En el moldeo por inyección, el canal es un componente crucial que guía el plástico fundido desde la boquilla de inyección hasta las cavidades del molde. Como profesional fabricante de moldeo por inyección de plásticoPor ello, estoy escribiendo esta guía completa para cubrir todo lo que necesita saber sobre los patines, incluidos los tipos, las consideraciones de diseño, cómo afectan a la calidad de las piezas y mucho más.
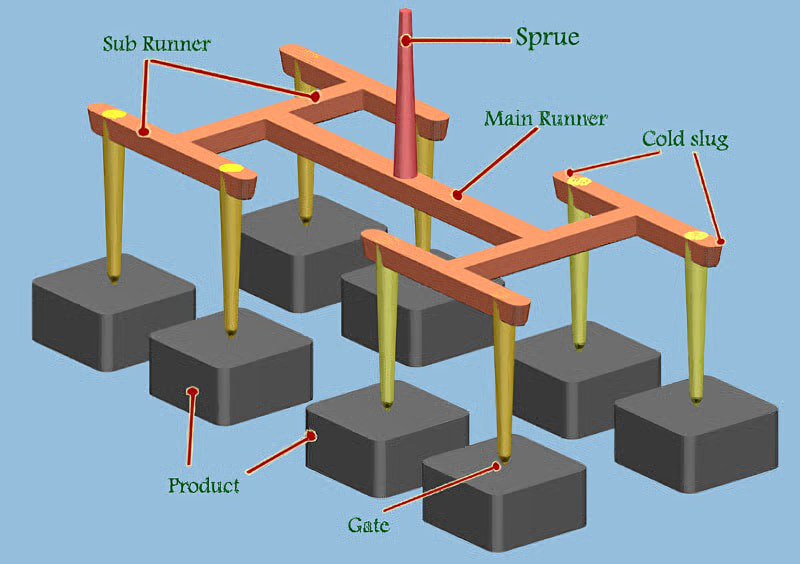
¿Qué es una corredera en el moldeo por inyección?
Un canal es un conducto cortado en el molde que transfiere el plástico fundido desde la boquilla de inyección a las cavidades durante el proceso de moldeo por inyección. Sirve como conducto que permite que el plástico fluya uniformemente hacia las cavidades.
Unas guías bien diseñadas son esenciales para producir piezas uniformes y de alta calidad. El tamaño, la forma y la posición de los patines influyen directamente en la rapidez de llenado de las cavidades, el desperdicio de material, la calidad de las piezas y los tiempos de ciclo.
Componentes del sistema de rodadura
El sistema completo de corredores está formado por unos pocos componentes clave:
Colada - En el primer segmento, el plástico fundido entra por la boquilla de inyección. El bebedero introduce material en los canales.
Corredores - Canales de diversas longitudes y diámetros que distribuyen el material a las compuertas del molde.
Puertas - Los puntos de transición finales constreñidos de los corredores a las cavidades de las piezas. Las compuertas regulan el flujo hacia las cavidades.
Juntos, estos elementos trabajan cohesivamente para proporcionar un frente de flujo uniforme de plástico en todas las cavidades simultáneamente. El objetivo final es producir piezas totalmente rellenas y sin defectos en el menor tiempo de ciclo posible.
Sistemas de canal frío frente a sistemas de canal caliente
Existen dos tipos principales de sistemas de canal de moldeo por inyección: canales fríos y canales calientes:
Corredores del frío
Los canales fríos se solidifican dentro del molde junto con las piezas moldeadas. El bebedero, los canales y las piezas permanecen unidos como una pieza sólida en el momento de la expulsión. Los canales fríos rellenos de material representan residuos que deben retirarse y reprocesarse o desecharse.
Las cámaras frías permiten fabricar moldes más sencillos, reducir los costes de utillaje, flexibilizar el diseño y adaptarse a una gran variedad de resinas. Sin embargo, generan más residuos y tienen tiempos de ciclo más largos en comparación con los canales calientes.
