¿Qué es la temperatura de fusión en el moldeo por inyección? Como uno de los parámetros más críticos del proceso, conseguir la temperatura de fusión correcta es clave para producir piezas de plástico de calidad de forma eficiente. En esta completa guía, como profesional fabricante de moldeo por inyección de plástico...te explicaré todo lo que necesitas saber sobre la temperatura de fusión, incluyendo..:
- ¿Qué es la temperatura de fusión?
- Por qué es importante controlar la temperatura de fusión
- Cómo influye la temperatura de fusión en las propiedades de las piezas
- Buenas prácticas para fijar y medir la temperatura de fusión
- Relación entre las temperaturas de la masa fundida y del molde
Al final, usted tendrá una sólida comprensión de este concepto fundamental para que pueda controlar mejor sus procesos de moldeo por inyección. ¡Empecemos!
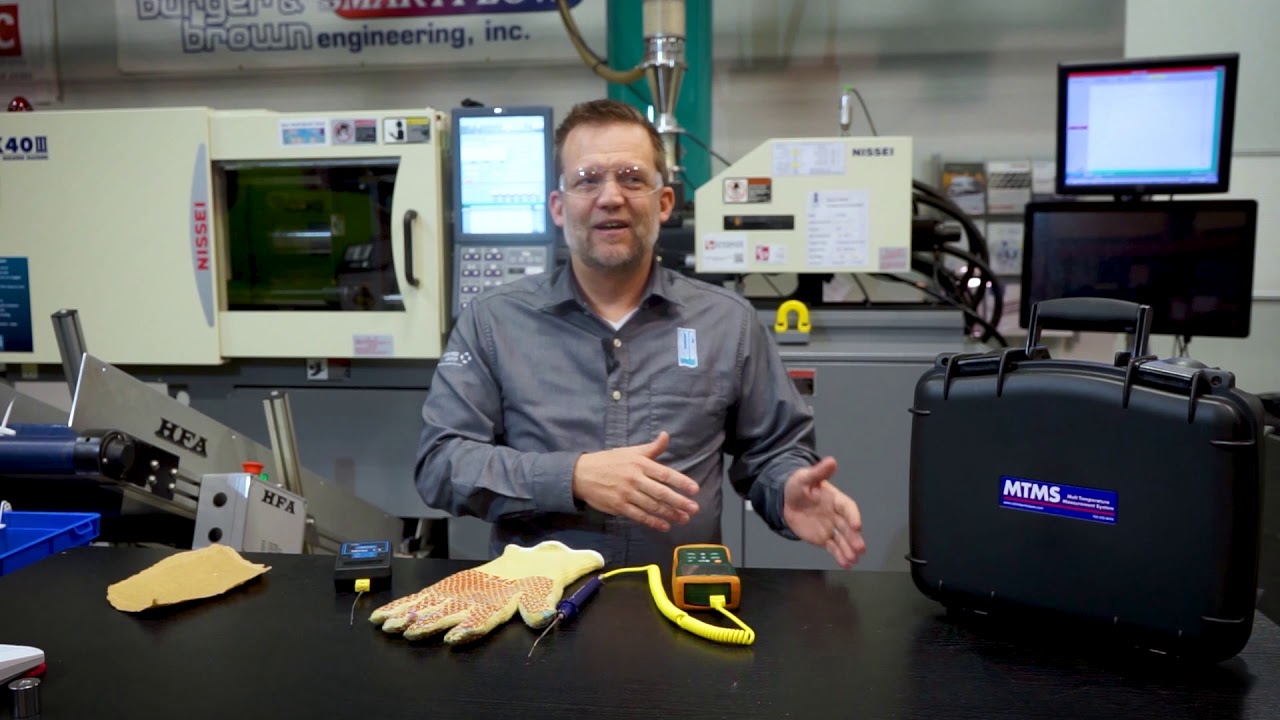
¿Qué es la temperatura de fusión en el moldeo por inyección?
La temperatura de fusión se refiere a la temperatura real del plástico fundido cuando sale de la boquilla de la máquina de moldeo por inyección y entra en el molde. Esta temperatura puede diferir sustancialmente de las temperaturas fijadas en el barril debido al calentamiento por cizallamiento y otros factores.
Acertar con la temperatura de fusión es crucial porque influye en la viscosidad del plástico, en la facilidad con que fluye en el molde y en las propiedades de la pieza acabada. Por ejemplo, una temperatura de fusión demasiado alta puede degradar el polímero, mientras que una demasiado baja puede impedir el flujo y provocar disparos cortos.
En general, las resinas amorfas como el ABS y el PC requieren temperaturas de fusión más altas, mientras que las resinas semicristalinas como el PP y el HDPE fluyen mejor a temperaturas más bajas. Pero la temperatura de fusión óptima depende del grado específico que se utilice.
¿Por qué es tan importante controlar la temperatura de fusión?
