El moldeo por inyección de plástico es uno de los procesos de fabricación más versátiles y rentables de la actualidad. Permite la producción en masa de todo tipo de productos, desde juguetes y artículos para el hogar hasta dispositivos médicos y piezas de automóviles.
Sin embargo, a pesar de su prevalencia en innumerables industrias, el moldeo por inyección de plásticos presenta algunas desventajas y limitaciones notables que los ingenieros y diseñadores de productos deben tener en cuenta. Como profesional fabricante de moldeo por inyección de plásticoLos enumeraré en este artículo.
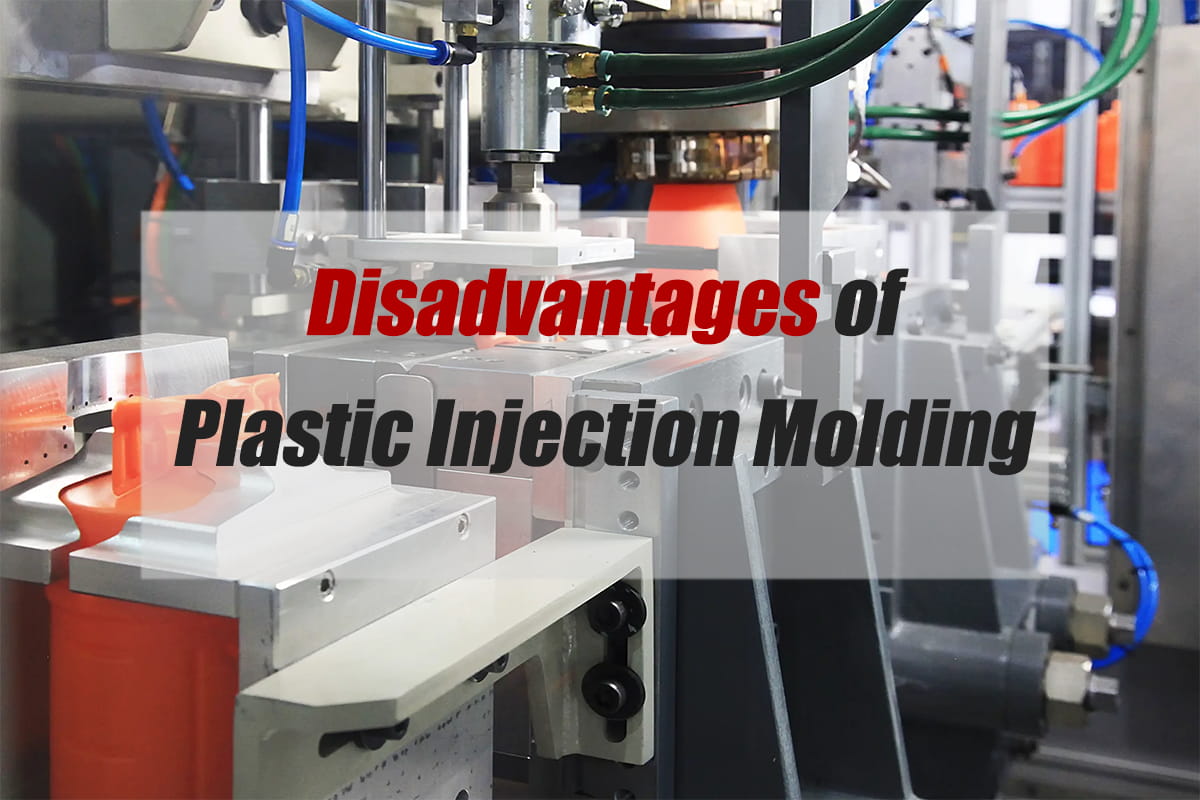
¿Cuáles son las desventajas del moldeo por inyección de plásticos?
Elevados costes de inversión inicial
Una de las desventajas más significativas del moldeo por inyección es la elevada inversión inicial que requiere. Antes de poder fabricar una sola pieza, se necesitan grandes costes iniciales para el propio utillaje del molde de inyección.
El coste de los moldes para productos de plástico estándar suele oscilar entre $1.000 y $5.000. Sin embargo, en el caso de moldes más grandes fabricados con calidad de exportación, los precios suelen superar los $50.000 y pueden llegar a varios cientos de miles de dólares.
