Was ist eine Einfallstelle beim Spritzgießen? Dieser häufige Fehler tritt in Form von leichten Vertiefungen auf der Oberfläche von geformten Kunststoffteilen auf. Einfallstellen bilden sich in der Regel an dickeren Abschnitten während des Spritzgießprozesses.
Einfallstellen beeinträchtigen zwar selten die Festigkeit oder Funktion, können aber die Ästhetik eines Teils ruinieren. Bei Produkten, bei denen das Aussehen entscheidend ist, wie z. B. bei Unterhaltungselektronik, sind Einfallstellen inakzeptabel.
In diesem vollständigen Leitfaden finden Sie als Fachmann Hersteller von Kunststoff-SpritzgussteilenIn diesem Kapitel werden wir uns mit den Ursachen von Einfallstellen befassen und erläutern, wie man sie durch eine bessere Teilekonstruktion und -bearbeitung vermeiden kann.
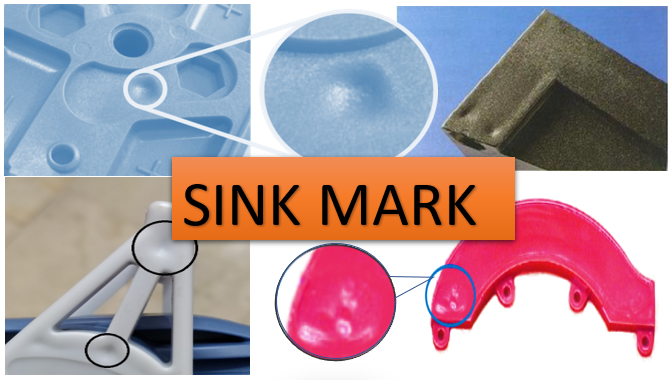
Was ist eine Einfallstelle beim Spritzgießen?
Einfallstellen sind lokale Vertiefungen auf der Oberfläche eines spritzgegossenen Kunststoffteils. Einfallstellen treten typischerweise an dickeren Abschnitten eines Bauteils auf.
Einfallstellen findet man in der Regel an Stellen wie:
- Die Basis der Rippen
- Um Naben und Einsätze herum
- Wo nominell dicke Wände in dünne Wände übergehen
Einfallstellen beim Spritzgießen sehen aus wie eine flache Vertiefung oder ein Grübchen auf der Oberfläche des Teils. Der Defekt reflektiert das Licht anders als der umgebende Bereich, wodurch Einfallstellen leicht zu erkennen sind.
Formteil mit sichtbarer Einfallstelle um die Nabe
Einfallstellen beeinträchtigen zwar nur selten die Leistung, aber sie verschlechtern das Aussehen eines Kunststoffteils. Einfallstellen sind häufige kosmetische Mängel beim Spritzgießen.
Was sind die Ursachen für Senkungsflecken?
Einfallstellen entstehen durch das Spritzgussverfahren selbst. Hier ist ein kurzer Überblick:
- Das Kunststoffgranulat wird in flüssigem Zustand geschmolzen und unter Druck in ein Stahlwerkzeug gespritzt.
- Das Formwerkzeug gibt dem flüssigen Kunststoff die Form des endgültigen Teils.
- Nach dem Füllen des Hohlraums kühlt der Kunststoff ab, bis er fest genug ist, um aus der Form ausgestoßen zu werden.
Durch die natürliche Schrumpfung des abkühlenden Kunststoffs können Senken entstehen. Wenn benachbarte Abschnitte mit sehr unterschiedlichen Geschwindigkeiten abkühlen, erfolgt die Schrumpfung ebenfalls ungleichmäßig.
Die schnellere Abkühlung an der Oberfläche bewirkt, dass das noch flüssige innere Material von der äußeren Schicht "wegsinkt". Das Ergebnis ist eine sichtbare Vertiefung an der Oberfläche, wenn der Kunststoff erstarrt.
Häufige Bereiche für ungleichmäßige Kühlung sind dicke Rippen, Vorsprünge usw. Die zusätzliche Dicke bedeutet eine langsamere innere Kühlung im Vergleich zum umgebenden Kunststoff.
Auch dicke Merkmale schrumpfen aufgrund des größeren Volumens stärker. Wenn benachbarte dünne Abschnitte zuerst "aushärten", können dicke Bereiche beim weiteren Schrumpfen weggezogen werden.
Warum sind Einfallstellen beim Spritzgießen wichtig?
Für die meisten Gießer sind Einfallstellen wichtig, weil sie auf einen kosmetischen Mangel hinweisen. Selbst winzige Vertiefungen reflektieren das Licht auf der Oberfläche des Teils unterschiedlich, so dass Einfallstellen leicht zu erkennen sind.
Das Problem der Sichtbarkeit stellt sich bei Kunststoffteilen, bei denen die Ästhetik im Vordergrund steht. Einfallstellen beeinträchtigen im Allgemeinen nicht die Leistung, aber sie beeinträchtigen die Produktqualität aus optischer Sicht.
