Was ist die Schmelzetemperatur beim Spritzgießen? Als einer der wichtigsten Prozessparameter ist die richtige Schmelzetemperatur der Schlüssel zur effizienten Herstellung hochwertiger Kunststoffteile. In diesem vollständigen Leitfaden werden Sie als Fachmann Hersteller von Kunststoff-Spritzgussteilenerkläre ich Ihnen alles, was Sie über die Schmelztemperatur wissen müssen, einschließlich:
- Was ist die Schmelztemperatur?
- Warum die Kontrolle der Schmelztemperatur wichtig ist
- Wie sich die Schmelztemperatur auf die Eigenschaften der Teile auswirkt
- Bewährte Verfahren zur Einstellung und Messung der Schmelztemperatur
- Die Beziehung zwischen Schmelz- und Werkzeugtemperaturen
Am Ende werden Sie ein solides Verständnis dieses grundlegenden Konzepts haben, so dass Sie Ihre Spritzgießprozesse besser steuern können. Legen wir los!
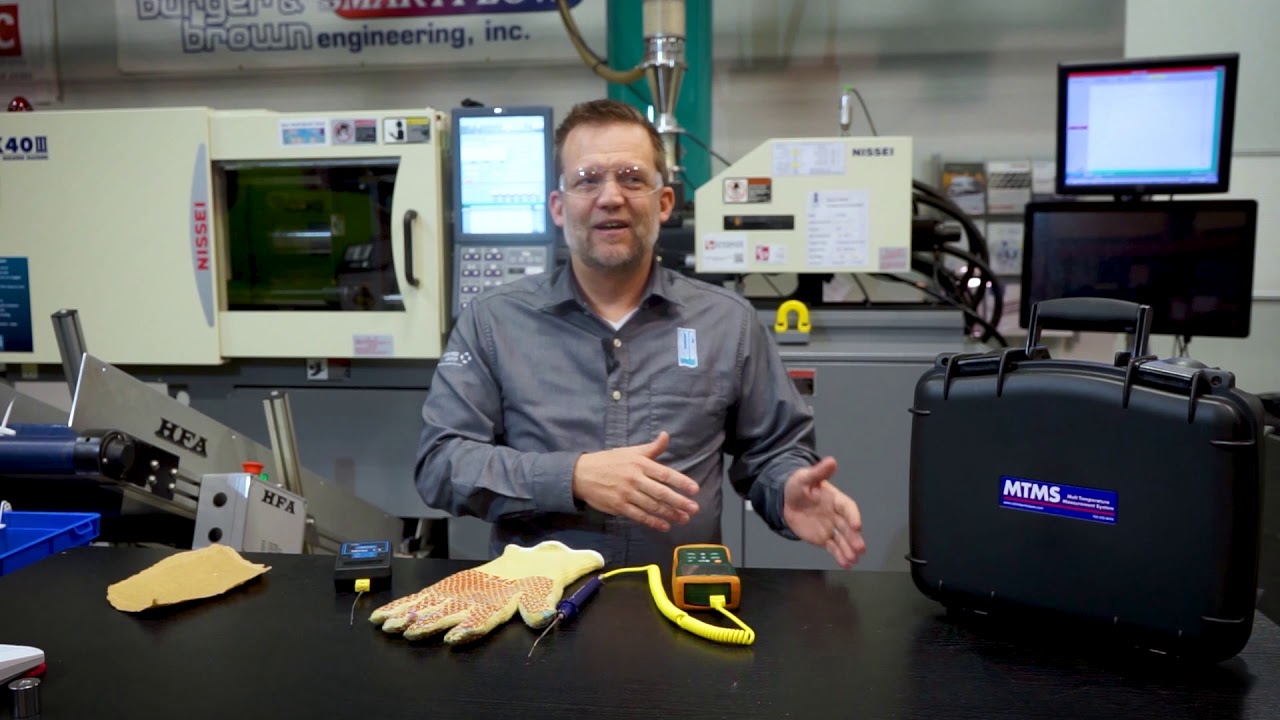
Was ist die Schmelztemperatur beim Spritzgießen?
Die Schmelzetemperatur bezieht sich auf die tatsächliche Temperatur des geschmolzenen Kunststoffs, wenn er aus der Düse der Spritzgießmaschine austritt und in die Form eintritt. Diese Temperatur kann aufgrund der Schererwärmung und anderer Faktoren erheblich von den Solltemperaturen des Zylinders abweichen.
Die richtige Schmelztemperatur ist von entscheidender Bedeutung, denn sie beeinflusst die Viskosität des Kunststoffs, wie leicht er in die Form fließt und die Eigenschaften des fertigen Teils. So kann eine zu hohe Schmelzetemperatur das Polymer zersetzen, während eine zu niedrige Temperatur das Fließen behindern und zu kurzen Schüssen führen kann.
Im Allgemeinen benötigen amorphe Harze wie ABS und PC höhere Schmelztemperaturen, während teilkristalline Harze wie PP und HDPE bei niedrigeren Temperaturen besser fließen. Die optimale Schmelztemperatur hängt jedoch von der jeweiligen Sorte ab, die verarbeitet wird.
Warum ist die Kontrolle der Schmelztemperatur so wichtig?
Die Schmelzetemperatur wirkt sich auf mehrere kritische Ziele beim Gießen aus:
Teil Qualität: Eine von der Spezifikation abweichende Schmelztemperatur kann die Viskosität und das Molekulargewicht des Harzes verändern, was zu Defekten, Dimensionsinstabilität, Eigenschaftsschwankungen und anderen Qualitätsproblemen führen kann.
Effizienz: Eine falsche Schmelztemperatur verlängert die Zykluszeiten und führt zu einem geringeren Ausstoß. Sie kann auch die Materialeigenschaften mit der Zeit verschlechtern.
