Qu'est-ce que la position de basculement dans le moulage par injection ?
La position de basculement, également connue sous le nom de point de basculement V/P, est un point de transition crucial dans le processus de moulage par injection. Cette position indique le moment où la machine de moulage par injection passe d'une phase de remplissage entraînée par la vitesse à une phase d'emballage entraînée par la pression.
Comprendre ce qu'est la position de basculement et comment l'optimiser est essentiel pour produire des pièces moulées cohérentes et de haute qualité. Dans ce guide complet, en tant que professionnel fabricant de moulage par injection de matières plastiquesJe vais vous expliquer tout ce que vous devez savoir pour déterminer et contrôler la position de basculement pour le moulage par injection de précision.
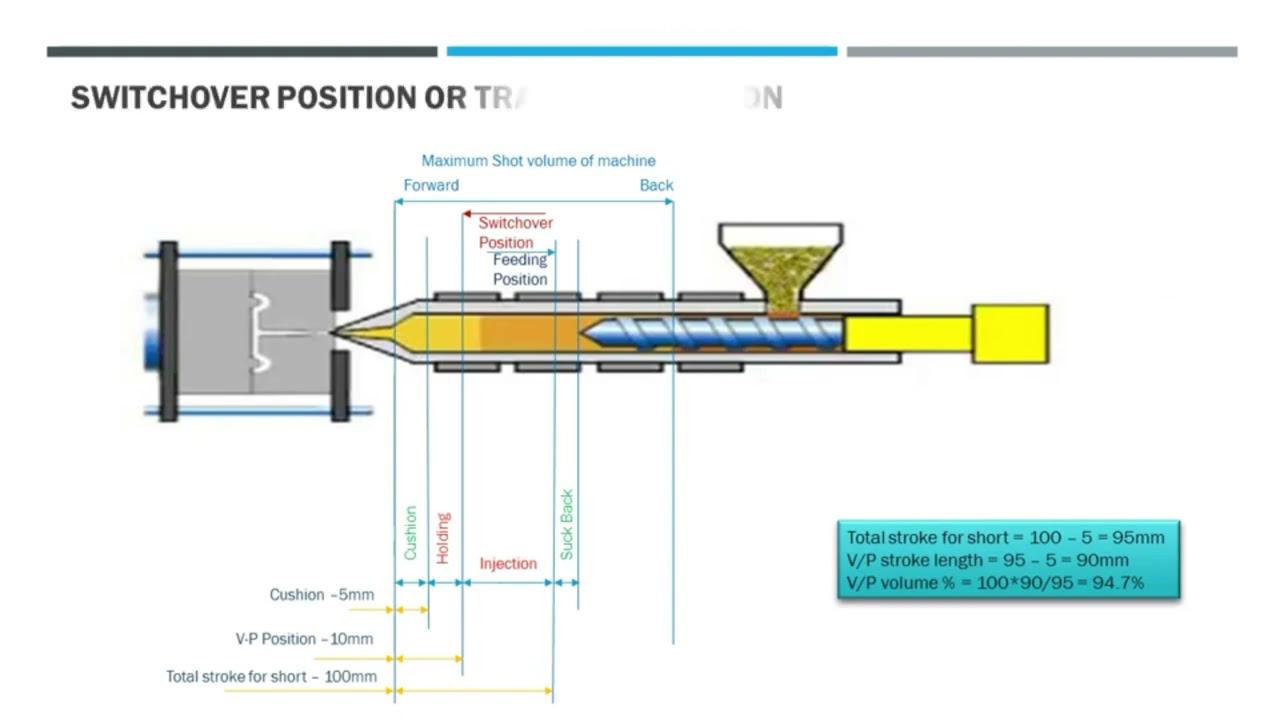
Quand le basculement a-t-il lieu ?
Au cours du cycle de moulage par injection, deux étapes distinctes permettent de remplir les cavités du moule avec du plastique en fusion :
- L'étape de remplissage ou d'injection
- L'étape de l'emballage ou de l'attente
La position de basculement marque la transition entre ces deux étapes :
- Étape de remplissage : La vis est projetée vers l'avant, injectant le plastique fondu dans le moule à une vitesse contrôlée. L'objectif est de remplir rapidement environ 95-98% du moule.
- Passage à l'euro : En position de commutation, la machine passe du contrôle de la vitesse au contrôle de la pression. Cela se produit généralement lorsque la cavité est 95-98% remplie.
