So you’re getting into vacuum forming and wondering what plastic can be used for vacuum forming?
Este es el trato:
Not all plastics are created equal when it comes to vacuum forming. Some work like a dream. Others? Total nightmare.
I’ve spent countless hours testing different materials (and ruining quite a few in the process). And in this guide, as a professional fabricante de conformado al vacío de plásticos, I’m going to share everything I’ve learned about choosing the right plastic for your vacuum forming projects.
Vamos a sumergirnos.
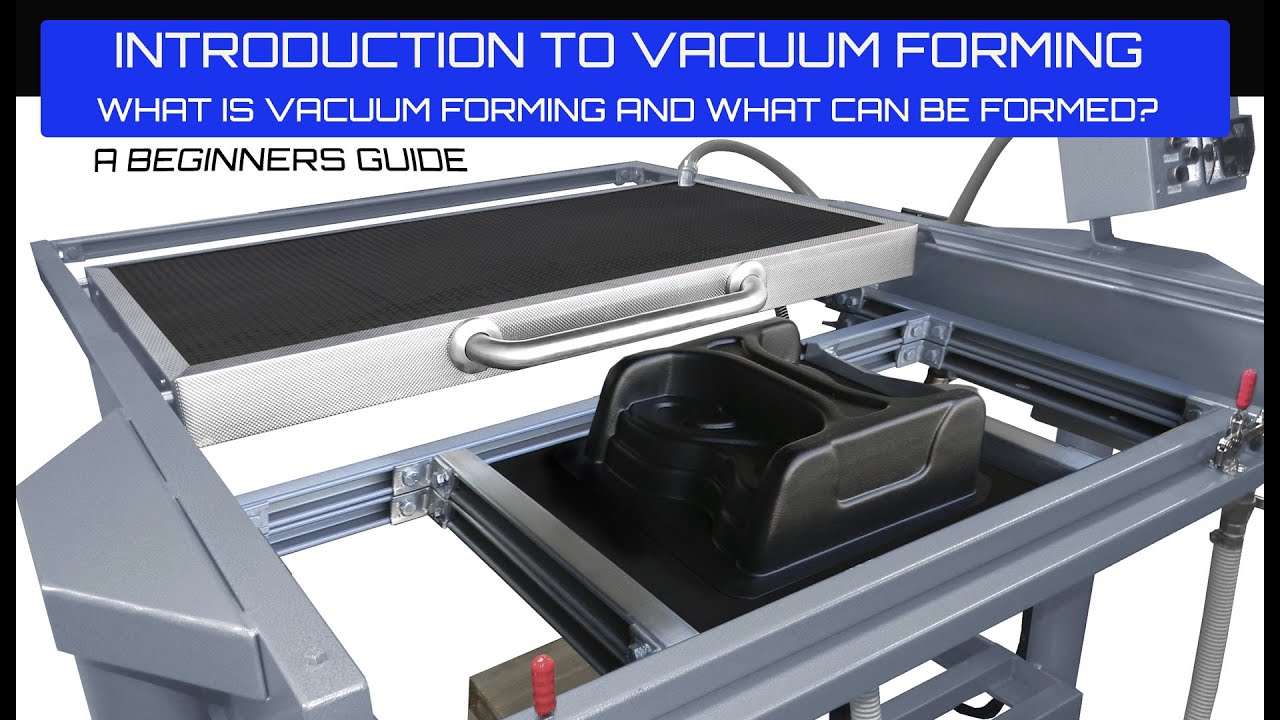
Why Plastic Selection Matters for Vacuum Forming
Before we get into the specific plastics, let’s talk about why this stuff matters.
Esto es lo que pasa:
Choose the wrong plastic and you’ll end up with:
- Warped parts that look like they melted in the sun
- Weak products that crack under pressure
- Wasted material (and money)
- Hours of frustration
But pick the RIGHT plastic?
You’ll get professional-looking parts that are strong, durable, and exactly what you need.
The key is understanding what makes a plastic suitable for vacuum forming in the first place.
What Makes a Plastic Good for Vacuum Forming?
Not every plastic plays nice with vacuum forming.
In fact, only thermoplastics work for this process.
¿Por qué?
Because thermoplastics have a superpower: they soften when heated and harden when cooled. And they can do this over and over again without breaking down.
But that’s just the beginning.
The BEST vacuum forming plastics also have:
Low forming temperatures: Nobody wants to wait forever for their plastic to heat up. Plus, lower temps mean less energy cost.
Good flow characteristics: The plastic needs to stretch and conform to your mold without tearing.
Minimal shrinkage: You want your final part to match your mold, not be 10% smaller.
High impact strength: Because who wants parts that shatter at the slightest bump?
Consistent thickness: Uneven material = uneven results.
Now let’s get into the specific plastics that check these boxes.
The Top 7 Plastics for Vacuum Forming
1. High Impact Polystyrene (HIPS)
HIPS is the workhorse of vacuum forming.
¿Por qué?
It’s cheap, easy to work with, and gives consistent results. Perfect for beginners and pros alike.
Forming temperature: 140-180°C (284-356°F)
Best for:
- Packaging trays
- Display stands
- Prototipos
- Señales
- Disposable products
Pro tip: HIPS comes in tons of colors and textures. I’ve even seen flocked versions that feel like velvet.
The downside? It’s not great for outdoor use. UV light makes it brittle over time.
2. ABS (Acrylonitrile Butadiene Styrene)
Think of ABS as HIPS’s tougher older brother.
This stuff is STRONG. We’re talking automotive-parts strong.
