Las fugas de plástico en la línea de separación son uno de los problemas más comunes en el moldeo por inyección. Estas fugas de plástico pueden afectar gravemente a la calidad y funcionalidad de la pieza. Afortunadamente, existen varias estrategias eficaces para evitar las fugas a lo largo de la línea de apertura. En esta completa guía, como profesional fabricante de moldeo por inyección de plásticodescubrirá 8 formas probadas de evitar que el plástico se escape de sus moldes.
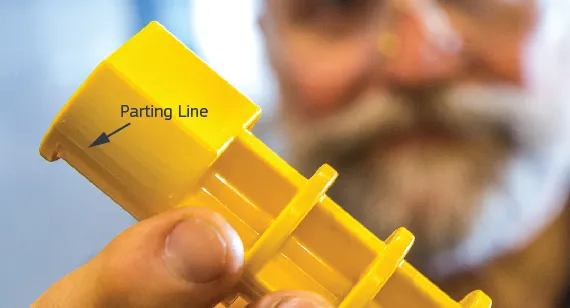
Por qué hay fugas de plástico en las líneas de separación
Antes de entrar en las soluciones, es útil entender qué causa las fugas de plástico a lo largo de las líneas de separación durante el moldeo por inyección.
La línea de apertura es el punto en el que las dos mitades de un molde de inyección se unen y se cierran herméticamente. Cuando el molde se cierra, toneladas de fuerza de cierre empujan las mitades entre sí para evitar que salga material.
Sin embargo, a veces el plástico fundido sigue chirriando a través de pequeños huecos a lo largo de la costura:
Contaminación
El polvo, el aceite, las virutas de plástico u otros residuos atascados en la línea de separación impiden que las dos superficies del molde se acoplen correctamente al cerrarse. Este pequeño espacio permite que se produzcan rebabas.
Desgaste del molde
A lo largo de miles de ciclos, la zona de contacto a lo largo de las caras de la línea de apertura se desgasta gradualmente. Estas microimperfecciones acaban permitiendo la salida de material, lo que provoca la formación de rebabas.
Ventilación inadecuada
Los gases atrapados no tienen forma de escapar de la cavidad cuando los respiraderos o los canales de ventilación están obstruidos. La excesiva presión interna fuerza entonces la salida del plástico a través del conducto de separación.
Presión de inyección excesiva
Si la presión de inyección supera la fuerza de cierre disponible, las mitades del molde pueden separarse. El plástico rellena entonces estos huecos recién abiertos, provocando rebabas.
Y eso es sólo la punta del iceberg. El alabeo, la desviación o los desplazamientos del núcleo también pueden crear vías de fuga a lo largo de las líneas de separación.
Pero, ¿la buena noticia? Existen varias formas probadas de combatir las fugas de plástico, como veremos en las secciones siguientes.
Cómo evitar fugas de plástico en la línea de separación Moldeo por inyección
Limpieza y mantenimiento de las superficies de la línea de separación
Mantenga las cosas limpias y ordenadas. Eso es Moldeado 101.
Al fin y al cabo, las partículas diminutas en la zona de la línea de apertura impiden que las mitades del molde se cierren por completo. E incluso los huecos microscópicos pueden provocar fugas, cizallamiento del material y otros problemas.
Por eso es imprescindible limpiar regularmente la línea de separación:
- Utilice aire comprimido para soplar los contaminantes sueltos
- Raspe con cuidado las virutas de plástico y las incrustaciones
- Aplique limpiador de moho y limpie suavemente las caras
Mientras limpias, inspecciona de cerca cualquier signo de desgaste. Incluso pequeñas imperfecciones que parecen inofensivas pueden degradar el rendimiento del sellado con el tiempo.
Mantenga los orificios de ventilación y los orificios de las clavijas eyectoras muy limpios, donde la suciedad se acumula fácilmente sin que se note.
Consejo profesional: Programe las limpiezas en función de ciclos, no de horas o días. Ciertos materiales generan más acumulación que otros.
Mantenimiento e inspecciones periódicas
Los moldes sucios no son los únicos responsables de las fugas de plástico. Los núcleos mal alineados, los componentes desgastados y los insertos de molde mal ajustados también pueden introducir vías de fuga.
Por eso, las inspecciones exhaustivas del moho deben complementar las limpiezas rutinarias.
He aquí una lista de comprobación general para orientar su protocolo de mantenimiento:
- Verificar que las dimensiones de los componentes del molde no se han desviado de las especificaciones originales.
- Inspeccionar el contacto general de la línea de separación utilizando películas indicadoras de presión.
- Examine detenidamente los orificios de ventilación, los pasadores eyectores y las correderas para detectar signos de desgaste.
- Garantizar un contacto uniforme entre los pilares guía y las superficies de los casquillos
- Compruebe si hay una distribución desigual de grasa o aceite en los conductos de refrigeración.
Si todo es correcto, sabrá con certeza que cualquier nuevo problema de parpadeo se debe a factores ajenos a la salud básica de la herramienta.
