Le rétrécissement. Le fléau de l'existence de tout mouleur par injection.
Vous concevez une pièce aux dimensions parfaites. Vous programmez la machine à mouler en conséquence. Vous lancez quelques échantillons. Puis, bam ! les pièces sortent sous-dimensionnées.
Ce n'est pas la fin du monde. Mais personne n'aime les surprises... surtout lorsque des pièces de haute précision sont en jeu.
La bonne nouvelle ? Le rétrécissement n'a pas à gâcher votre journée. Avec un peu de planification et de finesse, il est possible de l'apprivoiser.
En tant que professionnel moulage par injection de plastique Je vous expliquerai comment maîtriser le retrait afin de mouler des pièces répondant à des spécifications précises.
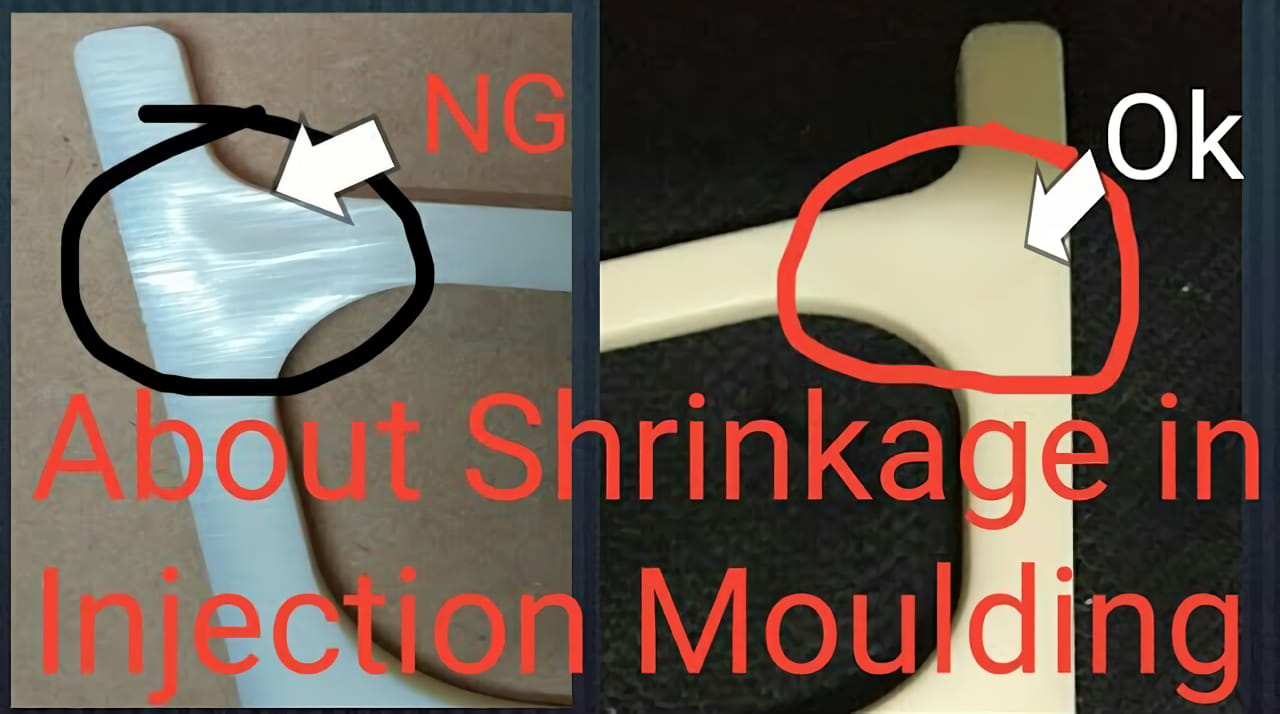
Quelles sont les causes du rétrécissement dans le moulage par injection ?
Avant de s'attaquer aux solutions, il faut d'abord comprendre les causes du problème.
Toutes les matières plastiques se rétractent lorsqu'elles se refroidissent et passent du stade de liquide fondu à celui de pièces solides. Plus le plastique est chaud, plus les chaînes de polymères se dilatent. Lorsque les choses se refroidissent, la contraction thermique se met en place. (Vous savez, cette histoire d'"air chaud qui monte" que l'on retrouve dans les cours de sciences de l'école primaire).
L'ampleur du rétrécissement dépend de plusieurs facteurs :
- Matériau : Les résines amorphes comme l'ABS ont tendance à se rétracter davantage que les résines cristallines comme le nylon. Pourquoi ? Les chaînes de polymères des matériaux amorphes ne sont pas aussi étroitement serrées, ce qui leur laisse plus de place pour se contracter pendant le refroidissement.
- Conception du moule : Les pièces plus épaisses ou les pièces dont l'épaisseur des parois est inégale sont sujettes à un retrait inégal. Les zones plus épaisses se refroidissent - et donc se rétractent - plus lentement que les sections plus fines.
- Conditions de traitement : Des vitesses d'injection rapides associées à une faible pression de maintien permettent au matériau de se tasser dans la cavité du moule. Ce qui permet une plus grande rétraction lorsque les choses refroidissent.
Maintenant que nous connaissons les raisons du rétrécissement, voyons comment y remédier.
Comment réduire le retrait dans le moulage par injection ?
La maîtrise du rétrécissement passe par trois approches principales :
- Optimisez la conception de votre moule
- Choisir le bon matériau
- Ajustez les paramètres de votre processus
Décortiquons-les.
1. Optimisez la conception de votre moule
Si la machine à mouler n'en faisait qu'à sa tête, chaque pièce serait refroidie exactement à la même vitesse dans toutes les sections. Pas de refroidissement inégal = pas de retrait ou de gauchissement inégal.
