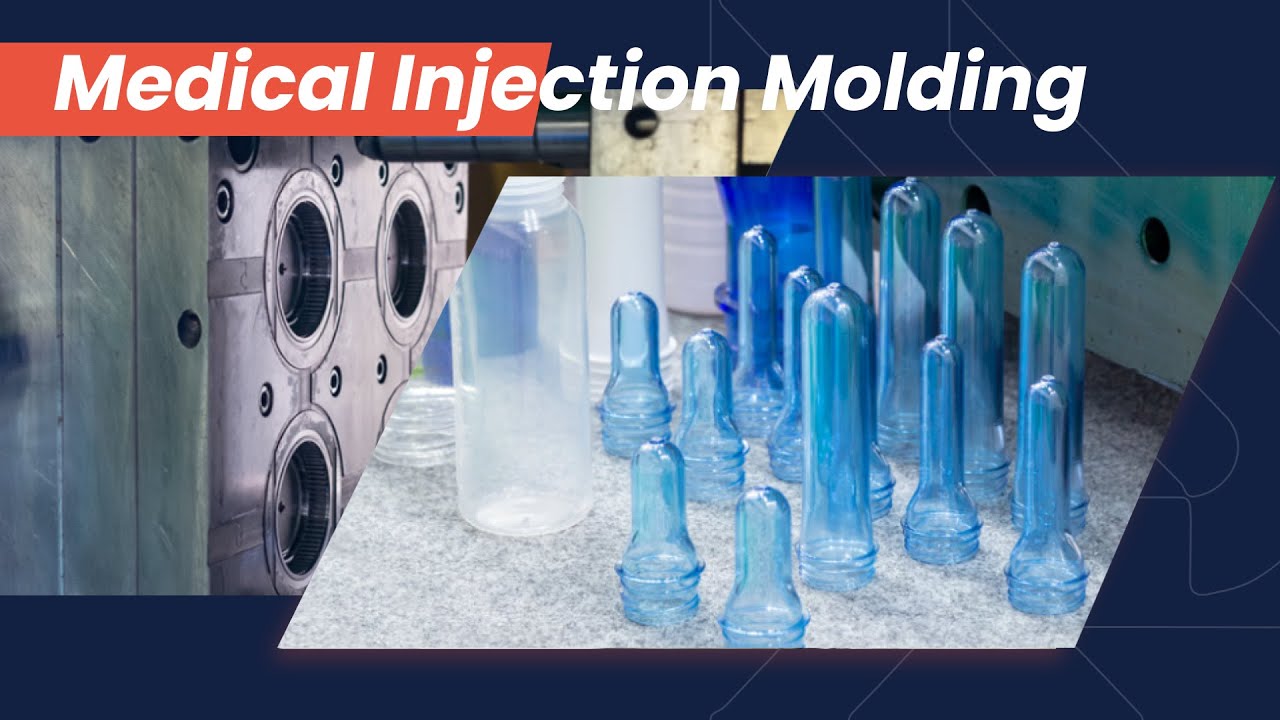
An Overview of Injection Molding for Medical Applications
Injection molding has been utilized for decades to mass produce everyday plastic items you likely use regularly – things like electronics cases, bottle caps, toys, household items, and more. This efficient, precise, and cost-effective manufacturing technique came about in the 1930s and continues evolving alongside technology.
The basic concept of injection molding applies to medical applications too. Plastic pellets are gravity fed from a hopper into the injection molding machine’s heated barrel. The pellets are heated to approximately 600°F, causing them to melt into a liquid state. This molten material then gets injected under intense pressure into a steel mold. The pressure packs the plastic into every crevice of the mold, which is cooled by water, allowing the plastic to solidify into the finished part.
The basics seem simple, but medical injection molding requires incredibly complex precision-built machines and tooling. Producing intricate medical components with tight tolerances is no easy feat.
Let’s look closer at the materials, design considerations, and specialty techniques used to create flawlessly fabricated medical devices via injection molding.
Medical-Grade Plastics for Injection Molding
Various plastic polymers get used for medical injection molding parts and devices. But not just any plastic works for biocompatible applications in the human body. Medical device manufacturers must use plastic resins that meet biocompatibility and FDA regulations.
Common Medical-Grade Plastic Polymers
- Polypropylen (PP) – Used for medical packaging, components, syringes, instruments, IV connectors, and more. Offers high strength, flexibility, and the ability to withstand repeat autoclave sterilization.
- Polyethylen (PE) – Available as low, medium, or ultra-high density material. Used for medical containers, breathing masks, RFID tags, wearable devices, and orthopedic implants. Offers chemical resistance and flexibility.
- Polystyrol (PS) – Primarily used for Petri dishes, vials, trays, diagnostic instrument housings. Provides dimensional stability and shock resistance.
- Polycarbonat (PC) – Exceptional strength yet transparent optical clarity. Used for intubation tubes, thermometers, surgical instruments, medical cases.
- Polyetheretherketone (PEEK) – An engineering thermoplastic offering incredible strength, temperature, and chemical resistance. Allows for repeated sterilization. Used in spinal, orthopedic, and dental implants and devices.