Establezca un calendario estructurado de inspecciones basado en ciclos u horas de funcionamiento. Aumente las frecuencias de los moldes con mayor actividad.
Aplique acabados de molde de alta calidad
Cuando dos superficies perfectamente planas se encuentran bajo presión, unas pocas partículas entre ellas pueden reducir el contacto de forma significativa.
Imagínese que esas caras no fueran tan lisas y planas. Los picos rugosos desiguales, incapaces de rellenar los valles microscópicos, dan lugar a microespacios que provocan fugas.
Por eso, la calidad del acabado en las zonas de las líneas de separación desempeña un papel fundamental. Las superficies más lisas aumentan el área de contacto cuando se acoplan. Y un contacto más estrecho equivale a una mejor estanqueidad.
La mayoría de los moldeadores por inyección especifican acabados superficiales de al menos Rz5 micras. Aunque se trata de un buen punto de partida, bajar a Rz1-3 micras proporciona un notable aumento de la capacidad de sellado por solo un moderado recargo.
Mantenga los acabados superfinos aislados sólo en las zonas de la línea de separación para minimizar el coste. Este enfoque reduce el trabajo de preparación de la superficie al tiempo que maximiza la capacidad donde más se necesita.
Diseño para una ventilación adecuada
Los gases que se escapan generan una presión tremenda dentro de las cavidades del molde. Y este aire atrapado realmente quiere ventilar.
Sin una vía de salida despejada, los gases presurizados acaban creando otras nuevas: al forzar la apertura del molde en la línea de apertura.
Garantizar una ventilación adecuada ayuda a evitar fugas de dos maneras:
- Reduce la presión de la cavidad durante el llenado
- Reduce la necesidad de abrazaderas
La colocación cuidadosa de los respiraderos y una sección transversal suficiente son suficientes. Coloque los respiraderos al final de los patrones de llenado en las regiones de empaquetamiento más lento.
Un tamaño adecuado también evita los atascos provocados por pequeños tapajuntas. Como norma general, opte por profundidades de ventilación de aproximadamente 70% del grosor de la pared. Y para las anchuras, limítese a unas 5 veces el grosor de la pared.
Los canales de ventilación se integran perfectamente con los circuitos de flujo de agua sin interrumpir la refrigeración. Las rejillas de ventilación estratégicamente colocadas equilibran el rendimiento con la complejidad del molde.
Aplique una fuerza de sujeción suficiente
En una batalla entre la presión de inyección y la fuerza de apriete, el plástico fluye buscando el camino de menor resistencia.
Y cuando se pierde fuerza de cierre, esas vías de flujo acaban atravesando la línea de apertura del molde. El material sobrante se solidifica, dejando tras de sí las evidentes rebabas.
Para garantizar una fuerza de sujeción adecuada es necesario calcular las presiones totales. A continuación, especificar el tonelaje de la abrazadera suficiente para resistir el escape.
Por ejemplo, las presiones de llenado por inyección, empaquetado, descomposición del material y otras fuentes suelen superar los 5.000 psi. Las fuerzas totales que intentan abrir el molde se acumulan rápidamente.
Una buena regla general es prever al menos 1,5 veces la presión de cavidad proyectada. Y no menos de 3 toneladas por pulgada cuadrada a lo largo de la línea de separación.
La capacidad de sujeción limita el tamaño de las piezas más que cualquier otra cosa. La creatividad en aspectos fundamentales como la minimización del área proyectada reduce los elevados costes asociados a los sistemas hidráulicos avanzados.
Presiones de inyección máximas más bajas
Si se especifica una fuerza de apriete suficiente, se obtiene una resistencia suficiente contra la salida del flujo de plástico.
Pero las presiones de inyección excesivamente altas sobrecargaban incluso las abrazaderas más robustas. Creando fugas. Disparos cortos. Destellos. Y otros defectos.
Un cuidadoso ajuste del proceso ayuda a evitar los picos de presión al tiempo que garantiza el llenado completo de la cavidad.
Empiece por elegir las resinas con los índices de fluidez que mejor se adapten a su aplicación. Las viscosidades de los termoplásticos influyen directamente en las presiones de inyección resultantes.
Los canales de flujo helicoidales favorecen entonces el llenado gradual sin que se produzcan puntos problemáticos de impacto del flujo de la fuente.
El cambio de colectores fríos a colectores aislados o calefactados elimina prácticamente la lentitud en la salida de la masa fundida que provoca defectos en las piezas de disparo corto.
Y la optimización de las velocidades de inyección lentas seguidas de etapas de empaquetado y retención altas favorecen el empaquetado en cavidades a las presiones más bajas.
Todo se reduce a un control preciso. Los sensores de monitorización que proporcionan retroalimentación PID implementan automáticamente ajustes que maximizan la calidad.
Invierta en herramientas sin rebabas
Pregunte a cualquier moldeador cuál es el camino más seguro para evitar absolutamente las rebabas y todos le dirán lo mismo:
Sin flash.
Aunque el utillaje de precisión ultraelevada cuesta bastante más por adelantado, algunas aplicaciones justifican la importante inversión de capital a largo plazo gracias a la mejora radical del rendimiento.
