Beim Spritzgießen ist der Angusskanal ein entscheidendes Bauteil, das den geschmolzenen Kunststoff von der Einspritzdüse zu den Formkavitäten führt. Als Profi Hersteller von Kunststoff-SpritzgussteilenIn diesem umfassenden Leitfaden finden Sie alles, was Sie über Kufen wissen müssen, einschließlich Typen, Designüberlegungen, Auswirkungen auf die Teilequalität und vieles mehr.
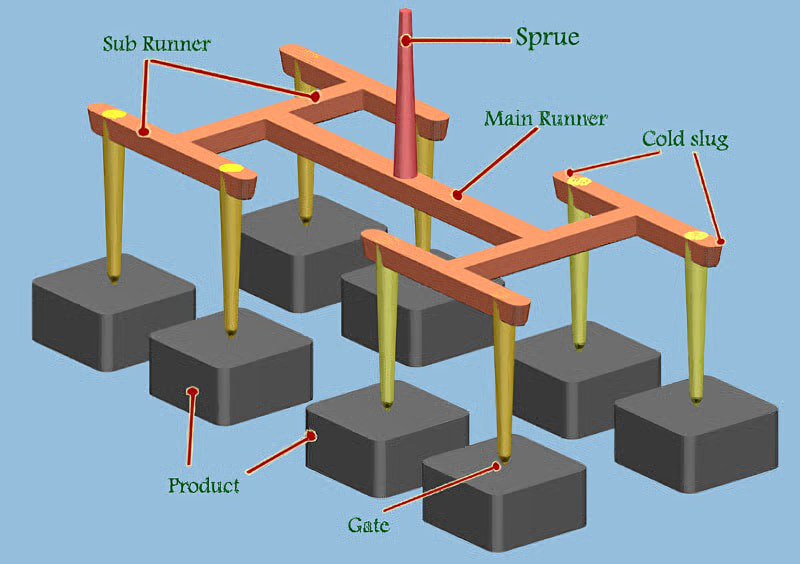
Was ist ein Angusskanal beim Spritzgießen?
Ein Angusskanal ist ein in die Form geschnittener Kanal, der während des Spritzgussverfahrens geschmolzenen Kunststoff von der Einspritzdüse zu den Kavitäten leitet. Er dient als Durchgang, durch den der Kunststoff gleichmäßig in die Kavitäten fließen kann.
Gut gestaltete Angusskanäle sind für die Herstellung qualitativ hochwertiger, gleichmäßiger Teile unerlässlich. Größe, Form und Position der Angusskanäle wirken sich direkt darauf aus, wie schnell sich die Kavitäten füllen, wie viel Material verschwendet wird, wie hoch die Teilequalität ist und wie lange die Zykluszeiten sind.
Komponenten des Läufersystems
Das komplette Kufensystem besteht aus einigen Schlüsselkomponenten:
Anguss - Im ersten Segment tritt der geschmolzene Kunststoff durch die Einspritzdüse ein. Der Anguss führt das Material in die Kanäle ein.
Läufer - Kanäle mit verschiedenen Längen und Durchmessern, die das Material auf die Formangüsse verteilen.
Pforten - Die letzten verengten Übergänge von Kufen in die Teilhohlräume. Schieber regeln den Durchfluss in die Kavitäten.
Gemeinsam wirken diese Elemente zusammen, um eine gleichmäßige Fließfront des Kunststoffs in alle Kavitäten gleichzeitig zu erzeugen. Das Ziel ist die Herstellung vollständig gefüllter, fehlerfreier Teile in möglichst kurzen Zykluszeiten.
Kaltkanalsysteme vs. Heißkanalsysteme
Es gibt zwei Haupttypen von Spritzgießkanalsystemen - Kaltkanäle und Heißkanäle:
Kalte Läufer
Kaltkanäle erstarren in der Form zusammen mit den Formteilen. Anguss, Angusskanäle und Teile bleiben beim Auswerfen als ein festes Stück miteinander verbunden. Mit Material gefüllte Kaltkanäle stellen Abfall dar, der entfernt und wiederaufbereitet oder entsorgt werden muss.
Kaltkanäle ermöglichen einfachere Formen, niedrigere Werkzeugkosten, Designflexibilität und die Verwendung einer Vielzahl von Harzen. Im Vergleich zu Heißkanälen erzeugen sie jedoch mehr Abfall und haben längere Zykluszeiten.
Heiße Kufen
Bei Heißkanälen werden beheizte Verteiler und Düsen verwendet, um den Kunststoff beim Fließen in die Kavitäten flüssig zu halten. Beim Auswerfen werden die verfestigten Teile ohne Angüsse oder Angusskanäle ausgeworfen. Dies reduziert den Ausschuss und beschleunigt die Zykluszeiten.
