El moldeo por inyección de acrílico es el proceso de dar forma al plástico acrílico inyectándolo en un molde. Permite dar forma al acrílico en productos como lentes, pantallas y paneles. Como profesional moldeo por inyección de acrílico fabricante, te guiaré paso a paso por todo el proceso de inyección de acrílico.
En proceso de moldeo por inyección de acrílico comienza diseñando un molde para crear la pieza deseada. A continuación se secan los gránulos acrílicos, se cargan en la máquina de inyección y se inyectan en el molde. Tras enfriarse y endurecerse, la pieza acrílica se expulsa y puede someterse a otros pasos de acabado.
Siga leyendo mientras desgloso cada etapa de moldeo por inyección de acrílico para ayudarle a entender exactamente cómo funciona.
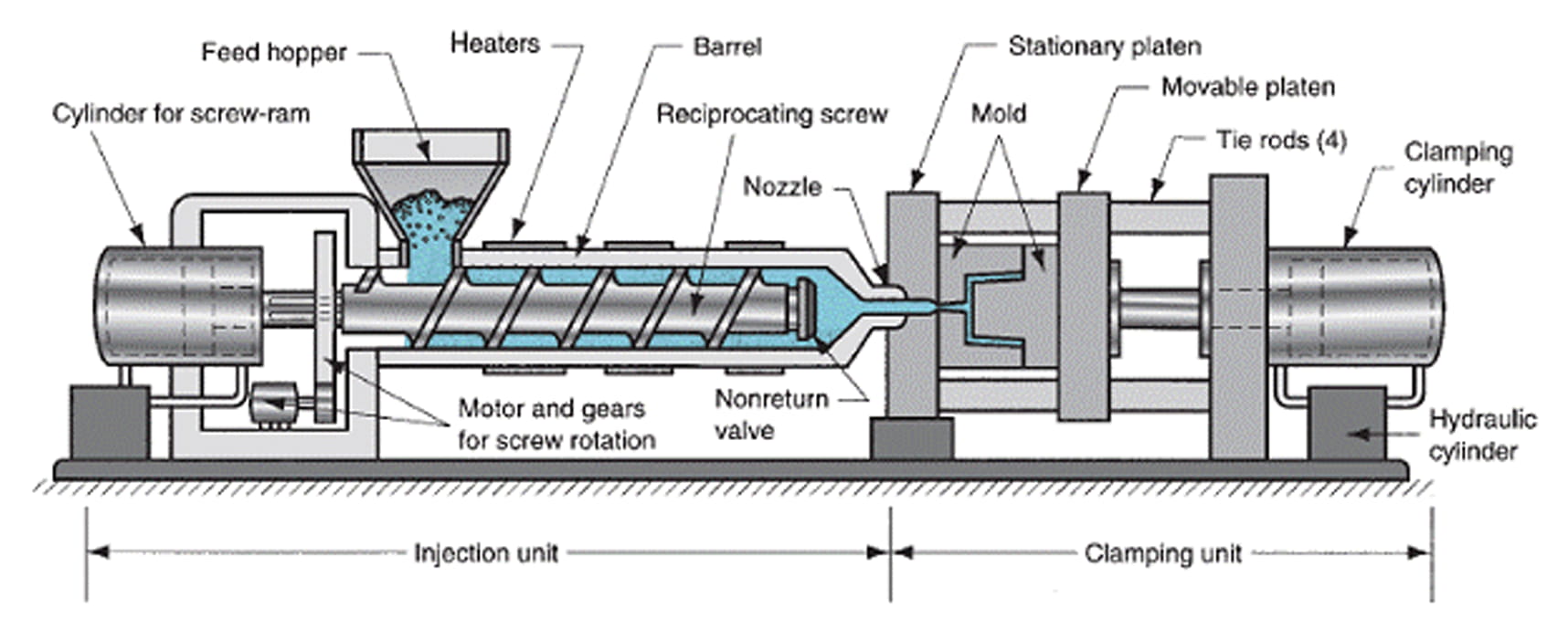
Proceso de moldeo por inyección de acrílico
Paso 1: Diseño del molde
El primer paso es crear el molde de inyección para formar las piezas acrílicas. El molde consta de dos mitades -la mitad de la cavidad y la mitad del núcleo- que se unen para formar el espacio interior del molde. El acrílico adopta esta forma una vez inyectado.
