Das Kunststoffspritzgießen hat die Fertigung revolutioniert. Dieses zentrale Verfahren stellt mit Hilfe von Spezialmaschinen alles her, von Legos bis zu iPhone-Hüllen. Aber was genau ist Kunststoffspritzguss? Und welche Rolle spielt es in der Weltwirtschaft?
In diesem vollständigen Leitfaden finden Sie als Fachmann Hersteller von Kunststoff-Spritzgussteilenwerden wir den Prozess des Kunststoffspritzgießens Schritt für Schritt erläutern. Außerdem erfahren Sie, warum sich große Hersteller bei der Massenproduktion von Kunststoffprodukten auf das Spritzgießen verlassen.
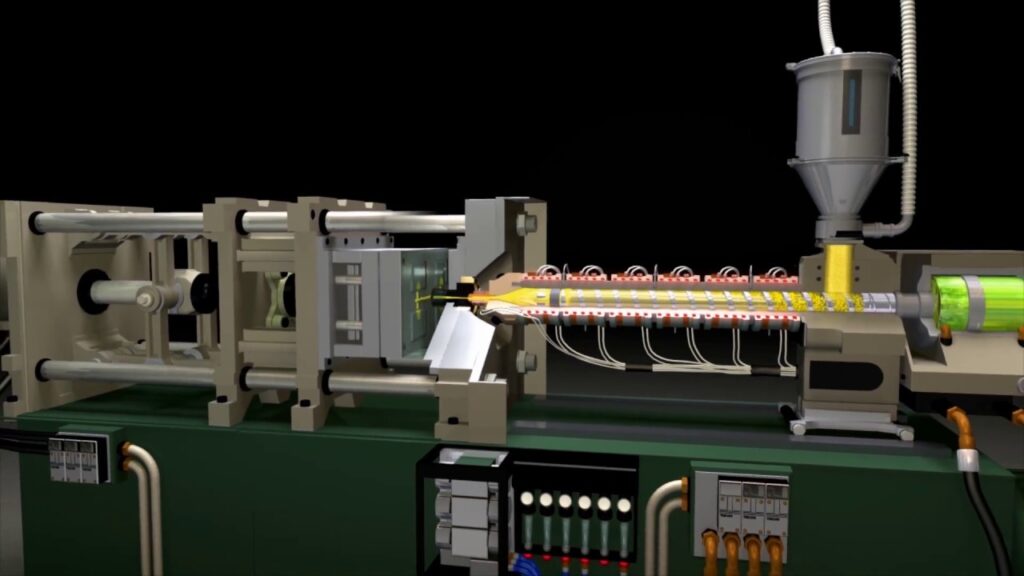
Was ist das Kunststoff-Spritzgießverfahren?
Das Kunststoff-Spritzgießen ist ein Fertigungsverfahren, bei dem Kunststoffgranulat in vollständig geformte Teile umgewandelt wird. Spezialisierte Maschinen schmelzen Kunststoff und spritzen ihn unter hohem Druck in kundenspezifische Stahlformen. Nachdem der Kunststoff abgekühlt und ausgehärtet ist, öffnet sich die Form und gibt das neu entstandene Produkt frei.
Dieses großvolumige Verfahren macht das Kunststoffspritzgießen ideal für die Massenproduktion. In der Tat nutzen Hersteller dieses Verfahren, um jedes Jahr Milliarden identischer Kunststoffteile zu produzieren. Zu den gängigen Spritzgussteilen gehören Flaschenverschlüsse, Angelköder und sogar medizinische Geräte. Auch die Automobilindustrie nutzt diese Technik, um komplizierte Teile für das Armaturenbrett herzustellen.
Die 4 Schritte des Kunststoff-Spritzgießverfahrens
Die Kunststoff-Spritzgießverfahren kann in vier Hauptschritte unterteilt werden:
- Klemmen
- Einspritzung
- Kühlung
- Auswurf
Damit ist der gesamte Formgebungszyklus gemeint, der sich wiederholt, um ein Teil nach dem anderen in einem Großserienverfahren herzustellen.
