El moldeo por inyección es uno de los procesos de fabricación más populares para piezas de plástico, desde pequeños Legos hasta parachoques de coches y componentes del salpicadero. Pero a pesar de lo común que es esta tecnología, mucha gente no entiende qué ocurre después de inyectar plástico fundido en un molde.
Uno de los comportamientos inherentes al plástico es que se contrae considerablemente al enfriarse. Esta contracción no es sólo un cambio en las dimensiones, sino que también puede causar tensiones internas que conducen a alabeo, una distorsión de la geometría o las dimensiones de una pieza.
Gestionar y reducir la contracción es un aspecto esencial del diseño y la fabricación de piezas de plástico complejas que mantienen tolerancias estrictas a lo largo de la vida útil de un producto. En esta guía, como profesional fabricante de moldeo por inyección de plásticoEn este artículo, explicaré las causas de la contracción en el moldeo por inyección, cómo puede predecirse y controlarse, y las estrategias para reducir los defectos en las piezas.
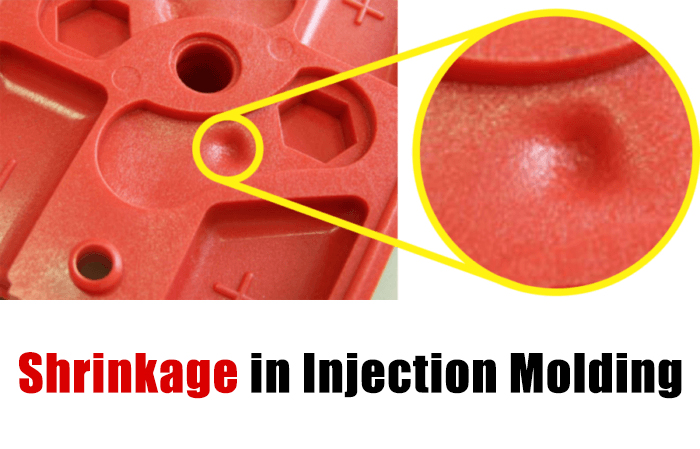
¿Qué es la contracción en el moldeo por inyección?
El encogimiento se refiere a la contracción de un componente de plástico moldeado a medida que se enfría después de la inyección en una máquina de moldeo por inyección. Por lo general, los polímeros plásticos se contraen entre 2-4%, aunque puede oscilar entre 0,5% y 10% en función del plástico, los aditivos de refuerzo, como las fibras de vidrio, y detalles como el grosor de las paredes. Es imposible eliminar por completo la contracción, por lo que debe tenerse en cuenta durante el diseño de las piezas de plástico.
En los casos más extremos, la contracción desigual llamada alabeo puede deformar las piezas hasta el punto de que no encajen dentro de las tolerancias especificadas. Pero el alabeo puede aparecer de forma muy sutil, como ligeras curvaturas o torsiones invisibles para el ojo humano, por lo que es fundamental gestionar la contracción mediante el diseño y las opciones de procesamiento.
La dinámica de la contracción y su impacto dependen de una combinación de:
- Composición del polímero: Cómo reaccionan las moléculas a los cambios de temperatura y presión, lo que influye en las tendencias de contracción direccional. Polímeros amorfos como ABS tienen comportamientos más uniformes, mientras que los plásticos semicristalinos como el PE y el PP tienen comportamientos anisótropos.
- Temperaturas de fusión: Las temperaturas de fusión más altas generalmente aumentan la contracción debido a la expansión de las cadenas de polímero.
- Temperaturas del moho: Un enfriamiento más rápido aumenta las tensiones internas. Los moldes más calientes permiten una mayor relajación de las moléculas antes de congelarse.
- Distribución del peso molecular: Los polímeros de mayor peso tienden a encogerse más.
- Presencia de rellenos/refuerzos: Las fibras restringen la contracción a lo largo de su orientación. Los rellenos minerales reducen la contracción general.
- Factores geométricos: Como el grosor de las paredes, las nervaduras, etc. Las zonas más gruesas se contraen más que las más finas, lo que puede provocar distorsiones.
¿Por qué se encoge el plástico?
Para entender lo que provoca la contracción, es importante observar primero lo que les ocurre a los polímeros a nivel molecular cuando pasan por el proceso de moldeo por inyección.
