¿Se ha preguntado alguna vez por qué destaca la fabricación italiana de productos médicos?
Supongo que sí, ya que estás aquí buscando el 10 principales empresas de moldeo por inyección médica en Italia.
Y no te culpo.
Italia se ha convertido silenciosamente en una potencia en el moldeo por inyección de componentes médicos, combinando sus legendarias habilidades de diseño con la tecnología de vanguardia para crear algunos componentes médicos realmente impresionantes.
En esta guía, como profesional fabricante de moldeo por inyección médicaEn este artículo, analizaré exactamente qué empresas italianas están a la cabeza en 2025, qué las hace especiales y cómo elegir el socio de fabricación adecuado para sus proyectos de dispositivos médicos.
Vamos a sumergirnos.
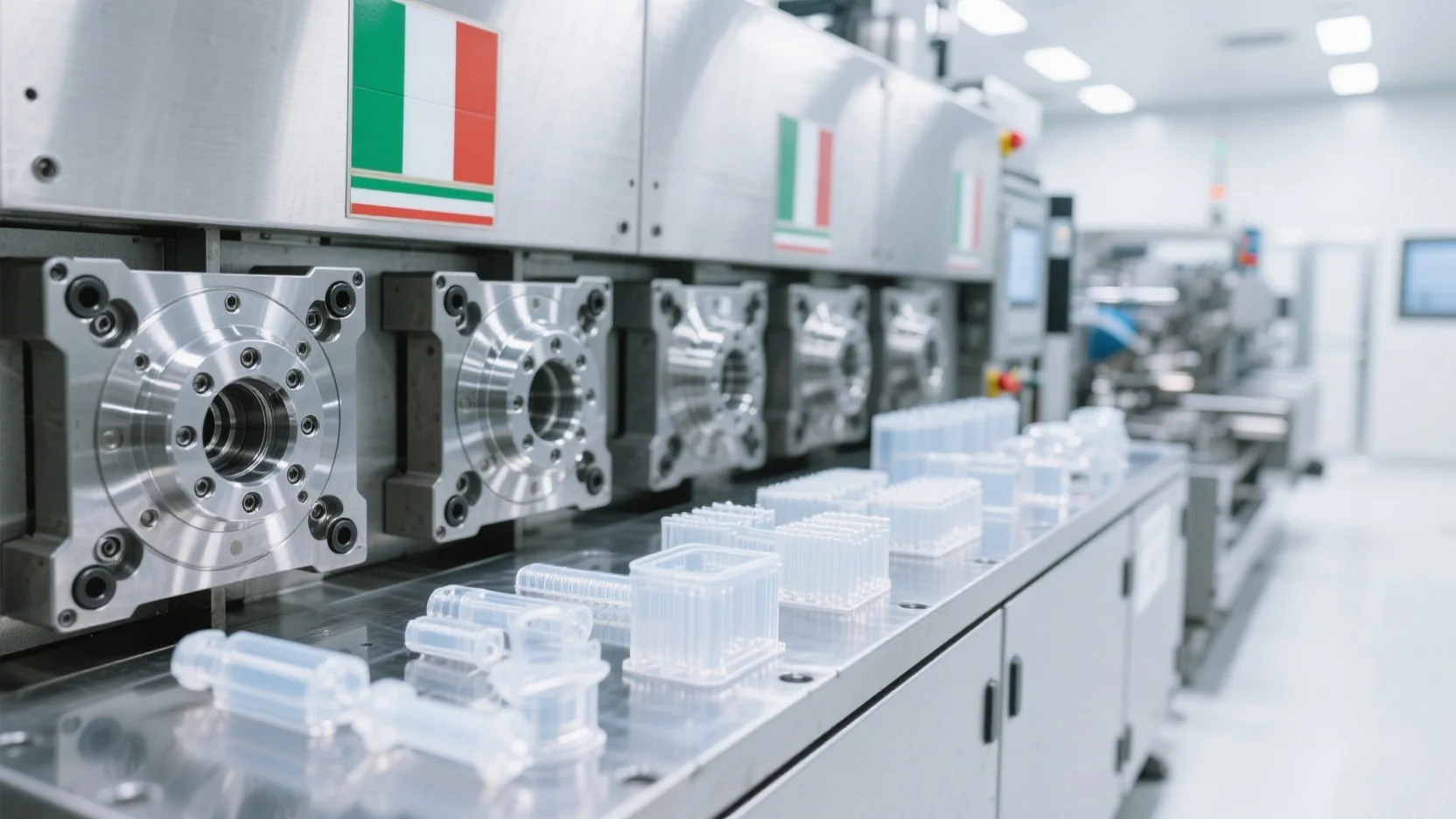
Por qué los moldes médicos italianos arrasan en 2025
Antes de pasar a la lista, hay algo que debes saber:
Las empresas italianas de moldeo por inyección médica no sólo compiten a nivel mundial, sino que a menudo van a la cabeza. He aquí por qué:
- ADN del diseño: Seamos realistas: los italianos saben de diseño. Esto va más allá de la moda y se extiende a la excelencia técnica de los componentes médicos.