Beispiele, bei denen Einfallstellen nicht akzeptabel sind, sind:
- Unterhaltungselektronik
- Gerätetafeln
- Automobilverkleidung
So ziemlich jedes Spritzgussteil, dessen Aussehen die wahrgenommene Qualität oder das Markenimage beeinflusst.
In diesen Fällen ist es wichtig, Einfallstellen zu vermeiden - auch wenn sie noch so klein sind.
Bei anderen Anwendungen wie Industrieteilen oder medizinischen Komponenten sind leichte Mängel nur dann von Bedeutung, wenn sie auf ein zugrunde liegendes Leistungsproblem hinweisen. Aber kosmetische Mängel bleiben in der Regel unbemerkt, wenn das Teil ordnungsgemäß funktioniert.
Vorbeugung gegen Spülsteinbildung
Nun, da wir wissen, warum Einfallstellen entstehen und wo sie auftreten, wie können wir sie verhindern?
Hier sind fünf gängige Methoden, mit denen Spritzgießer Einfallstellen reduzieren oder beseitigen können:
Tipp #1: Packen und Halten optimieren
Packen und Halten bezieht sich auf die Spritzgießphasen nach dem Füllen der Kavität.
Zunächst wird Verpackungsdruck ausgeübt, um zusätzlichen Kunststoff in das Werkzeug zu pressen. Dies hilft, die Schrumpfung beim Abkühlen des Teils auszugleichen.
Die Packphase geht in die Haltephase über, in der der Druck für eine bestimmte Zeit gehalten wird, damit sich dickere Bereiche verfestigen können.
Eine unzureichende Packung und ein unzureichender Halt können definitiv Senkungen verursachen. Aber auch eine zu hohe Packung belastet das Teil zu stark, was zu Verzugsproblemen führt.
Eine vorsichtige Druckeinstellung in Verbindung mit einer ausreichenden Haltezeit hilft am besten, Einfallstellen zu vermeiden.
Tipp #2: Gattergröße erhöhen
Der Anschnitt ist die Öffnung in der Spritzgussform, durch die der Kunststoff in das Werkzeug gelangt.
Ein größerer Anschnitt kann die Senken reduzieren, da er eine schnellere Füllung der Kavität und eine bessere Packung ermöglicht. Allerdings führt dies in der Regel auch zu einem stärkeren Erröten des Anschnitts auf der Oberfläche des Teils.
Es gibt immer Kompromisse!
Tipp #3: Entlüftung hinzufügen
Eingeschlossene Luft verursacht Probleme im Formhohlraum. Da die Kunststoff füllt, komprimiert es das Gas im Hohlraum.
Dieses eingeschlossene Gas will auf dem Weg des geringsten Widerstands entweichen - oft durch den heißen Kunststoff. Das Ergebnis können Brandflecken, Hohlräume und Senken sein.
Durch das Hinzufügen von Entlüftungsöffnungen am Werkzeug kann überschüssiges Gas aus dem Hohlraum entweichen, anstatt in den heißen Kunststoff gepresst zu werden. Eine ordnungsgemäße Entlüftung verhindert Luftblasen und Senken.
Tipp #4: Niedrigere Schmelz- und Formtemperaturen
Um qualitativ hochwertige Teile herzustellen, müssen die Techniker den Kunststoff mit der richtigen Schmelztemperatur einspritzen. Zu hohe Schmelzetemperaturen bedeuten jedoch eine langsamere Abkühlung in der Form.
Dieser Effekt wird durch überhitzte Formoberflächen noch verstärkt. Heiße Formen halten den Kunststoff länger flüssig, was die Schwindungsvariationen erhöht.
Eine sorgfältige Überwachung und Senkung der Schmelz- und Werkzeugtemperaturen hilft, Senken zu vermeiden, indem eine gleichmäßige Abkühlung ermöglicht wird.
Tipp #5: Ändern der Teilekonstruktion
Eine Änderung der Teilegeometrie ist die dauerhafteste Lösung für Einfallstellen.
Übliche Korrekturen sind das Hinzufügen von Rippen, die Reduzierung der Wandstärke oder die Änderung problematischer Merkmale wie Vorsprünge.
Rippen erhöhen die Festigkeit und ermöglichen eine Ausdünnung der angrenzenden Wände. Entkernen Sie schwere Abschnitte, um eine gleichmäßige Abkühlung zu fördern. Alles, um drastische Dickenänderungen zu reduzieren, die eine ungleichmäßige Schrumpfung verursachen.
Die Teilezeichnungen sollten während der Entwurfsphase von einem erfahrenen Gießer geprüft werden. Er kann Problembereiche identifizieren und Änderungen vorschlagen, bevor das Werkzeug gebaut wird.
Schlussfolgerung
Einfallstellen sind eine natürliche Folge des Spritzgießprozesses. Aber wenn man versteht, was ungleichmäßige Abkühlung und Schrumpfung verursacht, können Ingenieure Lösungen finden.
Mit diesen Erkenntnissen können Optimierungen an Werkzeugen, Formen und sogar Teiledesigns die Senkungsfehler an Kunststoffteilen für alle Arten von Anwendungen erheblich reduzieren.