Injection molding is one of the most versatile and cost-effective manufacturing processes for producing plastic parts at scale. From Legos to iPhone cases, countless products we use every day started as molten plastic injected into precision-machined steel molds.
However, injection molding only delivers on its potential if you design parts specifically for the process. Unlike 3D printing or CNC machining, injection molded components have very strict design requirements to fill molds properly, avoid defects, and eject cleanly from the tooling after cooling.
Ignoring injection molding design principles can lead to extensive delays and unnecessary costs at virtually every stage from prototyping through production. And with the process involving expensive steel tooling, design changes after mold fabrication can be extremely time-consuming and costly.
Throughout this comprehensive guide, as a professional injection molding manufacturer, I’ll share my best tips and strategies for designing plastic parts for injection molding success. You’ll learn about critical design considerations like uniform wall thickness, draft angles, rib and boss design, material shrinkage, surface finishing, and much more.
Let’s start with the basics of the injection molding process itself. Understanding precisely how molten plastic flows into cavities will help many design guidelines make sense.
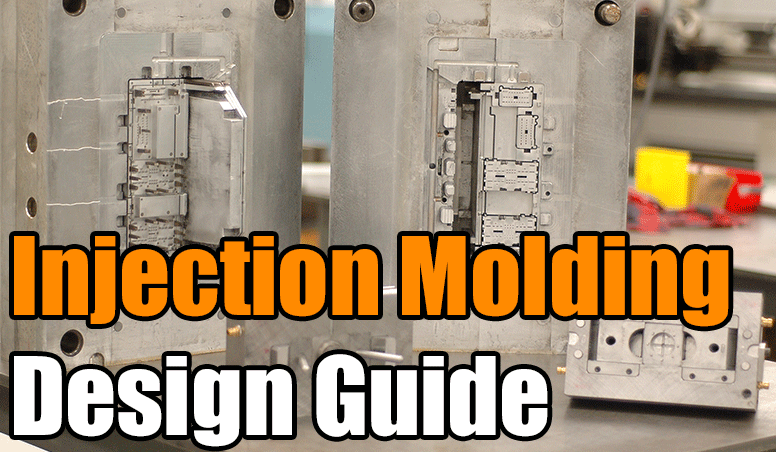
What Is Injection Molding and How Does It Work?
Injection molding machines heat plastic resin pellets to melt them into a liquid that machines force into steel molds under intense hydraulic pressure. After the plastic cools and solidifies, the mold opens and robotically ejects the finished parts.
Molds contain two primary steel components:
- Cavity: The front half of the tooling creates the exterior visual features of the parts. It’s common to refer to this as the “A side” of the tool.
- Core: The back half of the tooling forms interior and largely hidden geometry like ribs, bosses, inserts, and other functional features. Injection molders often call this the “B side”.
Where the two mold halves meet forms the parting line, which is a small witness line visible on the components after manufacturing.
Understanding the fundamentals of injection molding machines and tooling is crucial for designing parts successfully using the process. Let’s dive into the top design considerations every engineer needs to keep in mind.
Key Design Guidelines for Injection Molding
While skilled injection molders can manufacture incredibly precise and complex plastic components, much of their process control centers on perfecting parameters like temperature, pressure, clamp force, and cycle times.
As the component designer, your responsibility is to engineer products suited for the realities of flowing molten plastics into steel tooling costing upwards of $100,000.
Here are my best tips for getting the most out of the injection molding process:
Wall Thickness
The single most critical injection molding design guideline is maintaining uniform wall thickness throughout your parts. When plastic cools, it shrinks. Non-uniform parts cause uneven cooling, leading to warped or cracked components.
Here are important rules when considering wall thickness for your program:
- Target thickness between 2-4mm for most applications. Ultra-thin-walled parts below 1mm are possible but require extremely high precision.
- Never vary wall thickness by more than 15% across any single part to prevent uneven cooling.
- When you must transition between thicker and thinner walls, use gradual chamfers or fillets ensure smooth flow.