Konsistenz: Selbst kleine Schwankungen der Schmelztemperatur können zu inakzeptablen Abweichungen zwischen den einzelnen Chargen führen.
Es liegt auf der Hand, dass die Beherrschung der Schmelzetemperatur für die Herstellung hochwertiger Teile, die Maximierung der Produktivität und die Gewährleistung der Prozessstabilität unerlässlich ist.
Wie wirkt sich die Schmelztemperatur auf die Eigenschaften eines Teils aus?
Durch die Beeinflussung der Harzviskosität und anderer Eigenschaften ermöglicht die Einstellung der Schmelztemperatur den Verarbeitern eine gewisse Kontrolle über die Eigenschaften der fertigen Teile.
Festigkeit und Stoßfestigkeit: Niedrigere Schmelztemperaturen ergeben im Allgemeinen eine höhere Festigkeit und Schlagzähigkeit. Das kühlere Harz behält während des Formprozesses mehr von seinem Molekulargewicht.
Schrumpfung: Eine zu hohe Schmelztemperatur führt dazu, dass sich der Kunststoff in der Form stärker ausdehnt, was die Schrumpfung erhöht. Geringfügig niedrigere Schmelztemperaturen wirken dem entgegen.
Zykluszeit: Eine geringere Viskosität bei höheren Schmelztemperaturen kann die Formgebungszyklen verkürzen, geht aber in der Regel auf Kosten der Eigenschaften. Es muss ein Gleichgewicht gefunden werden.
Viskosität: Je heißer die Schmelze ist, desto geringer ist ihre Viskosität. Ein zu starkes Absinken der Viskosität birgt jedoch die Gefahr instabiler Fließfrontgeschwindigkeiten.
Durch gezielte Anpassungen der Schmelzetemperatur können die Hersteller die Festigkeit, die Schrumpfung, die Zykluszeiten und andere Eigenschaften der Teile an die Anforderungen der Anwendung anpassen.
Bewährte Praktiken zur Einstellung und Messung der Schmelztemperatur
Für die einzelnen Harze gibt es zwar empfohlene Schmelztemperaturbereiche, aber um die optimale Einstellung zu finden, sind Tests, Feinabstimmung und ständige Wachsamkeit erforderlich. Hier sind einige Tipps:
Fangen Sie niedrig an: Beginnen Sie mit der niedrigsten verarbeitbaren Schmelztemperatur für die jeweilige Materialsorte. Dadurch wird der thermische Abbau minimiert, während Sie die anderen Parameter einstellen. Sobald sich der Prozess stabilisiert hat, können Sie die Schmelzetemperatur langsam erhöhen, um die Viskosität oder die Zyklen zu verringern.
Verwenden Sie eine aktuelle Ausrüstung: Schmelztemperaturregler mit Thermoelement oder RTD-Sensoren, die in der Düse eingebettet sind und eine kontinuierliche Messung ermöglichen, eliminieren Rätselraten und beschleunigen die Optimierung.
Messen Sie systematisch: Wenden Sie bei jeder Überprüfung der Schmelztemperatur das gleiche Verfahren an (z. B. Spülen in einen isolierten Behälter), um Konsistenz zu gewährleisten. Automatisierte Inline-Messsysteme liefern die besten Daten.
Führen Sie Aufzeichnungen: Zeichnen Sie alle Prozessparameter zusammen mit der Schmelztemperatur auf, damit Sie Trends im Laufe der Zeit genau analysieren können. Für jede Veränderung sollte es einen nachvollziehbaren, quantitativen Grund geben.
Die Überwachung und Kontrolle der Schmelztemperatur ist mühsam, zahlt sich aber durch Qualität, Effizienz und Stabilität aus. Die Befolgung strukturierter Verfahren und der Einsatz intelligenter Technologien erleichtern die Arbeit und liefern gleichzeitig wertvolle Prozessdaten.
Wie ist das Verhältnis zwischen Schmelz- und Formtemperaturen?
Schmelz- und Werkzeugtemperaturen sind von Natur aus voneinander abhängig, auch wenn sie unabhängig voneinander eingestellt werden.
Zu den wichtigsten Zusammenhängen zwischen diesen beiden entscheidenden Spritzgießparametern gehören:
Scherheizung: Die Reibungswärme, die beim Fließen der Schmelze durch den Anguss und die Angusskanäle entsteht, erhöht die Oberflächentemperaturen der Form. Schnellere Zyklen verstärken diesen Effekt.
Effizienz der Kühlung: Wie schnell die Schmelze in der Form abkühlt, hängt unter anderem vom Temperaturgefälle zwischen dem Kunststoff und der Formoberfläche ab. Große Deltas fördern die Abkühlung.
Polsterung: Eine leichte Abweichung zwischen heißerer Schmelze und kühleren Werkzeugtemperaturen bietet einen hilfreichen Puffer, der verhindert, dass die Mindestviskosität des Materials unterschritten wird oder das Material gefriert, bevor die Kavität gefüllt ist.
Immobilienoptimierung: Wie bei den meisten Verarbeitungsvariablen maximiert die ideale Kombination von Schmelz- und Formtemperaturen die Qualität und Effizienz. Um den "Sweet Spot" für jedes Material zu finden, sind einige Versuche und Fehler erforderlich.
Schmelz- und Formtemperaturen mögen zwar unterschiedlich erscheinen, doch ist es wichtig, beide ganzheitlich zu betrachten. Das Gesamtenergiebild ist wichtiger als jede einzelne Komponente. Modellierungssoftware kann nützliche Hinweise zur Optimierung dieses Gleichgewichts liefern.