El moldeo por inyección es uno de los procesos de fabricación más versátiles y rentables para producir piezas de plástico a gran escala. Desde los Legos hasta las carcasas del iPhone, innumerables productos que usamos a diario empezaron como plástico fundido inyectado en moldes de acero mecanizados con precisión.
Sin embargo, el moldeo por inyección sólo ofrece todo su potencial si se diseñan piezas específicas para este proceso. A diferencia de la impresión 3D o Mecanizado CNCLos componentes moldeados por inyección tienen unos requisitos de diseño muy estrictos para llenar bien los moldes, evitar defectos y salir limpiamente del utillaje tras el enfriamiento.
Ignorar los principios de diseño del moldeo por inyección puede provocar grandes retrasos y costes innecesarios en prácticamente todas las fases, desde la creación de prototipos hasta la producción. Y dado que el proceso implica costosas herramientas de acero, los cambios de diseño tras la fabricación del molde pueden ser extremadamente lentos y costosos.
A lo largo de esta completa guía, como profesional fabricante de moldeo por inyeccióncompartiré mis mejores consejos y estrategias para el diseño de piezas de plástico para el éxito del moldeo por inyección. Aprenderá sobre consideraciones críticas de diseño, como el grosor uniforme de las paredes, los ángulos de desmoldeo, el diseño de nervaduras y resaltes, la contracción del material, el acabado de superficies y mucho más.
Empecemos por los fundamentos del propio proceso de moldeo por inyección. Comprender con precisión cómo fluye el plástico fundido en las cavidades ayudará a que muchas directrices de diseño tengan sentido.
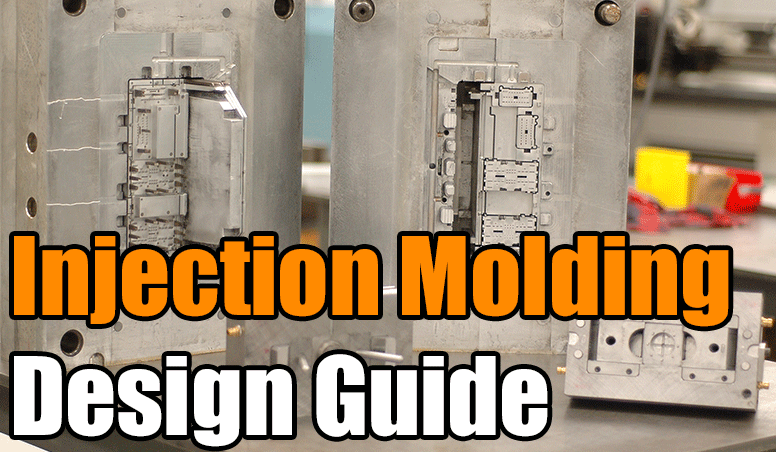
¿Qué es el moldeo por inyección y cómo funciona?
Las máquinas de moldeo por inyección calientan gránulos de resina de plástico para fundirlos en un líquido que las máquinas introducen a la fuerza en moldes de acero bajo una intensa presión hidráulica. Cuando el plástico se enfría y solidifica, el molde se abre y expulsa robóticamente las piezas acabadas.
Los moldes contienen dos componentes principales de acero:
- Cavidad: La mitad delantera del utillaje crea las características visuales exteriores de las piezas. Es común referirse a ella como la "cara A" del utillaje.
- Núcleo: La mitad posterior del utillaje forma la geometría interior y en gran medida oculta, como nervaduras, resaltes, insertos y otras características funcionales. Los moldeadores por inyección suelen llamarla "cara B".
El punto de unión de las dos mitades del molde forma la línea de separación, que es una pequeña línea testigo visible en los componentes después de la fabricación.
Comprender los fundamentos de las máquinas y herramientas de moldeo por inyección es crucial para diseñar piezas con éxito mediante este proceso. Veamos las principales consideraciones de diseño que todo ingeniero debe tener en cuenta.
Directrices clave de diseño para el moldeo por inyección
Aunque los expertos moldeadores por inyección pueden fabricar componentes de plástico increíblemente precisos y complejos, gran parte del control de sus procesos se centra en perfeccionar parámetros como la temperatura, la presión, la fuerza de cierre y los tiempos de ciclo.
Como diseñador de componentes, su responsabilidad es diseñar productos adaptados a la realidad de hacer fluir plásticos fundidos en utillajes de acero que cuestan más de $100.000.
Estos son mis mejores consejos para aprovechar al máximo el proceso de moldeo por inyección:
Espesor de pared
La directriz de diseño de moldeo por inyección más importante es mantener un grosor de pared uniforme en todas las piezas. Cuando el plástico se enfría, se contrae. Las piezas no uniformes provocan un enfriamiento desigual, lo que da lugar a componentes deformados o agrietados.
Estas son algunas reglas importantes a la hora de considerar el grosor de las paredes para su programa:
- Espesor objetivo entre 2 y 4 mm para la mayoría de las aplicaciones. Es posible fabricar piezas con paredes ultrafinas de menos de 1 mm, pero requieren una precisión extremadamente alta.
- Nunca varíe el grosor de la pared en más de 15% en una sola pieza para evitar un enfriamiento desigual.
- Cuando tenga que pasar de una pared gruesa a otra más fina, utilice chaflanes o filetes graduales para garantizar un flujo suave.
Además, las paredes gruesas no sólo se contraen más, sino que retienen el calor. Las paredes más finas y uniformes producen menos desechos por problemas de refrigeración. Los ciclos más rápidos también reducen los costes de producción.
Ángulos de calado
El plástico retráctil que se adhiere a las paredes de acero de los moldes detiene las líneas de producción, daña los utillajes y aumenta las tasas de desecho. Mientras que las superficies texturizadas ayudan a que las piezas se desprendan del utillaje, los ángulos de desmoldeo permiten la expulsión robotizada de piezas sin esfuerzo.
