La resolución de problemas en el proceso de moldeo por inyección es una habilidad crítica para cualquiera que trabaje en la fabricación de plásticos. Al tratarse de un método de producción complejo con muchas variables, inevitablemente surgen problemas que requieren una rápida identificación y solución para evitar costosos tiempos de inactividad. En esta completa guía, como profesional fabricante de moldeo por inyecciónAdemás, trataremos metodologías probadas de solución de problemas para resolver eficazmente los defectos y estabilizar los procesos.
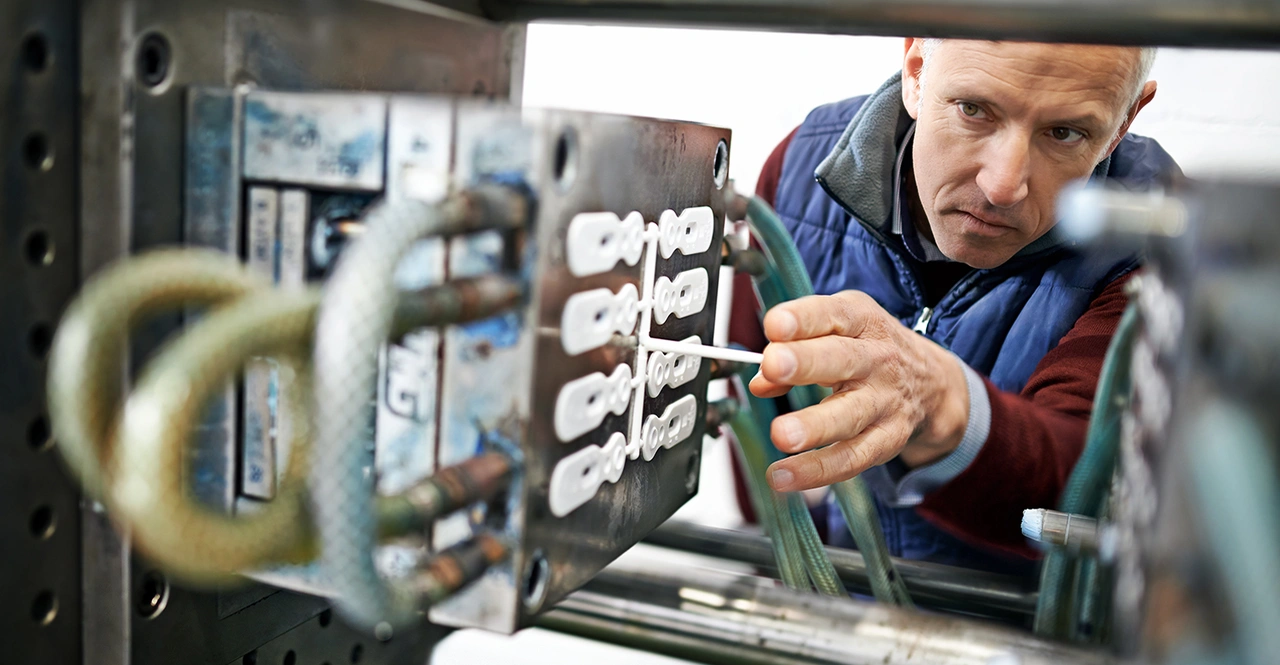
Introducción
En resolución de problemas en el proceso de moldeo por inyección implica medidas tanto reactivas como proactivas. Los esfuerzos reactivos implican abordar los defectos a medida que se producen mediante el análisis sistemático de la causa raíz y la corrección. Las medidas proactivas optimizan la estabilidad de los procesos mediante una sólida configuración de las máquinas, el control de los procesos y estudios de capacidad.
Dominar los principios de resolución de problemas es esencial para los moldeadores por inyección que buscan la excelencia operativa. Mediante la detección temprana de problemas y la rápida identificación de soluciones, los procesadores pueden lograr un mayor rendimiento, menos desechos/reparaciones, una mejora de la calidad y una reducción de los costes.
