Flow lines are a common defect that can occur during the injection molding process. These visible lines on the surface of a plastic part are mainly an aesthetic issue, but they can still cause problems. So what exactly causes flow lines?
In this complete guide, as a professional injection molding manufacturer, I’ll cover the key factors that contribute to flow lines in injection molding. By understanding what’s behind these defects, you can take steps to prevent them.
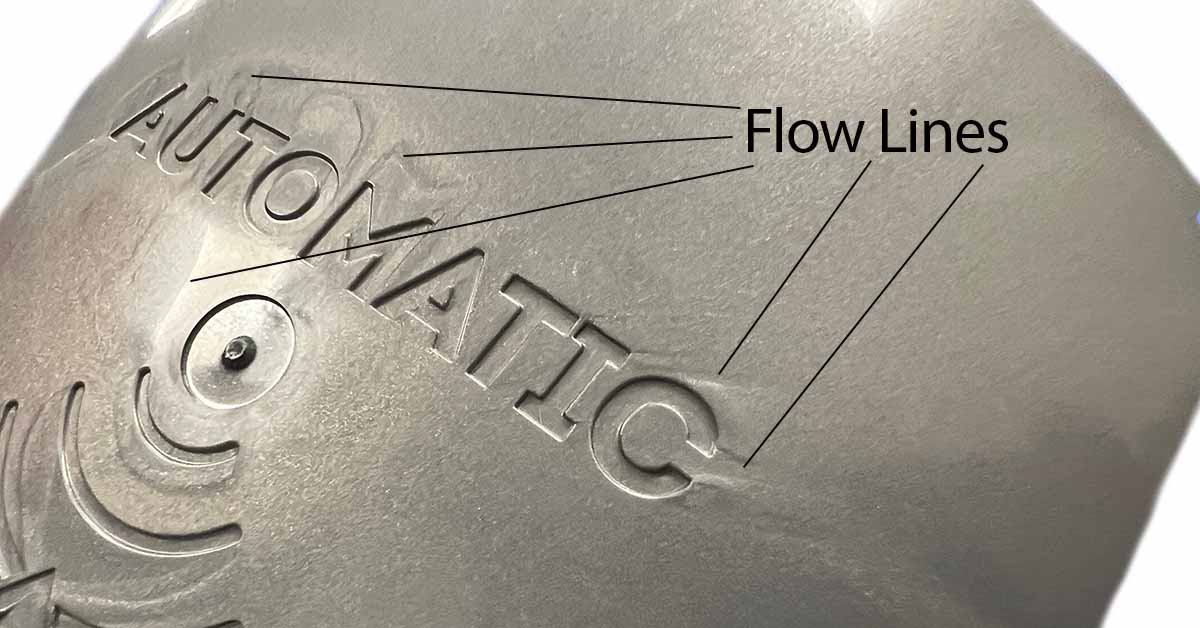
What Are Flow Lines in Injection Molding?
Before diving into the causes, let’s briefly go over what flow lines actually are.
Flow lines show up on an injection molded plastic part as visible lines, streaks, or patterns on the surface. They indicate uneven flow as the molten plastic enters and fills the mold cavity.
Often, flow lines appear as:
- Wavy lines
- Repeating circular patterns
- Discolored streaks on the plastic part
While flow lines don’t directly affect the strength or function of the finished part, they are an imperfection. For visual parts with tight cosmetic requirements, flow lines can lead to rejected parts.
Overall, flow lines come down to differences in the way sections of molten plastic cool and solidify within the mold. When there’s uneven cooling, you end up with visible lines where the flows meet.
Now let’s look at the reasons why this uneven cooling and flow can happen during injection molding.
What Causes Flow Lines in Injection Molding?
There are four main categories that lead to flow lines forming in molded plastic parts:
- The injection molding machine
- The mold itself
- The plastic material
- The machine operator
Issues in any of these areas can disrupt the way molten plastic flows into the mold cavity. When flow gets thrown off, some sections will cool at different rates, causing flow lines.
Machine Settings & Parameters
The injection molding machine itself plays a huge role in keeping plastic flow smooth and even. If any key parameters are off, flow lines can start forming.
Low injection pressure – Without enough pressure pushing the molten plastic into the mold, there won’t be uniform packing and material flow. Low pressure allows sections of the flow to cool at different rates.
Low nozzle temperature – The nozzle transfers heat into the plastic right before it enters the mold. If it’s not hot enough, cooling issues start immediately as the melt hits the mold.
Slow injection speed – Too slow of an injection speed gives molten plastic more time to start cooling non-uniformly before filling the mold. This variability in temperature causes flow issues.
Short cycle times – If the overall cycle or cooling time is too fast, the plastic in the barrel might not reach optimal melt temperature before getting injected.
Mold Design Issues
Flaws in mold design are another major factor behind flow line defects. Even tiny nuances like vents, gates, and geometry can disrupt flow:
Improper venting – Trapped air causes blocks and resistance to flow. When vents don’t do their job properly, this leads to uneven filling and cooling.
Small gates/runners – Restricted gates and thin runners impede flow, which allows cooling before plastic reaches mold cavities.
Complex geometry – Sharp edges or ribs act as barriers that radically change flow direction. Sudden changes encourage non-uniform cooling.
Variable wall thickness – Thin sections cool faster than thick ones. When molten plastic travels from thick areas to thin sections, the temperature difference causes flow issues.
Material Factors
Believe it or not, the plastic resin itself can also play a role in flow line formation:
Low melt flow rate – Very viscous, slow-flowing materials are prone to cooling at different intervals. This causes visible lines where flows meet.
Lack of lubricant – Insufficient lubricant inhibits flow for plastics traveling through longer narrow sections. More restriction allows cooling variations.
Operator Influence
While automated systems help avoid it, human error should not be underestimated:
Inconsistent cycle times – If an operator fails to maintain the same sequence timing, this fluctuates parameters like temperature. Inconsistent conditions from cycle to cycle lead to cooling issues.
Poor maintenance – Failure to remove burrs or obstructions in mold components adds flow resistance. Build-up contributes to uneven filling and cooling.
How to Prevent Flow Lines in Injection Molded Parts
Luckily, once you know what to look for, there are ways to combat flow lines. Tweaks to machines, molds, materials, and operator training help minimize the chances of flow defects.
Here are some key ways plastic manufacturers avoid flow lines:
- Optimize injection pressure, temperature, and speed
- Use proper mold venting and gates
- Choose plastic materials with suitable flow properties
- Design uniform part geometry and wall thickness
- Automate process settings and cycle timing
- Perform preventative mold maintenance
While completely eliminating flow lines is difficult, identifying why and where they occur is the first step. Adjustments to equipment and practicing vigilance goes a long way in minimizing flow defects.
Careful analysis of machine settings, material viscosity, mold components, and adherence to quality procedures all promote smooth, even flow of plastic through injection molds. This consistency means fewer opportunities for sections to cool non-uniformly.
The Bottom Line
Flow lines happen when the complex injection molding sequence gets thrown off balance. Understanding potential trouble areas helps get things back on track.
The good news is flow lines rarely compromise part strength if kept cosmetic. But keeping vigilant with your injection molding process controls and mold design helps avoid scrapping expensive plastic parts over mostly aesthetic defects.
Now that you know why flow disruptions happen, you can zero in on weak points in the system. Taking strategic steps to promote uniform plastic flow minimizes chances for sections to cool at different rates during injection molding.
What has your experience been dealing with flow line defects? Have any other tips for keeping injection molding flow smooth and consistent? Let me know in the comments section below!