Los diseñadores de moldes utilizan 3D CAD para modelar con precisión moldes de inyección. Las geometrías y características complejas pueden diseñarse al detalle y convertirse en código de mecanizado para el taller de moldes. En esta fase inicial también se tienen en cuenta los orificios, insertos, texturas y otras especificaciones.
Es fundamental diseñar bien el molde. Las compuertas inteligentes, los respiraderos y los ángulos de desmoldeo garantizan un flujo de acrílico adecuado y un resultado final de calidad. Un fabricante de moldes experimentado tendrá en cuenta estos matices a la hora de fabricar el molde de producción final.
Paso 2: Preparación del material acrílico
En bruto, el acrílico se presenta en forma de perlas o gránulos translúcidos parecidos al azúcar granulado. Los fabricantes mantienen la resina acrílica seca en un entorno de clima controlado para conservar el contenido de humedad adecuado. Un exceso de humedad crea burbujas y otros defectos una vez inyectada en el molde.
Algunas resinas acrílicas son higroscópicas. Por ello, los fabricantes cargan el material desde una unidad de tolva de secado que contiene lechos desecantes. A continuación, los secadores calientan el acrílico por encima de 200 °F para eliminar la humedad residual antes del moldeo.
El acrílico seco fluye hacia los depósitos de sobrepresión para esperar la inyección. Algunas máquinas de moldeo por inyección tienen incluso secadores de resina integrados para simplificar el sistema de suministro de material.
Proceso de secado del acrílico
Es fundamental que la resina acrílica esté completamente seca antes del moldeo por inyección. Cualquier rastro de humedad se convierte en vapor cuando el plástico caliente entra en el molde.
Incluso las piezas fabricadas con mayor precisión presentan pequeñas fisuras, burbujas y defectos visuales cuando hay humedad en su interior. No es bueno.
Paso 3: Sujeción del molde
Para iniciar la producción, un operario sujeta el molde de inyección en la prensa. Unos cilindros hidráulicos aplican toneladas de presión para cerrar firmemente las mitades del núcleo y la cavidad. Esto evita que el plástico fundido presurizado gotee una vez inyectado a altas velocidades.
La presión de la abrazadera debe superar las fuerzas colectivas que intentan separar las mitades del molde durante la inyección. Las barras de unión aumentan la robustez entre platinas.
Paso 4: Inyectar el acrílico
Con el molde bien sujeto, el acrílico fundido fluye desde el cilindro de inyección hasta el bebedero. El sistema de canalización dirige la resina caliente a cada hendidura de la cavidad de la herramienta para rellenar completamente el espacio vacío.
Las prensas de husillo introducen gránulos sólidos en el barril y utilizan calentadores eléctricos y energía mecánica para licuar el plástico. Sale disparado hacia delante una vez que la presión de inyección supera la presión de la cavidad del molde.
Embalar y retener
Para evitar la solidificación prematura, se inyecta más resina después de que se llene la cavidad. De este modo, se acumula más acrílico fundido y se aplica una presión de retención hasta que la puerta se congela.
Las piezas mantienen su forma y experimentan menos distorsión gracias a este paso de empaquetado secundario. Permite un tiempo extra para que la resina caliente busque su forma final antes de enfriarse.
Paso 5: Enfriamiento y curado
Tras el empaquetado, el agua fría circula por los puertos del interior de la herramienta para solidificar el plástico acrílico sobrecalentado. El complejo trazado de los canales se centra estratégicamente en los puntos calientes para acelerar la refrigeración.
Los pasadores eyectores se extienden ligeramente para retraer el plástico de las superficies del núcleo. Esto evita que las piezas se adhieran una vez que están listas para ser empujadas fuera del molde.
Los tiempos de enfriamiento varían en función del grosor de las paredes. El plástico más grueso retiene el calor durante más tiempo que las secciones transversales más finas. Los moldes más nuevos utilizan canales conformados para acelerar el enfriamiento y reducir los tiempos de ciclo.
Paso 6: Expulsión de piezas acrílicas
Para expulsar manualmente un componente acrílico curado:
- La fuerza de sujeción se libera, permitiendo que las mitades del molde de inyección se separen.
- Mediante varillas guía, la placa eyectora avanza hacia delante para empujar las piezas fuera del lado de la cavidad de la herramienta.
- Los brazos robóticos o los operarios cogen los artículos acabados fuera de la prensa de moldeo
Para formas más sencillas con diseños de moldes de tiro recto, los sistemas de expulsión automática funcionan mejor. Eliminan instantáneamente las piezas de cada cara de la herramienta sin necesidad de mano de obra.