- Obsesión por la calidad: La cultura manufacturera italiana tiene tolerancia cero con el "suficientemente bueno".
- Tecnología y tradición: Combinan siglos de conocimientos técnicos de fabricación con tecnología punta.
- Ninjas reguladores: ¿Navegar entre los requisitos MDR de la UE y los de la FDA? Las empresas italianas dominan este complejo panorama.
- Innovación de materiales: Muchos colaboran con instituciones de investigación en polímeros médicos de nueva generación.
Muy bien, basta de antecedentes. Vayamos a las empresas por las que has venido.
Las 10 principales empresas de moldeo por inyección en Italia
1. MediTech Plastics (Milán)
Si ha utilizado un dispositivo médico últimamente, es muy probable que MediTech haya participado en su fabricación.
Fundada en 1982, esta empresa se ha convertido en una auténtica bestia en el mundo del moldeo médico. Su sede de Milán alberga unas amplias instalaciones de 125 000 pies cuadrados con salas blancas de clase 7 que pondrían celosa a la NASA.
Lo que les hace especiales:
- Capacidad de micromoldeo hasta componentes más pequeños que un grano de arroz
- Sobremoldeo multimaterial para dispositivos complejos
- Validación de procesos que satisface incluso a los auditores de calidad más exigentes
En 2025, ampliaron su capacidad de moldeo por inyección de silicona en 40% para satisfacer la creciente demanda de dispositivos médicos portátiles. Su lista de clientes incluye básicamente todas las grandes empresas de dispositivos médicos de las que has oído hablar.
2. BioPharma Plastics (Roma)
Mientras algunos moldeadores intentan hacer de todo, BioPharma ha optado por la vía de la especialización, centrándose exclusivamente en los componentes de administración de fármacos.
Este enfoque ha dado sus frutos.
Por qué destacan:
- Sus ingenieros hablan con fluidez el lenguaje "farmacéutico" y comprenden aspectos como la extractabilidad y la lixiviabilidad.
- Producción totalmente automatizada con manipulación robotizada para eliminar la contaminación
- Laboratorio analítico dedicado a la certificación de materiales
Sus instalaciones de Roma funcionan 24 horas al día, 7 días a la semana, con 16 máquinas de moldeo por inyección de precisión en salas blancas de clase 8. En 2025 ganaron un premio de sostenibilidad de la UE por reducir los residuos de producción en 78%, algo impresionante para un fabricante de productos médicos.
3. VitaMold (Florencia)
Cuando visité las instalaciones de VitaMold en Florencia el año pasado, quedé impresionado por la forma en que combinan la artesanía tradicional con la tecnología más avanzada.
Se han hecho un hueco en el sector de los componentes de equipos de diagnóstico, donde la precisión no es negociable.
Puntos fuertes:
- Desarrollo de polímeros reciclables de calidad médica (algo que parecía imposible hace unos años).
- Aditivos antimicrobianos patentados para equipos hospitalarios
- Herramientas de múltiples cavidades que, de algún modo, mantienen tolerancias muy ajustadas
Su colaboración con la Universidad de Florencia ha dado lugar a tres materiales patentados específicamente para aplicaciones médicas. No está nada mal.
4. PrecisionMed (Turín)
El nombre lo dice todo. Esta gente está obsesionada con la precisión.
Cuando un fabricante de dispositivos médicos necesita componentes con tolerancias de ±0,01 mm, PrecisionMed suele ser su primera llamada.
Por qué son conocidos:
- Componentes de micromoldeo de tan sólo 0,4 mm (¡en serio!)
- Texturizado de superficies a nivel microscópico para el control de fluidos
- Formulaciones de materiales compatibles con rayos X
Sus instalaciones de Turín parecen más un laboratorio que una fábrica, con técnicos de bata blanca que supervisan los procesos a través de microscopios. No es de extrañar que sean la referencia en componentes quirúrgicos mínimamente invasivos.
5. MedComponents (Bolonia)
Lo que hace diferente a MedComponents es su enfoque integral. Diseño, utillaje, moldeo y montaje, todo bajo un mismo techo.
