La création d'un moule d'injection PVC personnalisé peut sembler intimidante. Mais lorsqu'il est décomposé en étapes simples, le processus est très facile à gérer.
Dans ce guide complet, en tant que Moulage par injection de PVC vous apprendrez à concevoir et à produire un moule d'injection en PVC du début à la fin. Plus précisément, nous aborderons les points suivants
- Aperçu des matériaux PVC
- Applications du moulage par injection du PVC
- Considérations relatives à la conception
- Prototypage de la pièce
- Création de l'outillage du moule
- Le processus de moulage par injection
- Touches finales
Commençons par quelques informations sur le PVC lui-même.
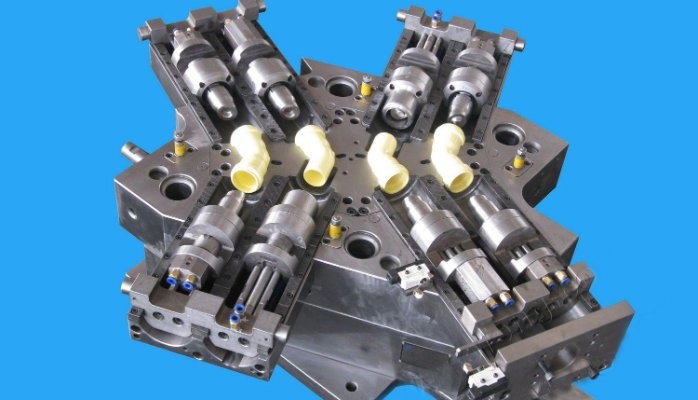
Qu'est-ce que le PVC ?
Le PVC, ou chlorure de polyvinyle, est l'un des thermoplastiques les plus polyvalents qui soient. Voici quelques informations sur le PVC :
Rentabilité - Par rapport aux plastiques spécialisés, les granulés de PVC et les matières premières sont peu coûteux. Cela permet de réduire les coûts de fabrication globaux.
Personnalisable - Le PVC peut être mélangé avec des plastifiants, des stabilisateurs et des charges pour obtenir des propriétés spécifiques. Le PVC peut ainsi être adapté à de nombreuses applications.
Durable - Grâce à sa grande résistance à la traction et aux chocs, les pièces en PVC moulé peuvent résister à des années d'utilisation.
Examinons maintenant quelques applications courantes des moules d'injection PVC personnalisés.
Cas d'utilisation du moulage par injection du PVC
Parmi les utilisations les plus courantes des moules d'injection en PVC, on peut citer les suivantes :
- Tuyaux - De la plomberie à la construction, les tuyaux en PVC font partie intégrante des projets d'infrastructure.
- Équipement médical - Tous les produits, des poches à perfusion aux masques à oxygène, utilisent des pièces moulées en PVC.
- Biens de consommation - Ce matériau est utilisé dans des produits tels que les jouets, les poignées d'outils et les conteneurs de stockage.
Essentiellement, si une application nécessite un plastique abordable résistant aux produits chimiques et à l'humidité, le moulage par injection de PVC est une option qui mérite d'être prise en considération.
Passons maintenant à quelques conseils de conception.
Conception de pièces pour le moulage par injection de PVC
La première étape consiste à CAD modéliser les dessins de vos pièces. Ce prototype numérique sera ensuite utilisé pour créer l'outillage du moule.
Lors de la conception de pièces destinées au moulage par injection de PVC, il convient de garder à l'esprit les lignes directrices suivantes :
Ajouter des angles de dépouille - Inclure une légère conicité ou un angle sur toutes les surfaces verticales pour s'assurer que la pièce peut se détacher proprement de l'outil de moulage après refroidissement.
Éviter les variations d'épaisseur des parois - L'épaisseur constante de la paroi permet un refroidissement uniforme. Cela permet d'éviter les défauts tels que le gauchissement et les marques d'enfoncement.
Inclure des rayons généreux - Les angles aigus concentrent les tensions. Dans la mesure du possible, remplacer les angles intérieurs/extérieurs par de grands rayons.
Minimiser la taille globale - Les pièces plus grandes se rétractent de manière plus irrégulière. Concevez vos pièces en PVC de manière à ce qu'elles soient aussi compactes que possible.
Le respect de ces règles de conception de base garantira que votre moule en PVC personnalisé produira des pièces de qualité supérieure, lot après lot.
Passons maintenant à l'étape du prototypage.