Comportamiento molecular de los plásticos
Los plásticos contienen largas cadenas moleculares de unidades repetidas unidas entre sí, conocidas como polímeros. El comportamiento de estas cadenas -el orden con el que se agrupan- determina si un material es amorfo o semicristalino.
Polímeros amorfos tienen una estructura enrollada aleatoriamente sin ninguna organización repetitiva entre las cadenas. Cuando se calientan, los polímeros amorfos forman un líquido que fluye libremente a medida que las moléculas se separan. El enfriamiento permite que las cadenas enredadas se acerquen, se encojan y se solidifiquen en su lugar, pero nunca se organizan en estructuras ordenadas.
Plásticos amorfos comunes:
- Acrilonitrilo butadieno estireno (ABS)
- Policarbonato (PC)
- Poliestireno (PS)
Plásticos semicristalinos contienen zonas en las que las cadenas moleculares se empaquetan formando regiones cristalinas ordenadas, mientras que otras zonas permanecen amorfas.
Cuando se calientan, las zonas cristalinas se funden en las regiones amorfas, pero las moléculas siguen apuntando mayoritariamente en las mismas direcciones. Al enfriarse, las estructuras cristalinas ordenadas se reforman y las moléculas ocupan un volumen menor, de ahí la contracción.
Plásticos semicristalinos comunes:
- Polietileno (PE)
- Polipropileno (PP)
- Nylon (PA)
El alto grado de alineación molecular de los materiales semicristalinos provoca una contracción perpendicular al flujo, mientras que los polímeros amorfos se contraen a lo largo de las direcciones de flujo.
Cómo el proceso de moldeo provoca el encogimiento
Volviendo al moldeo por inyección, ¿cómo influyen las condiciones de la máquina y el molde en la contracción?
Cuando el plástico entra en un barril calentado, las fuerzas de cizallamiento rompen las regiones cristalinas, mientras que el calentamiento permite que las cadenas moleculares se extiendan aumentando el volumen libre.
A continuación, el polímero fundido se introduce a alta presión y velocidad en una cavidad de molde relativamente más fría que restringe el movimiento perpendicular a la dirección del flujo. Las moléculas se alinean a lo largo de la dirección del flujo como espaguetis a través de una boquilla.
En los plásticos semicristalinos, a medida que desciende la temperatura comienzan a formarse de nuevo estructuras ordenadas. Las moléculas que se realinean tienen menos volumen libre, por lo que tiran con más fuerza, contrayendo el plástico.
Además, se desarrollan tensiones residuales entre el núcleo más caliente y las regiones superficiales más frías restringidas por las paredes rígidas del molde. Las piezas tratarán de aliviar estas tensiones a medida que continúan enfriándose una vez expulsadas del molde, lo que puede provocar alabeos.
¿Dónde se produce el encogimiento?
La mayor parte de la contracción se produce durante el enfriamiento dentro del molde, aunque puede producirse una cantidad menor después de la expulsión, cuando la temperatura se estabiliza por completo.
La contracción posterior al moldeo depende de varios factores:
- Condiciones de procesamiento como velocidad de inyección, presión y temperatura
- La rapidez con la que las capas superficiales se solidifican restringiendo el movimiento molecular
- Nivel de tensiones residuales
Por ejemplo, con plásticos amorfos como el PC y el ABS se produce una mayor contracción fuera del molde, ya que las secciones interiores permanecen fundidas durante más tiempo, lo que permite la relajación de las cadenas poliméricas. O las piezas muy finas se solidifican más rápido y generan menos tensiones internas.
Predicción y medición de los índices de contracción
Cada material plástico se encogerá de forma diferente en distintas condiciones. Por tanto, el primer paso para entender cómo puede deformarse una pieza es determinar con precisión los índices de contracción.
La contracción se mide como un cambio porcentual entre las dimensiones de la pieza moldeada por inyección en comparación con el molde de acero para herramientas: Contracción (%) = (Dimensión del molde - Dimensión de la pieza) / Dimensión del molde x 100
La mayoría de los fabricantes de resinas plásticas facilitan los datos de contracción en las fichas técnicas de los materiales, aunque lo ideal es realizar pruebas con los parámetros exactos de producción. Los valores típicos de contracción oscilan entre:
- Polímeros amorfos: 0.3-0.7%
- Plásticos semicristalinos: Alrededor de 2%
Tenga en cuenta que los detalles del procesado influyen en la contracción de un plástico determinado. Los cambios en la velocidad de inyección, la temperatura y la presión, entre otros, pueden influir en el índice de contracción.