Schritt 1: Einspannen
Zu Beginn des Spritzgießvorgangs schließen sich die beiden Hälften der Spritzgussform und bilden den Formhohlraum. Die Formhälften werden unter Druck sicher zusammengeklemmt, um die Form während des Einspritzvorgangs geschlossen zu halten.
Zugstangen außerhalb der Form verbinden die feststehende Hälfte mit der beweglichen Hälfte, um die Steifigkeit zu gewährleisten und dem Druck während des Schließvorgangs standzuhalten.
Schritt 2: Injektion
Nachdem die Form sicher geschlossen ist, wird im nächsten Schritt der geschmolzene Kunststoff in den Formhohlraum eingespritzt. Die Einspritzeinheit der Spritzgießmaschine besteht aus einem Trichter, einem Zylinder, einer Schnecke und einer Düse.
Die Kunststoffpellets werden aus dem Trichter in den Zylinder befördert. Die Schnecke dreht sich und bewegt sich rückwärts, sodass die Pellets eintreten und sich vorwärts bewegen können.
Leistungsstarke Heizbänder schmelzen das Kunststoffgranulat bei hohen Temperaturen. Während sich die Schnecke vorwärts bewegt, baut sie genügend Druck auf, um geschmolzenen Kunststoff durch die Düse in den Formhohlraum zu spritzen.
Schritt 3: Kühlung
Nach dem Füllen der Kavität wird der Nachdruck aufrechterhalten, damit der Anschnitt erstarrt und der geschmolzene Kunststoff nicht zurückfließt. Dieses Packen geschieht bei optimaler Temperatur und optimalem Druck.
In dieser Phase führen Kühlkanäle das Kühlmittel um die Formoberfläche herum, um den geschmolzenen Kunststoff zu verfestigen. Die genaue Kühlzeit hängt von der Wandstärke und der Komplexität des Kunststoffteils ab. Dickere Wände benötigen einen längeren Kühlzyklus.
Eine ordnungsgemäße Temperaturregelung ist für eine gleichmäßige Abkühlung unerlässlich. Dadurch werden Fehler durch schnelles Abkühlen und lange Zyklen durch langsames Abkühlen vermieden.
Schritt 4: Auswurf
Wenn die Temperatur sinkt, ist das erstarrte Teil bereit, entnommen zu werden. Die Klemmkraft, die die beiden Hälften zusammenhält, lässt nach und die Form öffnet sich.
Schließlich drücken Auswerferstifte die fertigen Kunststoffteile aus dem Formhohlraum heraus, so dass der Bediener die Teile aus der Formmaschine entnehmen kann. Die Form schließt sich wieder, der Produktionszyklus wiederholt sich und ein neues Kunststoffteil nimmt Gestalt an.
Erforderliche Werkzeuge für das Kunststoff-Spritzgießverfahren
Für das Spritzgießverfahren werden eine Spritzgießmaschine und eine Form benötigt. Die Form wird in der Spritzgießmaschine befestigt und nimmt den geschmolzenen Kunststoff auf, um Teile zu formen.
Spritzgießmaschine - Sie enthält einen Trichter, einen Zylinder, Heizeinheiten, einen Stempel, eine Form und eine Schließeinheit. Die neueren vollelektrischen Maschinen sind in horizontaler und vertikaler Ausführung erhältlich und bieten höchste Präzision und Energieeffizienz. Die Pressengrößen reichen von 5 bis über 6.000 Tonnen Schließkraft.
Schimmelpilz - Formen haben einen Hohlraum mit der genauen Geometrie des endgültigen Teils. Sie können einen einzigen Hohlraum oder mehrere Hohlräume für die Großserienproduktion haben. Kanäle werden für die Kühlung der Form, das Auswerfersystem usw. bearbeitet. Komplexe Formen können Schieber, Nocken, Drehtische und andere Vorrichtungen zur Herstellung komplizierter Kunststoffteile haben.
Rohmaterial für das Spritzgießen
Es gibt eine breite Palette von thermoplastische Polymere die sich für Spritzgussanwendungen eignen. Zu den gängigsten gehören Polyethylen (PE), Polyvinylchlorid (PVC), Polystyrol (PS), Acrylnitril-Butadien-Styrol (ABS) und Polypropylen (PP).
