Moldeo por inyección es un proceso de fabricación habitual para producir piezas de plástico a gran escala. Diseñar correctamente las piezas para el moldeo por inyección es fundamental para evitar defectos, controlar los costes y conseguir el aspecto y el rendimiento deseados. Esta completa guía de diseño describe las consideraciones clave en cuanto a geometría de la pieza, selección de materiales, utillaje y operaciones secundarias para optimizar los componentes moldeados por inyección.
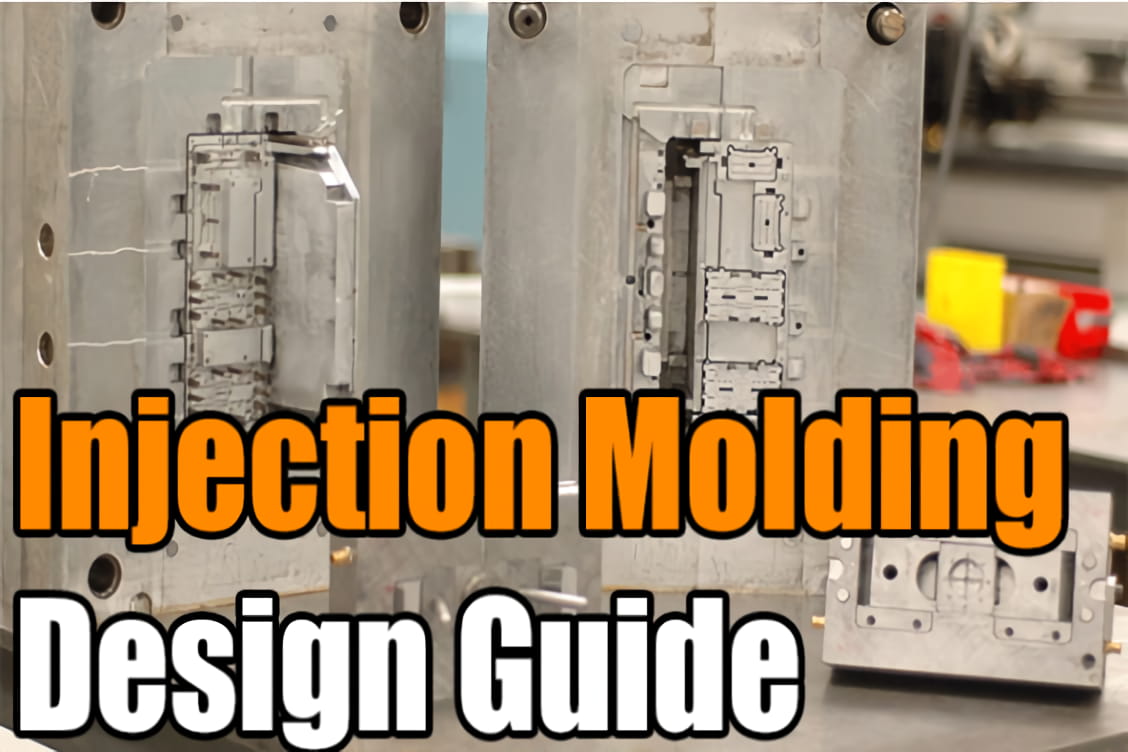
Guía de diseño de moldeo por inyección
Elementos críticos de diseño
Hay varios elementos críticos que deben tenerse en cuenta a la hora de diseñar piezas para el moldeo por inyección:
Líneas de separación
La línea de partición es el punto en el que las dos mitades de un molde de inyección se unen para expulsar la pieza enfriada y solidificada. Las líneas de partición siempre serán visibles en las piezas acabadas hasta cierto punto en función de la ubicación, los ángulos de desmoldeo permitidos y los acabados superficiales. La colocación estratégica de las líneas de separación puede ayudar a minimizar la visibilidad.
Socava
Las socavaduras se refieren a geometrías de piezas que sobresalen o causan una interferencia tal que la pieza no puede expulsarse limpiamente de un molde de inyección simple de dos piezas. Algunos ejemplos comunes son los orificios transversales, las roscas y los ganchos de ajuste a presión. Los rebajes aumentan la complejidad y los costes de las herramientas. En la medida de lo posible, las piezas deben diseñarse de forma que se eviten las socavaduras mediante técnicas como los ángulos de desmoldeo o los elementos de remodelación. Los destalonamientos inevitables pueden solucionarse utilizando machos de acción lateral y otros insertos.
Ángulos de calado
Los ángulos de desmoldeo son esenciales en todas las caras verticales de una pieza para reducir la fricción y permitir una expulsión limpia del molde. Se recomienda un ángulo de desmoldeo mínimo de 1 a 2 grados para la mayoría de las piezas, pero se requiere más para geometrías más altas o acabados superficiales texturizados.
