Plastic injection molding can be a great way to manufacture plastic parts at scale. However, the costs involved can vary widely depending on the complexity of the parts and other factors. In this comprehensive guide, as a professional plastic injection molding manufacturer, I’ll cover everything you need to know about the key factors that affect plastic injection molding costs.
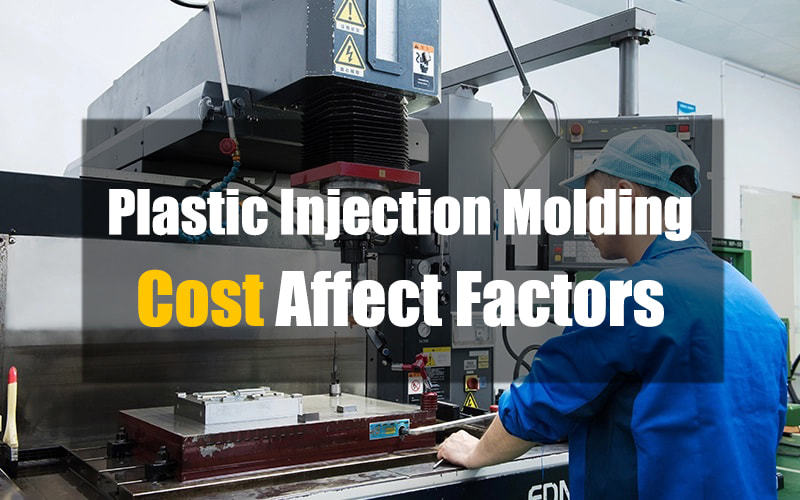
What Factors Affect the Cost of Plastic Injection Molding?
Complex molds, more cavities, larger parts, exotic materials, extra machining, lower budgets, location, and poor design decisions all increase injection molding costs substantially. Careful analysis and standardization helps optimize manufacturing economics.
Mold Complexity Drives Costs Up
One of the biggest factors that impacts injection molding pricing is the complexity of the mold design. Molds with complex geometries, tight tolerances, and precision details cost more to produce.
Several specific mold design elements can increase costs, including:
- Sharp corners or edges
- Thin ribs or walls
- Undercuts and side pulls
- Actions, cams, and other moving components
In general, anything that makes the mold more difficult or time-consuming to machine will increase the injection molding cost. Simple molds can be made for as little as $1,000 to $5,000, while highly complex precision molds can cost $50,000 to $100,000 or more.
And it’s not just the upfront mold fabrication fees that go up. Complex molds also often require specialized skills and machinery to operate and maintain properly over time. So while simplified mold designs may cost more per part upfront, they frequently save money over the total production lifecycle.
More Cavities Mean Higher Initial Costs
Another key pricing factor for injection molds is the number of cavities—the impressions in the mold that shape each product part. Molds can have anywhere from one to dozens of cavities.
Generally speaking, the more cavities in the mold, the higher the total cost will be. After all, the mold has to be larger overall to accommodate more cavities. The added size and detail requires more material, machining time, finishing work, etc.
However, keep in mind that adding cavities also increases total throughput capacity. So while a 4-cavity mold costs more than a 2-cavity design, you can recover some of that added expense by producing more parts per cycle.
Determining the optimal number of cavities for cost efficiency depends on your budget, part design complexity, machine capacity, and projected order volumes. A mold flow analysis can help visualize fill and cooling issues to find the right balance.
Part Size and Design Restrictions
Larger injection molded components require larger steel molds, more plastic resin per shot, longer cycle times, and higher clamp tonnage injection molding machines. All of these dimensional factors increase manufacturing costs.
Furthermore, certain part geometries like deep ribs, bosses, and square internal corners may shrink and warp unevenly, causing defects. Avoiding overly restrictive design details allows molds and parts to be produced faster and more affordably.
Carefully evaluate your part size and layout to minimize unnecessary bulk and complexity. Thorough DFM analysis early on can optimize the mold and component for functionality rather than arbitrary aesthetic choices that ultimately drive up cost for no added benefit.
Exotic Materials Are More Expensive
For simple injection molds running commodity resins like PP, PE, PS, ABS, etc., material costs are fairly consistent—usually between $1.00-$2.00 per pound. However, filling molds with more advanced polymers or composites can multiply those material prices significantly.
For example, specialized grades of engineering thermoplastics can range from $3-$5 per pound or higher. Additives like impact modifiers, UV stabilizers, flame retardants, and glass/carbon reinforcement also bump cost per pound values up.
In addition, high performance resins usually run on the upper end of processing temperature windows. So they require higher clamp tonnage machines and more heat-resistant cavity tool steel to injection mold successfully without degrading properties.