Corredores calientes
Los canales calientes utilizan colectores y boquillas calentados para mantener el plástico fundido mientras fluye hacia las cavidades. En el momento de la expulsión, las piezas solidificadas se expulsan sin bebederos ni canales. Esto reduce los residuos y acelera los tiempos de ciclo.
Los moldes de canal caliente son más complejos y costosos de producir que los de canal frío. Aunque a largo plazo, la reducción de residuos puede suponer un importante ahorro de costes en escenarios de producción de gran volumen.
Por qué es clave un diseño adecuado de las guías
El rendimiento de cualquier molde de inyección depende en gran medida del diseño del sistema de canales. Por eso es tan importante optimizar el diseño de los canales:
Tiempo de llenado y presión
Los canales de tamaño adecuado llenan las cavidades más rápidamente al permitir el flujo con menos pérdida de presión. Los canales finos y largos pueden congelarse prematuramente y provocar disparos cortos.
Calidad de las piezas
Un diseño de canal equilibrado proporciona un frente de flujo de masa fundida uniforme a todas las cavidades. Esta consistencia produce propiedades y apariencia uniformes en cada pieza. Los sistemas desequilibrados provocan variaciones entre cavidades que causan problemas de calidad.
Eficiencia del ciclo
Un exceso de canales implica un aumento de los tiempos de solidificación y enfriamiento, lo que ralentiza los ciclos. Un diseño optimizado minimiza el volumen de los canales para enfriar y expulsar rápidamente las piezas.
Ahorro de material
Los canales más cortos y de menor diámetro reducen el desperdicio de plástico de bebedero y canal. Esto supone un importante ahorro de costes, especialmente en aplicaciones de canal frío.
Directrices de diseño de Key Runner
Estos son algunos consejos cruciales para diseñar un sistema de corredores eficaz:
Dimensionamiento
1. Diámetros - Deben dimensionarse adecuadamente en función de factores como el grosor de la pared de la pieza, la longitud de flujo, las propiedades de la masa fundida y la velocidad/presión de inyección. Los diámetros típicos oscilan entre 2 mm y 10 mm.
2. Longitudes - Reducir al mínimo todos los segmentos del canal: mantener los recorridos desde el bebedero hasta las compuertas lo más cortos posible. Las longitudes de paso largas reducen la presión y favorecen la congelación prematura.
Equilibrio
3. Vías de flujo iguales - Asegúrese de que las rutas a cada cavidad tengan la misma longitud para proporcionar condiciones equilibradas. Utilice simulaciones de flujo para validar el rendimiento.
4. Puertas estratégicas - Aumentar el número de compuertas/ubicaciones para proporcionar un acceso más directo a la cavidad y minimizar el volumen de corredores.
Configuración
5. Simplicidad - Utilice el sistema menos complejo que satisfaga los objetivos de rendimiento. Más sencillo es mejor. Evalúe la necesidad de corredores secundarios o subpuertas.
6. Diseño racionalizado - Los patines se curvan suavemente para seguir los contornos en lugar de girar bruscamente en ángulos. Elimine las zonas muertas donde el material puede estancarse.
Si se tienen en cuenta correctamente estos elementos de diseño, cualquier sistema de canalización se prepara para un éxito fiable, maximizando la calidad y la eficiencia.
Cómo afectan las correderas a la calidad de las piezas moldeadas por inyección
Los fallos en el trazado del canal suelen manifestarse como defectos visibles de las piezas o problemas de rendimiento. He aquí cómo:
Relleno desequilibrado - Cuando las vías de flujo presentan diferencias drásticas en las pérdidas de presión, las cavidades se llenan a ritmos diferentes. Un llenado más lento permite que el material se enfríe de forma desigual dentro del molde, creando líneas de soldadura visibles, marcas de hundimiento, huecos o alabeos.
Congelación prematura - Un tamaño inadecuado del canal en relación con las longitudes de flujo ahoga la presión, permitiendo que la masa fundida se congele antes de llenarse completamente. El resultado son piezas cortas con detalles incompletos.