Forming temperature: 150-190°C (302-374°F)
Best for:
- Piezas de automóviles
- Electronic housings
- Luggage
- Equipo de protección
- Heavy-duty enclosures
ABS costs more than HIPS, but you get what you pay for. It’s incredibly durable and handles chemicals like a champ.
Plus, it’s UV-stabilized, so it won’t fall apart in the sun.
3. PETG (Polietileno Tereftalato Glicol)
PETG is my go-to when I need crystal-clear parts.
This plastic is so clear it makes glass jealous. And unlike glass, it won’t shatter when you drop it.
Forming temperature: 120-140°C (248-284°F)
Best for:
- Envases médicos
- Expositores para minoristas
- Recipientes para alimentos
- Expositores para puntos de venta
- Clear protective covers
Here’s what I love about PETG:
It’s FDA-approved for food contact. So if you’re making anything food-related, PETG has your back.
The only catch? It scratches easier than some other plastics. But for most applications, that’s not a deal-breaker.
4. Policarbonato (PC)
Need something practically bulletproof?
Enter polycarbonate.
This is the stuff they make riot shields from. Seriously.
Forming temperature: 180-210°C (356-410°F)
Best for:
- Protecciones para máquinas
- Aircraft components
- Productos sanitarios
- Equipamiento de seguridad
- High-stress applications
Fair warning: polycarbonate requires higher temps and more vacuum pressure than other plastics. But the results are worth it.
5. Acrílico (PMMA)
El acrílico es la reina de los plásticos moldeados al vacío.
It’s crystal clear, scratch-resistant, and gives a high-end look to any project.
Forming temperature: 160-190°C (320-374°F)
Best for:
- Letreros luminosos
- Vitrinas
- Light diffusers
- Claraboyas
- Decorative pieces
The challenge with acrylic?
It’s more brittle than other plastics. You need to be careful with sharp corners and thin sections.
But when you nail it? The results are stunning.
6. PVC (cloruro de polivinilo)
PVC is everywhere. And for good reason.
It’s versatile, affordable, and handles weather like a pro.
Forming temperature: 100-120°C (212-248°F)
Best for:
- Packaging blisters
- Señalización exterior
- Componentes industriales
- Envases médicos
- Chemical-resistant parts
One thing to watch out for:
PVC releases harmful fumes when overheated. Always use proper ventilation.
7. Polypropylene (PP)
Polypropylene is the flexibility champion.
This plastic can take a beating and bounce right back.
Forming temperature: 150-170°C (302-338°F)
Best for:
- Living hinges
- Recipientes para alimentos
- Depósitos químicos
- Medical components
- Flexible packaging
The tricky part?
PP has high shrinkage rates. You’ll need to compensate in your mold design.
Thickness Matters: Choosing the Right Gauge
Here’s something most beginners overlook:
Thickness is just as important as material type.
Too thin? Your parts will be flimsy.
Too thick? Good luck getting clean details.
Here’s my rule of thumb:
0.5-1.5mm: Light-duty packaging, disposable items
1.5-3mm: Standard parts, displays, enclosures
3-6mm: Heavy-duty applications, structural components
6mm+: Specialized applications requiring extreme strength
Remember: thicker plastic needs more heating time and stronger vacuum pressure.
Material Selection Based on Your Application
Different projects need different plastics.
Let me break it down by application:
For outdoor use: Go with ABS, ASA, or UV-stabilized plastics
For food contact: PETG, PP, or food-grade HIPS
For clarity: PETG, PC, or acrylic
For chemical resistance: PP, PVC, or HDPE
For cost-sensitive projects: HIPS all the way
For high-stress parts: PC or ABS
Consejos profesionales para moldear al vacío con éxito
After years of vacuum forming, here are my top tips:
1. Always pre-dry hygroscopic plastics
Materials like PC and PETG absorb moisture from the air. This moisture turns to steam during forming, creating bubbles and weak spots.
Solution? Pre-dry these plastics at 60-80°C for 2-4 hours.
2. Use the right forming temperature
Too hot = sagging and webbing
Too cold = poor detail and weak parts
Invest in a good infrared thermometer. Your parts will thank you.
3. Consider draft angles
Straight walls are vacuum forming’s enemy. Add at least 3-5 degrees of draft to all vertical surfaces.
4. Test, test, test
Every vacuum forming setup is different. What works on my machine might need tweaking on yours.
Start with scrap material and dial in your settings before using the good stuff.
Where to Source Vacuum Forming Plastics
Finding good plastic suppliers can be tricky.
Here’s where I get my materials:
For small quantities: Local plastics distributors often sell remnants perfect for testing
For production runs: Industrial plastics suppliers offer better pricing on full sheets
For specialty materials: Online suppliers like McMaster-Carr have everything (but at a premium)
Pro tip: Check with local sign shops. They often have offcuts they’ll sell cheap or even give away.
Common Vacuum Forming Mistakes to Avoid
I’ve made every mistake in the book. Learn from my failures:
Using the wrong plastic: Just because it’s a thermoplastic doesn’t mean it’s good for vacuum forming
Sobrecalentamiento: More heat isn’t always better. You’ll end up with thin spots and tears
Mal diseño del molde: Sharp corners and undercuts = failed parts
Ignoring material properties: Each plastic has quirks. Respect them.
Skipping surface preparation: Clean your plastic sheets. Dust and oils cause defects.
Lo esencial
Choosing the right plastic for vacuum forming doesn’t have to be complicated.
Start with HIPS for general projects. Move to ABS when you need more strength. Use PETG for clarity. And save polycarbonate for when you need maximum durability.
Remember: the best plastic is the one that meets YOUR specific needs at a price that makes sense.
Now that you know what plastic can be used for vacuum forming, it’s time to start creating.
What will you make first?