- Étape d'emballage : La vis applique une pression constante pour tasser le moule et compenser le rétrécissement du matériau lors du refroidissement.
En résumé :
- La position de commutation correspond à la transition entre le contrôle de la vitesse et le contrôle de la pression.
- Il se produit généralement lorsque la cavité du moule est 95-98% pleine
- La détermination du point de basculement optimal est cruciale pour la cohérence.
Voyons maintenant comment déterminer le moment du basculement.
Comment la position de basculement est-elle déterminée ?
Les machines de moulage par injection peuvent détecter le moment où elles doivent passer du remplissage à l'emballage de quelques manières courantes :
1. Par position de la vis
C'est la méthode la plus répandue. La machine surveille le mouvement linéaire de la vis pendant l'injection. Lorsque la vis atteint une position prédéfinie, généralement 95-98% de sa position maximale vers l'avant, la commutation est déclenchée.
La position de la vis est un indicateur du remplissage de la cavité. La logique veut que si la vis s'est déplacée jusqu'à une certaine position, la cavité du moule devrait maintenant être en grande partie remplie de plastique.
Toutefois, cette méthode peut être incohérente :
- Les différences de densité ou de viscosité du matériau d'un tir à l'autre modifient la corrélation entre la position de la vis et le pourcentage de remplissage de la cavité.
- L'usure de la vis et du canon peut modifier les valeurs de position au fil du temps.
Cependant, la position de la vis est simple et suffisante pour de nombreuses applications.
2. Par pression
Certaines machines peuvent passer du contrôle de la vitesse au contrôle de la pression lorsque la pression d'injection mesurée atteint un point de consigne.
Au fur et à mesure que le moule se remplit de plastique, la pression augmente progressivement. Lorsque la pression atteint le niveau prédéfini, indiquant généralement un remplissage de 95%+, la transition se produit.
Cela permet d'éliminer les incohérences dues à l'usure des vis et aux changements de consistance du matériau. La pression est en corrélation directe avec le remplissage de la cavité, indépendamment de l'état de l'équipement ou de la qualité du matériau. résine les différences entre les lots.
Toutefois, cette méthode peut encore être faussée si des facteurs tels que la vitesse d'injection ou la température du moule changent de manière significative.
3. En fonction de l'heure
Une autre option consiste à basculer en fonction de l'heure d'injection. La machine utilise simplement une minuterie pour effectuer la transition à un moment précis de chaque cycle.
Par exemple, l'analyse des données peut montrer que 1,4 seconde d'injection à une certaine vitesse remplit 95% du moule de manière fiable. La machine passera donc du contrôle de la vitesse au contrôle de la pression à 1,4 seconde à chaque fois.
Cette approche est cependant rarement réalisable. Pour définir et maintenir une valeur de temps précise, des paramètres tels que la taille des pièces, la viscosité du matériau, le taux d'injection et la conception du moule doivent être extrêmement cohérents d'un cycle à l'autre. Dans la plupart des scénarios réels, il y a trop de variables incontrôlables pour se fier à une minuterie fixe.
4. Par la pression de la cavité
Enfin, les capteurs de pression dans la cavité constituent le moyen le plus avancé et le plus précis de déterminer la position de basculement.
Des capteurs discrets placés dans le moule mesurent en temps réel la pression à l'intérieur des cavités pendant l'injection. Lorsque les capteurs indiquent que la pression atteint une cible, correspondant au remplissage de 95%, le basculement est déclenché.
Cette approche tient compte des incohérences inévitables entre les prises de vue, telles que les changements de viscosité du matériau, les fluctuations de température, l'usure des vis, etc. Elle élimine également les variables de déflexion du moule que l'on trouve dans les capteurs montés sur les machines.
Cependant, l'intégration de ces capteurs augmente les coûts et la complexité. Chaque moule doit être équipé de capteurs avec ou sans fil et du matériel de transmission de données nécessaire pour communiquer avec le contrôleur central.
L'importance d'un bon passage au numérique
La position de commutation relie l'étape d'injection et l'étape d'emballage. Elle garantit que la cavité se remplit correctement au moment où la machine passe à l'application de la pression d'emballage.
Il est essentiel de réussir cette transition pour mouler des pièces de haute qualité :
- Commutation prématurée peut provoquer des tirs courts. Si la pression diminue avant que la cavité ne se remplisse complètement, le matériau cessera de s'écouler, laissant des sections non remplies.
