Blasen sind einer der häufigsten Fehler beim Kunststoffspritzgießen und beeinträchtigen das Aussehen und die Leistung der Teile. Aber was genau verursacht Blasen?
In diesem vollständigen Leitfaden finden Sie als Fachmann Hersteller von Kunststoff-Spritzgussteilenwerden wir die verschiedenen Ursachen für Blasen untersuchen, von Problemen mit Materialien, Maschinen und Formen bis hin zu Prozessparametern. Wenn Sie verstehen, was hinter diesen Fehlern steckt, können Sie gezielte Präventiv- und Korrekturmaßnahmen für eine einwandfreie Produktion ergreifen.
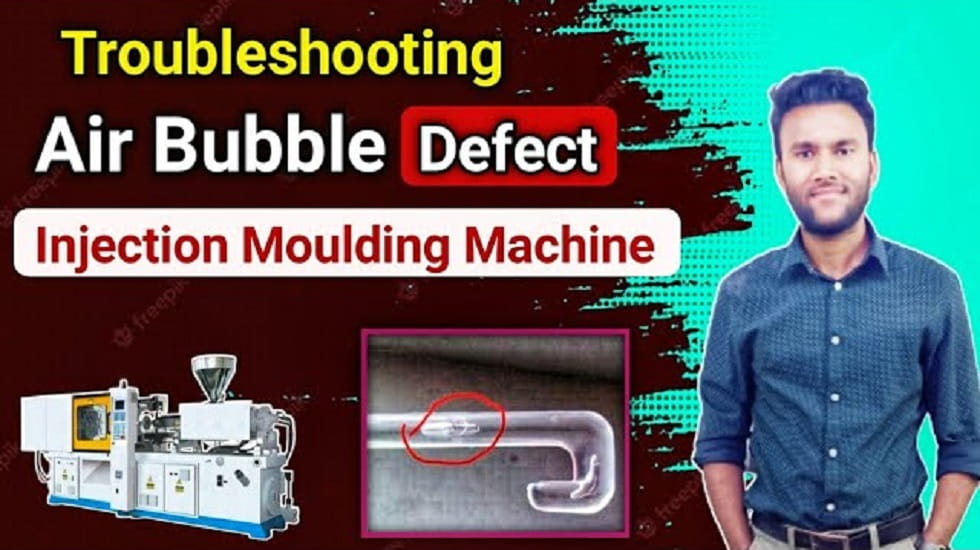
Was verursacht Blasen beim Kunststoff-Spritzgießen: Hauptursachen
Blasen entstehen, wenn Gase während des Formens im Kunststoff eingeschlossen werden. Untersuchen wir die typischen Schuldigen für eingeschlossene Gase:
Unzureichende Trocknung
Viele Harze nehmen leicht Feuchtigkeit aus der Umgebung auf. Materialien wie Nylon, Polycarbonat und PET können erhebliche Feuchtigkeit enthalten, wenn sie nicht vorher richtig getrocknet werden. Unter der Hitze des Fasses verwandelt sich diese Feuchtigkeit in Dampf, der den Schmelzfluss aufbläht. Gründliches Trocknen ist entscheidend für die Vermeidung von Blasenbildung.
Verschlucken von Luft
Auch nach der Trocknung können noch Luftblasen in die Harzverarbeitung eindringen. Die Vakuumförderung nach der Trocknung minimiert das Eindringen von Luft in das Granulat. Sorgfältiges Gießen und gute Haushaltsführung vermeiden ebenfalls Verunreinigungen.
Turbulente Strömung
Eine zu hohe Einspritzgeschwindigkeit verursacht einen turbulenten, nicht-laminaren Schmelzfluss. Diese chaotische Bewegung peitscht Luft in das Polymer und erzeugt Mikroblasen. Eine langsamere laminare Strömung verhindert Gaseinschlüsse.
Materialverschlechterung
Wenn Harz über längere Zeit im Fass verbleibt, wird es durch übermäßige Hitzeeinwirkung abgebaut. Durch die geringere Viskosität des abgebauten Kunststoffs können sich gasförmige Nebenprodukte einmischen und Blasen verursachen.
Schlechte Entlüftung
Bei einer unzureichenden Entlüftung der Form kann die eingeschlossene Luft den Hohlraum während des Füllens nicht verlassen. Da die Gase nirgends entweichen können, haben sie keine andere Möglichkeit, als in Form von Blasen eingeschlossen zu bleiben.
Vorzeitiges Einfrieren
Kühlere Werkzeugtemperaturen beschleunigen die Gefriergeschwindigkeit der Fließfront, bevor die Gase vollständig entweichen. Durch die schnellere Erstarrung werden Blasen im Inneren eingeschlossen und können nicht entweichen.
Wenn Sie herausfinden, welche Faktoren in Ihrer Anwendung zu Blasenbildung führen, können Sie gezielte Gegenmaßnahmen ergreifen. Als Nächstes werden wir bewährte Methoden zur Behebung der einzelnen Faktoren untersuchen.
Wie man Blasen verhindert: Lösungen für jede Grundursache
Mit einem klaren Verständnis für die Ursache von Blasen können wir nun maßgeschneiderte Lösungen für fehlerfreies Spritzgießen anwenden:
Gründliche Materialtrocknung
Kunststoffe, die zur Feuchtigkeitsaufnahme neigen, wie nylon und PET müssen vor dem Formen auf einen Gehalt von weniger als 0,2% getrocknet werden, wobei in der Regel Trockenmittel verwendet werden. Dies verhindert Dampfblasen.