Diese Kunststoffe sind in Granulatform für das Spritzgießen erhältlich. Die Hersteller können verschiedene Füllstoffe, Verstärkungsstoffe, Schmiermittel, Farbstoffe, Flammschutzmittel und andere Additive verwenden, um die Materialeigenschaften zu verändern.
Sie wählen den optimalen Kunststofftyp je nach mechanischen Eigenschaften, Temperaturbeständigkeit, chemischer Beständigkeit, Farboptionen, speziellen Leistungszusätzen und anderen Anforderungen an die fertigen Bauteile aus.
Vorteile des Kunststoffspritzgießens
Das Kunststoffspritzgießen bietet einzigartige Fertigungseffizienzen, die es in vielen Branchen zu einem bevorzugten Produktionsverfahren machen. Hier sind einige seiner Vorteile:
Produktion großer Mengen - Ist die Spritzgießmaschine einmal eingerichtet, kann sie an einem einzigen Tag Tausende von identischen Kunststoffteilen herstellen. Die Automatisierung ermöglicht eine Massenproduktion rund um die Uhr. Die Teilekosten sind niedrig.
Feintoleranzen - Beim Spritzgießen können engere Toleranzen eingehalten werden als bei konkurrierenden Verfahren wie CNC-Bearbeitung oder Gießen. Die Teile weisen ein hohes Maß an Präzision auf, mit geringen Abweichungen zwischen den Teilen.
Material Vielseitigkeit - Thermoplastische Polymere bieten eine enorme Vielfalt an mechanischen Eigenschaften, Ästhetik, chemischer Beständigkeit, Leistung usw. Die Teile können eingefärbt, gefüllt oder für besondere Eigenschaften verändert werden. Recycelte Kunststoffe senken die Kosten.
Komplexe Geometrien - Mehrkavitätenformen, die die Techniken der Seitenbewegung, des Herausdrehens und des Einfallkerns verwenden, können hochkomplexe Teile herstellen, ohne dass eine Nachbearbeitung erforderlich ist.
Montage Konsolidierung - Beim Insert Molding werden vormontierte Komponenten während der Produktion in ein Kunststoffteil eingesetzt. Bei Multi-Shot-Techniken werden nacheinander verschiedene Kunststoffe gespritzt. Dies vereinfacht die Produktmontage.
Schnelle Produktion - Sobald Form und Maschine eingerichtet sind, sind die Produktionsraten beim Spritzgießen wesentlich schneller als bei Alternativen wie CNC-Bearbeitung oder 3D-Druck. Die Aufnahmen dauern Sekunden oder Minuten. Die 24/7-Automatisierung maximiert die Produktionsplanung.
Weniger Arbeit - Die Automatisierung von Spritzgießsystemen senkt die Arbeitskosten erheblich. Roboter handhaben sogar fertige Teile. Ein Bediener kann mehrere Maschinen/Formen verwalten und die Teilehandhabungssysteme überwachen.
Grenzen des Kunststoff-Spritzgießens
Trotz der Möglichkeit der Massenproduktion hat das Kunststoffspritzgießen gewisse Grenzen:
Hohe Schimmelpilzkosten - Präzisionsstahlformen haben hohe Anschaffungskosten. Aluminiumformen haben niedrigere Kosten für kurze Produktionsläufe, können aber keine langen Zyklen überstehen. Bei höheren Stückzahlen verteilen sich die Werkzeugkosten jedoch auf die insgesamt produzierten Teile.
Materialabfall - Ausschussteile können 5-10% nach Gewicht betragen. Angüsse, Angusskanäle und Anschnitte enden als Abfall. Gute Konstruktionen optimieren den Materialeinsatz. Granulatoren zerkleinern Angüsse und Angusskanäle zu Mahlgut für die Wiederaufbereitung zu Teilen.
Teil Gewicht - Sehr große Kunststoffteile neigen dazu, unter ihrem eigenen Gewicht durchzuhängen oder sich zu verformen, wenn sie in offenen Formen abkühlen. Die meisten Teile sind auf ein paar Pfund begrenzt, aber mehr, wenn sie hohl sind. Eine beidseitig entkernte Konstruktion verhindert das Durchhängen großer Teile.
