Las líneas de soldadura son uno de los defectos más comunes en las piezas de plástico moldeadas por inyección. Cuando dos frentes de flujo del plástico fundido convergen en el molde, es posible que no se fusionen completamente. El resultado es una línea visible en la pieza llamada línea de soldadura, que indica un punto débil. Como profesional moldeo por inyección de plástico fabricante, compartiré 4 causas fundamentales de los defectos en la línea de soldadura y algunas soluciones para prevenirlos.
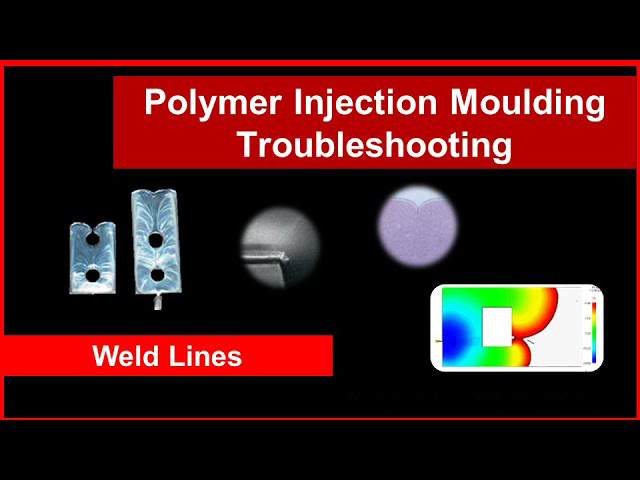
Por qué son importantes las líneas de soldadura en las piezas moldeadas por inyección
A primera vista, líneas de soldadura pueden parecer una cuestión puramente estética. Pero, en realidad, afectan negativamente a la resistencia y durabilidad de los componentes moldeados por inyección.
Por ejemplo, las piezas de plástico con defectos en las líneas de soldadura son más propensas a agrietarse o romperse en esos puntos cuando se someten a tensión. Esta fragilidad plantea problemas de seguridad en productos como piezas de automoción o dispositivos médicos.
Además, las líneas de soldadura distorsionan el aspecto estético de los artículos en los que el acabado superficial es importante. Así, pueden reducir el atractivo comercial de bienes de consumo como cajas de aparatos electrónicos o bloques de construcción de juguete.
Es evidente que las líneas de soldadura presentan consecuencias funcionales y económicas que los fabricantes no pueden ignorar. Examinemos qué las causa durante el proceso de moldeo por inyección.
¿Qué causa las líneas de soldadura en el moldeo por inyección? 4 causas principales
Durante la ejecución de las tiradas de moldeo por inyección, los frentes de flujo de plástico pueden separarse y volver a unirse en varias situaciones:
1. Obstáculos en la cavidad del molde
Los orificios, bordes, insertos y otras obstrucciones en el utillaje del molde desvían temporalmente el flujo de plástico fundido en dos o más trayectorias. Cuando los flujos vuelven a unirse a lo largo de la parte posterior del obstáculo, una temperatura o presión inadecuadas impiden que se mezclen de nuevo en una masa fundida homogénea.
Los pasadores de núcleo utilizados para crear aberturas internas como orificios o roscas son causas comunes de líneas de soldadura. Otro ejemplo son las levas y correderas de acción lateral que se retraen durante la inyección y luego se extienden dentro de la cavidad del molde antes de la solidificación.
2. Moldes multicavidad
Los moldes que contienen dos o más cavidades separadas con puntos de entrada específicos dividen intrínsecamente la presión de inyección. Este flujo dividido converge en algún punto del sistema de canalización en su camino hacia las cavidades. El punto de convergencia tiende a producir líneas de soldadura recurrentes de pieza a pieza.
Aunque minimizar las compuertas puede ayudar, la mayoría de los moldes multicavidad mostrarán líneas de soldadura en algún grado. Los fabricantes de moldes inteligentes intentarán localizarlas en zonas sutiles y no críticas durante el diseño.
