¿Qué es la posición de cambio en el moldeo por inyección?
La posición de conmutación, también conocida como punto de conmutación V/P, es un punto de transición crucial en el proceso de moldeo por inyección. Esta posición indica el momento en que la máquina de moldeo por inyección pasa de una etapa de llenado impulsada por la velocidad a una etapa de envasado impulsada por la presión.
Comprender qué es la posición de cambio y cómo optimizarla es clave para producir piezas moldeadas uniformes y de alta calidad. En esta completa guía, como profesional fabricante de moldeo por inyección de plásticole explicaré todo lo que necesita saber para determinar y controlar la posición de conmutación en el moldeo por inyección de precisión.
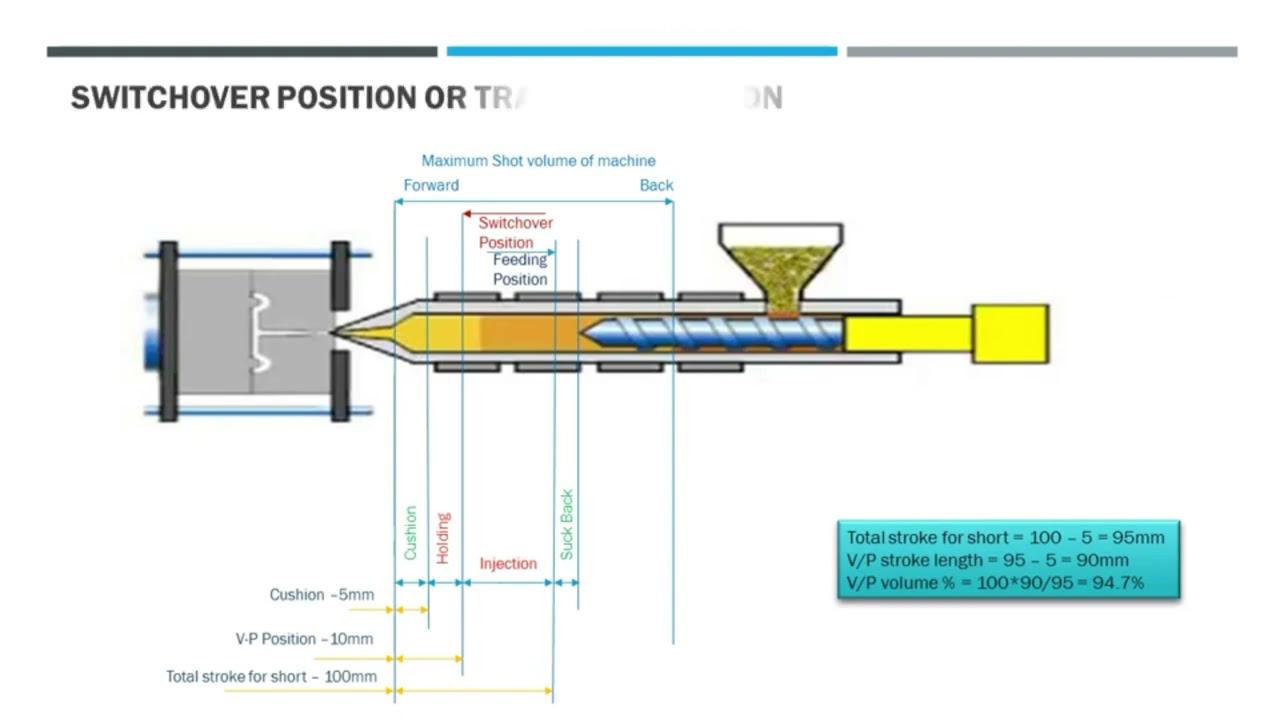
¿Cuándo se produce la transición?
Durante el ciclo de moldeo por inyección, hay dos etapas distintas que llenan las cavidades del molde con plástico fundido:
- La fase de llenado o inyección
- La fase de envasado o conservación
La posición de conmutación marca la transición entre estas dos etapas:
- Etapa de llenado: El tornillo sale disparado hacia delante, inyectando plástico fundido en el molde a una velocidad controlada. El objetivo es llenar rápidamente alrededor de 95-98% del molde.
- Conmutación: En la posición de conmutación, la máquina cambia de control de velocidad a control de presión. Esto suele ocurrir cuando la cavidad está 95-98% llena.
