Der Gegendruck ist ein entscheidender, aber oft übersehener Parameter beim Spritzgießen. Die korrekte Einstellung des Gegendrucks verbessert die Konsistenz von Schuss zu Schuss und die Qualität der Teile.
In diesem umfassenden Leitfaden finden Sie als Fachmann Hersteller von Kunststoff-SpritzgussteilenIn diesem Kapitel erfahren Sie, was Gegendruck ist, warum er wichtig ist und wie Sie ihn Schritt für Schritt einstellen.
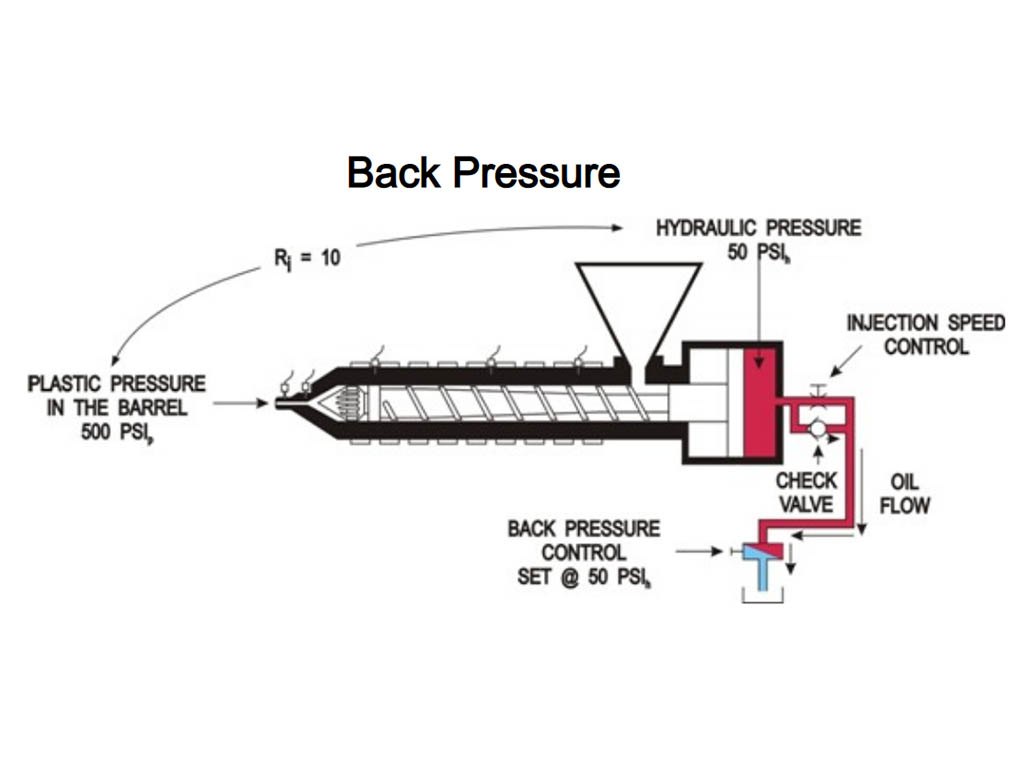
Was ist Hinterdruck-Spritzgießen?
Unter Gegendruck versteht man den Widerstand gegen die Schnecke, wenn sie sich erholt, um den nächsten Schuss zu erzeugen. Er komprimiert den Kunststoff vor dem Rückschlagventil, um eine gleichmäßige Schussgröße und Dichte zu gewährleisten.
Ein höherer Gegendruck sorgt für eine bessere Gleichmäßigkeit der Schmelze und eine bessere Temperaturkontrolle, ohne die Schmelzetemperatur zu erhöhen. Er verbessert auch die Farbverteilung, die Entlüftung und die Dimensionsstabilität und verhindert das Schneckenwandern.
Ein zu hoher Gegendruck kann jedoch verstärkte Harze beschädigen und temperaturempfindliche Kunststoffe zersetzen. Außerdem erhöht er die Zykluszeiten.
Warum ist die Einstellung des Gegendrucks wichtig?
Hier sind 5 Gründe, warum die richtige Einstellung des Gegendrucks wichtig ist:
1. Konsistente Schussgröße
Bei der Gegendruckkompression werden die Moleküle fest verpackt, so dass jeder Schuss die gleiche Dichte und das gleiche Gewicht hat. Diese Konsistenz ist entscheidend für gute Teile.
2. Bessere Schmelzqualität
Erhöhter Gegendruck mischt Additive und Pigmente gründlicher, ohne die Schmelztemperatur zu erhöhen. Dies führt zu einer glatten, gleichmäßigen Schmelze.
3. Reduzierte Spreizung und Blitzlicht
Durch die Kontrolle der Schussdichte verhindert der Gegendruck Spreizung, Gratbildung und andere Defekte, die durch uneinheitliche Füllung entstehen.
4. Schnellere Farbwechsel
Durch den Gegendruck wird der Lauf bei Farbwechseln effektiver gereinigt, da die Schneckenspitze eng an der Kehle gehalten wird.