Hablamos de tolerancias inferiores a 0,005" mantenidas en toda la base del molde. Acabados submicrónicos en las zonas de la línea de partición. Componentes guiados que eliminan por completo los desplazamientos.
Los moldes sin rebabas incorporan incluso ventilación multietapa que gestiona altas cargas de desgasificación a la vez que evita fugas tanto grandes como microscópicas.
Para aplicaciones de moldeo críticas en las que la perfección es la única opción, el utillaje sin flash cumple lo prometido cuando se configura correctamente. Solo tiene que estar preparado para pagar más a cambio de una capacidad sin igual.
Controlar cuidadosamente las condiciones de transformación
El ajuste de los puntos de ajuste del proceso recae directamente sobre los hombros del técnico de moldeo. Pero las pequeñas sobrecorrecciones que intentan compensar las fluctuaciones sospechosas causan más daños que beneficios.
Presión. Temperatura. Velocidad. Todos ellos exigen un ajuste fino y juicioso para equilibrar necesidades contrapuestas. Saber qué mandos girar y cuándo es crucial.
Como ya se ha dicho, reducir la viscosidad disminuye la presión. Pero si se va demasiado lejos, el material se quema fácilmente en pequeños espacios. O se quema, degradando el rendimiento mecánico.
Del mismo modo, las fugas menores parecen justificar el aumento de los tiempos de empaquetado y retención. Pero las duraciones prolongadas introducen innecesariamente tensiones de orientación en el camino.
Confíe en los datos, no en la intuición para dirigir los pasos siguientes. Los sensores que indican los umbrales activan automáticamente los ajustes de los puntos de ajuste a través de las interfaces de la máquina. Las pruebas rápidas verifican los efectos en los parámetros objetivos de calidad.
Mantenerse firmemente anclado en los fundamentos hace que los procesos funcionen sin problemas, independientemente de la función que se desempeñe. Dar un paso atrás permite evaluar ecosistemas más amplios y conectar las decisiones con los resultados. La comprensión cohesiva alinea los esfuerzos optimizando los resultados en todos los departamentos.
Cómo eliminar el flash existente
A pesar de todos los esfuerzos, a veces las rebabas de plástico siguen apareciendo. Afortunadamente, existen varios métodos eficaces para eliminar las rebabas tras la expulsión de las piezas.
El recorte manual con cuchillas o limas funciona muy bien para prototipos y tiradas cortas. Es lento, pero garantiza una eliminación mínima de material de las dimensiones críticas. Los diseños exclusivos de las fijaciones facilitan el posicionamiento en lugares difíciles.
Los medios abrasivos, como la arena inyectada en cubas vibratorias, eliminan rápidamente un gran volumen de rebabas. Los medios de cribado de piezas garantizan que el tamaño de las partículas sea el adecuado para eliminar las rebabas sin comprometer la integridad de los componentes debido a un adelgazamiento general involuntario. Aunque los sistemas de bajo coste se escalan con facilidad, los escudos de seguridad son definitivamente imprescindibles para los operarios.
Para materiales difíciles como PEEK y siliconaEl desbarbado criogénico ha despegado recientemente. Las piezas se sumergen en nitrógeno líquido, fragilizando selectivamente sólo las partes delgadas del revestimiento. La vibración desprende fácilmente las partes quebradizas sin dañar el plástico dúctil que hay debajo. Es sorprendentemente barato, dado lo exótico del proceso, y no genera residuos secundarios que deban eliminarse.
Conclusión
Las fugas de plástico son habituales, pero no inevitables. La aplicación de las directrices aquí descritas contribuye en gran medida a evitar las fugas en la línea de separación, incluso en las aplicaciones más exigentes.
Para empezar, el primer paso inspecciona las causas de las fugas. Tratar la contaminación o el desgaste en esta fase temprana prolonga considerablemente la vida útil del molde.
El mantenimiento proactivo, junto con pequeños ajustes de las herramientas, garantiza que los problemas de fugas no vuelvan a producirse después de haber solucionado los problemas iniciales. El mecanizado de precisión centrado en las superficies de sellado combinado con una ventilación suficiente reduce las posibilidades de que el plástico escape de las cavidades bajo presión.
Y para los trabajos más duros en los que la única opción es la ausencia total de rebabas, el utillaje sin rebabas de alta gama cumple lo prometido. Aunque son caros, los resultados de rendimiento sin precedentes pueden justificar la inversión de capital inicial para determinados programas.
Al final, atenerse a los principios básicos suele ganar la batalla contra el flasheo la mayoría de las veces. Pero cuando todo lo demás falla, existen varias técnicas eficaces para eliminar el flasheo y devolver las piezas a su estado original.
Ahora dispone de un plan completo para atajar las fugas de plástico en su origen. La aplicación de estas directrices reduce significativamente el impacto de las molestas salpicaduras en las operaciones de fabricación. La mejora de la calidad y el rendimiento se traduce en unos resultados finales espectaculares.