Esta integración vertical les ha hecho especialmente valiosos para las nuevas empresas médicas que necesitan un socio que pueda hacerlo todo.
Su ventaja:
- Consultoría de diseño para la fabricación (DFM) que ahorra millones a los clientes
- Montaje integrado en sala blanca de dispositivos acabados
- Preparación acelerada de la documentación reglamentaria
En 2025, completaron la tercera ampliación de sus instalaciones, añadiendo capacidades de procesamiento de polímeros biodegradables. Su enfoque integral ha ayudado a lanzar con éxito más de 40 dispositivos médicos en los últimos cinco años.
6. SurgicalMold (Parma)
Si le han operado recientemente, es muy probable que SurgicalMold haya tenido algo que ver con el instrumental utilizado.
Dominan el arte de fabricar instrumentos quirúrgicos mediante moldeo por inyección avanzado, que a menudo sustituye a los componentes metálicos tradicionales.
Liderazgo en el sector:
- Trabajar directamente con los cirujanos para optimizar el diseño de los instrumentos
- Proceso de sobremoldeado patentado para superficies de agarre suave integradas
- Sistemas de fabricación "justo a tiempo" de kits de procedimientos específicos para hospitales
Sus instalaciones de Parma mantienen salas blancas de clase 7 con una automatización avanzada que permite una trazabilidad completa de cada componente, desde la materia prima hasta el producto acabado. Impresionante.
7. CardioPlast (Padua)
Como único moldeador italiano centrado exclusivamente en dispositivos cardiovasculares, CardioPlast ha desarrollado una experiencia sin parangón en aplicaciones que entran en contacto con la sangre.
Esta especialización les ha convertido en el socio preferido de fabricantes de válvulas cardíacas y empresas de dispositivos vasculares.
Capacidades especializadas:
- Procesos validados para polímeros compatibles con la sangre
- Técnicas de acabado de superficies ultrasuaves (críticas para el flujo sanguíneo)
- Protocolos de manipulación de material implantable
Su colaboración con el Centro de Investigación Médica de Padua ha dado lugar a varios diseños de componentes innovadores para válvulas cardíacas de nueva generación. Si va a entrar en el corazón o cerca de él, llame a esta gente.
8. OrthoMold (Nápoles)
OrthoMold se ha labrado un sólido nicho en el sector ortopédico, produciendo componentes para todo tipo de productos, desde dispositivos de fijación externa hasta instrumentos quirúrgicos.
Diferenciación del mercado:
- Polímeros vitrificados de alta resistencia para aplicaciones portantes
- Sistemas de codificación por colores para la identificación del instrumental quirúrgico
- Diseños ergonómicos optimizados para procedimientos ortopédicos
En 2025, introdujeron su tecnología patentada "OsteoFuse", que permite la unión directa entre componentes moldeados y herrajes ortopédicos metálicos. Esta innovación eliminó varios pasos de montaje para sus clientes.
9. DiagnosticMolding (Génova)
Fundada por antiguos científicos de laboratorio, DiagnosticMolding aporta una perspectiva única a los consumibles y equipos de diagnóstico.
Conocimientos técnicos:
- Moldeo de canales microfluídicos para aplicaciones lab-on-chip
- Polímeros de calidad óptica para lectores de diagnóstico
- Fabricación de componentes de kits de pruebas en grandes volúmenes y sin iluminación
Sus instalaciones de Génova producen más de 500 millones de componentes de diagnóstico al año, una cifra que se disparó durante las recientes crisis sanitarias. Cuando la velocidad y la escala son importantes en el diagnóstico, los fabricantes recurren a ellos.
10. MediForm (Milán)
Completa nuestra lista MediForm, una empresa familiar que pasó con éxito del moldeo industrial general a la especialización médica.
Estrategia de crecimiento:
- Adquisición estratégica de clientes del sector sanitario
- Fuerte inversión en ISO 13485 sistemas de calidad
- Desarrollo de conocimientos especializados en material médico
Aunque su especialización médica es más reciente que la de otros fabricantes de esta lista, su enfoque ágil y su compromiso con el servicio al cliente les han convertido rápidamente en una estrella emergente entre los moldeadores médicos italianos.
Moldeado Baiwe
Moldeado Baiwe comprende los requisitos exclusivos de la industria médica, incluido el estricto cumplimiento de la normativa y la necesidad de materiales de alto rendimiento. Nuestras capacidades de moldeo por inyección de última generación están diseñadas para producir piezas médicas que cumplan los más altos estándares de seguridad, calidad y funcionalidad.