Cómo predice el software de simulación los índices de contracción
Un software de simulación especializado puede modelar el proceso de moldeo por inyección para un diseño de pieza de plástico específico con el fin de predecir comportamientos como la contracción. Funcionan imitando digitalmente factores como:
- Propiedades reológicas del plástico
- Rendimiento de la máquina de moldeo
- Temperaturas, velocidades, presiones
- Geometría de la pieza
Como resultado, los ingenieros pueden visualizar las tendencias de contracción y los riesgos de alabeo de su diseño. Esto permite realizar ajustes antes de comprometerse con costosas herramientas de moldeo.
La simulación también ayuda a determinar el mejor compromiso entre las propiedades necesarias para la funcionalidad y los defectos de distorsión por contracción. Los cambios pueden implicar la modificación de la geometría, la ubicación de las puertas o incluso operaciones secundarias.
Cómo controlar la contracción del moldeo por inyección
Eliminar por completo la contracción es casi imposible con los plásticos. Sin embargo, mediante un diseño intencionado y decisiones de proceso, puede minimizarse lo suficiente como para fabricar piezas funcionales y de dimensiones robustas.
Estrategias para reducir la contracción del plástico
He aquí algunas estrategias de buenas prácticas utilizadas para reducir los defectos de contracción:
1. Conseguir el equilibrio adecuado entre llenado, envasado y refrigeración
Llenado demasiado rápido - Favorece la alineación de las moléculas con riesgo de contracción anisotrópica.
Embalaje inadecuado - Las secciones internas de la pieza se colapsan de forma impredecible una vez expulsada.
Enfriar demasiado rápido - Provoca una contracción variable en las zonas gruesas y finas, lo que provoca alabeos.
2. Aumento de la temperatura del molde
Permite la relajación de las cadenas poliméricas antes de la solidificación completa, reduciendo las tensiones internas. Lo ideal suele ser 30-50 °C por debajo de la temperatura de fusión.
3. Utilización de sistemas de canal caliente
Los canales calientes mantienen los bebederos y los canales fundidos, eliminando los desechos fríos y reduciendo los requisitos de longitud de flujo, lo que permite optimizar las secciones de las piezas.
4. Adición de fibras de vidrio
Alrededor de 30% de corte por peso las fibras dificultan la contracción proporcionando refuerzo. Aunque reduce la resistencia al impacto.
5. Incluir una ventilación adecuada del molde
La ventilación evita que el aire quede atrapado en la cavidad durante el llenado, lo que favorece un empaquetado completo para una retracción uniforme.
6. Utilización del moldeo por inyección asistida por gas
Se inyecta gas comprimido en la cavidad empujando el material contra las paredes, lo que mejora la reproducción y la precisión dimensional. La presión impulsa la contracción en pequeños canales huecos previstos.
7. Sobreembalaje de zonas de alta retracción
Normalmente, las zonas en dirección contraria al flujo sufren una mayor contracción a medida que las moléculas se relajan. Esto puede compensarse con un empaquetamiento intencionadamente mayor.
Reglas de diseño para minimizar la contracción irregular
Unas geometrías de pieza adecuadas contribuyen enormemente a la estabilidad, ya que el plástico se contrae al enfriarse. Algunas pautas de diseño que ayudan a reducir la contracción desigual son:
- Ajustar el grosor total de la pared lo más fino posible para obtener una resistencia adecuada. Las zonas gruesas sufren mayor contracción que las finas.
- Restringe la variación del grosor de las paredes en las piezas individuales manteniendo las secciones uniformes. Los cambios bruscos provocan una contracción preferente que distorsiona las zonas más delgadas.
- Incluyendo ángulos de tiro adecuados en paredes verticales que permiten una contracción uniforme al expulsar evitando que se pegue.
- Posicionamiento de las líneas de soldadura y fusión lejos de las zonas de alta apariencia o tolerancia. Estas zonas son intrínsecamente propensas a la contracción incoherente.
- Utilizar nervaduras o estructuras de soporte con detalles de perfil delgado sólo donde sea necesario gestiona el volumen. Los nervios ayudan a limitar las contracciones diferenciales en muros más grandes, pero añaden masa adicional si no es necesario.