- Etapa de embalaje: El tornillo aplica una presión constante para llenar el molde y compensar la contracción del material al enfriarse.
En resumen:
- La posición de conmutación es la transición del control de velocidad al control de presión.
- Suele ocurrir cuando la cavidad del molde está 95-98% llena
- Determinar el punto óptimo de conmutación es crucial para la coherencia
Veamos ahora cómo determinar cuándo debe producirse la conmutación.
¿Cómo se determina la posición de conmutación?
Las máquinas de moldeo por inyección pueden detectar de varias formas cuándo pasar del llenado al envasado:
1. Por posición del tornillo
Es el método más popular. La máquina controla el movimiento lineal del husillo durante la inyección. Cuando el husillo alcanza una posición preestablecida, normalmente 95-98% de su posición máxima de avance, se activa la conmutación.
La posición del tornillo es un indicador del llenado de la cavidad. La lógica es que si el tornillo se ha movido a una posición determinada, la cavidad del molde debería estar ahora llena de plástico en su mayor parte.
Sin embargo, este método puede ser incoherente:
- Las diferencias en la densidad o viscosidad del material de un disparo a otro alteran la correlación entre la posición del tornillo y el porcentaje de llenado de la cavidad.
- El desgaste del tornillo y del barrilete puede modificar los valores de posición con el paso del tiempo.
Aun así, la posición del tornillo es sencilla y suficiente para muchas aplicaciones.
2. Por presión
Algunas máquinas pueden cambiar de control de velocidad a control de presión cuando la presión de inyección medida alcanza un valor de consigna.
A medida que el molde se llena de plástico, la presión aumenta gradualmente. Cuando la presión alcanza el nivel preestablecido, que suele indicar un llenado 95%+, se produce la transición.
Esto elimina las incoherencias causadas por el desgaste de los tornillos y los cambios en la consistencia del material. La presión se correlaciona directamente con el llenado de la cavidad, independientemente del estado del equipo o resina diferencias de lote.
Sin embargo, este método puede fallar si factores como la velocidad de inyección o la temperatura del molde cambian significativamente.
3. Por tiempo
Otra opción es conmutar en función del tiempo de inyección. La máquina utiliza simplemente un temporizador para realizar la transición en un momento constante de cada ciclo.
Por ejemplo, el análisis de datos puede mostrar que 1,4 segundos de inyección a una velocidad determinada llenan de forma fiable 95% del molde. Así, la máquina cambiaría de control de velocidad a control de presión a los 1,4 segundos cada vez.
Sin embargo, este enfoque rara vez es factible. Para establecer y mantener un valor de tiempo preciso, parámetros como el tamaño de la pieza, la viscosidad del material, la velocidad de inyección y el diseño del molde deben ser extremadamente constantes de una tirada a otra. En la mayoría de los escenarios del mundo real, hay demasiadas variables incontrolables como para confiar en un temporizador fijo.
4. Por presión de cavidad
Por último, los sensores de presión de cavidad ofrecen la forma más avanzada y precisa de determinar la posición de conmutación.
Unos sensores discretos colocados en el molde miden la presión en tiempo real dentro de las cavidades durante la inyección. Cuando los sensores indican que la presión alcanza un objetivo, correspondiente al llenado 95%, se activa la conmutación.
Este enfoque tiene en cuenta las inevitables incoherencias entre disparos, como los cambios de viscosidad del material, las fluctuaciones de temperatura, el desgaste de los tornillos, etc. También elimina las variables de desviación del molde que se encuentran en los sensores montados en la máquina.
Sin embargo, la integración de estos sensores añade costes y complejidad. Cada molde debe estar equipado con sensores cableados o inalámbricos y el hardware de transmisión de datos necesario para comunicarse con el controlador central.
Por qué es importante hacer bien la transición
La posición de conmutación une la fase de inyección y la fase de envasado. Garantiza que la cavidad se llene correctamente justo cuando la máquina pasa a aplicar presión de envasado.
Hacer bien esta transición es crucial para moldear piezas de alta calidad:
- Conmutación prematura puede causar disparos cortos. Si la presión disminuye antes de que la cavidad se llene completamente, el material dejará de fluir, dejando secciones sin llenar.
- El cambio a la empaquetadura después del llenado de la cavidad puede dar lugar a intermitente en la línea de separación o en los pasadores eyectores. El material sobrante no tiene otro destino que salir.