Además de los propios moldes de inyección, también hay costes asociados al diseño de los moldes, las pruebas exhaustivas y la creación de prototipos, la planificación de la producción, la fijación y las medidas de garantía de calidad.
Si se tienen en cuenta todos estos costes iniciales, el moldeo por inyección sólo resulta económicamente viable en volúmenes de producción superiores a 100 o 150 piezas. Para series de producción muy pequeñas, de decenas o centenares de unidades, las tecnologías de fabricación aditiva como Impresión 3D o el mecanizado CNC suelen ser más rentables.
Plazos de entrega largos
Además de los elevados costes de inversión inicial, los largos plazos de entrega son otro inconveniente del moldeo por inyección de componentes de plástico. De principio a fin, el proceso completo puede durar entre 10 y 12 semanas como mínimo.
He aquí un desglose aproximado de los plazos del moldeo por inyección:
- 2-4 semanas: Diseño e ingeniería
- 4-6 semanas: Fabricación de moldes
- 2-4 semanas: Muestras, pruebas, modificaciones
- 2+ Semanas: Producción, montaje, expedición
Como ilustra esta cronología, la producción no empieza de la noche a la mañana con el moldeo por inyección. En concreto, dependiendo de la complejidad de la pieza, los plazos de entrega de las herramientas de moldeo suelen superar el mes.
Para los ingenieros y jefes de proyecto que trabajan con plazos ajustados, estos largos plazos de entrega exigen una planificación y coordinación cuidadosas si se quieren cumplir las fechas de lanzamiento. Como alternativa, soluciones provisionales como la impresión 3D de prototipos de producción pueden ayudar a verificar los diseños mientras se fabrican los moldes de inyección.
Retos del control de calidad
A pesar de su precisión y consistencia, la producción de moldeo por inyección sigue siendo propensa a problemas de calidad si no se ejecuta correctamente. Defectos como disparos cortos, rebabas, alabeo y líneas de molde pueden inutilizar rápidamente componentes complejos si no se toman medidas correctoras.
La mayoría de los defectos tienen su origen en un diseño de molde subóptimo o en controles de proceso inadecuados de parámetros clave como la temperatura, la presión, la fuerza de cierre y la velocidad de inyección. A medida que se acumulan más variables y tolerancias, mantener la coherencia supone un reto cada vez mayor.
Por ejemplo, pequeños cambios en el contenido de humedad de la resina plástica y en la temperatura del molde pueden alterar significativamente la viscosidad y la velocidad de flujo, provocando una variación sutil, pero inaceptable, entre disparos.
Por lo tanto, es esencial establecer sólidas medidas de control de calidad, especialmente cuando se colabora con un nuevo socio de moldeo por inyección. Las listas de comprobación de inspección exhaustivas y los procesos de aprobación por niveles ayudan a minimizar el riesgo.
Limitaciones de diseño
Para beneficiarse del moldeo por inyección a gran escala, las piezas de plástico deben diseñarse teniendo en cuenta las limitaciones del proceso. Sin embargo, para los ingenieros más acostumbrados a los componentes metálicos mecanizados, adaptarse a los matices de los plásticos moldeados por inyección puede resultar menos intuitivo.
Lo ideal es mantener uniformes los espesores de las paredes para garantizar una solidificación uniforme a medida que el plástico fundido dentro del molde pierde calor. Las variaciones de grosor pueden crear tensiones que se manifiesten como grietas o alabeos.
También hay que evitar los destalonamientos y otras geometrías que impiden un desmoldeo limpio. Asimismo, la incorporación de ángulos de desmoldeo facilita la expulsión de la pieza después de que la inyección moldeada se haya endurecido dentro del molde de dos placas.
Aunque los elevadores y los deslizadores pueden aliviar algunas limitaciones de diseño en torno a los rebajes, añaden costes y consideraciones de fiabilidad a la mezcla. La necesidad de acciones laterales también limita la velocidad a la que pueden producirse ciclos consecutivos de moldeo por inyección.
