Las piezas roscadas son muy comunes en innumerables sectores, desde accesorios de fontanería hasta fijaciones y botellas de plástico. La creación de componentes roscados requiere técnicas y consideraciones especializadas en comparación con las piezas de plástico convencionales. En esta completa guía, como profesional moldeo por inyección de plástico fabricante, le guiaré a través de todo lo que necesita saber sobre la fabricación de piezas de plástico roscadas mediante moldeo por inyección.
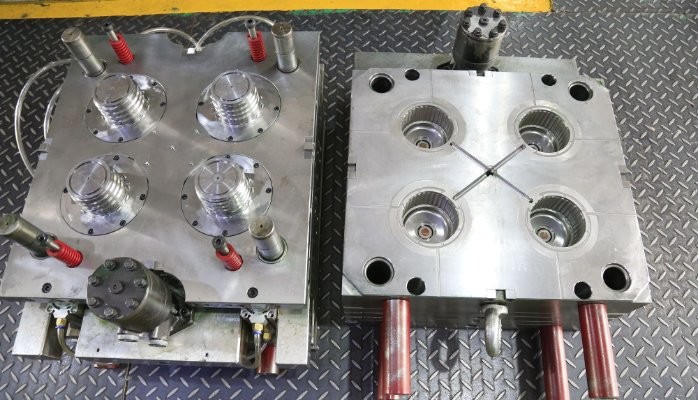
Visión general de las piezas roscadas
Las piezas roscadas contienen unas crestas en espiral, denominadas roscas, que les permiten unirse con otras roscas. Tornillos, pernos, tuercas, tapones de botellas y accesorios para mangueras son algunos ejemplos de piezas roscadas.
La principal ventaja de las roscas es que forman una conexión fuerte, estanca y reutilizable sin necesidad de soldaduras, soldaduras fuertes ni adhesivos. Basta con girar el componente roscado para que se ensamble firmemente en su pieza correspondiente.
Tipos de hilo comunes
Existen varios perfiles de rosca normalizados, entre ellos:
- Norma de rosca unificada (UNC/UNF): De uso general en Estados Unidos. Se define por el ángulo, el paso y los diámetros de la rosca.
- Rosca métrica ISO: La norma internacional con un ángulo de rosca de 60°. Especifica el paso y el diámetro de la rosca.
- NPT/NPS: Para conexiones de tubos roscados cónicos o rectos.
- ACME: Rosca trapezoidal para husillos y otras aplicaciones de transmisión de potencia.
El tipo de rosca debe ser compatible con el componente de acoplamiento. Por tanto, es fundamental seleccionar y especificar correctamente las roscas.
Consideraciones clave para roscas moldeadas por inyección
Debido a su compleja geometría, la producción de elementos roscados en plástico moldeado por inyección requiere componentes de molde y consideraciones de proceso especiales en comparación con el moldeo convencional.
He aquí algunos factores clave que hay que tener en cuenta:
1. Componentes del molde
- Núcleos roscados: Núcleos de acero templado mecanizados con el perfil de rosca objetivo. Insertados en la cavidad del molde.
- Mecanismos de desenroscado: Medios automáticos o manuales para desenganchar los núcleos roscados de la pieza moldeada.
- Núcleos laterales: Puede producir destalonamientos en las roscas para evitar la rotura.
2. Selección de materiales
- Los materiales deben tener la resistencia, dureza y ductilidad adecuadas para resistir los daños de las roscas.
- Rellenos como la fibra de vidrio reducen la flexibilidad del material durante el desmoldeo.
3. Diseño de piezas
- Ángulos de desmoldeo para facilitar el desmoldeo.
- Uniformidad del grosor de la pared.
- Bloqueos mínimos del núcleo.
Conseguir estos parámetros es crucial para producir piezas de plástico roscadas funcionales mediante moldeo por inyección.
El proceso de moldeo por inyección roscada paso a paso
Estas son las fases clave para fabricar componentes de plástico roscados mediante moldeo por inyección:
Paso 1: Diseño del molde
El molde debe estar mecanizado con precisión para que detalles como las roscas se reproduzcan con exactitud en las piezas moldeadas.
Entre las submedidas clave se incluyen:
- Diseño de la cavidad del molde en torno a la geometría de la pieza.