Sekundär-Bearbeitung - Einige Aspekte der Form, wie z. B. scharfe Außenecken, müssen nach dem Gießen bearbeitet werden, um ein optimales Ergebnis zu erzielen. Andere sekundäre Vorgänge wie das Einbringen von Gewinden oder die Montage von Einsätzen erfolgen nach dem Gießen.
Anwendungen des Kunststoffspritzgießens
Spritzgegossene Kunststoffe haben die Fertigung in allen Branchen revolutioniert, von der Automobilindustrie bis zur Medizin. Die Verbraucher verwenden spritzgegossene Kunststoffteile in alltäglichen Haushaltsgegenständen.
Hier sind einige wichtige Anwendungen:
Automobilindustrie - Verkleidungen, Stoßstangen, Beleuchtungskomponenten, Flüssigkeitsbehälter, Armaturenbrettgehäuse und Teile für die Belüftung werden in großem Umfang im Spritzgussverfahren hergestellt. Mit neueren Techniken werden hybride Kunststoff-Metall-Verbundwerkstoffe und Spritzgussteile hergestellt.
Elektronik - Gehäuse von Mobilgeräten, Computertastaturen, Fernsehapparate und andere Unterhaltungselektronik sind auf Präzisionskunststoffteile aus dem Spritzgussverfahren angewiesen. Bei diesem Verfahren werden auch winzige elektrische Anschlüsse und Präzisionsgehäuse gegossen.
Medizinische Industrie - Einwegspritzen, Fläschchen, Ventile, Infusionsschläuche, chirurgische Instrumente wie Pinzetten und Diagnosegeräte, die aus für medizinische Geräte entwickeltem Kunststoff geformt werden. Auch für neuere leichte Prothesen werden spritzgegossene Kunststoffe verwendet.
Verpackungsindustrie - Im Spritzgussverfahren werden Kunststoffflaschen, -behälter, -kappen und -verschlüsse, Etuis, Schalen und Beutel für Konsumgüter hergestellt. Bei Lebensmittelverpackungen werden antibakterielle Kunststoffe geformt. Bei Kosmetikverpackungen liegt der Schwerpunkt auf ästhetischen Kunststoffteilen.
Spielzeug - Von Modellbauteilen über Puppen bis hin zu Brettspielteilen bietet das Spritzgießen die Vielseitigkeit und Präzision, die für die Massenproduktion von Spielzeug erforderlich sind. Spielzeug kann komplizierte Produktdesigns nachbilden, die mit den meisten anderen Herstellungsverfahren nicht möglich sind.
Haushaltsgegenstände - Alltägliche Kunststoffprodukte werden im Spritzgussverfahren hergestellt, darunter Aufbewahrungsbehälter, Küchenutensilien, Ventilatoren, Vakuumkomponenten, Organizer, Haushaltsgeräte und Wäschezubehör.
Das Spritzgießen nutzt technische Thermoplaste zur Herstellung einer Vielzahl von Kunststoffteilen für die unterschiedlichsten kommerziellen und privaten Anwendungen!
Fazit
Beim Kunststoff-Spritzgießen werden ausgewählte Kunststoffpolymere mit Hilfe von Formen zu verwendbaren Konsum- und Industrieprodukten umgeformt. Diese großvolumige Fertigungstechnik beruht auf wissenschaftlichen Formgebungsprinzipien, um Präzision, Wiederholbarkeit und hohe Produktionsraten zu erreichen.
Beim Spritzgießen werden körnige thermoplastische Pellets in Formteile verwandelt, indem das Rohmaterial unter kontrollierten Hitze- und Druckbedingungen plastifiziert wird, bevor es in Präzisionsformhohlräume gespritzt wird. Wenn die Teile abkühlen und aushärten, können sie aus den Formen entnommen werden, und der Gießzyklus wiederholt sich automatisch.
Dank der vielseitigen Thermoplaste, der Konsolidierung der Baugruppen zu Teilen, des Präzisionsspritzgießens winziger und komplexer Komponenten und der Automatisierung, die die Produktion maximiert, bietet das Spritzgießen eine außergewöhnliche Fertigungsproduktivität in fast allen Branchen.