Pasos de acabado adicionales
Tras la expulsión básica, las piezas acrílicas suelen someterse a procesos adicionales de postmoldeo que:
- Recorte el plástico sobrante
- Lijar o pulir las marcas de las herramientas de acoplamiento
- Pulido de superficies con llama y vapor
- Aplique revestimientos duros para mejorar la protección
- Unir conjuntos mediante adhesivo o soldadura
Este trabajo de acabado mejora la cosmética y prepara los componentes acrílicos para su envío o el siguiente proceso de fabricación.
En proceso de moldeo por inyección de acrílico continúa a medida que se sobremoldean componentes adicionales, se adhieren las etiquetas, se montan los herrajes y las pruebas finales validan la calidad de la pieza.
Aplicaciones del moldeo por inyección de acrílico
Transparente o coloreado, el plástico acrílico ofrece flexibilidad de producción mediante técnicas de moldeo por inyección. Veamos algunas aplicaciones comunes.
Faros y pilotos traseros automáticos
Los fabricantes de automóviles moldean los faros delanteros y traseros a partir de acrílico. Este material resiste años de maltrato en carretera sin degradarse por la exposición a los rayos UV.
Los conjuntos de faros delanteros presentan reflectores complejos que requieren capacidades de moldeo por inyección de precisión. El plástico acrílico también crea lentes ópticas ideales para difundir los haces de luz donde sea necesario.
Hielo sintético
Se pueden moldear por inyección grados especializados de acrílicos para imitar el aspecto y las propiedades de fricción del hielo. Las pistas de hielo sintético abordan el elevado coste de mantener congelado el hielo tradicional.
Las instalaciones de curling, patinaje artístico y hockey permanecen operativas todo el año gracias al acrílico inyectado. Este material también es adecuado para eventos sobre hielo temporales que no cuentan con una infraestructura de refrigeración permanente.
Pantallas LCD
Las pantallas planas se basan en ventanas de visualización acrílicas y tubos ópticos de luz para ofrecer una claridad de visualización vibrante. Los fabricantes de moldes fabrican con precisión plástico ultratransparente sin defectos para que la luz atraviese las distintas capas de la pantalla LCD.
Los técnicos especializados pulen las líneas de separación moldeadas después del desmoldeo. Así se eliminan las imperfecciones antes de intercalar otros componentes electrónicos entre los paneles moldeados.
Preguntas frecuentes sobre el proceso de moldeo por inyección de acrílico
A continuación encontrará respuestas a preguntas frecuentes sobre el proceso de moldeo por inyección de acrílico:
¿Qué máquinas se utilizan?
Las prensas de moldeo por inyección estándar procesan térmicamente compuestos acrílicos para aplicaciones de moldeo. Las máquinas van desde pequeñas verticales a grandes horizontales con toneladas de fuerza de cierre.
El acrílico inyectado también funciona con prensas de moldeo por inyección de metal. Estas máquinas especializadas admiten mezclas de metal en polvo además de las resinas tradicionales.
¿Se pueden moldear por inyección todos los tipos de acrílico?
Sí, grados como el acrílico extruido, el acrílico de colada celular y el acrílico de colada continua se moldean todos por inyección con éxito. Los fabricantes adaptan las rutinas de enfriamiento, los índices de llenado, la temperatura del molde y otros parámetros para procesar diferentes formulaciones acrílicas.
¿Por qué plastificar el acrílico?
En su forma de gránulo bruto, el acrílico no fluye ni rellena los detalles intrincados de las piezas. La plastificación transforma la resina acrílica rígida en un fluido que fluye libremente. Esto permite una penetración completa en el molde antes de que el enfriamiento vuelva a dar al acrílico una forma sólida.
Calentar el acrílico entre 240°C y 320°C funde el material para obtener una viscosidad de inyección adecuada. El acrílico no se descompondrá químicamente hasta superar los 380 °C, muy por encima de las temperaturas de moldeo estándar.
Conclusión
Comprender la totalidad proceso de moldeo por inyección de acrílico le permite planificar el lanzamiento de un producto que utilice eficazmente este material plástico transparente.
Contar con el socio de moldeo por inyección adecuado ayuda a evitar retrasos en la fabricación y costosos errores de iteración. Su experiencia marcará la diferencia durante la cualificación del molde acrílico.