Un enfoque estructurado para la resolución de problemas de moldeo por inyección
La resolución eficaz de problemas requiere una estructura para recorrer metódicamente los posibles problemas. Los pasos suelen incluir:
Inspeccione a fondo
Compruebe cuidadosamente si la pieza presenta defectos y mida las dimensiones críticas. Las fotos ayudan al análisis. Limpie el molde y asegúrese de que los componentes móviles funcionan correctamente.
Comprender las condiciones de partida
Comparar los valores de consigna del proceso con línea de base parámetros de un proceso validado. Revise las listas de comprobación para la preparación de máquinas, materiales y moldes.
Analizar las causas profundas
Evaluar posibles factores de proceso, material, molde y máquina en función del patrón de defectos. Analizar tendencias utilizando los datos del proceso.
Implantar soluciones
Las medidas correctoras deben abordar directamente las causas profundas, empezando por ajustar las condiciones del proceso. Los cambios de hardware sólo se realizan si son necesarios.
Confirmar resultados
Ejecutar pruebas para confirmar que el problema se ha resuelto por completo. Actualice la documentación del proceso y comparta los resultados entre los equipos para evitar que se repitan.
Examinemos ahora algunos de los defectos más comunes del moldeo por inyección y consejos prácticos para abordarlos con eficacia.
Defectos comunes del moldeo por inyección y soluciones
Alabeo
El alabeo se refiere a la distorsión o torsión de la pieza moldeada tras la expulsión. Se produce por una contracción desigual, normalmente debida a espesores de pared no uniformes o a variaciones en el enfriamiento. El alabeo es común en piezas grandes y planas con nervaduras mínimas para rigidez estructural.
Causas
- Enfriamiento desigual de secciones gruesas y finas
- Orientación a partir de altas velocidades de inyección
- Tensiones residuales de moldeo
- Expulsión antes de la solidificación adecuada
Soluciones
- Optimizar los circuitos de refrigeración para un enfriamiento uniforme
- Reducir la velocidad de inyección y envasar a presiones más bajas
- Aumentar la temperatura del molde para reducir las variaciones de viscosidad
- Retrasar la expulsión hasta que la temperatura del plástico descienda lo suficiente
Marcas de fregadero
Las marcas de hundimiento son pequeñas depresiones brillantes en el moldeado debidas a una presión de empaquetado insuficiente. Suelen aparecer cuando el grosor de las paredes cambia bruscamente. De naturaleza cosmética, los hundimientos pueden ser desde abolladuras poco profundas hasta cráteres profundos en función del grosor de la pieza.
Causas
- Bajas presiones de inyección o envasado
- Congelación anticipada de puertas
- Alta temperatura del molde
- Tiempo de enfriamiento insuficiente
Soluciones
- Aumentar la presión del envase, el tiempo y la velocidad de inyección de la masa fundida
- Aumentar el tamaño del disparo y reducir la amortiguación
- Reubicar la puerta en las zonas más gruesas
- Temperaturas de fusión y moldeo más bajas
Disparos cortos
Las tomas cortas se refieren a un llenado incompleto del molde que da lugar a secciones faltantes, normalmente las más alejadas de la compuerta. Las piezas tienen frentes de flujo visibles donde el plástico ha dejado de moverse. Los disparos cortos se producen cuando el volumen de material, la temperatura o la presión son insuficientes para llenar completamente el molde.
Causas
- Baja tasa de inyección o presiones
- Congelación temprana de puertas
- Viscosidad excesiva
- La humedad inhibe el flujo
- Ventilaciones obstruidas que atrapan gases
Soluciones
- Aumentar el tamaño de disparo, la velocidad de inyección y la temperatura de fusión
- Aumentar la presión del envase/mantenerla, tiempo
- Garantizar una profundidad de ventilación adecuada
- Secar el material según las especificaciones
Flash
Las rebabas consisten en finas capas de plástico con protuberancias en forma de aletas a lo largo de las líneas de separación del molde, los pasadores eyectores, las correderas o los insertos. Las rebabas aparecen cuando la fuerza de sujeción es insuficiente para resistir las presiones de inyección, lo que permite que las caras del molde se separen ligeramente.