Die Herstellung von Heißkanalwerkzeugen ist komplexer und kostspieliger als die von Kaltkanalwerkzeugen. Obwohl die Abfallreduzierung langfristig angelegt ist, kann sie in der Großserienproduktion zu erheblichen Kosteneinsparungen führen.
Warum das richtige Laufraddesign entscheidend ist
Die Leistung eines jeden Spritzgießwerkzeugs hängt in hohem Maße von der Konstruktion des Angusssystems ab. Hier erfahren Sie, warum die Optimierung Ihres Angusskanalsystems so wichtig ist:
Füllzeit & Druck
Richtig dimensionierte Angusskanäle füllen Hohlräume schneller, da sie den Durchfluss mit weniger Druckverlust ermöglichen. Dünne, lange Kufen können vorzeitig einfrieren und zu kurzen Schüssen führen.
Teil Qualität
Ein ausgewogenes Angussdesign liefert eine gleichmäßige Schmelzeflussfront zu allen Kavitäten. Diese Konsistenz führt zu einheitlichen Eigenschaften und Erscheinungsbildern bei jedem Teil. Unausgewogene Systeme führen zu Abweichungen zwischen den Kavitäten und damit zu Qualitätsproblemen.
Zyklus-Effizienz
Zu viele Angusskanäle bedeuten längere Erstarrungs- und Abkühlzeiten und verlangsamen die Zyklen. Ein optimiertes Layout minimiert das Volumen der Angusskanäle, um die Teile schnell abzukühlen und auszuwerfen.
Materialeinsparungen
Kürzere Kanäle mit kleinerem Durchmesser verringern die Verschwendung von Anguss- und Angussplastik. Dies führt zu erheblichen Kosteneinsparungen, insbesondere bei Kaltkanalanwendungen.
Richtlinien für das Design von Schlüsselläufern
Hier finden Sie wichtige Tipps für die Planung eines effektiven Kufensystems:
Größenbestimmung
1. Durchmesser - Die Größe sollte auf der Grundlage von Faktoren wie Wandstärke des Teils, Fließlänge, Schmelzeeigenschaften und Einspritzgeschwindigkeit/-druck angemessen sein. Typische Durchmesser reichen von 2 mm bis 10 mm.
2. Längen - Minimieren Sie alle Fließkanalsegmente - halten Sie die Strecken vom Anguss bis zu den Anschnitten so kurz wie möglich. Lange Fließwege verringern den Druck und fördern das frühzeitige Einfrieren.
Ausgleichen
3. Gleiche Fließwege - Stellen Sie sicher, dass die Routen zu jedem Hohlraum gleich lang sind, um ausgewogene Bedingungen zu schaffen. Nutzen Sie Strömungssimulationen, um die Leistung zu überprüfen.
4. Strategische Pforten - Erhöhen Sie die Anzahl bzw. den Standort der Gates, um einen direkteren Zugang zur Kavität zu ermöglichen und das Volumen der Läufer zu minimieren.
Konfiguration
5. Einfachheit - Verwenden Sie das am wenigsten komplexe System, das die Leistungsziele erfüllt. Einfacher ist besser. Prüfen Sie den Bedarf an sekundären Läufern oder Sub-Gates.
6. Straffes Layout - Sanft gekrümmte Kufen, die den Konturen folgen, statt scharfkantig zu sein. Eliminieren Sie tote Zonen, in denen das Material stagnieren kann.
Die korrekte Berücksichtigung dieser Designelemente ist die Grundlage für den zuverlässigen Erfolg eines jeden Läufersystems und maximiert die Qualität und Effizienz.
Wie Kufen die Qualität von Spritzgussteilen beeinflussen
Fehler in der Kufenauslegung äußern sich oft als sichtbare Teilefehler oder Leistungsprobleme. So geht's:
Unausgewogene Füllung - Wenn die Fließwege drastische Unterschiede im Druckverlust aufweisen, füllen sich die Kavitäten unterschiedlich schnell. Eine langsamere Füllung führt dazu, dass das Material ungleichmäßig in der Form abkühlt, was zu sichtbaren Bindenähten, Einfallstellen, Hohlräumen oder Verzug führt.
Vorzeitiges Einfrieren - Eine unzureichende Dimensionierung der Angusskanäle im Verhältnis zur Fließlänge drosselt den Druck, so dass die Schmelze vor dem vollständigen Füllen gefriert. Das Ergebnis sind kurz gespritzte Teile mit unvollständigen Details.
Scheren - Übermäßige Winkelübergänge oder Einschnürungen verschlechtern die Polymere durch übermäßiges Erhitzen und Abkühlen unter Scherung. Führt zu lokalisierten Veränderungen der Materialeigenschaften.