Carefully balance your part performance requirements against material options to avoid paying for overspec’d resins. Sometimes an uncompounded commodity polymer can deliver adequate properties at a fraction of the cost.
Cooling Channel Machining Adds Cost
Effective cooling channels help minimize injection mold cycle times by rapidly pulling heat out of the mold and solidifying parts faster. The fastest injection mold cooling possible reduces manufacturing costs in the long run by maximizing hourly production rates.
However, all that extra machining work to drill precise conformal cooling lines does entail higher upfront mold fabrication costs. In some cases, replacing straight-drilled channels with conformal geometry can more than double the total machining time required.
Weigh your break-even timeline to determine if and where conformal cooling layouts may pay off economically vs conventional drilled holes given projected part quantities. Simplifying the cooling system is an easy way to reduce injection mold tooling costs substantially when appropriate.
Low Initial Budgets Benefit From 3D Printed Molds
Constructing injection molds via CNC machining or electrical discharge machining (EDM) requires expensive equipment operated by highly-skilled technicians. So metal tooling through traditional fabrication methods often costs thousands to tens of thousands depending on part size and complexity factors.
However, 3D printing molds with desktop stereolithography (SLA) 3D printers provides an affordable alternative. Printed molds for short run injection molding can cost less than $100 in many cases.
While 3D printed molds won’t last for as many shots as machined metal tooling, this rapid prototyping process gives product developers more flexibility to test ideas and make iterative improvements early on without breaking the bank on hardened tool steel molds. When budgets are exceptionally tight, embracing additive manufacturing is an effective way to get injection molded sample parts in hand faster and cheaper.
Standardizing Saves Money Over Time
Companies that produce a diverse range of injection molded components can streamline costs substantially by analyzing part families for common attributes to standardize wherever possible.
Standardizing on certain resin materials, wall thicknesses, surface finishes, gate locations, ejection layouts, and post-molding secondary operations vastly simplifies the injection molding process overall. It reduces sources of variability that add costs, while taking advantage of bulk purchasing power.
Carefully review all existing and pipeline plastic part designs for potential standardization opportunities. Sometimes process simplification savings offset any perceived benefits of overly customized molds and components that provide no real added value.
Location Impacts Labor Rates and Expertise
Injection molding services and rates can vary substantially depending on geographic location. In general, North American and Western European manufacturers command higher pricing due to higher local labor costs and advanced equipment capabilities serving those markets.
However, these regions also tend to offer more injection molding expertise accumulated over decades in technical precision molding. So domestic tooling and services often offset their pricing premium with higher quality consistency that avoids expensive secondary rework compared to offshore vendors.
In contrast, Asian regions like China offer significantly lower-cost injection molding tooling and services. But substantial quality variability remains a common issue with overseas outsourcing. Hidden costs frequently erase apparent upfront pricing advantage once production problems arise after tools arrive and parts reach downstream QA stages.
Carefully balance cost savings against critical quality risk factors when sourcing injection molded components from unfamiliar offshore vendors sight unseen. Domestic manufacturing provides more safeguards and technical molding support even though tooling sticker prices run higher.
Smart Design Saves More over Time
Making informed design decisions upfront avoids overbuilding complexity into injection molds that ultimately drives minimal (if any) value in the finished molded parts. Keeping planned features practical rather than for solely aesthetic reasons pays dividends in simplified molds.
Thoughtful design-for-manufacturability early on relies heavily on cross-disciplinary collaboration between designers and process engineers. Align on “good enough” requirements to prevent chasing marginal gains diminishing returns that needlessly inflate costs.
Pursuing aggressive DFM analysis also ensures adequate draft angles in the part geometry to promote easy ejection. It validates uniform section thicknesses throughout features wherever possible also to prevent defects from uneven cooling. And proactive DFM helps steer well clear of overly restrictive tolerances causing quality issues unnecessarily.
Getting injection molding tooling and part design right at the start prevents problems arising later that lead to expensive production line downtime. Rushing to market without carefully optimizing the complete manufacturability process almost always proves costlier long run.
Conclusion
This guide covers the most influential factors affecting plastic injection molding costs. But it’s not an exhaustive list, as many secondary variables can move pricing up or down to some degree situationally.
In general, the simplest molds using common resins and straightforward features prove most affordable to produce at scale. Unique customer requirements mandating atypical materials or geometries inherently drive costs upward compared to standardized configurations.
Work closely with your chosen mold maker and injection molder to capture all cost reduction opportunities around simplifying tooling and secondary operations. Then remain diligent about regularly reviewing future component designs using past lessons learned for continual process refinement and savings over time.