3. Paredes desiguales
Cuando las piezas de plástico incorporan secciones de paredes gruesas y finas, los frentes de fusión que fluyen a través de estas zonas se solidifican a velocidades diferentes. El flujo de pared gruesa, más lento, y el de pared fina, más rápido, acaban confluyendo aguas abajo, con el riesgo de no unificarse correctamente.
Las transiciones bruscas en el espesor de pared actúan como obstrucciones del flujo, bifurcando la corriente de fusión hasta que se vuelve a conectar por la parte trasera. La reducción gradual de los cambios de espesor permite una convergencia más uniforme del flujo con un menor riesgo de líneas de soldadura.
4. Ventilación inadecuada
Los gases atrapados suponen otro obstáculo para conciliar dos frentes de flujo de masa fundida en la cavidad del molde. Sin una ventilación adecuada, las bolsas de aire se comprimen entre los flujos convergentes en lugar de escapar del utillaje del molde.
Esto provoca un punto caliente localizado debido a la rápida compactación del gas. En casos extremos, el pico de temperatura degrada el plástico polímerodejando una marca de quemadura negra o marrón. Los casos más benignos, con un ligero atrapamiento de aire, interrumpen la fusión adecuada entre las capas de flujo, lo que da lugar a un defecto de soldadura muy fino.
Cómo evitar las líneas de soldadura en el moldeo por inyección
Lo ideal sería que las piezas se diseñaran para evitar por completo las obstrucciones y perturbaciones del flujo. Pero en la mayoría de los artículos comerciales, algunas irregularidades son inevitables.
Afortunadamente, los ajustes en el utillaje del molde y la optimización de los parámetros de procesamiento pueden minimizar la aparición de líneas de soldadura:
- Aumente la velocidad de llenado de la inyección para conseguir frentes de fusión más calientes y una soldadura más fluida.
- Aumentar la presión de inyección para mejorar la mezcla de flujo turbulento de los frentes convergentes.
- Aumentar la temperatura del barril para reducir la viscosidad y mejorar la capacidad de fusión.
- Reubicar las posiciones de las compuertas para cambiar las zonas con defectos de soldadura en las piezas.
- Añada rejillas de ventilación, aumente los espacios libres y mejore las vías de evacuación del aire en las zonas con problemas de moho.
- Utilizar sistemas de canal caliente para mantener temperaturas de fusión más altas durante todo el llenado de la cavidad.
- Normalizar las variaciones de stock de pared entre secciones gruesas y finas.
- Reduzca gradualmente la presión de inyección máxima con un ajuste de transferencia de velocidad/presión.
- Aumentar la temperatura del molde para ralentizar el enfriamiento y prolongar el tiempo de fusión del flujo.
Aunque pueden persistir pequeñas líneas de soldadura en algunos componentes moldeados por inyección después de aplicar estas correcciones, el objetivo es controlar su tamaño y ubicación. De este modo se evitan debilidades o defectos visuales importantes.
La inspección minuciosa de las muestras de preproducción proporciona información valiosa para perfeccionar los ajustes óptimos del proceso y el control del suministro de material. Este ajuste reduce la prevalencia de la línea de soldadura antes de las series de producción formales.
Conclusión
En resumen, las líneas de soldadura aparecen siempre que dos frentes de flujo no consiguen recombinarse durante el llenado de la cavidad en el moldeo por inyección. Las causas comunes incluyen obstrucciones del molde, compuertas multipunto, paredes desiguales y ventilación deficiente.
Mientras que los pequeños defectos de soldadura sólo estropean la estética, los más importantes comprometen la resistencia y el funcionamiento de la pieza en esos puntos. Los moldes cuidadosamente diseñados y los refinados parámetros de procesamiento minimizan las problemáticas separaciones de flujo. Así se obtienen componentes de plástico más uniformes y sin defectos.
¿Qué cree que causa más problemas en la línea de soldadura en sus aplicaciones de moldeo por inyección? ¿Son más preocupantes los defectos visuales o los impactos funcionales? Comparta sus experiencias y opiniones a continuación.