5. Keine schwarzen Flecken
Es minimiert die Lücken zwischen den Schneckengängen, um zu verhindern, dass sich das Material zersetzt und schwarze Flecken verursacht.
Wie viel Gegendruck ist erforderlich?
Als Faustregel gilt, dass ein hydraulischer Gegendruck von 50-100 psi pro Zoll Schneckendurchmesser gute Ergebnisse liefert.
Eine 3-Zoll-Schraube benötigt also 150-300 psi. Bei übermäßigem Gegendruck besteht die Gefahr einer Beschädigung, also erhöhen Sie den Druck vorsichtig in Schritten von 50 psi, bis er optimal ist.
Behalten Sie den niedrigstmöglichen Gegendruck bei, der noch gute Teile liefert. Jedes Material und jede Form hat einzigartige Anforderungen.
Wie man den Gegendruck beim Spritzgießen in 6 Schritten einstellt
Befolgen Sie diese Best-Practice-Prozedur, um den Gegendruck einzustellen:
Schritt 1: Beginnen Sie ohne Gegendruck
Stellen Sie den Gegendruck auf Null und legen Sie einen Basisprozess fest. Dies ist Ihr Referenzpunkt.
Schritt 2: Schneckendrehzahl erhöhen
Erhöhen Sie die Schneckendrehzahl in Schritten von 25 bis 50 Umdrehungen pro Minute, bis der Prozess durch zu starke Schererwärmung inkonsistent wird. Reduzieren Sie dann die Drehzahl leicht, bis sie stabil ist.
Dadurch wird die maximale Drehzahl ermittelt, die Ihre Konfiguration bewältigen kann. Legen Sie nun die Drehzahl fest und passen Sie nur noch den Gegendruck an.
Schritt 3: Gegendruck erhöhen
Beginnen Sie mit einem Gegendruck von 50-100 psi. Lassen Sie die Maschine sich stabilisieren und achten Sie auf Veränderungen der Konsistenz.
Schritt 4: Wiederholen Sie den Vorgang bis zum Optimum
Erhöhen Sie den Gegendruck zwischen den Schüssen schrittweise in Schritten von 50 psi. Fahren Sie bis zum maximalen Gegendruck fort, der für das Material empfohlen wird, oder bis Sie die beste Konsistenz erreichen.
Schritt 5: Feinabstimmung der Einstellung
Es kann sein, dass Sie feststellen, dass der optimale Wert zwischen zwei Gegendruckeinstellungen liegt. Wählen Sie in diesem Fall den niedrigeren Wert, um etwas mehr Sicherheit zu haben.
Schritt 6: Bestätigen Sie mit Data Monitoring
Schließlich validieren Sie Ihr neues Verfahren mit wissenschaftlichen Daten aus den kritischen Prozessdaten (CPOs). Die wichtigsten Messgrößen sind Schussgewicht/-größe und Schneckenerholungszeit.
Überwachen Sie sorgfältig die Abweichungen von Schuss zu Schuss. Wenn die Werte um mehr als +/- 1% abweichen, benötigen Sie wahrscheinlich mehr Gegendruck für einen wirklich wiederholbaren Prozess.
FAQs
Beeinflusst der Gegendruck die Schmelztemperatur?
Nein, der Gegendruck hat nur einen geringen Einfluss auf die Schmelzetemperatur. Die Schneckendrehzahl ist mehr als 10-mal so groß.
Können Sie den erforderlichen Gegendruck berechnen?
Nicht wirklich. Der optimale Gegendruck hängt stark vom Material ab, Farbstoff, Formgestaltung und andere Faktoren. Sie muss experimentell ermittelt werden.
Gibt es eine maximale Gegendruckgrenze?
Ja, die meisten Experten empfehlen, den Gegendruck auf nicht mehr als 20% der maximalen Tonnage der Spritzeinheit zu begrenzen. Bei übermäßigem Gegendruck besteht die Gefahr von Schäden.
Warum erhöht sich mit steigendem Gegendruck die Schussgröße?
Ein höherer Gegendruck verdichtet die Moleküle stärker. Bei gleichem Schussvolumen wird also mehr Material komprimiert, was das Schussgewicht erhöht.
Schlussfolgerung
Die Einstellung eines angemessenen Gegendrucks ist entscheidend für ein robustes, wiederholbares Spritzgießen mit gleichbleibend hochwertigen Teilen.
Befolgen Sie diese 6 Schritte, beginnend mit einem Gegendruck von Null, maximieren Sie zunächst die Schneckendrehzahl und erhöhen Sie dann schrittweise den Gegendruck, bis die optimale Konsistenz klinisch ermittelt ist.
Wenn Sie den Gegendruck gleich beim ersten Mal richtig einstellen, ersparen Sie sich stundenlange Fehlersuche und frustrierte Kunden in der Folge. Nehmen Sie sich die Zeit für eine präzise Einstellung unter Anwendung wissenschaftlicher Formgebungsprinzipien, um einen störungsfreien Prozess zu gewährleisten.