Kann HDPE spritzgegossen werden?
Ja, Polyethylen hoher Dichte (HDPE) kann durchaus spritzgegossen werden. Als einer der vielseitigsten und am weitesten verbreiteten Kunststoffe weltweit ist HDPE eine äußerst beliebte Wahl für Spritzgießanwendungen in einer Vielzahl von Branchen.
In dieser Stelle, als Fachmann HDPE-Spritzgießen Hersteller, werde ich alles über HDPE beim Spritzgießen erzählen.
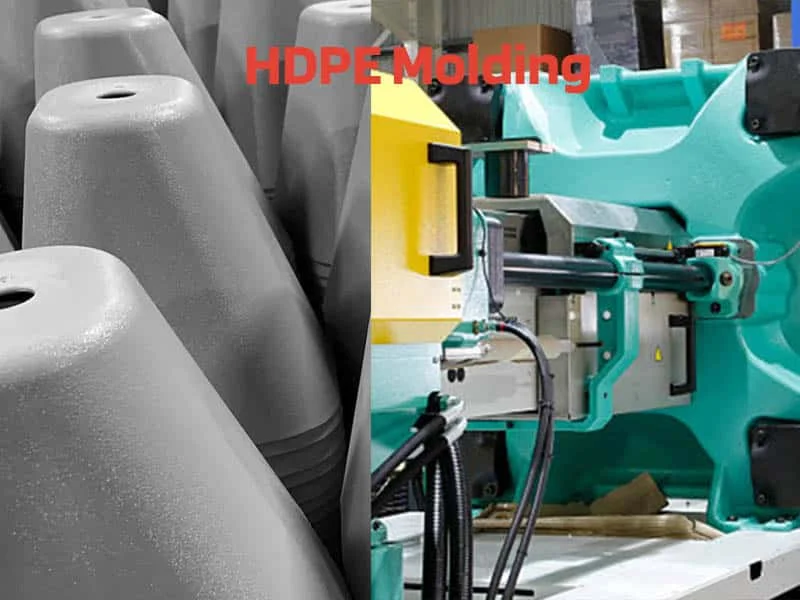
Warum HDPE für das Spritzgießen verwenden?
Es gibt mehrere wichtige Gründe, warum HDPE so häufig für Spritzgussteile und Produkte gewählt wird:
Stärke und Langlebigkeit
Mit einer hohen Zugfestigkeit und einem hohen Biegemodul sind aus HDPE geformte Teile in der Regel sehr haltbar und steif. HDPE hat auch eine ausgezeichnete Chemikalien- und Spannungsrissbeständigkeit. Das macht es ideal für Produkte, die einer starken Beanspruchung und dem Kontakt mit Chemikalien standhalten müssen.
Kosteneffizienz
Im Vergleich zu vielen technischen Harzen sind ungefüllte HDPE-Typen relativ preiswert. In Verbindung mit einer effizienten Herstellung im Spritzgussverfahren kann dies zu sehr wirtschaftlichen Endprodukten führen.
Bereich der Benotung
HDPE ist in einer breiten Palette von Viskositätsgraden erhältlich, was den Verarbeitern eine große Flexibilität bietet. Zur Optimierung der Fließeigenschaften und Merkmale wie Schrumpfung können Harze mit niedriger und hoher Viskosität ausgewählt werden.
einfache Färbung
Wenn farbige Teile benötigt werden, kann HDPE leicht mit flüssigen oder pulverförmigen Farbstoffen eingefärbt werden. Dadurch werden die höheren Kosten vermieden, die mit der Verwendung von vorgefärbtem HDPE-Material verbunden sind.
Schlüsselanwendungen für spritzgegossenes HDPE
Dank seiner herausragenden Eigenschaften in Verbindung mit einer effizienten Herstellbarkeit sind spritzgegossene HDPE-Teile allgegenwärtig:
Konsumgüter
Kappen, Verschlüsse, Behälter, Haushaltswaren
Industrielle Güter
Eimer, Kisten, Kästen, Schalen, Tanks, landwirtschaftliche Komponenten
Autoteile
Komponenten des Kraftstoffsystems, Leitungen, Gebläse, Pedale
Mit innovativem Produktdesign dienen HDPE-Spritzgussteile in neuen und wachsenden Anwendungen wie:
- Schutzausrüstung
- Wiederverwendbare Verpackungen
- Schiffskomponenten
- Freizeitartikel
Überblick über den HDPE-Spritzgießprozess
Die Herstellung von HDPE-Teilen im Spritzgießverfahren besteht aus drei Hauptphasen:
1. Plastifizierung
HDPE-Harz (in der Regel in Form von Granulat) wird durch Schwerkraft aus einem Trichter in den Zylinder der Spritzgießmaschine befördert. Eine sich hin- und herbewegende Schnecke befördert das Granulat vorwärts, während sie sich dreht, wodurch das Material zu einer homogenen Schmelze verarbeitet wird.
