La excentricidad es un defecto estético común en el moldeo por inyección de plásticos en el que aparecen rayas plateadas o blancas en la superficie de una pieza. Para corregir este problema y mejorar el control de calidad, es fundamental identificar las causas de la holgura. Como profesional fabricante de moldeo por inyección de plásticoDespués de analizar miles de piezas moldeadas por inyección, he descubierto los principales culpables de los defectos de separación.
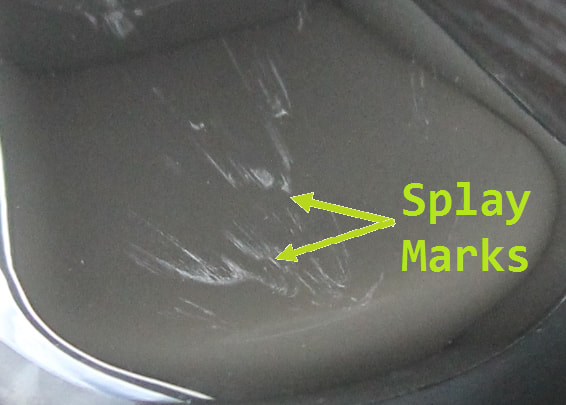
¿Cuál es la causa de la holgura en el moldeo por inyección de plásticos?
La holgura es un defecto estético común en el moldeo por inyección de plásticos, que se caracteriza por la aparición de estrías de color, a menudo plateadas, en la superficie de las piezas moldeadas. Las principales causas son la humedad, el cizallamiento, la degradación del plástico y el sobrecalentamiento.
Humedad
La humedad es, con diferencia, la causa más común de la deformación de las piezas de plástico moldeadas por inyección. ¿Cuáles son las causas de la holgura en el moldeo por inyección de plásticos? a menudo se debe a un secado incorrecto de la resina plástica.
Cuando la resina plástica absorbe humedad ambiental o agua, esa humedad se vaporiza en forma de vapor cuando los gránulos se calientan dentro del barril de inyección. A medida que el molde se llena, las burbujas de vapor migran a la superficie, provocando marcas de separación.
He visto que la holgura causada por la humedad cubre toda una pieza de forma aleatoria. Rara vez aparece en el mismo lugar exacto de una pieza a otra. Eso es un indicador clave de que la humedad es la culpable.
Las resinas higroscópicas, como el nailon y el policarbonato, absorben fácilmente la humedad y requieren un secado adecuado antes del moldeo. Pero incluso las resinas no higroscópicas pueden contribuir a la deformación si no se secan lo suficiente.
Siga las recomendaciones del proveedor del material en cuanto a temperatura y duración del secado. Considere la posibilidad de instalar un analizador de humedad para validar que los gránulos de plástico se mantienen por debajo de un contenido máximo de humedad durante el proceso de secado.
Cizalla
Aunque la humedad es la fuente más frecuente de desviación, las fuerzas de cizallamiento también pueden arrastrar burbujas y degradar el plástico, provocando desviaciones durante el llenado.
Hay dos formas principales en que el cizallamiento induce las estrías de separación:
Cizalla de tornillo
Si la velocidad del husillo, la contrapresión o la temperatura de la masa fundida son demasiado elevadas, puede producirse un exceso de cizallamiento de la masa fundida de plástico, con la consiguiente formación de gases y degradación. En ambos casos se crea una masa fundida espumosa que se desprende de la superficie de la pieza.
Disminuya las revoluciones del tornillo, reduzca la contrapresión y disminuya la temperatura de fusión para limitar el cizallamiento. Deje que los cambios surtan efecto durante 20 minutos antes de evaluar su impacto.
Cizalla de compuerta
Una compuerta de tamaño inadecuado para la geometría de la pieza también puede imponer un cizallamiento excesivo cuando el polímero entra en la cavidad del molde. El resultado pueden ser marcas de separación justo delante de la zona de la compuerta.
Examine cuidadosamente la ubicación de la separación con respecto a la puerta. Ajuste las dimensiones de la compuerta o añada compuertas adicionales para minimizar la exposición al cizallamiento. Disminuir la velocidad de llenado puede reducir aún más los efectos de cizallamiento de la compuerta.
