Das Spritzgießen ist ein Fertigungsverfahren, mit dem Kunststoffteile in großen Mengen hergestellt werden. Dabei wird Kunststoffgranulat geschmolzen und der geschmolzene Kunststoff in einen Formhohlraum gespritzt, wo er abkühlt und zur endgültigen Form des Teils erstarrt.
Eine der wichtigsten Komponenten einer Spritzgießform ist das Angusssystem, das den geschmolzenen Kunststoff von der Düse der Spritzgießmaschine zu den Kavitäten in der Form befördert. Der Angusskanal kann beheizt sein oder unbeheizt bleiben.
A Heißkanal ist ein beheiztes Fördersystem, das den Kunststoff beim Einfließen in die Formhohlräume in der Schmelze hält. Mit Heißkanälen lassen sich Teile schneller und mit weniger Abfall herstellen als mit herkömmlichen Kaltkanalwerkzeugen. Als Profi Hersteller von Kunststoff-SpritzgussteilenIn diesem Beitrag werde ich alles über Heißkanäle beim Spritzgießen erzählen.
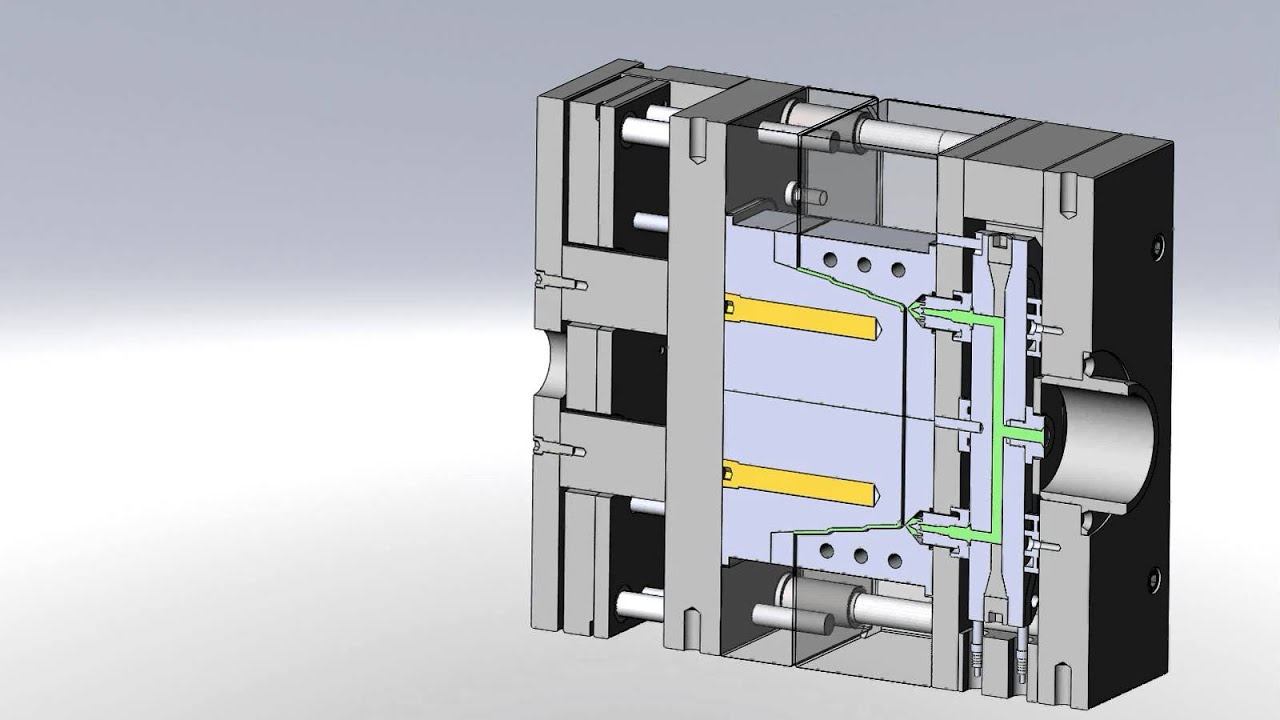
Was genau ist ein Heißkanal?
Ein Heißkanal besteht aus einem beheizten Verteiler und einer Reihe von beheizten Düsen. Die Hauptaufgaben sind:
- Verteilen Sie den geschmolzenen Kunststoff, der in die Form gelangt, auf mehrere Düsenspitzen
- Präzise Dosierung des Kunststoffs in jede Kavität durch Einspritzpunkte an den Düsenspitzen
Der Heißkanalverteiler und die Düsen bleiben beheizt, so dass der Kunststoff auf seinem Weg in die Formhohlräume geschmolzen bleibt.
Sobald die Kavitäten gefüllt sind, wird das Teil abgekühlt und wie bei einem Kaltkanalsystem ausgestoßen. Der Unterschied ist, dass nach jedem Zyklus kein fester Kunststoff im Heißkanal verbleibt.
Heißkanalsysteme vermeiden Kunststoffabfälle vollständig. Außerdem verkürzen sie die Zykluszeiten, da ein großer Kunststoffbatzen nicht in einem Kaltkanal gekühlt werden muss.