Sorgfältige Handhabung des Harzes
Verwenden Sie nach dem Trocknen geschlossene Vakuumförderer für den Transport der Pellets. Vermeiden Sie das Bewegen und Schütten im Freien, da dadurch Luft eingeschlossen werden kann. Eine schonende Handhabung hält das Material blasenfrei.
Konservative Injektionsgeschwindigkeit
Langsamere, laminare Fließprofile verhindern Turbulenzen und Lufteinschlüsse. Orientieren Sie sich bei der Wahl der Einspritzgeschwindigkeit an der Viskosität und den Fließeigenschaften des jeweiligen Materials.
Genaue Überwachung der Schussgröße
Durch die Anpassung des Schussvolumens an die Teilegeometrie wird eine längere Hitzeeinwirkung vermieden, die den Kunststoff zersetzen kann. Kombiniert mit einem ausreichenden Gegendruck, um ein gutes Polster zu erhalten.
Verbessertes Entlüftungsdesign
Die richtige Entlüftungstiefe, der richtige Durchmesser, die richtige Position und der richtige Winkel erleichtern die Luftentfernung aus dem Hohlraum während des Füllens. Vakuumentlüftungen verbessern die Luftblasenentfernung zusätzlich.
Ausreichende Formtemperatur zulassen
Innerhalb der zulässigen Grenzen hält die Verwendung wärmerer Formen die Materialien länger flüssig, so dass die Gase vor dem Einfrieren vollständig entweichen können.
Anstatt Probleme im Nachhinein zu beheben, setzt dieser proaktive Ansatz bei den Grundursachen an, um sie dauerhaft zu vermeiden. Lassen Sie uns nun anhand einer realen Fallstudie sehen, wie diese Lösungen anzuwenden sind.
Fallstudie: Eliminierung von Blasen in transparenten Teilen
Um eine einwandfreie optische Klarheit in geformten Visieren zu erreichen, kämpfte ein Hersteller von medizinischen Geräten mit sporadischen Blasen in der Nähe der gebogenen Abschnitte. Durch methodisches Vorgehen bei den Ursachen konnten die Blasen schließlich beseitigt werden.
Schritt 1: Gründliche Trocknung
Trotz der Verwendung von PC, einem hygroskopischen Harz, wurde zuvor keine spezielle Trocknung durchgeführt. Ein Trockenmittel-Radtrockner, der für mindestens 4 Stunden auf 250°F eingestellt war, trocknete die Teile konstant unter 0,1% Feuchtigkeit.
Schritt 2: Abstimmung der Strömungsdynamik
Hohe Einspritzgeschwindigkeiten führten zu Turbulenzen in der Mitte der Füllung, da der einzelne kleine Anschnitt nicht mithalten konnte. Eine Verringerung der Geschwindigkeit ermöglichte eine laminare Strömung, während ein zweiter Anschnitt die Befüllung ausglich.
Schritt 3: Erhöhung der Entlüftungskapazität
Ursprünglich gab es nur zwei winzige Entlüftungsöffnungen für den großen, 14 Zoll großen gebogenen Bereich. Durch das Hinzufügen weiterer breiterer Entlüftungsöffnungen wurde sichergestellt, dass die Gase entweichen können.
Die Kombination von Material-, Werkzeug- und Prozessänderungen gemäß den zuvor beschriebenen Grundlagen führte zu fehlerfreien, blasenfreien Teilen in hohen Stückzahlen.
Durch die Beseitigung der verschiedenen Ursachen für die Blasenbildung mit maßgeschneiderten Lösungen konnte dieser Hersteller eine präzise Klarheit erreichen, die den strengen medizinischen Standards entspricht. Der Schlüssel lag in der korrekten Identifizierung und Beseitigung der Ursachen.
Ausarbeitung einer Präventionsstrategie
Während Korrekturen nach der Produktion eine gewisse Wirkung haben, erfordert die dauerhafte Verhinderung von Blasen einen vorgelagerten Ansatz:
- Überprüfung der optimalen Vortrocknungsprotokolle für jedes Material
- Gehen Sie vorsichtig mit den Harzen um, um das Einatmen von Luft zu vermeiden.
- Planen Sie konservative Injektionsfüllraten
- Genaue Überwachung der Schussmengen
- Verbesserte Entlüftung für optimalen Luftabzug
- Ausreichende Formwärme für die Entlüftungszeit zulassen
Anstatt reaktiv die Symptome zu bekämpfen, stoppt diese proaktive Philosophie die Blasen an der Quelle und sorgt so für eine einwandfreie, widerstandsfähige Produktion. Nur ein paar kleine Änderungen machen einen großen Unterschied!
In Verbindung mit einer robusten Prozesssteuerung und wissenschaftlicher Formgebung wird die Blasenfreiheit zu einem erreichbaren Maßstab, der zu einer perfekten Oberflächenqualität und optimaler struktureller Integrität führt.
Durch eine fundierte, ursachenbezogene Betrachtung von Blasenfehlern können Kunststoffverarbeiter von der Bekämpfung von Blasen zu ihrer völligen Beseitigung durch grundlegende Best Practices übergehen. Das Ergebnis ist maximale Leistung und Ästhetik.