La capacité de grenaille, également connue sous le nom de capacité d'injection, est un concept crucial pour toute personne impliquée dans le moulage par injection. Comme nous le verrons, la compréhension de la capacité d'injection permet d'éviter des problèmes courants tels que le sous-remplissage, un mauvais contrôle du processus et la dégradation des matériaux.
Dans ce guide complet, en tant que professionnel fabricant de moulage par injection de matières plastiquesNous commencerons par les principes de base :
- Qu'est-ce que la capacité de tir ?
- Pourquoi la capacité de tir est-elle importante ?
- Calcul de la taille du tir
Nous aborderons également des sujets plus avancés tels que :
- Utilisation de la capacité de tir
- Facteurs influençant la taille de l'injection du produit
- Différents concepts d'unités d'injection
Plongeons dans le vif du sujet.
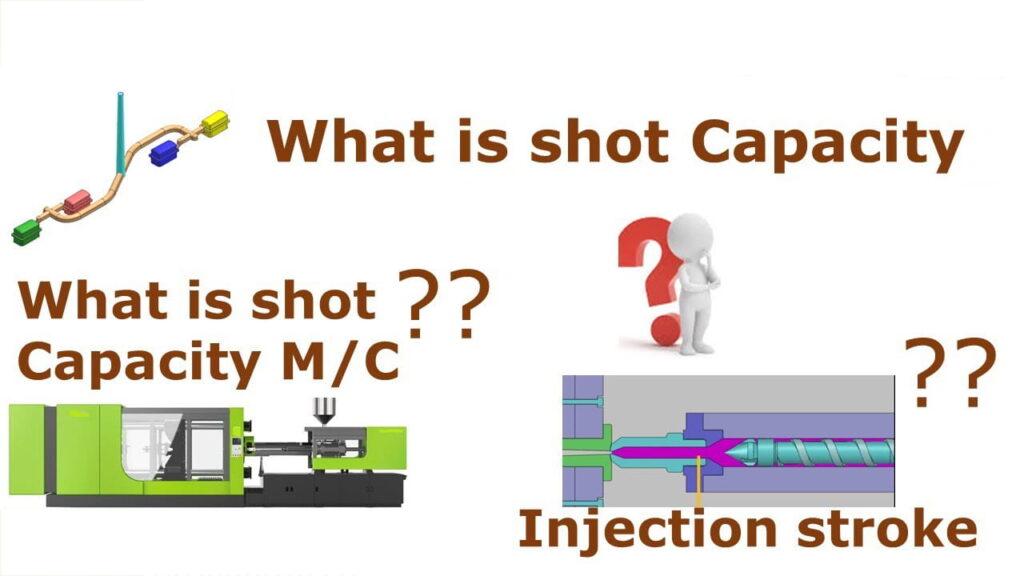
Qu'est-ce que la capacité de grenaillage dans le moulage par injection ?
La capacité de tir (ou capacité d'injection) est la quantité maximale de matériel qui peut être injecté dans un moule au cours d'un cycle.
Plus précisément, il s'agit du poids ou du volume total de matériau que la vis d'injection peut délivrer par injection.
La capacité de tir est généralement mesurée en :
- Centimètres cubes (cc)
- Pouces cubes (in3)
- Onces (oz)
- Grammes (g)
Par exemple, une machine de moulage par injection peut avoir une capacité de production de 8 onces ou 266 grammes.
Le poids/volume maximal de la grenaille dépend de plusieurs facteurs :
- La taille de la vis d'injection
- Pression hydraulique disponible
Voyons maintenant pourquoi il est important de calculer avec précision la capacité de tir.
Pourquoi il est essentiel de comprendre la capacité de tir
Il est important de bien choisir la taille de l'injection afin d'éviter plusieurs problèmes liés au moulage par injection :
1. Dégradation des matériaux
Les petites tailles de grenaille (moins de 20% de capacité de tonneau) donnent souvent lieu à des longs temps de séjour.
De longs temps de séjour peuvent dégrader le polymère par surchauffe, oxydation ou même combustion. Cela conduit à :
- Pièces décolorées
- Parties faibles
- Pièces avec odeur
2. Sous-remplissage
Une taille d'injection inadéquate signifie qu'il n'y a pas assez de matériau pour remplir complètement le moule.