Additional specialized medical polymers continue emerging, like color-stable nylon 6-6, antibacterial TPU filament, and more. But the polymers above cover about 90% of current applications.
Design Considerations for Medical Injection Molding
Several critical design considerations go into manufacturing flawless medical components via injection molding, including:
- Präzision – Medical components often have incredibly tight tolerances, sometimes within a couple thousandths of an inch. This level of precision ensures proper device assembly and performance.
- Cleanliness – Medical parts must not shed particulates into the body, as this contamination risks infection or complications. Proper injection molding machine setup prevents this.
- Biocompatibility – Only FDA-approved medical-grade polymers should get molded for device applications. The plastics must not leach harmful chemicals when interacting with the body’s tissues and fluids.
- Sterilization – Most components need sterilization prior to use, usually via an autoclave machine, gamma irradiation, or ethylene oxide gas. The polymer choice must withstand the sterilization approach without degrading.
Considering these design factors early when planning injection molded medical components reduces production issues down the road.
Advanced Injection Molding Techniques for Medical Applications
While basic injection molding suits many medical parts, certain applications call for additional solutions:
Einsatzformteil
Insert molding marries multiple materials by first molding a component, then placing it into another mold so an additional material gets molded over or around it. The final product becomes a single bonded piece.
Common examples include:
- Needle hubs with formed metal cannulas
- Plastic handles overmolded onto surgical grade steel instruments
This technique improves ergonomics and allows combining materials for increased functionality.
Umspritzen
Similar to insert molding, but without necessarily inserting a pre-molded component. The technique injection molds one polymer, then a second right over the first without removing the piece from the tooling. As with insert molding, the two materials bond together.
Overmolding example:
- Creating the grippy, shock-absorbing handles on medical devices by overmolding a thermoplastic elastomer (TPE) onto a rigid polymer handle
Mehrschüssiges Gießen
Yet another option allowing the use of multiple materials is multi-shot molding. This puts two or more injection molding machines in line with a single mold. As the mold opens and closes between cycles, each machine injects a different material into the same cavities, layering the polymers.
Two-material examples include:
- Syringe plungers with a lubricious coating to ease movement
- Breathing circuits with sections requiring greater flexibility or rigidity
With precise process timing and control, even more than two materials can get layered.
Gas-Assist Injection Molding
Injecting pressurized gas into the molten plastic prior to cooling improves flow in detailed molds, creates hollow internal channels, or even produces blow-molded areas within an injection molded part. The gas applies internal pressure as the plastic cools, preventing sink marks and distortion while allowing thicker plastic sections without excess weight.
Flüssigsilikonkautschuk (LSR) Formgebung
LSR molding produces silicone parts with incredible tear resistance plus improved clarity and purity. As a thermoset elastomer, liquid silicone cures inside the mold then gets ejected as a durable finished component or device. This method works well for flexible medical parts like CPR masks, N95 mask seals, catheter tips, stoppers, valve membranes, and more.
Micro Molding for Miniature Components
Micro molding allows creating incredibly tiny yet intricate components out of various medical-grade plastics through injection molding. Parts with dimensions under 0.04 inches get reliably produced. Tiny molded gears, seals, stopcocks, drug delivery devices, and electronic components play integral roles treating health conditions or improving quality of life.
Cardiac stents exemplify the possibilities and impact of micro-molded medical devices. These tiny mesh tubes expand arteries allowing improved blood flow. The polymer coatings also slowly release drugs preventing recurring blockages. Micro molding provides the miniscule precision stents required.
Essential Considerations for Medical Injection Molding
Medical device manufacturers utilizing plastic injection molding solutions must adhere to stringent protocols and standards, including:
- FDA regulations
- ISO 13485
- GMP – Good Manufacturing Practices
- Clean room protocols
Validation protocols must prove out all production processes, equipment, software, materials, and final products to ensure uncompromising quality and consistency. Regular revalidation also comes necessary.
Thorough documentation provides full traceability on all materials and production details for each batch of devices. Parts get inspected and tested per the validation plan as well.
For custom medical injection molding, work only with a specialist familiar with the standards and regulations. Taking chances risks patient health and lands companies in hot water with FDA auditors. There’s no room for errors with injection molded medical products.
Transforming Healthcare Through Innovative Plastic Molding
The quest advancing medical technology and finding new ways restoring patient health relies heavily on injection molding capabilities evolving in parallel. Molding provides a practical, repeatable approach mass producing intricate components that would otherwise prove difficult or downright impossible to manufacture.
Injection molding repeatedly demonstrates medical device miracles once considered improbable science fiction. From stents restoring cardiovascular function to microfluidics advancing practical at-home diagnostics to drug infusion delivery systems improving quality of life – injection molding propels healthcare innovations saving patient lives.
The 21st century promises exhilarating medical technology breakthroughs as injection molding processes continue maturing in accuracy, precision, sustainability, and efficiency. By optimizing designs for manufacturability in conjunction with the latest molding techniques, the possibilities stay wide open for creating ingenious biocompatible devices alleviating suffering and detectability threats like cancer, heart disease, diabetes, and so much more.
Injection molding for medical applications has already impacted healthcare in astonishing ways – the future outlook shines brightly.