Moderne Spritzgießmaschinen verwenden Sensoren, um Variablen wie Temperatur, Druck, Viskosität und Schneckendrehzahl während der Plastifizierung sorgfältig zu steuern.
2. die Injektion
Sobald das geschmolzene HDPE die optimale Konsistenz erreicht hat, wird es unter hohem Druck in das Formwerkzeug gespritzt. Das Formwerkzeug besteht aus zwei präzisionsgefertigten Stahlhälften mit Merkmalen, die die Form der fertigen Kunststoffteile bilden.
Die ausgeklügelte Prozesssteuerung der Spritzgusspresse regelt den Einspritzdruck und die Einspritzgeschwindigkeit für eine gleichbleibende Qualität.
3. Erstarrung
Nach dem Einspritzen in die Form entziehen Kühlkanäle im Formwerkzeug dem HDPE-Material schnell Wärme. Dadurch verfestigt sich der Kunststoff in der gewünschten Form.
Die Form öffnet sich dann und ermöglicht die Entnahme des abgekühlten und festen Kunststoffteils. Danach schließt sich die Form und der Einspritzvorgang wird wiederholt.
Mehrkavitätenwerkzeuge in Verbindung mit Hochleistungs-Spritzgießmaschinen ermöglichen sehr hohe stündliche Produktionsraten.
Vorteile des HDPE-Spritzgießens
Die Entscheidung für das Spritzgießen mit HDPE-Materialien bietet Verarbeitern und Produktmarken erhebliche Vorteile:
Hoher Grad an Automatisierung - Nach dem ersten Entwurf der Form ermöglicht das HDPE-Spritzgießen eine hochautomatisierte, rationelle Fertigung mit wenig direktem Arbeitsaufwand.
Skalenvorteile - Mit richtig konzipierten Formen können sehr große Mengen an gleichbleibend hochwertigen Kunststoffteilen hergestellt werden. Dies führt zu einer Senkung der Kosten pro Teil.
Gestaltungsfreiheit - Komplexe Geometrien von HDPE-Kunststoffteilen, Hinterschneidungen und 3D-Merkmale können spritzgegossen werden, und zwar in einem einzigen nahtlosen Stück. Dies gibt Marken einen großen Spielraum für Produktinnovationen.
Auswahl an Oberflächen - HDPE-Spritzgussteile können mit Techniken wie Spritzlackierung, Tampondruck, Heißprägen und Ultraschallschweißen nachbearbeitet werden, um praktisch jede Ästhetik zu erreichen.
Wachstum des HDPE-Spritzgießens
In den letzten Jahren hat der Markt eine drastische Ausweitung der Anwendungen und des Volumens von HDPE-Spritzgussteilen erlebt. Warum dieser Anstieg?
Materialeigenschaften - Wie bereits erwähnt, zeichnet sich HDPE durch eine außergewöhnliche Kombination aus Festigkeit, Chemikalien- und Temperaturbeständigkeit und Erschwinglichkeit aus.
Nachhaltigkeit - Sowohl das HDPE-Material als auch das Spritzgussverfahren bieten Marken Möglichkeiten für eine nachhaltige Gestaltung. Dazu gehören recycelte Inhalte, Wiederverwertbarkeit, geringes Gewicht, Haltbarkeit und mehr.
Vorteile gegenüber anderen Kunststoffen - Im Vergleich zu anderen Materialien wie PVC, Acetal oder NylonMit dem HDPE-Spritzgießen können die Kosten für die Teile erheblich gesenkt werden, während gleichzeitig eine hervorragende Leistung erzielt wird.
Globale Nachfrage - Die Nachfrage nach nachhaltigeren Verpackungen, Baumaterialien und Konsumgütern nimmt weiter zu, insbesondere in Asien und Afrika. Das HDPE-Spritzgießen ermöglicht es, diese Nachfrage effizient zu erfüllen.
Schlussfolgerung
Dank seiner Vielseitigkeit, Langlebigkeit und Fertigungseffizienz nimmt die Verwendung von spritzgegossenem HDPE exponentiell zu. Sowohl Verbraucher- als auch Industriemarken profitieren von der Designfreiheit, der Vielfalt der verfügbaren Oberflächen und den Größenvorteilen, die das HDPE-Spritzgießen bietet.
In Kombination mit innovativem Produktdesign bietet das HDPE-Spritzgießen Marken ein nahezu unbegrenztes Potenzial, das Leben mit erschwinglichen und nachhaltigen Kunststoffformteilen zu verbessern.
Also nicht nur kann HDPE im Spritzgussverfahren - HDPE eignet sich hervorragend für das Spritzgussverfahren. Vom kleinsten Bauteil bis hin zu großen Fertigprodukten bietet spritzgegossenes HDPE in Tausenden von Anwendungen auf der ganzen Welt hervorragende Leistung und Wert.