Schweißnähte sind einer der häufigsten Fehler bei spritzgegossenen Kunststoffteilen. Wenn zwei Fließfronten des geschmolzenen Kunststoffs in der Form zusammenlaufen, verschmelzen sie möglicherweise nicht vollständig miteinander. Das Ergebnis ist eine sichtbare Linie auf dem Teil, die als Schweißnaht bezeichnet wird und auf eine Schwachstelle hinweist. Als Fachmann Kunststoff-Spritzguss Hersteller, werde ich 4 Ursachen für Schweißnahtfehler und einige Lösungen zu deren Vermeidung vorstellen.
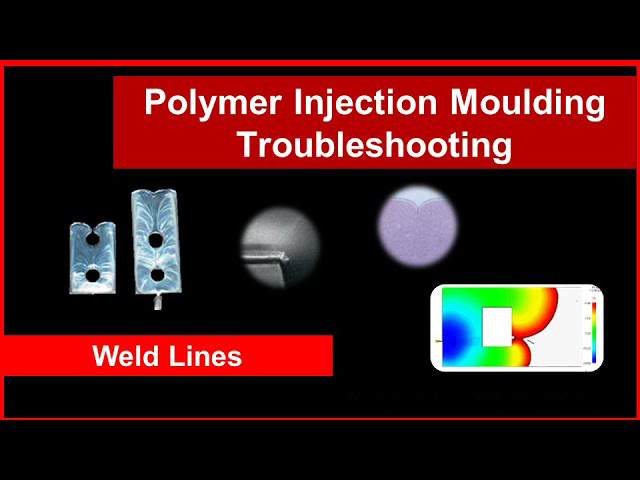
Warum Schweißnähte bei Spritzgussteilen wichtig sind
Auf den ersten Blick, Bindenähte mögen wie ein rein kosmetisches Problem erscheinen. In Wirklichkeit wirken sie sich jedoch negativ auf die Festigkeit und Haltbarkeit von Spritzgussteilen aus.
Kunststoffteile mit Schweißnahtfehlern sind beispielsweise anfälliger für Risse oder Brüche an diesen Stellen, wenn sie unter Spannung stehen. Diese Zerbrechlichkeit stellt ein Sicherheitsproblem für Produkte wie Automobilteile oder medizinische Geräte dar.
Außerdem verzerren Schweißnähte das ästhetische Erscheinungsbild von Gegenständen, bei denen die Oberflächenbeschaffenheit wichtig ist. So können sie die kommerzielle Attraktivität von Konsumgütern wie Elektronikgehäusen oder Spielzeugbausteinen beeinträchtigen.
Es liegt auf der Hand, dass Bindenähte funktionelle und wirtschaftliche Folgen haben, die Hersteller nicht ignorieren können. Untersuchen wir, was sie während des Spritzgießprozesses verursacht.
Was sind die Ursachen für Schweißnähte beim Spritzgießen? 4 Grundursachen
Bei der Durchführung von Spritzgießvorgängen können sich die Kunststofffronten in verschiedenen Situationen trennen und wieder zusammenführen:
1. Hindernisse im Formhohlraum
Löcher, Kanten, Einsätze und andere Hindernisse in den Formwerkzeugen lenken den Fluss der Kunststoffschmelze vorübergehend in zwei oder mehr Richtungen ab. Wenn sich die Ströme auf der Rückseite des Hindernisses wieder vereinigen, verhindern unzureichende Temperatur oder Druck, dass sie sich wieder zu einer homogenen Schmelze vereinigen.
Kernstifte, die zur Herstellung von Innenöffnungen wie Löchern oder Gewinden verwendet werden, sind häufige Ursachen für Bindenähte. Ein weiteres Beispiel sind seitlich wirkende Nocken und Schieber, die sich während des Einspritzens zurückziehen und vor dem Erstarren in den Formhohlraum ausfahren.
2. Mehrkavitäten-Werkzeuge
Bei Werkzeugen mit zwei oder mehr separaten Kavitäten mit speziellen Anschnittpunkten wird der Einspritzdruck naturgemäß aufgeteilt. Diese geteilte Strömung läuft auf dem Weg zu den Kavitäten irgendwo im Kanalsystem zusammen. Die Stelle, an der der Druck zusammenläuft, führt in der Regel zu wiederkehrenden Bindenähten von Teil zu Teil.
Auch wenn eine Minimierung der Anschnitte hilfreich sein kann, weisen die meisten Mehrkavitätenformen bis zu einem gewissen Grad Schweißnähte auf. Erfahrene Formenbauer werden versuchen, diese während der Konstruktion in unauffälligen, unkritischen Bereichen zu platzieren.