Cizalla - Las transiciones o constricciones angulares excesivas degradan los polímeros por sobrecalentamiento y enfriamiento. Provoca cambios localizados en las propiedades del material.
Cada uno de estos defectos comunes apunta a deficiencias subyacentes en el diseño del corredor.
Optimización y análisis del diseño de los patines
Crear un sistema de corredores óptimo es una empresa compleja que requiere experiencia y herramientas de simulación especializadas. He aquí una visión general del enfoque de diseño moderno:
1. Diseño conceptual - La configuración inicial del canal se esboza a grandes rasgos basándose en la geometría de la pieza, la selección del material, las propiedades de procesamiento y la experiencia.
2. Análisis del flujo de molde - Los estudios de simulación detallados evalúan los diseños propuestos en condiciones reales. Realiza predicciones de rendimiento precisas. Permite explorar rápidamente múltiples ideas "hipotéticas" para perfeccionar la estrategia.
3. Validación final - Los diseños óptimos derivados del análisis se prueban en última instancia empíricamente mediante el muestreo real del molde. Ofrece la oportunidad de ajustar la configuración antes de fabricar el molde a escala real.
El uso de métodos de análisis en los diseños evita costosas correcciones posteriores en caso de que las opciones no óptimas se conviertan en acero. La inversión de tiempo inicial se amortiza sustancialmente a lo largo de la vida útil del molde.
Preguntas frecuentes sobre la corredera de moldeo por inyección
He aquí las respuestas a algunas preguntas frecuentes sobre los patines de moldeo por inyección:
¿Cuál es el mejor diámetro de corredor?
Los diámetros típicos oscilan entre 2 mm y 10 mm, en función de factores como la longitud de flujo, la viscosidad del material y la velocidad de inyección. Los canales más anchos permiten velocidades de llenado más rápidas, pero se solidifican más lentamente, lo que aumenta la duración de los ciclos.
¿Dónde deben situarse las puertas de acceso a las cavidades?
Las compuertas deben introducirse en las secciones de paredes más gruesas de las piezas en los puntos exteriores menos visibles. Esto permite un llenado más rápido y un desengrase más sencillo, al tiempo que se minimizan las imperfecciones visibles.
¿Cómo deben ramificarse los corredores hacia múltiples cavidades?
Un canal principal debe dividirse en ramificaciones espaciadas uniformemente que conduzcan directamente a cada compuerta de cavidad en las mismas longitudes. Esto garantiza unas condiciones de llenado equilibradas y simultáneas en todas las cavidades.
¿Qué ventajas tiene el canal caliente frente al canal frío?
Las cámaras calientes eliminan los residuos y permiten ciclos más rápidos. Sin embargo, los canales fríos cuestan menos al principio y funcionan con más materiales. Determine las ventajas y desventajas en función de las prioridades o restricciones específicas de la aplicación.
¿Qué longitud debe tener un canal de inyección?
Lo más corto posible. En general, mantenga los tramos por debajo de 2 pies de longitud si la aplicación lo permite. Si son más largas, se corre el riesgo de pérdidas excesivas de refrigeración y presión que degraden la calidad de la pieza final.
¿Cómo crear el sistema de corredores más rentable?
Centrarse en minimizar las dimensiones para utilizar la menor cantidad de material sin dejar de llenar suficientemente las piezas. La colocación estratégica de las compuertas también minimiza el trabajo de degradación. Evite las geometrías demasiado complejas cuando una ruta más sencilla produce los mismos resultados. Utilice herramientas de análisis para encontrar las compensaciones óptimas.
Conclusión
La optimización de los canales es crucial para lograr el éxito en la fabricación de moldes de inyección en cualquier sector. Aunque invisibles para los usuarios finales, estos componentes "entre bastidores" ponen en escena todo lo necesario para una producción fiable y eficiente de piezas de plástico de alta calidad a partir de todos y cada uno de los moldes.