- Fabricación de insertos de cavidades roscadas.
- Integración de funciones para la eliminación automática o manual del núcleo.
Cualquier rebaje en las roscas puede necesitar levas o correderas de acción lateral para no obstruir la expulsión.
Paso 2: Montaje del molde
Antes de la producción, el molde debe montarse y calibrarse:
- Los pasadores y los bloques roscados del núcleo se insertan en las mitades del molde.
- Se confirma la alineación de la cavidad para reducir al mínimo las rebabas alrededor de las roscas.
- Cualquier componente de acción lateral está orientado.
- Los canales de refrigeración están conectados.
Paso 3: Moldeo por inyección
Ahora el molde completo se monta en una máquina de moldeo por inyección de plástico para comenzar la producción de piezas.
El ciclo básico incluye:
- Sujeción - Las dos mitades del molde se presionan entre sí con gran fuerza.
- Inyección - El plástico fundido sobrecalentado llena la cavidad del molde a través de canales y compuertas.
- Enfriamiento - Tras llenar completamente la impresión, los canales de enfriamiento y las paredes del molde enfrían el plástico.
- Expulsión - Los pasadores expulsan la pieza de plástico sólido del molde. Las roscas se forman en la cavidad.
- Reajuste - El molde se cierra a medida que los mecanismos automatizados retraen los machos laterales y expulsan los machos roscados.
A continuación, el molde se abre, se extraen las piezas y el ciclo automatizado se repite continuamente.
Para obtener piezas roscadas de alta calidad es necesario ajustar los parámetros de moldeo, como la temperatura de la masa fundida, la velocidad de inyección y el tiempo de enfriamiento.
Paso 4: Tratamiento posterior
- Las piezas se recortan, se acaban y se inspeccionan después del moldeo.
- Las comprobaciones funcionales evalúan la integridad de la rosca mediante una prueba de ajuste con los herrajes roscados correspondientes.
- Las piezas aprobadas se embalan y envían. Las piezas defectuosas se descartan o se granulan.
Con una construcción robusta del molde y un ajuste adecuado del proceso durante las primeras series de muestreo, el moldeo por inyección puede producir de forma fiable componentes de plástico con detalles intrincados en las roscas.
Preguntas frecuentes
¿Se puede moldear cualquier plástico con roscas?
- Técnicamente sí, pero cada material tiene requisitos diferentes en función de su viscosidad, contracción, flexibilidad, etc. Plásticos amorfos y semicristalinos como nailon, acetal, polipropileno, ABS son los más adecuados para piezas roscadas.
¿Cuántos hilos por pulgada (TPI) se pueden moldear?
- Como regla general, las roscas de plástico deben tener un paso más grueso que las de metal. Para evitar daños prematuros en las roscas de los plásticos, se suele preferir un paso de entre 10 y 20 TPI. Los pasos ultrafinos por debajo de 20 TPI requieren un moldeo de muy alta precisión.
¿Qué tolerancia pueden tener las roscas moldeadas por inyección?
- Con herramientas de precisión y control de procesos, las roscas moldeadas pueden alcanzar tolerancias 3-5% bastante ajustadas dependiendo del plástico utilizado. Pero, en general, las roscas de plástico tienen intrínsecamente tolerancias más holgadas que las roscas metálicas mecanizadas o forjadas.
¿Es adecuada la soldadura por ultrasonidos para ensamblar piezas roscadas de plástico?
- La soldadura por ultrasonidos provoca el flujo y la deformación del material, por lo que no suele ser adecuada para fijar piezas de plástico roscadas, que dependen de unas dimensiones precisas para funcionar eficazmente. En su lugar, se recomienda unir las piezas roscadas mediante técnicas de fijación convencionales.
Principales conclusiones
- Los núcleos y componentes de molde especializados permiten el moldeo por inyección de roscas de plástico.
- La flexibilidad del material y los ángulos de desmoldeo minimizan los daños.
- Los mecanismos de desenroscado automatizados mejoran la calidad y reducen los costes.
- Las roscas y tolerancias más gruesas permiten una mayor variación del proceso plástico.
Si se presta atención al diseño del molde, la asignación de tolerancias y las características del material, es posible fabricar componentes roscados de plástico intrincados mediante moldeo por inyección de forma económica a escala industrial.