Espesor de pared
Un espesor de pared uniforme en toda la pieza es óptimo para facilitar el flujo de material, reducir los riesgos de alabeo, minimizar los tiempos de ciclo y reducir los costes. Las especificaciones típicas de espesor de pared oscilan entre 0,060 y 0,180 pulgadas, dependiendo del material utilizado. Las transiciones graduales deben conectar las secciones con espesores de pared diferentes.
Radios y esquinas
Las esquinas afiladas concentran las tensiones y provocan fallos prematuros de la pieza. Siempre que sea posible, deben aplicarse filetes y radios generosos en todas las esquinas interiores y exteriores para mantener la resistencia.
Consideraciones de diseño avanzadas
Además de los requisitos básicos de geometría y calado, las siguientes características proporcionan una funcionalidad adicional de la pieza y requieren una mayor diligencia en el diseño:
Jefes
Los resaltes sirven como puntos de fijación para insertos o tornillos autorroscantes. Siempre que sea posible, las nervaduras finas o los refuerzos deben conectar los salientes a las paredes principales para mejorar la estabilidad y evitar las marcas de hundimiento debidas a la contracción del material.
Costillas
Las nervaduras refuerzan las piezas sin aumentar el espesor de la pared. Las nervaduras deben diseñarse de acuerdo con los límites de espesor de pared e incorporar filetes en su base para evitar concentraciones de tensiones.
Encaje a presión
Los ajustes a presión permiten el montaje de piezas moldeadas por inyección sin elementos de fijación. Al igual que otras proyecciones de la geometría de la pared nominal, el ángulo de inclinación es esencial en las paredes verticales de ajuste a presión para permitir el desmoldeo. El espesor relativo a la pared nominal y la colocación requieren un análisis adicional al diseñar ganchos o voladizos de ajuste a presión.
Bisagras vivas
Las bisagras vivas actúan como conexiones delgadas y flexibles entre segmentos de plástico rígido. La selección del material es fundamental, con polipropileno y el polietileno son opciones habituales en los productos de consumo. El grosor de las bisagras, los límites de longitud y la inclusión de hombros influyen en la durabilidad a lo largo de los ciclos de vida previstos.
Consideraciones materiales
La selección del material influye en el aspecto de la pieza, los requisitos de rendimiento, las opciones de utillaje y los procesos de fabricación necesarios. Algunas de las principales alternativas de plástico son:
- Polipropileno (PP) - Resina de bajo coste con buena resistencia química, a menudo utilizada para productos de consumo y tuberías
- Acrilonitrilo butadieno estireno (ABS) - Elección habitual cuando se necesita una mayor resistencia y ductilidad en relación con el PP. Se utiliza en armarios de automoción y electrónica.
- Policarbonato - Opción de alta resistencia ópticamente transparente cuando la resistencia a los impactos y la estabilidad dimensional son fundamentales
- Poliamida (nailon) - Preferido para piezas mecánicas que requieren mayor resistencia, fatiga y desgaste
Acabados superficiales
En las superficies de las piezas moldeadas por inyección pueden conseguirse diferentes aspectos estéticos dependiendo del pretratamiento del molde y de las texturas transferidas. Entre las alternativas comunes según las normas SPI se incluyen:
- SPI-A2 - Acabado brillante, como un espejo, conseguido mediante el pulido con diamante del molde.
- SPI-B1 - Acabado mate satinado con papel de lija de grano 600 en el molde
- Texturizado de moldes - Acabados granulados personalizados aplicados mediante moldes de granallado
Operaciones secundarias
Los pasos posteriores al moldeo, como el montaje, el etiquetado, la impresión, la soldadura o el mecanizado, pueden ampliar la funcionalidad de la pieza según sea necesario:
- Tampografía - Método para añadir logotipos, etiquetas y gráficos en color sobre superficies curvas moldeadas por inyección
- Soldadura por ultrasonidos - Fusiona componentes moldeados por separado induciendo vibraciones de alta frecuencia.
- Mecanizado CNC - Permite características de mayor precisión difíciles de integrar directamente en diseños moldeados
Lista rápida de diseño
Al finalizar los diseños de piezas moldeadas por inyección, la siguiente lista de comprobación incluye los elementos clave que deben revisarse:
- Espesor de pared uniforme de 0,060 a 0,180 pulgadas
- Ángulo de calado mínimo de 1 grado aplicado a todas las caras verticales
- Radios en todas las esquinas interiores y exteriores
- Costillas de apoyo añadidas a jefes aislados
- Cartelas que unen las costillas proyectadas a las paredes nominales
- Puerta, pasador eyector, ubicaciones de ventilación inspeccionadas
- Eliminación de socavones en la medida de lo posible
- Acabado superficial estándar SPI especificado
Si se tienen en cuenta correctamente estas consideraciones críticas de diseño, se obtendrán piezas dimensionalmente precisas con menos defectos y costes de fabricación. Póngase en contacto con nosotros si tiene alguna pregunta sobre la optimización de su próximo componente o conjunto moldeado por inyección.