Degradación del plástico
Aunque la humedad y el cizallamiento son las causas principales, el plástico degradado también puede desprender gases y provocar la separación.
Piense en la resina plástica como en un ovillo de hilo: polímeros de largas cadenas moleculares enredadas. El exceso de tiempo de permanencia en el barril, unido a unas temperaturas demasiado elevadas, corta y recorta lentamente esas cadenas moleculares mediante la degradación térmica. Las pequeñas moléculas gaseosas resultantes aparecen entonces en forma de briznas.
Supervise cuidadosamente factores como los puntos de ajuste del barril, el tiempo de residencia y la temperatura de fusión para evitar problemas de degradación. La adición de recuperación de retardo del tornillo puede ayudar a garantizar que el tornillo termine de mezclar justo antes de la inyección para minimizar la degradación del polímero.
Sobrecalentamiento
Por último, la deformación puede deberse simplemente al sobrecalentamiento durante el moldeo por inyección de plástico. Las temperaturas del barril que superan las recomendaciones producen una masa fundida caliente y llena de gas que se transfiere a patrones de deformación rayados.
El secado excesivo del plástico es un factor común y oculto. Si bien es cierto que la resina debe estar seca, el secado excesivo destruye literalmente la estructura molecular del plástico. polímeros. El control estricto del protocolo de secado y de las temperaturas de las barricas es fundamental.
Confirme qué causa la holgura en su moldeo por inyección
Aislar la humedad, el cizallamiento, la degradación y el sobrecalentamiento ayuda a reducir las causas de la holgura en el moldeo por inyección de plástico. Pero cada célula de trabajo de moldeo tiene matices que requieren conocimientos prácticos de moldeo a la antigua usanza.
Obtenga información detallada analizando factores como:
- Temperaturas reales del cilindro, la boquilla y el canal caliente del molde
- Tiempo de llenado, velocidad, presión
- Revoluciones del tornillo, contrapresión
- Puerta, dimensiones de la corredera
- Tiempo de secado, temperatura
- Contenido en humedad
Cómo eliminar la holgura en el moldeo por inyección
Ahora que ya sabe lo que hay detrás de esas molestas rayas plateadas, entremos en materia para eliminar realmente los defectos de separación de sus componentes moldeados por inyección.
Paso 1: Inspeccionar las piezas en busca de defectos
Como primer paso, compruebe cuidadosamente sus piezas moldeadas para patrones en los defectos de separación.
- Si las marcas se producen aleatoriamente por todas partes, la humedad es probablemente la culpable.
- Los defectos, principalmente en las puertas, apuntan a cizalla.
- Las marcas consistentes indican un a base de moho como la pérdida de lubricante de los taqués.
Por lo tanto, preste mucha atención a cómo y dónde se manifiesta exactamente el desgarro antes de lanzarse a solucionarlo. El patrón del defecto guiará las soluciones adecuadas.
Paso 2: Abordar las causas relacionadas con la humedad
Dado que la humedad es la causa más común de las holguras, vamos a seguir un proceso sistemático para atajarla:
A. Comprobar los materiales higroscópicos
Examine los tipos de material y las hojas de datos para ver si alguna resina es higroscópica, como el nailon o el PC. Incluso pequeñas cantidades de humedad en estos materiales pueden provocar una holgura importante.
B. Verificar la temperatura y el tiempo de secado
Compruebe la temperatura y la duración del secado con las recomendaciones del proveedor de la resina. Por ejemplo, los nylons necesitan 8 horas a 180°F. No haga suposiciones.
C. Inspeccionar las secadoras
Compruebe físicamente que los conductos de aire de impulsión están calientes y los de retorno calientes. Utilice sondas para confirmar que las temperaturas coinciden con los valores de consigna. Los secadores defectuosos son sinónimo de plástico húmedo.
D. Ajustar los rendimientos
Si se utilizan secadores de tamaño insuficiente, es posible que los materiales no pasen suficiente tiempo en su interior para secarse completamente. Aumente el tiempo de secado reduciendo el rendimiento.