El calado consiste en estrechar ligeramente las paredes verticales -normalmente entre 1 y 5 grados- para evitar que los componentes moldeados se peguen. Como directrices:
- Añada un tiro mínimo de 2 grados en todas las paredes verticales.
- Aumente los ángulos de inclinación en los elementos de núcleo/cavidad más altos o en los acabados de superficie con texturas profundas.
Los moldes de acero requieren mantenimiento y sustituciones periódicas a lo largo de la producción. Sin embargo, los ángulos de desmoldeo eficaces prolongan la vida útil de la herramienta.
Diseño de costilla y jefe
Las nervaduras y los resaltes refuerzan las secciones de pared delgada propensas a flexionarse o alabearse bajo carga. La correcta incorporación de estas características permite reducir el uso de material y los costes, al tiempo que se evitan fallos.
Sigue estas reglas de diseño para las costillas:
- Añada filetes en la base de todas las costillas para reforzarlas.
- Ajustar el espesor de la nervadura entre 50-60% del espesor nominal de la pared para evitar el hundimiento.
- Para las piezas de apariencia, mantenga la altura de las nervaduras por debajo de 2,5 veces el grosor para eliminar el encogimiento visible.
Las directrices del jefe incluyen:
- Dimensione el diámetro del saliente exterior 2,5X el diámetro de los herrajes (tornillos, etc.).
- Limite el grosor del saliente a <60% de las paredes para evitar marcas de hundimiento en las superficies exteriores visibles.
- Añada cartelas desde los resaltes a las paredes adyacentes para mayor rigidez.
Los nervios de refuerzo bien diseñados y los resaltes de los herrajes son características distintivas de los componentes funcionales y duraderos moldeados por inyección.
Índices de contracción del material
Cada material plástico se contrae de forma única cuando se enfría dentro de los moldes de inyección. Sin embargo, la mayoría encogen entre 2-4%, lo que debe tenerse en cuenta en los diseños.
Si no se tiene en cuenta la contracción, se obtienen piezas demasiado pequeñas que no pueden ensamblarse correctamente con los componentes del producto acabado. El truco consiste en compensarlo diseñando deliberadamente piezas ligeramente sobredimensionadas.
Entre las técnicas más utilizadas por los fabricantes de moldes experimentados se incluyen:
- Aumento del grosor total de las paredes.
- Añadir ajustes de interferencia como nervios de aplastamiento en insertos.
- Diseño de grandes postes a presión en lugar de agujeros.
Revisar los datos de contracción del molde del fabricante durante la selección del material. Además, cree prototipos de nuevas herramientas para confirmar las estrategias adecuadas de compensación de la contracción.
Conseguir la contracción correcta en la fase de diseño evita dolores de cabeza con las operaciones secundarias posteriores al moldeo.
Líneas de separación
Anteriormente, revisamos los fundamentos de los moldes de inyección de varias piezas y cómo forman componentes donde las mitades se encuentran a lo largo de la línea de separación.
Como directriz de diseño, la ubicación de las líneas de separación exige alcanzar un equilibrio estético/funcional y reconocer su impacto en la fabricabilidad.
Por razones estéticas, a menudo ocultamos las líneas de separación a lo largo de bordes afilados no estéticos o las colocamos en la parte posterior de los componentes. Las acciones laterales y otros mecanismos complejos aumentan los costes de utillaje al sellar superficies curvas.
Una buena colocación de la línea de apertura también mejora la resistencia y el ciclo de vida del molde. Tenga cuidado con los puntos de llenado, los rebajes y la expulsión para evitar las rebabas.
Ubicación/tipo de puerta
El diseño de las compuertas está directamente relacionado con el éxito del moldeo, ya que introducen plástico fundido en las cavidades. La ubicación de las compuertas influye enormemente en los tiempos de ciclo, las presiones de inyección necesarias y la estética de los componentes.
Los tipos de puertas más comunes son:
- Puertas de borde: El enfoque más popular con un perfil rectangular a lo largo de la línea de separación.
- Puertas de punta caliente: Puerta redonda inyectada a través del techo de la cavidad mejor para la concentricidad.
- Puertas directas: Compuertas grandes para un llenado rápido del molde, pero requiere la retirada de la compuerta secundaria.
Más allá del tipo, respete estos principios básicos de ubicación de puertas:
- Coloque las compuertas para llenar primero las secciones más profundas del molde.
- Mantener alejado de superficies cosméticas o puntos de gran tensión.
- Utilice varias compuertas para rellenar más fácilmente geometrías complejas.
Las compuertas actúan esencialmente como "bebederos" que guían el flujo de plástico hacia las cavidades del molde, al igual que en la fundición. Para conseguir un moldeo por inyección sin defectos y de alto rendimiento, es fundamental tener mucho cuidado con la cantidad, la forma, la colocación y el tamaño de las compuertas.
Lo esencial
Esperamos que esta guía le haya proporcionado algunas directrices útiles de alto nivel sobre el diseño del moldeo por inyección a modo de introducción. Ahora que entiende las directrices principales y tiene acceso a recursos complementarios, está listo para diseñar increíbles piezas de plástico optimizadas para la fabricación de moldeo por inyección de precisión.
Poner en práctica estos conceptos agilizará la preproducción, evitará defectos y permitirá establecer líneas de producción robustas que bombeen productos impecables.
¿Qué preguntas de diseño le surgen cuando se aventura en su próximo proyecto de componentes moldeados por inyección? No dude en ponerse en contacto conmigo si desea seguir hablando. Siempre estoy dispuesto a ayudar a mis colegas a reforzar sus capacidades técnicas y compartir las mejores prácticas.