Causas
- Presión o velocidades de inyección elevadas
- Fuerza de sujeción del molde insuficiente
- Profundidad de ventilación inadecuada
- Mala alineación de las placas del molde
Soluciones
- Reducir la presión de inyección y aumentar el tiempo
- Aumentar el tonelaje de la pinza o la presión de sobrealimentación
- Ajustar la profundidad de la tierra flash
- Mejorar la alineación y el mecanizado de moldes
Marcas de quemaduras
Las marcas de quemado se refieren a las motas y rayas oscurecidas o descoloridas en una pieza moldeada, normalmente cerca de compuertas, respiraderos o canales. Las quemaduras se producen por sobrecalentamiento en estas zonas de flujo restringido, ya sea por cizallamiento excesivo o por falta de refrigeración.
Causas
- Alta velocidad de inyección que aumenta el calor de cizallamiento
- Diseño deficiente de la puerta, el corredor y el terreno
- Falta de refrigeración cerca de las puertas
- Problemas de compatibilidad de materiales
Soluciones
- Reducir las velocidades y presiones de inyección
- Actualizar compuertas, patines, boquilla
- Añadir canales de refrigeración cerca de la puerta
- Garantizar el secado adecuado del material
Chorro
El chorro se refiere a las líneas de flujo o rayas de alto brillo causadas por el efecto de fuente de fusión. Se produce cuando la masa fundida no impacta en las paredes de la cavidad y crea un flujo turbulento y precipitado. La formación de chorros se debe a velocidades de inyección elevadas sin suficiente contrapresión.
Causas
- Alta velocidad de inyección
- Contrapresión baja
- Diámetro de puerta pequeño
- Falta de pinzamiento
Soluciones
- Reducir la velocidad de inyección
- Aumentar la contrapresión para un flujo laminar
- Tamaño de puerta abierto para una entrada suave
- Fusión por impacto en costillas gruesas/bostes
Vacíos
Los huecos son pequeñas bolsas de aire que aparecen en las piezas, normalmente en las zonas más gruesas. Surgen a partir de gases disueltos en la masa fundida bajo calor/presión que salen de la solución cuando las presiones caen repentinamente. Los gases quedan atrapados en el interior de la pieza.
Causas
- Desgasificación por humedad
- Congelación temprana de puertas
- Baja presión de la empaquetadura
- Diseño de ventilación deficiente
Soluciones
- Secar el material según las directrices
- Aumentar la presión del paquete, puertas
- Reubicar las puertas en las secciones más pesadas
- Añada rejillas de ventilación del tamaño adecuado
Líneas de flujo
Las líneas de flujo se refieren a las líneas de soldadura visibles a lo largo de los límites del frente de flujo que surgen del flujo de la fuente. Aparecen como ondulaciones o rugosidades superficiales en línea con el flujo de fusión, acentuadas por los aditivos orientadores. Las líneas de flujo indican el empaquetamiento antes de la congelación de las compuertas.
Causas
- Bajas temperaturas de fusión
- Velocidad de llenado lenta que permite la formación de pieles
- Refrigeración no uniforme
- Formas geométricas que provocan divisiones del flujo
Soluciones
- Aumento de las temperaturas de fusión y moldeo
- Aumentar el índice de inyección
- Igualar los espesores de pared de las secciones
- Esquinas interiores redondeadas
Defectos superficiales
Los defectos superficiales cubren texturas moldeadas que causan una estética pobre en lugar del alto brillo diseñado. Surgen de rellenos, humedad u otros contaminantes que alteran el acabado de la superficie. Los tipos de defectos van desde hoyos, rayas y hoyuelos hasta texturas de piel rugosa.