Le présent sous-remplissage laisse une section non remplie à l'intérieur de la pièce, ce qui entraîne des problèmes esthétiques.
3. Clignotant
D'autre part, les grenailles de grande taille (plus de 65% de capacité de tonneau) fournissent un excès de matière.
Le matériau supplémentaire s'échappe du moule, ce qui provoque clignotant - l'excédent de plastique attaché à la pièce finie.
4. Mauvais contrôle des processus
Qu'il s'agisse de petites ou de grandes quantités, il est extrêmement difficile de contrôler des facteurs tels que la température et la pression.
Il en résulte des incohérences entre les cycles et les rejets.
Voyons maintenant comment calculer la taille de la grenaille pour votre application.
Comment calculer la taille de la grenaille dans le moulage par injection ?
Pour déterminer la taille optimale d'un tir, il faut prendre en compte les éléments suivants :
- Volumes du système d'alimentation
- Volume de la pièce
- Rétrécissement du polymère
- Impact des additifs éventuels
Voici la formule de base :
Taille du produit/moule = Volume du système d'alimentation + Volume de la pièce + Retrait
Les principaux éléments du système d'alimentation sont les suivants
- Épicéa : Fixe le système de glissières à la buse de la machine
- Coureur : Acheminement du matériel de l'épicéa jusqu'aux portes
- Portes: Contrôler le flux dans les cavités
Examinons de plus près chacun de ces facteurs :
Volume du système d'alimentation
Le système d'alimentation comprend l'épicéa, les stolons et les portes.
Veillez à calculer le volume de chaque composant du système d'alimentation en fonction de ses dimensions.
Par exemple, un coureur ayant une section transversale de 8 mm x 3 mm et une longueur de 35 mm aura un volume de.. :
Volume = Section x Longueur
= 8 mm x 3 mm x 35 mm = 840 mm3 (0,84 cc)
Additionnez les volumes de l'épicéa, des stolons et des portes pour obtenir le volume total du système d'alimentation.
Volume de la pièce
Lorsque vous concevez ou sélectionnez une pièce, faites attention au volume des cavités.
Par exemple, une pièce en forme de cube mesurant 25 mm x 25 mm x 25 mm a un volume de.. :
Volume = Longueur x Largeur x Hauteur
= 25 mm x 25 mm x 25 mm = 15,625 mm3 (15,65 cc)
Il est essentiel de déterminer avec précision le volume, c'est pourquoi vous devez travailler avec le concepteur du moule si nécessaire.
Rétrécissement des polymères
Comme nous le savons, les polymères rétrécissent lorsqu'ils refroidissent. Veillez à tenir compte de cette réduction de volume.
Par exemple, polypropylène (PP) se rétrécit autour de 2% au fur et à mesure qu'il se solidifie.
Ainsi, si notre pièce a un volume de 15,65 cm3, nous nous attendons à ce qu'elle se rétracte jusqu'à.. :
15,65 cc x 0,02 = 0,313 cc
L'importance du retrait dépend fortement du matériau. Travaillez avec votre fournisseur de résine pour obtenir un chiffre précis.
Impact des additifs
Les charges, les renforts, les colorants et autres additifs modifient la densité et la viscosité du polymère.
Prenez soigneusement en compte les additifs lors de la détermination de la taille de la dose afin d'éviter les surprises !
Tout mettre bout à bout
Par exemple, disons que nous devons déterminer la taille d'un tir pour une pièce PP avec :
- Volume du système d'alimentation : 25 cc
- Volume de la pièce : 15,65 cc
- 2% retrait : 0,313 cc
La taille totale de la prise de vue serait de :
Taille du jet = Volume du système d'alimentation + Volume de la pièce + Retrait
= 25 cc + 15,65 cc + 0,313 cc = 40,96 cc
Ce chiffre nous donne la taille totale de la grenaille en centimètres cubes.
Ensuite, nous nous intéresserons à l'utilisation de la capacité de tir, c'est-à-dire à la proportion de votre baril que vous devez remplir.