- El punto de cambio óptimo equilibra el llenado rápido de la cavidad al tiempo que garantiza una presión suficiente para llenar el molde. El resultado es estabilidad dimensional tiro a tiro.
Para llevar: Un tiempo de conmutación constante, que se activa en torno al llenado de 95%, permite un llenado uniforme de la cavidad ciclo tras ciclo. Esto se traduce en pesos y dimensiones estables de las piezas, menos pérdida de piezas desechadas y componentes de mayor calidad.
Cómo optimizar la posición de conmutación
Comience por revisar los datos históricos del proceso para establecer un valor objetivo inicial de cambio. Los éxitos o fracasos pasados moldeando la misma herramienta con el mismo material proporcionan una línea de base razonable.
Recopile conjuntos de datos que relacionen los valores de conmutación registrados y las métricas de calidad de las piezas ciclo a ciclo. El registro de la posición del husillo, la presión, la presión de la cavidad, el tiempo de llenado, etc. permite evaluar las correlaciones entre la conmutación y las dimensiones clave a lo largo de numerosos ciclos:
- ¿El cambio se produce de forma constante en una posición o hay variaciones de un tiro a otro?
- ¿Se correlacionan las transiciones tempranas o tardías con piezas fuera de especificación?
- ¿Qué valor de conmutación tiende a producir la mayor estabilidad dimensional?
El análisis de estas relaciones de datos ayuda a acotar la posición óptima. Las pruebas de validación adicionales ajustan la configuración de la máquina, como la velocidad de inyección, la temperatura del molde, etc., para ayudar a modelar y mantener las condiciones deseadas en varios ciclos.
Puntos de partida típicos para la posición de conmutación según el método de transición:
- Posición del tornillo: 95-98% de recorrido completo del tornillo
- Presión de inyección: ~95% de presión máxima de llenado
- Sensores de presión de cavidad: 90-98% de la presión de llenado requerida
Las precisas máquinas eléctricas de hoy en día y los controles de proceso más inteligentes permiten marcar posiciones de cambio altamente repetibles para obtener componentes moldeados increíblemente uniformes.
El desarrollo de un proceso sólido con un control optimizado de la conmutación V-P ofrece enormes ventajas de calidad. Pero sin una recopilación de datos y una validación diligentes desde el principio, combinadas con una supervisión disciplinada y continua, incluso las variaciones más pequeñas pueden socavar todo el esfuerzo. Una verificación rigurosa del proceso garantiza una producción de precisión sostenida durante largos periodos de producción.
Conclusión
En posición de conmutación marca la transición vital durante el moldeo por inyección cuando la máquina pasa de llenar la cavidad a una velocidad controlada (inyección) a aplicar una presión constante (empaquetado). Este cambio se produce normalmente a 95-98% de llenado de la cavidad.
Seleccionar el más adecuado método de detección de conmutación - La posición del tornillo, la presión de inyección, el tiempo preciso o los sensores directos de cavidad permiten determinar cuándo el molde ha alcanzado el porcentaje de llenado parcial objetivo. Esto activa el comando de cambio calculado de llenado a envasado ciclo tras ciclo.
Una estrecha correlación entre los puntos de datos de conmutación supervisados y las características de salida medibles ayuda a identificar los valores de transición óptimos. El mantenimiento de estos parámetros de proceso idealizados ayuda a maximizar la productividad y minimizar las desviaciones. La validación cuidadosa de que sólo se producen piezas conformadas correctamente que cumplan todas las especificaciones constituye una garantía de calidad esencial.
Con cientos de ajustes de dispositivos interconectados y propiedades de materiales que influyen en la precisión general, verificación del rendimiento mediante una evaluación exhaustiva de los datos confirma que los límites de calidad medidos estadísticamente cumplen de forma sostenible las expectativas a lo largo de campañas de fabricación prolongadas.
Ahora ya sabe qué es exactamente la posición de conmutación y cómo aprovecharla para un control meticuloso del proceso. La activación sistemática de la transición en el punto ideal de la secuencia de llenado y envasado favorece una enorme uniformidad de las piezas y minimiza las variaciones que merman la eficacia y la calidad.
¿Qué preguntas tiene aún sobre la determinación y optimización de la posición de conmutación para sus aplicaciones de moldeo por inyección de precisión? Hágamelo saber en los comentarios.