La temperatura de fusión influye en varios objetivos críticos del moldeo:
Calidad parcial: Una temperatura de fusión fuera de especificación puede alterar la viscosidad y el peso molecular de la resina, provocando defectos, inestabilidad dimensional, variaciones en las propiedades y otros problemas de calidad.
Eficiencia: Una temperatura de fusión incorrecta alarga la duración de los ciclos y reduce el rendimiento. También puede degradar las propiedades del material con el tiempo.
Coherencia: Las fluctuaciones de la temperatura de fusión, aunque sean pequeñas, pueden introducir variaciones inaceptables entre lotes.
Está claro que es imprescindible controlar la temperatura de fusión para producir piezas de calidad, maximizar la productividad y garantizar la estabilidad del proceso.
¿Cómo afecta la temperatura de fusión a las propiedades de las piezas?
Al influir en la viscosidad de la resina y otras características, los ajustes de la temperatura de fusión permiten a los procesadores controlar en cierta medida las propiedades de las piezas acabadas.
Fuerza y resistencia al impacto: Las temperaturas de fusión más bajas suelen producir una mayor fuerza y resistencia al impacto. La resina más fría retiene más peso molecular durante el proceso de moldeo.
Encogimiento: Una temperatura de fusión demasiado alta hace que el plástico se expanda más en el molde, aumentando la contracción. Las temperaturas de fusión ligeramente más bajas contrarrestan este efecto.
Duración del ciclo: Una viscosidad reducida a temperaturas de fusión más elevadas puede reducir los ciclos de moldeo, pero normalmente a expensas de las propiedades. Hay que encontrar un equilibrio.
Viscosidad: Cuanto más caliente esté la masa fundida, menor será su viscosidad. Pero si la viscosidad disminuye demasiado, se corre el riesgo de que el frente de flujo se vuelva inestable.
Mediante ajustes acertados de la temperatura de fusión, los fabricantes pueden adaptar la resistencia, la contracción, los tiempos de ciclo y otros atributos de las piezas para satisfacer los requisitos de la aplicación.
Buenas prácticas para ajustar y medir la temperatura de fusión
Aunque cada resina tiene unos intervalos de temperatura de fusión recomendados, hay que probar, ajustar y vigilar constantemente para encontrar el ajuste óptimo. He aquí algunos consejos:
Empieza por abajo: Comience con la temperatura de fusión más baja posible para el tipo de material. Así se minimiza la degradación térmica mientras se ajustan otros parámetros. Una vez que el proceso se estabilice, aumente lentamente la temperatura de fusión si es necesario para reducir la viscosidad o los ciclos.
Utilizar equipos actualizados: Controladores de temperatura de fusión con termopar o sensores RTD integrados en la boquilla para una medición continua eliminan las conjeturas y aceleran la optimización.
Mida sistemáticamente: Utilice el mismo procedimiento (por ejemplo, purgar en un recipiente aislado) cada vez que compruebe la temperatura de fusión para garantizar la coherencia. Los sistemas de medición en línea automatizados proporcionan los mejores datos.
Lleva un registro: Registre todos los parámetros del proceso junto con la temperatura de fusión para poder analizar con precisión las tendencias a lo largo del tiempo. Cualquier cambio debe tener una razón cuantitativa y trazable.
La supervisión y el control de la temperatura de fusión requieren esfuerzo, pero reportan beneficios en términos de calidad, eficacia y estabilidad. Seguir procedimientos estructurados y aprovechar la tecnología inteligente facilita las cosas y genera valiosos datos del proceso.
¿Cuál es la relación entre las temperaturas de fusión y de moldeo?
Las temperaturas de la masa fundida y del molde son intrínsecamente interdependientes, aunque se fijen de forma independiente.
Las principales conexiones entre estos dos parámetros cruciales del moldeo por inyección incluyen:
Calentamiento por cizallamiento: El calor de fricción generado por el flujo de la masa fundida a través del bebedero y los canales aumenta la temperatura de la superficie del molde. Los ciclos más rápidos agravan este efecto.
Eficiencia de refrigeración: La rapidez con la que la masa fundida se enfría en el molde depende en parte del gradiente térmico entre el plástico y la superficie del molde. Los deltas grandes favorecen el enfriamiento.
Cojín: Una ligera variación entre la temperatura de la masa fundida más caliente y la del molde más frío proporciona un amortiguador útil que evita caídas por debajo de la viscosidad mínima del material o que se congele antes de que se llene la cavidad.
Optimización de la propiedad: Como ocurre con la mayoría de las variables de procesamiento, la combinación ideal de temperaturas de fusión y moldeo maximiza la calidad y la eficacia. Es necesario probar y equivocarse para encontrar el "punto óptimo" de cada material.
Por tanto, aunque las temperaturas de fusión y del molde puedan parecer distintas, es importante considerar ambas de forma holística. La energía total es más importante que cualquiera de ellas por separado. El software de modelado puede proporcionar una orientación útil para optimizar este equilibrio.