La rebaba es uno de los defectos más frustrantes del moldeo por inyección. Esta fina capa de plástico a lo largo de la línea de separación de las piezas moldeadas no solo tiene mal aspecto, sino que también puede dar lugar a costosos procesos posteriores.
¿Qué es lo que provoca el flash? Y lo que es más importante, ¿cómo se puede evitar que ocurra?
En esta completa guía de solución de problemas, como profesional fabricante de moldeo por inyección de plásticoEn este artículo, le explicaré las principales causas de las rebabas en el moldeo por inyección. También compartiré consejos prácticos para eliminar este defecto de su proceso de fabricación.
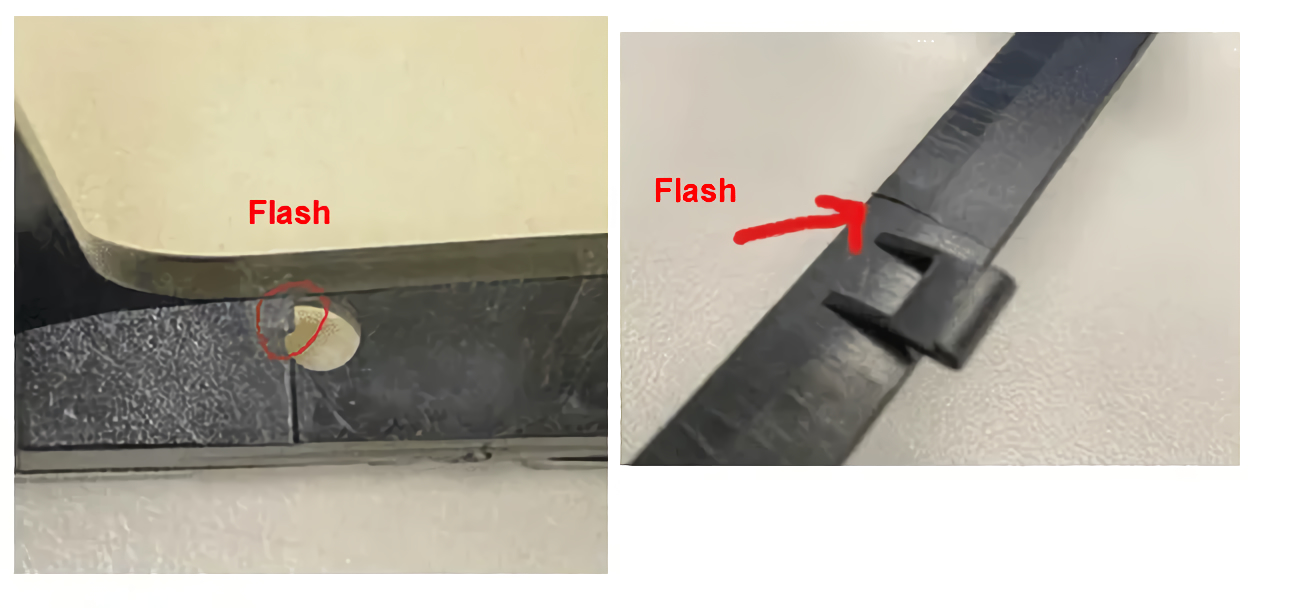
¿Qué es la rebaba en el moldeo por inyección?
Antes de entrar en las causas, asegurémonos de que estamos de acuerdo en lo que realmente es la rebaba del moldeo por inyección.
Se trata de una fina capa o "aleta" de plástico que se escapa de la cavidad del molde durante el proceso de moldeo por inyección. Parece una pequeña solapa o pestaña de exceso de plástico a lo largo de la línea de separación del componente moldeado.
A veces también se observan rebabas alrededor de los pasadores eyectores, las correderas o los orificios de ventilación. Pero, en términos generales, la línea de separación del molde es la zona en la que se producen con más frecuencia las rebabas.
El flash se produce cuando la presión durante las fases de inyección o envasado supera la capacidad del molde para permanecer completamente cerrado. Hablaremos más sobre estas causas específicas dentro de un momento.
Ahora que ya sabes qué aspecto tiene el flash, vamos a descubrir las causas profundas.
¿Qué causa las rebabas en el moldeo por inyección?
Existen varias causas potenciales de las rebabas en las piezas moldeadas por inyección:
- Desajustes en la línea de separación
- Ventilación inadecuada
- Baja presión de apriete
- Baja viscosidad del material
- Relleno irregular
- Sobreembalaje
A continuación, desglosaré cada una de estas causas comunes del parpadeo.
Desajustes en las líneas de separación
La línea de apertura es el punto en el que se unen y sellan las dos mitades de un molde de inyección. Los desajustes en la línea de partición se producen cuando hay huecos o aberturas en cualquier parte de esta superficie.
Durante la inyección, los destellos se forman cuando el plástico fundido escapa a través de estos pequeños huecos en las juntas de la línea de apertura.
¿Qué es lo que provoca los desajustes en las líneas de separación? He aquí algunas de las causas más comunes:
- Contaminación: El polvo, la suciedad, el aceite y los residuos pueden impedir un sellado correcto a lo largo de la línea de separación.
