Gewindeteile sind in unzähligen Branchen weit verbreitet, von Sanitärarmaturen über Befestigungselemente bis hin zu Kunststoffflaschen. Die Herstellung von Gewindeteilen erfordert spezielle Techniken und Überlegungen im Vergleich zu herkömmlichen Kunststoffteilen. In diesem umfassenden Leitfaden werden Sie als Fachmann Kunststoff-Spritzguss Hersteller, werde ich Sie durch alles führen, was Sie über die Herstellung von Kunststoffteilen mit Gewinde im Spritzgussverfahren wissen müssen.
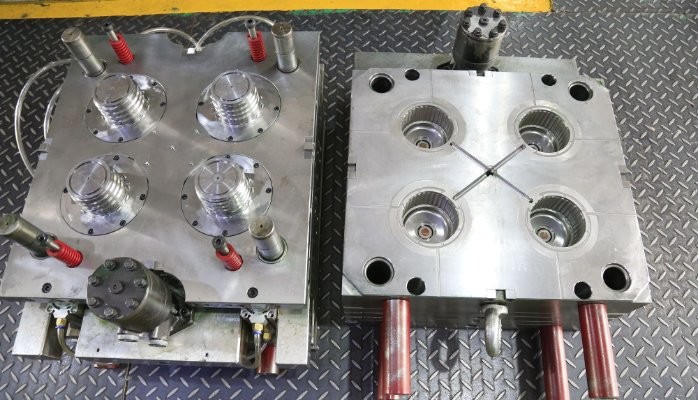
Ein Überblick über Gewindeteile
Gewindeteile enthalten spiralförmige Rippen, die als Gewinde bezeichnet werden und es ihnen ermöglichen, sich mit dem Gegengewinde zu verbinden. Schrauben, Bolzen, Muttern, Flaschenverschlüsse und Schlauchanschlüsse sind einige Beispiele für Gewindeteile.
Der Hauptvorteil von Gewinden besteht darin, dass sie eine feste, dichte und wiederverwendbare Verbindung bilden, ohne dass Schweißen, Löten oder Kleben erforderlich sind. Durch einfaches Drehen der Gewindekomponente wird diese fest mit dem entsprechenden Teil verbunden.
Gemeinsame Gewindetypen
Es gibt mehrere standardisierte Gewindeprofile, darunter:
- Vereinheitlichte Gewindenorm (UNC/UNF): In den USA für allgemeine Zwecke gebräuchlich. Definiert durch Gewindewinkel, -steigung und -durchmesser.
- Metrisches ISO-Gewinde: Die internationale Norm mit einem 60°-Gewindewinkel. Gibt die Gewindesteigung und den Durchmesser an.
- NPT/NPS: Für konische oder gerade Rohrverbindungen mit Gewinde.
- ACME: Trapezgewinde für Gewindespindeln und andere Kraftübertragungsanwendungen.
Der Gewindetyp muss mit dem zugehörigen Bauteil kompatibel sein. Daher ist die richtige Auswahl und Spezifikation von Gewinden entscheidend.
Wichtige Überlegungen zu spritzgegossenen Gewinden
Aufgrund ihrer komplexen Geometrie erfordert die Herstellung von Gewinden in Kunststoff-Spritzguss im Vergleich zum konventionellen Spritzguss spezielle Werkzeugkomponenten und Prozessüberlegungen.
Hier sind einige wichtige Faktoren zu berücksichtigen:
1. Bestandteile der Form
- Kerne mit Gewinde: Gehärtete Stahlkerne, die mit dem gewünschten Gewindeprofil bearbeitet sind. Sie werden in den Formhohlraum eingesetzt.
- Abschraubmechanismen: Automatische oder manuelle Vorrichtung zum Lösen von Gewindekernen aus dem Formteil.
- Seitliche Kerne: Kann Hinterschneidungen in Gewinden erzeugen, um ein Aufspalten zu verhindern.
2. Auswahl des Materials
- Die Materialien müssen eine ausreichende Festigkeit, Härte und Duktilität aufweisen, um Gewindeschäden zu widerstehen.
- Füllstoffe wie Glasfasern verringern die Flexibilität des Materials beim Entformen.
3. Teil Design
- Entformungsschrägen zur Erleichterung der Entformung.
- Gleichmäßigkeit der Wandstärke.
- Minimale Kernsperren.
Die richtige Wahl dieser Parameter ist entscheidend für die Herstellung funktionaler Kunststoffteile mit Gewinde im Spritzgussverfahren.
Der Prozess des Gewindespritzgießens - Schritt für Schritt
Hier sind die wichtigsten Phasen der Herstellung von Kunststoffteilen mit Gewinde durch Spritzgießen:
Schritt 1: Formenbau
Die Form muss präzise bearbeitet werden, damit Details wie Gewinde in den Formteilen genau wiedergegeben werden können.
Zu den wichtigsten Teilschritten gehören:
- Gestaltung des Formhohlraums um die Teilegeometrie herum.
- Herstellung von Hohlraumgewindeeinsätzen.