Utilisation de la capacité de grenaillage pour le moulage par injection
Les lignes directrices générales suggèrent
- Résines de base (PP, PE) : Utiliser 20-80% de la capacité totale d'injection.
- Résines techniques (nylon, ABS) : Utiliser 30-50% de la capacité totale d'injection.
Cela permet d'éviter les problèmes liés à des temps de séjour trop longs ou à un excès de matière dans le tonneau.
Par exemple, disons que notre canon a une capacité totale de 100 cc.
Pour le polypropylène, la taille de l'échantillon doit être comprise entre 20 et 80 cm3.
Et pour les ABS entre 30 et 50 cc.
Si vous prévoyez d'utiliser différents matériaux, envisagez d'acheter plusieurs tailles de fûts pour vous donner de la flexibilité.
Examinons maintenant quelques-uns des facteurs qui déterminent la quantité de matériau que vous pouvez injecter dans le moule.
Quels sont les facteurs qui influencent la taille des tirages de produits ?
La taille de la prise de vue du produit dépend fortement de la taille de la prise de vue :
1. Dimensions du système d'alimentation
La taille et la conception des composants tels que les carottes, les glissières et les portillons déterminent la quantité de matériau qui peut atteindre les cavités.
L'optimisation de ces trajets permet de réduire la quantité de matière piégée dans le système d'alimentation.
2. Nombre de cavités
Plus il y a de cavités dans votre moule, plus il faut de matériau. Soyez attentif à l'impact de la modification du nombre de cavités sur la taille de l'injection.
3. Propriétés des matériaux
Comme indiqué précédemment, la résine spécifique choisie et les additifs éventuels déterminent le retrait volumétrique et la viscosité, qui ont tous deux une incidence sur le calcul de la taille de la grenaille.
4. Exigences en matière d'emballage
Si l'application exige des tolérances dimensionnelles serrées, il faut généralement utiliser plus de matériau pour tenir compte du retrait post-moulage.
Prenez soigneusement en compte les exigences en matière de précision ou de stabilité.
La première étape consiste à comprendre ce qui entre dans la composition de la dose de produit. Ensuite, explorons l'unité d'injection qui prépare et délivre cette dose.
Concepts d'unités d'injection pour la capacité de tir
L'unité d'injection est chargée de :
- Chauffage et fusion de la résine
- Mélange du polymère
- Tirer de manière cohérente sur le moule
Cela est difficile avec des polymères tels que les polymères fluorés qui posent des problèmes :
- Conductivité thermique
- Chaleur spécifique
- Viscosité de la matière fondue
Il existe quelques configurations courantes de systèmes d'injection :
1. Piston ou vérin à un étage
Utilise un piston pour injecter le produit sans traitement préalable. Simple mais inefficace pour le chauffage et le mélange.
2. Ram à deux étages
Les tentatives d'amélioration des performances en une seule étape restent inefficaces.
3. Vis à un étage
La vis assure le mélange et le chauffage. Le vérin fournit la pression pour l'injection.
4. Combo vis/barre
Option la plus avancée. Optimisée pour le chauffage/mélange (vis) et la pression d'injection (bélier).
Malgré les différences de conception, les unités d'injection sont cotées sur :
- Pression d'injection maximale
- Volume d'injection disponible
Tenez compte de ces spécifications lors de la sélection d'un système.
Maintenant que vous avez compris les principes de base de la capacité de tir, récapitulons quelques points essentiels.
Conclusion et résumé
Déterminer la taille de la grenaille et disposer de la capacité du barillet nécessaire est essentiel pour la réussite du moulage par injection.
Pour résumer :
- La capacité de tir est la quantité maximale de matériau par tir en centimètres cubes ou autres unités.
- Éviter les problèmes liés à la dégradation des matériaux, au flashage et au contrôle des processus
- Calculer soigneusement les volumes du système d'alimentation, de la pièce et de la rétraction.
- L'utilisation typique de la capacité d'injection est de 20-80% pour les résines de base.
J'espère que ce guide vous a donné une bonne vue d'ensemble de la capacité de grenaillage dans le moulage par injection. N'hésitez pas à me contacter si vous avez d'autres questions !