- Le passage à l'emballage après le remplissage de la cavité peut entraîner clignotant au niveau du plan de joint ou des goupilles d'éjection. L'excédent de matière ne peut alors que s'échapper.
- Le point de commutation optimal permet d'équilibrer le remplissage rapide de la cavité tout en assurant une pression suffisante pour le démoulage. Il en résulte stabilité dimensionnelle coup par coup.
À retenir : Une synchronisation cohérente, déclenchée à environ 95% de remplissage, permet un remplissage uniforme de la cavité d'un cycle à l'autre. Cela signifie des poids et des dimensions de pièces stables, moins de pertes et des composants de meilleure qualité.
Comment optimiser la position de basculement
Commencez par examiner les données historiques du processus afin de fixer une valeur cible initiale de basculement. Les succès ou les échecs antérieurs dans le moulage du même outil avec le même matériau constituent une base de référence raisonnable.
Collecte d'ensembles de données cartographiant les valeurs de commutation enregistrées et les mesures de qualité des pièces, cycle par cycle. L'enregistrement de la position de la vis, de la pression, de la pression de la cavité, du temps de remplissage, etc. permet d'évaluer les corrélations entre le passage à la vitesse supérieure et les dimensions clés sur de nombreux cycles :
- Le passage d'une position à l'autre se produit-il systématiquement à un endroit donné ou existe-t-il des variations d'un tir à l'autre ?
- Les transitions précoces ou tardives sont-elles en corrélation avec des pièces non conformes ?
- Quelle valeur de commutation tend à produire la plus grande stabilité dimensionnelle ?
L'analyse de ces données permet d'affiner la position optimale. Des tests de validation supplémentaires permettent d'affiner les réglages de la machine (vitesse d'injection, température du moule, etc.) afin d'obtenir et de maintenir les conditions souhaitées sur plusieurs cycles.
Points de départ typiques de la position de basculement en fonction de la méthode de transition :
- Position de la vis : 95-98% de la course complète de la vis
- Pression d'injection : ~95% de la pression de remplissage maximale
- Capteurs de pression dans la cavité : 90-98% de la pression de remplissage requise
Les machines électriques précises d'aujourd'hui et les commandes de processus plus intelligentes permettent de régler un positionnement de commutation hautement reproductible pour obtenir des composants moulés incroyablement cohérents.
La mise au point d'un processus robuste avec un contrôle optimisé de la commutation V-P offre des avantages considérables en termes de qualité. Mais sans une collecte et une validation diligentes des données dès le début, combinées à une surveillance continue et disciplinée, des variations même minimes peuvent compromettre l'ensemble des efforts déployés. Une vérification rigoureuse du processus garantit une production de précision soutenue sur de longues séries de production.
Conclusion
Le position de commutation marque la transition vitale au cours du moulage par injection lorsque la machine passe du remplissage de l'empreinte à une vitesse contrôlée (injection) à l'application d'une pression constante (conditionnement). Ce changement se produit généralement à 95-98% pour le remplissage de la cavité.
Sélection de l'outil le plus approprié méthode de détection du basculement - La position de la vis, la pression d'injection, le temps précis ou les capteurs directs dans la cavité permettent de déterminer le moment où le moule a atteint le pourcentage de remplissage partiel cible. Cela déclenche, cycle après cycle, la commande calculée de passage du remplissage à l'emballage.
Une corrélation étroite entre les points de données de commutation surveillés et les caractéristiques de sortie mesurables permet d'identifier les valeurs transitoires optimales. Le maintien de ces paramètres de processus idéalisés permet ensuite de maximiser la productivité et de minimiser les écarts. La validation minutieuse du fait que seules des pièces correctement formées et répondant à toutes les spécifications sont produites constitue une assurance qualité essentielle.
Des centaines de paramètres interconnectés et de propriétés des matériaux influencent la précision globale, vérification des performances grâce à une évaluation complète des données, qui confirme que les limites de qualité mesurées statistiquement répondent durablement aux attentes au cours de campagnes de fabrication prolongées.
Vous savez désormais ce qu'est exactement la position de basculement et comment l'exploiter pour un contrôle méticuleux du processus. Le fait de déclencher systématiquement la transition au point idéal de la séquence de remplissage et d'emballage favorise une grande cohérence des pièces et minimise les variations qui nuisent à l'efficacité et à la qualité.
Quelles sont les questions que vous vous posez encore sur la détermination et l'optimisation de la position de commutation pour vos applications de moulage par injection de précision ? N'hésitez pas à me le faire savoir dans les commentaires !