- Certificaciones ISO: Contamos con la certificación ISO 13485:2016, que garantiza que nuestros procesos cumplen los estrictos requisitos de fabricación de dispositivos médicos.
- Salas blancas: Ofrecemos entornos de fabricación en sala blanca para la producción de componentes sensibles, manteniendo los más altos niveles de limpieza y minimizando los riesgos de contaminación.
- Experiencia en materiales: Trabajamos con una amplia gama de materiales de grado médico, incluidos plásticos biocompatibles, polímeros de grado médico y elastómeros termoplásticos (TPE), adaptados a sus necesidades específicas.
- Soluciones a medida: Tanto si necesita componentes sencillos como piezas complejas de varios materiales, nuestro equipo puede ofrecerle soluciones de moldeo personalizadas que satisfagan sus especificaciones exclusivas.
Cómo elegir el socio italiano adecuado para el moldeo de moldes médicos
Ahora que conoce a los jugadores, ¿cómo elige?
Según mi experiencia trabajando con empresas de productos sanitarios, estos son los factores que más importan:
- Experiencia normativa: Verifique la certificación ISO 13485 y la experiencia con las normativas pertinentes para sus mercados objetivo.
- Salas blancas: Adapte su clasificación de sala limpia (ISO 7, 8, etc.) a los requisitos de su producto.
- Conocimientos materiales: Asegúrese de que disponen de procesos validados para sus polímeros médicos específicos.
- Sistemas de calidad: Infórmese sobre sus protocolos de inspección y procesos de validación: aquí es donde no se pueden escatimar esfuerzos.
- Capacidades técnicas: ¿Tienen experiencia con sus retos específicos (micromoldeo, sobremoldeo, etc.)?
- Integración de la cadena de suministro: ¿Pueden abastecerse de materiales especializados y gestionar operaciones secundarias?
- Estilo de comunicación: Nunca subestimes la importancia de una comunicación clara y coherente, sobre todo en varios idiomas.
Consejo profesional: pida ejemplos concretos de proyectos similares al suyo. El mejor predictor del éxito futuro es el rendimiento pasado con retos comparables.
El futuro del moldeo por inyección para uso médico en Italia
De cara al futuro, veo varias tendencias que están reconfigurando esta industria:
Revolución sostenible
Incluso en la fabricación de productos médicos, la sostenibilidad se ha convertido en algo innegociable. Empresas como BioPharma Plastics y VitaMold son pioneras en polímeros médicos reciclables sin comprometer el rendimiento ni el cumplimiento normativo.
Integración de la fabricación digital
Industria 4.0 ya no es solo una palabra de moda. El entorno de producción totalmente digitalizado de PrecisionMed permite ahora a los clientes supervisar la producción en tiempo real y acceder a la documentación completa de los lotes al instante.
Impulso a la deslocalización
La pandemia alteró permanentemente la forma de pensar sobre las cadenas de suministro médico. Los fabricantes italianos son los grandes beneficiarios de que las empresas europeas de productos sanitarios acerquen la producción a su país.
Innovación de materiales
La integración de aditivos antimicrobianos, polímeros bioabsorbibles y compuestos de alto rendimiento está ampliando las posibilidades de los componentes médicos moldeados por inyección. Empresas como CardioPlast están validando estos materiales para aplicaciones clínicas.
Para terminar
Aquí la tiene: la guía definitiva de la 10 principales empresas de moldeo por inyección médica en Italia en 2025.
Lo que hace especiales a estas empresas no son sólo sus capacidades técnicas (aunque son impresionantes). Es la forma en que combinan la excelencia de la fabricación tradicional italiana con los conocimientos médicos específicos y la tecnología punta.
Tanto si está desarrollando dispositivos implantables, plataformas de diagnóstico o consumibles médicos de gran volumen, estos especialistas italianos ofrecen capacidades que rivalizan o superan las que se encuentran en cualquier lugar del mundo.
Para las empresas de dispositivos médicos que buscan sacar al mercado productos de última generación o reforzar su cadena de suministro con socios europeos de alta calidad, estas 10 principales empresas de moldeo por inyección médica de Italia ofrecen ventajas convincentes difíciles de igualar en otros lugares.
¿Has trabajado con alguna de estas empresas? Me encantaría conocer tu experiencia en los comentarios.
Y si está considerando la fabricación italiana para su próximo proyecto de dispositivos médicos, espero que esta guía de la 10 principales empresas de moldeo por inyección médica en Italia le ayuda a tomar la decisión correcta.