Jeder dieser häufigen Defekte lässt sich auf grundlegende Mängel in der Konstruktion des Laufrades zurückführen.
Optimierung und Analyse der Laufradkonstruktion
Die Entwicklung eines optimalen Kufensystems ist ein komplexes Unterfangen, das Erfahrung und spezielle Simulationswerkzeuge erfordert. Im Folgenden finden Sie einen allgemeinen Überblick über den modernen Konstruktionsansatz:
1. Konzeptionelles Layout - Die anfängliche Laufradkonfiguration wird auf der Grundlage der Teilegeometrie, der Materialauswahl, der Verarbeitungseigenschaften und der Erfahrung grob skizziert.
2. Moldflow-Analyse - Detaillierte Simulationsstudien bewerten die vorgeschlagenen Layouts unter realen Bedingungen. Ermöglicht genaue Leistungsvorhersagen. Ermöglicht die schnelle Erkundung mehrerer "Was-wäre-wenn"-Ideen, um die Strategie zu verfeinern.
3. Endgültige Validierung - Optimale Entwürfe, die aus der Analyse abgeleitet werden, werden schließlich durch tatsächliche Formabmusterung empirisch nachgewiesen. Bietet die Möglichkeit, die Einstellungen vor der Herstellung der Gussform in Originalgröße zu optimieren.
Der Einsatz von Analysemethoden bei der Konstruktion verhindert kostspielige Korrekturen, falls suboptimale Entscheidungen in den Stahl einfließen. Die anfängliche Zeitinvestition zahlt sich über die Lebensdauer einer Form erheblich aus.
Häufig gestellte Fragen zu Spritzgießkanälen
Hier finden Sie Antworten auf einige häufig gestellte Fragen zu Spritzgießkanälen:
Welches ist der beste Laufraddurchmesser?
Typische Durchmesser reichen von 2 mm bis zu 10 mm, abhängig von Faktoren wie Fließlänge, Materialviskosität und Einspritzgeschwindigkeit. Breitere Angusskanäle ermöglichen zwar schnellere Füllraten, erstarren aber langsamer, was die Zykluszeiten verlängert.
Wo sollten Tore in Hohlräumen angebracht werden?
Die Anschnitte sollten in dickere Wandabschnitte der Teile an möglichst wenig sichtbaren äußeren Stellen münden. Dies ermöglicht die schnellste Befüllung und einfachste Entgasung bei gleichzeitiger Minimierung sichtbarer Verunreinigungen.
Wie sollten Läufer zu mehreren Kavitäten abzweigen?
Ein Hauptkanal sollte sich in gleichmäßig verteilte Abzweigungen aufteilen, die in gleicher Länge direkt zu jeder Kavitätenklappe führen. Dies gewährleistet gleichzeitig ausgeglichene Füllbedingungen in allen Kavitäten.
Was ist der Vorteil eines Heißkanals gegenüber einem Kaltkanalsystem?
Heißkanäle vermeiden Abfall und ermöglichen schnellere Zyklen. Aber Kaltkanäle kosten anfangs weniger und arbeiten mit mehr Materialien. Bestimmen Sie Kompromisse auf der Grundlage von anwendungsspezifischen Prioritäten oder Einschränkungen.
Wie lang sollte ein Spritzgießkanal sein?
So kurz wie möglich. Im Allgemeinen sollte die Länge der Leitungen unter 2 Fuß gehalten werden, wenn die Anwendung dies zulässt. Bei einer größeren Länge besteht die Gefahr von übermäßigen Kühlungs- und Druckverlusten, die die Qualität der Endteile beeinträchtigen.
Wie erstelle ich das kosteneffizienteste Ausführungssystem?
Konzentrieren Sie sich auf die Minimierung der Abmessungen, um möglichst wenig Material zu verbrauchen und die Teile dennoch ausreichend zu füllen. Die strategische Platzierung von Anschnitten minimiert auch den Arbeitsaufwand. Vermeiden Sie übermäßig komplexe Geometrien, wenn eine einfachere Route zu den gleichen Ergebnissen führt. Verwenden Sie Analysetools, um optimale Kompromisse zu finden.
Schlussfolgerung
Die Optimierung der Angusskanäle ist entscheidend für den Produktionserfolg beim Spritzgießen in jeder Branche. Obwohl sie für den Endverbraucher unsichtbar sind, stellen diese Komponenten "hinter den Kulissen" alles dar, was für eine zuverlässige, effiziente Produktion von qualitativ hochwertigen Kunststoffteilen aus jedem einzelnen Werkzeug erforderlich ist.