Restricciones del rendimiento material
Las resinas modificadas y las aleaciones de polímeros actuales permiten que el moldeo por inyección de plásticos compita con los metales -o incluso los supere- en determinadas aplicaciones que requieren flexibilidad, resistencia a la corrosión, aislamiento eléctrico o precisión.
Sin embargo, los plásticos moldeados por inyección siguen estando por detrás de las piezas de aluminio y acero en aspectos clave como la resistencia a la tracción final, la fuerza pura, la rigidez y la resistencia al desgaste. Estas limitaciones del material restringen su uso en determinadas aplicaciones estructurales, de soporte de carga y de alta durabilidad.
Por término medio, la resistencia máxima al calor de los plásticos convencionales para moldes de inyección oscila entre 180 y 220 °C, aunque las resinas especiales como el PEEK y el PPS pueden soportar más de 300 °C. Aun así, los metales superan con creces a los plásticos en aplicaciones de alta temperatura.
Mientras que los componentes metálicos toleran fácilmente el autoclave, la esterilización por vapor u otras modalidades de esterilización agresivas, esta exposición puede deformar o degradar las piezas de plástico. En consecuencia, los ingenieros de dispositivos médicos deben examinar cuidadosamente la biocompatibilidad de cada resina.
Dificultades de reciclaje
Lo ideal sería que, a medida que la sostenibilidad se convierte en una prioridad urgente en todo el mundo, los fabricantes pudieran recuperar, clasificar y reutilizar la resina de plástico después de su vida útil. Sin embargo, el reciclaje del plástico se enfrenta a importantes barreras técnicas y económicas a pesar de los intensos esfuerzos de investigación y desarrollo.
A grandes rasgos, cuatro factores complican el reciclado de plásticos en la actualidad, especialmente en el caso de los plásticos mixtos:
- Separación y clasificación
- Descontaminación
- Identificación
- Reprocesamiento
Como paso inicial, separar y clasificar los plásticos por tipos de resina es esencial para el reciclado, pero tremendamente laborioso, ya que actualmente requiere un esfuerzo manual.
Asimismo, las pinturas, los insertos metálicos, las etiquetas y los adhesivos impiden el reciclado directo y requieren una descontaminación exhaustiva para extraer el material plástico base.
En otros casos, los códigos oscuros de las resinas hacen imposible la identificación definitiva del material. Incluso cuando se puede establecer la composición química de la resina, las diferencias en la longitud de las cadenas de polímeros, las mezclas de copolímeros y la edad del material pueden afectar a las propiedades y confundir el procesamiento.
Desde el punto de vista económico, el elevado componente de mano de obra para clasificar los residuos plásticos no puede justificarse, salvo en el caso de flujos de resina de gran pureza y volumen. Pero las inversiones en infraestructuras de reciclaje químico podrían mejorar algún día la viabilidad mediante una mayor automatización del proceso.
Conclusión
Sin duda, el moldeo por inyección de plástico seguirá dominando la fabricación mundial gracias a su rentabilidad, versatilidad y precisión. Sin embargo, los ingenieros que evalúan el proceso deben moderar sus expectativas teniendo en cuenta también sus limitaciones y retos.
En concreto, los elevados costes iniciales y de utillaje exigen grandes volúmenes de producción que superen las 100.000 unidades para garantizar un retorno de la inversión convincente. Para cantidades inferiores, los métodos de fabricación aditiva como la impresión 3D tienen más sentido desde el punto de vista económico.
Aunque los plásticos poseen una flexibilidad, una resistencia química y unas propiedades de aislamiento eléctrico impresionantes, adecuadas para componentes intrincados, sus prestaciones mecánicas son inferiores a las de las piezas mecanizadas de aluminio o acero en aplicaciones críticas de automoción y aeroespaciales que soportan cargas.
Por último, a pesar de mostrar una eficiencia ejemplar en la producción de recursos, el reciclado generalizado de plásticos sigue siendo un objetivo difícil de alcanzar, lastrado por obstáculos económicos y técnicos.
En general, una evaluación realista de estas desventajas del moldeo por inyección de plásticos facilita la selección de la tecnología y sirve de base para las decisiones de diseño a la hora de planificar el lanzamiento de un nuevo producto.