- Integration von Funktionen zur automatischen oder manuellen Kernentfernung.
Eventuelle Hinterschneidungen in den Gewinden erfordern möglicherweise seitlich wirkende Nocken oder Schieber, um den Auswurf nicht zu behindern.
Schritt 2: Montage der Form
Vor der Produktion muss die Form zusammengesetzt und kalibriert werden:
- Die Gewindekernstifte und -blöcke werden in die Formhälften eingesetzt.
- Die Ausrichtung des Hohlraums wird bestätigt, um den Grat um das Gewinde herum zu minimieren.
- Alle Komponenten der Nebenwirkung werden ausgerichtet.
- Die Kühlkanäle sind angeschlossen.
Schritt 3: Spritzgießen
Nun wird die komplette Form in eine Kunststoffspritzgießmaschine eingebaut, um mit der Teileproduktion zu beginnen.
Der Grundzyklus umfasst:
- Spannen - Die beiden Hälften der Form werden mit großem Druck zusammengepresst.
- Einspritzen - Überhitzte Kunststoffschmelze füllt den Formhohlraum über Angusskanäle und Anschnitte.
- Kühlung - Nach dem vollständigen Auffüllen des Abdrucks wird der Kunststoff durch Kühlkanäle und Formwände abgekühlt.
- Auswerfen - Die Stifte werfen das feste Kunststoffteil aus der Form aus. Die Gewinde werden in der Kavität gebildet.
- Zurücksetzen - Die Form schließt sich, wenn automatische Mechanismen die Seitenkerne zurückziehen und die Gewindekerne auswerfen.
Dann öffnet sich die Form, die Teile werden entnommen, und der automatische Zyklus wiederholt sich kontinuierlich.
Eine Feinabstimmung der Formgebungsparameter wie Schmelzetemperatur, Einspritzgeschwindigkeit und Kühlzeit ist erforderlich, um qualitativ hochwertige Gewindeteile zu erhalten.
Schritt 4: Nachbearbeitung
- Nach dem Gießen werden die Teile beschnitten, fertiggestellt und geprüft.
- Bei der Funktionsprüfung wird die Unversehrtheit des Gewindes durch einen Probemontageversuch mit einem passenden Gewindeteil überprüft.
- Bestätigte Teile werden verpackt und versandt. Defekte Teile werden aussortiert oder granuliert.
Mit einer robusten Werkzeugkonstruktion und der richtigen Einstellung des Prozesses bei der Erstbemusterung lassen sich im Spritzgussverfahren zuverlässig Kunststoffteile mit komplizierten Gewindedetails herstellen.
Häufig gestellte Fragen
Kann jeder Kunststoff mit Gewinde geformt werden?
- Technisch gesehen ja, aber jedes Material hat unterschiedliche Anforderungen in Bezug auf Viskosität, Schrumpfung, Flexibilität usw. Amorphe und teilkristalline Kunststoffe wie Nylon, Acetal, Polypropylen, ABS sind am besten für Gewindeteile geeignet.
Wie viele Gewinde pro Zoll (TPI) können geformt werden?
- Als Faustregel gilt, dass Kunststoffgewinde eine gröbere Steigung haben sollten als Metallgewinde. In der Regel werden 10-20 TPI bevorzugt, um eine vorzeitige Beschädigung der Gewinde in Kunststoffen zu vermeiden. Ultrafeine Gewindesteigungen unter 20 TPI erfordern eine sehr hohe Präzision beim Gießen.
Welche Toleranz kann bei spritzgegossenen Gewinden eingehalten werden?
- Mit Präzisionswerkzeugen und Prozesskontrolle können bei geformten Gewinden je nach verwendetem Kunststoff recht enge 3-5%-Toleranzen erreicht werden. Aber im Allgemeinen haben Kunststoffgewinde von Natur aus engere Toleranzen als bearbeitete oder geschmiedete Metallgewinde.
Eignet sich das Ultraschallschweißen für die Montage von Kunststoffteilen mit Gewinde?
- Das Ultraschallschweißen verursacht Materialfluss und Verformung und ist daher im Allgemeinen nicht für die Befestigung von Kunststoffteilen mit Gewinde geeignet, bei denen es für eine effektive Funktion auf genaue Abmessungen ankommt. Stattdessen wird das Verbinden von Gewindeteilen mit herkömmlichen Befestigungstechniken empfohlen.
Wichtigste Erkenntnisse
- Spezialisierte Kerne und Formkomponenten ermöglichen das Spritzgießen von Kunststoffgewinden.
- Materialflexibilität, Entformungsschrägen minimieren Entformungsschäden.
- Automatisierte Abschraubmechanismen verbessern die Qualität und senken die Kosten.
- Gröbere Gewindegänge und Zugaben ermöglichen größere Abweichungen bei der Kunststoffverarbeitung.
Unter Berücksichtigung der Werkzeugkonstruktion, der Toleranzzuordnung und der Materialeigenschaften können komplizierte Kunststoffgewindeteile im Spritzgussverfahren wirtschaftlich im industriellen Maßstab hergestellt werden.