E. Cargadores de drenaje
La humedad puede reabsorberse en el plástico enfriado en los cargadores. Escurra siempre las porciones iniciales antes de moldear de cualquier carga de secadora.
Siga esta metodología para descartar o abordar sistemáticamente las causas relacionadas con la humedad. Esto soluciona la mayoría de los problemas de holgura.
Paso 3: Hacer frente a la propagación del calor
Si la humedad no es definitivamente la culpable, el calor excesivo es el siguiente sospechoso probable. He aquí cómo resolver los defectos de separación térmica:
A. Comparar las temperaturas de fusión
Compruebe las temperaturas de fusión registradas con las directrices del proveedor del material. Si es demasiado alta, reduzca gradualmente la temperatura del barril y vuelva a probar las piezas.
B. Reducir las contrapresiones
Una contrapresión excesiva puede sobrecalentar y degradar las resinas. Disminuya gradualmente la contrapresión hasta eliminar la holgura.
C. Temperaturas más bajas en la zona de alimentación
Las zonas de alimentación más frías reducen el tiempo de permanencia de la resina en el barril caliente, minimizando la degradación por exposición prolongada al calor.
D. Retraso en la recuperación del tornillo
Si los tiempos de enfriamiento son largos, retrase la rotación del tornillo para terminar la recuperación justo antes de abrir el molde. Esto evita el sobrecalentamiento por residencia.
Abordar metódicamente los factores relacionados con el calor resolverá muchos de los problemas de holgura que aún persisten.
Paso 4: Abordar las causas relacionadas con el cizallamiento
Si el calentamiento y la humedad no son factores concluyentes, entonces es probable que el cizallamiento contribuya a los problemas de las rayas plateadas. Aquí tienes consejos para contrarrestar el cizallamiento:
A. Tornillo inferior RPM
Las altas velocidades del husillo generan un exceso de calor de cizallamiento que degrada el plástico. Disminuya gradualmente las RPM hasta que desaparezca la holgura.
B. Ensanchar las compuertas
Las compuertas subdimensionadas provocan el cizallamiento del material. Ensanche las compuertas o utilice compuertas de abanico para minimizar el calentamiento por cizallamiento.
C. Inyección lenta
La forma más rápida de resolver el cizallamiento de la compuerta es reducir la velocidad de inyección. Esto da a la resina más tiempo para fluir.
D. Eliminar obstrucciones
Compruebe las puntas de las boquillas y los canales de ventilación del molde en busca de residuos o rebabas que puedan interrumpir el flujo uniforme de la masa fundida.
Como último recurso, el tratamiento de las causas del cizallamiento debería abordar los defectos residuales de separación no resueltos por otras soluciones.
Paso 5: Abordar los factores de contaminación
Si la deformación persiste después de tratar el calor, la humedad y el cizallamiento, la contaminación puede ser la culpable. A continuación se explica cómo tratar el plástico y los moldes contaminados:
A. Eliminar el remolido
Si se utiliza plástico triturado o reciclado, purgue todo y exclúyalo para las pruebas. Los contaminantes de la resina reutilizada a menudo provocan holguras.
B. Aumentar la purga
Purgue ampliamente con compuestos especiales para limpiar completamente el tornillo, el cañón, la boquilla y los canales calientes de residuos o aceites, ceras y contaminantes acumulados.
C. Moldes limpios
Desmonte los moldes y limpie meticulosamente con disolventes adecuados los lubricantes, antioxidantes u otras materias extrañas acumuladas en las superficies de las cavidades.
El tratamiento exhaustivo de la contaminación no dejará piedra sin remover en su lucha contra los enemigos de la hojarasca.
Lo esencial
Como se suele decir, "el diablo está en los detalles" en el moldeo por inyección. El examen meticuloso de los datos del proceso y de las piezas permite obtener información valiosísima para corregir defectos como la holgura.
La causa de la separación se debe probablemente a la absorción de humedad o al exceso de fuerzas de cizallamiento que degradan la masa fundida. Pero una configuración incorrecta en cualquier punto del proceso puede provocar marcas de separación irregulares. Trabaje metódicamente en los posibles problemas hasta que aísle la causa raíz y la resuelva como corresponda.