Additionally, thick walls not only shrink more but retain heat. Thinner, uniform walls produce less scrap due to cooling issues. Faster cycles also lower production costs.
Draft Angles
Shrinking plastic sticking to steel mold walls stops production lines, damages tooling, and drives up scrap rates. While textured surfaces help parts release from the tooling, draft angles enable effortless robotic part ejection.
Draft involves tapering vertical walls slightly—usually between 1-5 degrees—to prevent molded components from sticking. As guidelines:
- Add a minimum 2-degrees draft on all vertical walls.
- Increase draft angles on taller core/cavity features or deeply textured surface finishes.
Expect steel molds to require maintenance and periodic replacement over production runs. However, effective draft angles extend overall tool longevity.
Rib and Boss Design
Ribs and bosses strengthen otherwise thin-walled sections prone to flexing or warping under load. Properly incorporating these features enables reducing material usage and costs while preventing failures.
Follow these design rules for ribs:
- Add fillets at the base of all ribs for strength.
- Set rib thickness between 50-60% of the nominal wall thickness to prevent sink.
- For appearance parts, keep rib height under 2.5X thickness to eliminate visible shrinkage.
Boss guidelines include:
- Size outer boss diameter 2.5X hardware diameter (screws, etc.).
- Limit boss thickness to <60% of walls to avoid sink marks on visible outer surfaces.
- Add gussets from bosses to adjacent walls for rigidity.
Well-designed strengthening ribs and hardware bosses are hallmarks of functional, durable injection molded components.
Material Shrinkage Rates
Every plastic material shrinks uniquely as it cools within injection molds. However, most shrink between 2-4% which must factor into your designs.
Neglecting shrinkage results in undersized parts unable to assemble properly with mating components in the finished product. The trick is compensating by deliberately designing parts slightly oversized.
Common techniques used by experienced mold makers include:
- Increasing overall wall thickness.
- Adding interference fits like crush ribs onto inserts.
- Designing large press-in posts instead of holes.
Review manufacturer mold shrink data during material selection. Also, prototype new tooling to confirm proper shrink compensation strategies.
Getting shrinkage right in the design phase prevents headaches with post-molding secondary operations down the line.
Parting Lines
Earlier, we reviewed the basics of multi-piece injection molds and how they form components where the halves meet along the parting line.
As a design guideline, locating parting lines demands striking an aesthetic/functional balance and recognizing their impacts on manufacturability.
For appearance, we often hide parting lines along sharp non-cosmetic edges or place them on the rear of components. Side actions and other complex mechanisms drive up tooling costs when sealing onto curved surfaces.
Great parting line placement also improves mold strength and lifecycle. Just take care regarding fill points, undercuts, and ejection to prevent工flashing.
Gate Location/Type
Gate design ties directly into molding success, as they introduce molten plastic into cavities. Gate locations greatly influence cycle times, required injection pressures, and component cosmetics.
Common gate types include:
- Edge gates: Most popular approach with a rectangular profile along the parting line.
- Hot tip gates: Round gate injected through the cavity roof best for concentricity.
- Direct gates: Large gates for fast mold filling but requires secondary gate removal.
Beyond type, adhere to these gate location fundamentals:
- Position gates to fill the deepest mold sections first.
- Keep away from cosmetic surfaces or high-stress points.
- Use multiple gates for easier filling of complex geometries.
gates essentially act as the “sprues” guiding the flow of plastic into mold cavities just like casting. Taking great care engineering gate quantity, shape, placement, and size remains critical for defect-free, high-yield injection molding.
The Bottom Line
Hopefully this guide provided some helpful high-level injection molding design guidelines as an introduction. Now that you understand top guidelines and have access to supplemental resources, you’re ready to design incredible plastic parts optimized for precision injection molding manufacturing.
Putting these concepts into play will streamline pre-production, prevent defects, and lead to establishing robust production lines pumping out flawless products.
What design questions come up as you venture into your next injection molded component project? Feel free to reach out if you want to discuss further. I’m always happy to help colleagues strengthen technical capabilities and share best practices.