Mais nous ne vivons pas dans un monde parfait. Et il est plus facile à dire qu'à faire d'obtenir un refroidissement totalement uniforme sur des géométries 3D complexes.
Malgré cela, nous pouvons utiliser quelques stratégies de conception pour nous en approcher le plus possible :
- Éliminer les changements brusques dans l'épaisseur de la paroi : Essayez de passer progressivement d'une section mince à une section épaisse (les filets sont vos amis dans ce cas). Cela permet d'éviter les "points chauds" et de minimiser le rétrécissement inégal.
- Attention aux angles : Les angles vifs agissent comme des concentrateurs de tension, ce qui accentue le retrait du matériau. Les angles arrondis répartissent les contraintes de manière plus homogène.
- Placement stratégique des côtes : Les nervures et les goussets renforcent les pièces sans modifier de manière significative l'épaisseur des parois. Attention toutefois à ne pas créer de nouveaux points chauds.
- Composez le numéro de votre portail : L'emplacement de la porte détermine la manière dont le matériau s'écoule dans le moule. Veillez à ce que le remplissage soit agréable et régulier. Il n'y a pas de points faibles où le matériau ne peut pas se tasser complètement.
Conseil de pro : les logiciels de simulation permettent de prévisualiser la répartition des températures et le rétrécissement avant de découper l'acier. Cela vous permet d'optimiser la conception du moule numériquement plutôt que de procéder à des essais et erreurs coûteux dans l'atelier de production.
2. Choisir le bon matériau
Si une précision dimensionnelle extrême est nécessaire, il faut commencer par la bonne matière première.
Voici quelques éléments à prendre en compte concernant le rétrécissement :
- Résines amorphes ou cristallines : Comme indiqué précédemment, les matériaux amorphes tels que l'ABS ou le polycarbonate (PC) ont tendance à se rétracter davantage que les résines cristallines. L'acétal et le nylon sont de meilleures options si le retrait doit être limité.
- Plastiques renforcés : L'ajout de fibre de verre, de fibre de carbone ou de talc au mélange de matériaux renforce la stabilité dimensionnelle. En contrepartie, ces charges ou renforts peuvent rendre le plastique plus visqueux, ce qui peut poser des problèmes de moulage.
- Connaissez vos données PVT : Chaque fournisseur de matériaux fournit des informations détaillées sur les caractéristiques de retrait de sa résine dans différentes plages de température et de pression (données PVT). Consultez ces informations pour choisir la meilleure option.
Conclusion : Travaillez avec votre fournisseur de matériaux pour choisir la résine qui répond aux besoins de l'application ET qui offre un retrait minimal.
3. Affiner les paramètres du processus
Enfin, tirez parti de la flexibilité des machines de moulage par injection pour affiner le processus de moulage lui-même.
L'objectif est d'introduire autant de matière que possible dans le moule AVANT que les choses ne commencent à se solidifier. Cela laisse moins de place à la contraction naturelle qui se produit pendant le refroidissement.
Voici quelques modifications de processus qui méritent d'être essayées :
- Augmentez la pression : L'application d'une pression d'injection plus importante rapproche les chaînes de polymères les unes des autres. L'augmentation de la pression de tassement et de maintien permet de contrer le rétrécissement après l'injection initiale en compactant encore plus les molécules.
- Ralentir les remplissages : Les taux de remplissage rapides peuvent laisser des points faibles dans le profil du matériau. La diminution de la vitesse d'injection permet au matériau de se tasser davantage.
- Prolonger le temps de refroidissement : Je sais, je sais... les temps de cycle plus longs réduisent la productivité. Mais le fait de laisser les pièces refroidir complètement avant de les éjecter évite de les retirer dans un état "solidifié mais encore en contraction".
Conseil de pro : n'augmentez pas les pressions dès le départ. Commencez par une pression modérée et augmentez-la progressivement tout en évaluant la qualité de la pièce. Une pression excessive peut également entraîner des problèmes tels que des marques d'enfoncement, des vides ou des éclats.
Combien faut-il "surdimensionner" pour tenir compte du rétrécissement ?
L'heure de vérité a sonné.
La mise en pratique de toutes ces connaissances nécessite une étape supplémentaire : compenser le retrait en surdimensionnant intentionnellement l'empreinte du moule.
Mais de combien ?
Comme toujours, il n'y a pas de règle absolue. Le rétrécissement dépend de tous les facteurs décrits ci-dessus. La meilleure réponse consiste à produire des échantillons qui reproduisent le plus fidèlement possible votre moule/processus de production.
Cependant, voici quelques objectifs approximatifs de surdimensionnement en fonction de la résine avec laquelle vous travaillez :
- Polyéthylène (PE) : 2-5%
- Polypropylène (PP) : 1.5-3%
- Acrylonitrile Butadiène Styrène (ABS) : 2-4%
- Nylon : 2-4%
Ces pourcentages doivent être validés par des échantillonnages, mais ils constituent des points de départ raisonnables pour le dimensionnement initial des moules.
L'essentiel est d'ajuster les dimensions à partir de là, en se basant sur des données réelles mesurées à partir de pièces moulées. Il faut procéder à des ajustements itératifs, mais le fait de trouver la surcote exacte nécessaire pour produire des pièces de dimensions précises et stables en vaut la peine.
Personne n'a dit que le moulage par injection était facile ! Mais un peu de connaissances combinées à quelques ajustements stratégiques du processus permettent de minimiser les retraits.
Et lorsque tout est dit et fait, cette pièce de belle taille qui sort du moule en vaut la peine !