Causas
- ArrastreContaminación cruzada
- Pulido de moho deficienteHumedad en los materialesEnrojecimiento de la puertaRecubrimiento con contaminantes
Soluciones
- Secuenciación de la producción
- Limpieza de moho
- Secadoras funcionando correctamente
- Ventilación
- Ciclos más cortos
- Rectificado limpio
Estrías de color
Las rayas de color consisten en una distribución desigual del color en la pieza moldeada, que aparecen como rayas claras/oscuras. Es el resultado de una mala dispersión de los colorantes en la resina o de una masa fundida no homogénea. El alto cizallamiento o las altas temperaturas degradan los aditivos.
Causas
- Mezcla inadecuada
- Obstrucción parcial de los canales calientes
- Tiempo de residencia excesivo de la resina
- Altas revoluciones del tornillo, velocidades de inyección
Soluciones
- Aumentar la contrapresión y las revoluciones del tornillo
- Limpiar completamente los canales calientes
- Reducir los ciclos y el tiempo de permanencia
- Velocidades de inyección más bajas
Marcas de separación
Las marcas de separación son rayas plateadas que irradian irregularmente desde los frentes de flujo causadas por una pequeña separación de las capas de fusión. Se asemejan a grietas en una inspección ampliada. La separación se debe a la contaminación, la humedad o la descomposición en las zonas de cizallamiento.
Causas
- Sobrecalentamiento y degradación del material
- La humedad atrapada se desprende
- Contaminación de la corteza
- Calentamiento excesivo por cizallamiento
Soluciones
- Temperaturas más bajas de los barriles
- Secar correctamente los materiales
- Eliminar las fuentes de contaminación
- Aumentar la profundidad de ventilación
Líneas de soldadura
Las líneas de soldadura son líneas de costura visibles donde confluyen frentes de flujo de fusión separados. Tienen menor resistencia que el material a granel. La presión de mantenimiento debe empaquetar el molde antes de que las pieles se congelen completamente en una línea de punto débil.
Causas
- Formación prematura de piel
- Bajas temperaturas de fusión
- Refrigeración no uniforme
- Ventilación inadecuada
Soluciones
- Aumento de las temperaturas de fusión y moldeo
- Aumentar el índice de inyección
- Igualar los espesores de las secciones
- Ampliar los respiraderos para gases atrapados
Fragilidad
La fragilización se refiere a la pérdida de resistencia al impacto o ductilidad de las piezas, lo que provoca grietas o fracturas bajo tensión. Las cargas, los refuerzos y los pigmentos pueden fragilizar los materiales. La degradación térmica o mecánica también reduce la tenacidad.
Causas
- Contaminación por materiales degradados o resinas de mezcla cruzada
- Rellenos excesivos que reducen la resistencia al impacto
- Sobrecalentamiento por cizallamiento o temperaturas elevadas
- Huecos internos que inician la propagación de grietas
Soluciones
- Evitar la contaminación cruzada
- Optimizar las cargas de relleno para la resistencia al impacto
- Temperaturas de proceso más bajas
- Aumente la presión de la empaquetadura para minimizar los huecos
Solución eficaz de problemas de moldeo por inyección
Aprender a reconocer rápidamente los defectos, evaluar exhaustivamente sus causas fundamentales e identificar las acciones correctivas separa a los moldeadores por inyección normales de los de élite. Desarrollar el control del proceso a través de principios científicos de moldeo minimiza la resolución de problemas.
Mediante un enfoque estructurado y esta visión general de los problemas comunes de moldeo, los procesadores pueden lograr un alto tiempo de actividad, rendimiento y capacidad. Dominio de resolución de problemas en el proceso de moldeo por inyección establece la estabilidad necesaria para las operaciones ajustadas.