3. Ungleichmäßiger Wandbestand
Wenn Kunststoffteile sowohl dick- als auch dünnwandige Abschnitte enthalten, erstarren die Schmelzfronten, die durch diese Bereiche fließen, unterschiedlich schnell. Die langsamere dickwandige Strömung und die schnellere dünnwandige Strömung treffen schließlich stromabwärts aufeinander und vereinigen sich möglicherweise nicht richtig.
Plötzliche Übergänge in der Wandstärke wirken selbst wie Strömungshindernisse und spalten den Schmelzestrom, bis er sich auf der Rückseite wieder vereinigt. Eine allmähliche Verjüngung von Dickenänderungen ermöglicht eine gleichmäßigere Fließkonvergenz mit geringerem Schweißnahtrisiko.
4. Unsachgemäße Entlüftung
Eingeschlossene Gase stellen ein weiteres Hindernis dar, um zwei Schmelzeströmungen im Formhohlraum in Einklang zu bringen. Ohne angemessene Entlüftung werden Lufttaschen zwischen den konvergierenden Strömungen komprimiert, anstatt aus dem Werkzeug zu entweichen.
Dies führt zu einer lokal begrenzten heißen Stelle, die durch die schnelle Verdichtung des Gases entsteht. In extremen Fällen verschlechtert die erhöhte Temperatur den Kunststoff Polymerund hinterlässt einen verräterischen schwarzen oder braunen Brandfleck. In harmloseren Fällen mit geringem Lufteinschluss ist die ordnungsgemäße Verschmelzung zwischen den Fließschichten immer noch unterbrochen, was zu einem haarfeinen Schweißfehler führt.
Wie man Schweißnähte beim Spritzgießen vermeidet
Idealerweise sollten die Teile so konstruiert sein, dass Strömungshindernisse und -störungen gänzlich vermieden werden. Bei den meisten handelsüblichen Artikeln sind jedoch einige Unregelmäßigkeiten unvermeidbar.
Glücklicherweise können Anpassungen an den Werkzeugen und optimierte Verarbeitungsparameter das Auftreten von Bindenähten minimieren:
- Erhöhen Sie die Einspritzgeschwindigkeit, um heißere Schmelzfronten für besseres Fließschweißen zu erzielen.
- Erhöhen Sie den Einspritzdruck, um die turbulente Durchmischung der konvergierenden Fronten zu verbessern.
- Erhöhen Sie die Zylindertemperaturen, um die Viskosität zu verringern und die Schmelzfähigkeit zu verbessern.
- Verschieben Sie die Anschnittpositionen, um Schweißfehlerbereiche an Teilen zu ändern.
- Fügen Sie Entlüftungsöffnungen hinzu, vergrößern Sie die Abstände und verbessern Sie die Abluftwege in problematischen Schimmelbereichen.
- Verwenden Sie Heißkanalsysteme, um höhere Schmelzetemperaturen während der gesamten Hohlraumbefüllung aufrechtzuerhalten.
- Standardisieren Sie die Unterschiede zwischen dicken und dünnen Wandabschnitten.
- Senken Sie den Spitzeneinspritzdruck schrittweise mit einer Geschwindigkeits-/Druckübertragungseinstellung.
- Erhöhen Sie die Formtemperatur, um die Abkühlung zu verlangsamen und die Fließschmelzzeit zu verlängern.
Auch wenn bei einigen Spritzgussteilen nach der Umsetzung dieser Maßnahmen winzige Bindenähte verbleiben können, besteht das Ziel darin, ihre Größe und Lage zu kontrollieren. Dadurch werden größere Schwachstellen oder optische Mängel vermieden.
Die sorgfältige Inspektion von Vorproduktionsmustern liefert wertvolles Feedback, um die optimalen Prozesseinstellungen und die Steuerung der Materialzufuhr zu verbessern. Durch diese Einarbeitung wird die Prävalenz der Schweißlinie vor den offiziellen Produktionsläufen reduziert.
Schlussfolgerung
Zusammenfassend lässt sich sagen, dass Bindenähte überall dort auftreten, wo sich zwei Fließfronten während der Füllung der Kavität beim Spritzgießen nicht wieder vereinigen können. Zu den häufigsten Ursachen gehören Hindernisse im Werkzeug, Mehrfachanschnitte, unebene Wände und schlechte Entlüftung.
Während kleine Schweißnähte nur die Ästhetik beeinträchtigen, gefährden größere Schweißnähte die Festigkeit und Funktion des Teils an diesen Stellen. Sorgfältig konstruierte Formen und verfeinerte Verarbeitungsparameter minimieren problematische Fließtrennungen. Das Ergebnis sind gleichmäßigere, fehlerfreie Kunststoffteile.
Was glauben Sie, verursacht die meisten Probleme mit der Bindenaht bei Ihren Spritzgießanwendungen? Sind visuelle Defekte oder funktionelle Beeinträchtigungen besorgniserregender? Teilen Sie uns Ihre Erfahrungen und Gedanken mit!