- Molde desgastado: Después de miles de ciclos, el desgaste puede distorsionar las mitades del molde y producir huecos.
- Geometrías de piezas complejas: Las formas intrincadas de las piezas ejercen una presión adicional que puede provocar aberturas sutiles.
Ventilación inadecuada
Los respiraderos permiten que el aire atrapado escape de la cavidad del molde durante la inyección. Sin una ventilación adecuada, la presión del aire dentro de la cavidad puede forzar el plástico fundido a través de cualquier pequeño hueco en las juntas.
Si sus moldes no tienen respiraderos colocados adecuadamente alrededor de la cavidad, es mucho más probable que se produzcan velos.
Baja presión de apriete
La presión de cierre se refiere a la fuerza aplicada para mantener el molde cerrado durante la inyección y el envasado. Si la presión de cierre no puede resistir la presión del material dentro de la cavidad, se formarán rebabas.
Esto suele ocurrir cuando la velocidad de inyección, la presión o la temperatura son demasiado altas en relación con la fuerza de sujeción disponible.
Baja viscosidad del material
La viscosidad se refiere al espesor y las características de fluidez del plástico fundido. Menor viscosidad los materiales fluyen más fácilmente a través de aberturas estrechas.
El calor excesivo de la boquilla/barril, el contenido de humedad o el lubricante pueden contribuir a reducir la viscosidad. Y cuando la viscosidad es demasiado baja, la inflamación es mucho más probable.
Relleno irregular
Si la cavidad del molde no se llena de manera uniforme, puede producirse una presión de empaquetado desequilibrada. Las guías de flujo ayudan a dirigir el frente de material, pero la colocación incorrecta de compuertas y canales también provoca un flujo desigual.
A medida que aumenta la presión dentro de la cavidad, se forman destellos al escapar el plástico por cualquier abertura disponible.
Sobreembalaje
Incluso con un llenado adecuado, pueden surgir problemas si se introduce demasiado material en el molde. Este sobrellenado localizado induce destellos a medida que el exceso de material encuentra vías de escape.
El diseño de la compuerta, la colocación del canal, la velocidad/presión de inyección y los tiempos de retención influyen en la uniformidad del envasado.
Cómo evitar las rebabas en el moldeo por inyección
Ahora que hemos tratado las causas principales, hablemos de prevención. He aquí seis consejos para evitar las rebabas en sus componentes moldeados por inyección:
1. Diseño adecuado del molde
La precisión de los componentes del molde y la calidad de los acabados superficiales contribuyen en gran medida a evitar las rebabas. Esto incluye una colocación adecuada de los orificios de ventilación, unos bordes con radios generosos y la eliminación de deslizamientos, tirones y cierres complejos innecesarios.
2. Mantenimiento riguroso de los moldes
Con el tiempo, la distorsión por desgaste puede dar lugar a sutiles aberturas para la formación de rebabas. Cumplir los programas de mantenimiento preventivo ayuda a conservar la geometría del molde. Esto incluye revisiones periódicas, pulidos, inspecciones y sustituciones cuando sea necesario.
3. Tonelaje de pinza adecuado
Determine el tonelaje necesario para mantener el molde sellado y evitar aberturas para la formación de rebabas. Un sobredimensionamiento de las prensas conduce a un desgaste más rápido, mientras que unas pinzas de tamaño insuficiente conducen directamente a la formación de rebabas.
4. Ajustes optimizados del proceso
Mantenerse dentro de las recomendaciones del proveedor de resina en cuanto a tasa de llenado, velocidad/presión de inyección y temperaturas del cilindro es un buen punto de partida. Pero un mayor ajuste le ayudará a tener en cuenta la dinámica específica de su molde y máquina.
5. Estabilidad dimensional
La elección de materiales con el nivel adecuado de estabilidad dimensional evita la contracción posterior a la inyección, que puede empeorar los defectos de rebabas existentes.
6. Tolerancia dimensional
Aunque pueda parecer insignificante, dejar un espacio un poco mayor en la línea de separación permite un mejor sellado contra posibles rebabas. Asegúrese de tener en cuenta estas bandas de tolerancia ampliadas en todo el montaje.
Elimine las rebabas y mejore el moldeo por inyección
Y ahí lo tiene: una guía completa sobre las causas, la prevención y las soluciones de los defectos de rebabas en el moldeo por inyección.
La ciencia de los materiales que hay detrás de este proceso es compleja. Pero recuerde que, en última instancia, el flash se reduce a que la presión dentro de la cavidad supera lo que el molde puede soportar.
Alinee el diseño de sus herramientas, las capacidades de la maquinaria, los ajustes del proceso y la selección de materiales para evitar estos desequilibrios de presión. Si lo hace, eliminará los planos y mejorará la calidad, los tiempos de ciclo y los costes.
Como siempre, espero que esta guía le proporcione los conocimientos prácticos necesarios para mejorar sus operaciones de fabricación. Si tiene alguna otra pregunta, hágamelo saber en los comentarios.