Komponenten des Heißkanalsystems
Ein grundlegendes Heißkanalsystem besteht aus:
- Verteiler - Verteilt die Schmelze an die Düsen
- Düsen - Präziser Anschnitt des Kunststoffs in jede Kavität
- Heizungen - Heizelemente, die die Temperatur aufrechterhalten
- Steuerungen - Überwachung und Steuerung von Verteiler-/Düsenheizungen
Komplexere Systeme enthalten auch zusätzliche Komponenten wie Düsenspitzen, Nadelverschlüsse, Filter usw.
Heißkanal vs. Kaltkanal
Kaltkanäle verwenden unbeheizte Kanäle, um den Kunststoff in die Formhohlräume zu befördern. Nach jedem Zyklus muss der kalte Kunststoffballen in den Kanälen zusammen mit den Teilen ausgestoßen werden.
Die Vorteile von kalten Läufern:
- Geringere Anfangskosten
- Unterbringung von mehr Materialtypen
- Leichteres Ändern von Kufenlayouts
Die Nachteile sind längere Zykluszeiten, Kunststoffabfälle und eine geringere Teilequalität.
Heißkanäle bieten vollständige Schmelzkontrolle, schnellere Zyklen und keinen Kunststoffabfall. Der Nachteil sind höhere Anschaffungskosten und Wartungsanforderungen.
Langfristig gesehen amortisieren sich Heißkanalsysteme oft von selbst:
- Schnellere Produktionsraten
- Geringere Energie- und Materialkosten
- Hochwertige Teile
Arten von Heißkanalsystemen
Es gibt zwei Hauptkonfigurationen von Heißkanälen:
1. Innerbetrieblich beheizt
Interne Heizelemente sind in die Heißkanalkomponenten eingebettet. Dies ermöglicht präzise thermische Profile und eine hervorragende Prozesssteuerung.
Am häufigsten bei technischen Harzen wie ABS, PC, Nylon, wenn enge Toleranzen erforderlich sind.
2. Extern beheizt
Externe Heizelemente werden an der Außenseite der Heißkanalkomponenten angebracht. Besser geeignet für thermisch empfindliche Materialien wie PVC und PET.
Außerdem ermöglichen sie im Vergleich zu internen Designs schnellere Farbwechsel.
Heißkanalanschnitt-Typen
Der Anschnitt ist der Punkt, an dem der Kunststoff in den Formhohlraum eintritt. Heißkanäle verwenden entweder einen Heißspitzenanschnitt oder einen Nadelverschluss.
Hot Tip Gates
Eine beheizte Düsenspitze spritzt den Kunststoff durch einen offenen Anschnitt in die Kavität. Nach dem Einspritzen friert der Kunststoff im Anschnitt auf natürliche Weise ab.
Vorteile: Einfach, kostengünstig, kleiner Torrest
Nachteile: Geringere Prozesskontrolle, Potenzial für Stringing
Absperrschieber
Ein Ventilstift öffnet und schließt den Schieber schnell, um den Durchfluss zu starten und zu stoppen. So entsteht ein sauberer Schieber ohne Rückstände oder Fäden.
Nadelverschlüsse bieten die beste Leistung für anspruchsvolle Harze und strenge Qualitätsanforderungen.
Vorteile von Heißkanälen
Heißkanalsysteme bieten eine vollständige Kontrolle der Schmelze von der Maschinendüse bis zum Formhohlraum. Dies ermöglicht:
- Schnellere Formgebungszyklen
- Höhere Produktionsleistung
- Verringerung des Kunststoffabfalls
- Verbesserte Qualität und Konsistenz der Teile
- Größere Gestaltungsfreiheit
Heißspitzen- und Nadelverschlussdesigns dosieren den Kunststoff durch Präzisionsanschnitte in die Formkavitäten. Durch eine intelligente Anschnittplatzierung werden kosmetische Makel an den fertigen Kunststoffteilen vermieden.
Wann werden Heißkanäle verwendet?
Jede Anwendung mit mehr als 1 Million Zyklen pro Jahr ist ein guter Kandidat für Heißkanäle. Die Vorteile vervielfachen sich bei Werkzeugen mit höheren Kavitätenzahlen.
Typische Heißkanalanwendungen:
- Großvolumige Kunststoffteile - Verschlüsse, Becher, Kappen, Deckel
- Medizinisches Verbrauchsmaterial - Pipettenspitzen, Spritzenteile
- Elektrische Steckverbinder und Verkapselungen
- Technische Präzisionsteile
Größere Heißkanalsysteme mit 128+ Tropfen werden zur Herstellung von Milliarden von Flaschenverschlüssen und anderen großvolumigen Kunststoffteilen verwendet.
Schlussfolgerung
A Heißkanal hält den geschmolzenen Kunststoff heiß, wenn er direkt in die Formhohlräume fließt, ohne in einem Angusskanal abzukühlen. Dadurch wird Kunststoffabfall vermieden und die Zykluszeiten werden beschleunigt.
Das Heißkanalspritzgießen verbessert die Teilequalität, senkt die Produktionskosten und erhöht die Fertigungseffizienz. Bei richtiger Konstruktion und Verarbeitung führen Heißkanäle langfristig zu erheblichen Einsparungen gegenüber dem Kaltkanalverfahren.