Prototype de votre pièce en PVC avant le moulage
Une fois votre modèle CAO 3D terminé, il est tentant de se lancer dans l'usinage CNC d'un outil de moulage en aluminium. Mais ce serait une erreur.
Avant d'investir plus de $5 000 dans un moule en métal, validez d'abord votre conception à l'aide d'un prototype imprimé en 3D. Voici comment procéder :
Étape 1 - Exportez votre fichier CAO au format STL et téléchargez-le auprès d'un fournisseur de services d'impression 3D réputé. Sélectionnez un matériau durable comme le nylon ou le plastique ABS.
Étape 2 - Inspectez votre pièce imprimée en 3D dès sa réception. Vérifiez les caractéristiques essentielles telles que la précision dimensionnelle et l'état de surface.
Étape 3 - Apporter toutes les modifications nécessaires à la conception sur la base d'un examen pratique du prototype.
Ce processus de validation ne coûte que quelques centaines de dollars au maximum. Mais il garantit que votre coûteux moule d'injection métallique produira des pièces précises dès le départ.
Il est temps de fabriquer l'outillage du moule !
Créer l'outil de moulage par injection
Une fois la conception de la pièce bien établie, il est temps d'usiner les composants de l'outillage du moule. Il s'agit des éléments suivants
- Bloc de la cavité - Les inserts de moule usinés sur mesure
- Noyau/système d'éjection - Pointes et composants qui éjectent la pièce refroidie
- Système Sprue/Runner - Canaux qui acheminent le plastique fondu vers les cavités
L'usinage CNC est généralement utilisé pour fabriquer des composants de moules à partir d'acier à outils ou d'aluminium. Il s'agit d'un processus complexe qu'il vaut mieux laisser aux moulistes expérimentés.
Il faut s'attendre à des délais d'exécution de 4 à 6 semaines et à des coûts unitaires allant de $3 000 à $100 000+ en moyenne. Oui, les moules à injection nécessitent des dépenses d'investissement importantes. Mais n'oubliez pas que l'outil doit produire de manière fiable des milliers, voire des millions de répliques sur des années de cycles de production.
Vous avez donc en main les composants usinés de votre moule. Passons maintenant à l'exécution du processus d'injection à l'aide de granulés de résine PVC.
Gestion de la production de moulage par injection
Vous trouverez ci-dessous le processus de base pour passer des granulés de PVC aux pièces finies et refroidies :
Étape 1) Outil de serrage/fermeture du moule - Des presses hydrauliques de plusieurs tonnes sont utilisées pour fixer solidement les côtés du noyau et de la cavité.
Étape 2) Chauffer le fût/Injecter le PVC - La friction fait fondre les granulés qu'une vis alimente à haute pression dans les cavités du moule.
Étape 3) Outil de refroidissement du moule - Les canaux de refroidissement découpés dans l'outil solidifient rapidement le PVC en quelques secondes.
Étape 4) Ouverture/éjection de la pièce - Des systèmes hydrauliques séparent les deux moitiés du moule afin que les broches puissent sortir des pièces en plastique solides.
Le cycle entier se répète plusieurs fois par heure, produisant des pièces à un rythme rapide. Il est impératif de prendre des précautions lors de l'utilisation d'équipements de moulage par injection de qualité industrielle !
Post-traitement et finition
Les pièces en PVC fraîchement moulées présentent un excès de plastique sur le pourtour. Il convient de les éliminer à l'aide d'une lame de rasoir, de papier de verre ou d'une ponceuse à bande.
Les pièces peuvent ensuite être soudées par ultrasons en sous-ensembles ou peintes/sérigraphiées pour améliorer l'esthétique selon les besoins. Avec un outillage de moulage bien conçu, il est également possible de procéder à un marquage à chaud décoratif.
Un travail d'assemblage léger peut également être nécessaire pour transformer des paquets de composants en PVC en produits finis prêts à être emballés et expédiés.
Conclusion
Et le tour est joué ! Avec la maîtrise de la CAO, le prototypage, la fabrication de moules sur mesure, l'expertise en matière d'injection plastique et le savoir-faire en matière de post-traitement, vous êtes maintenant prêt à créer des outils de moules d'injection en PVC de qualité de production en peu de temps.
Bien sûr, il y a des détails que nous n'avons pas abordés, mais ce guide couvre toutes les phases clés du début à la fin. Nous espérons que ces conseils vous donneront confiance pour poursuivre vos propres projets de moulage par injection de PVC.
Si vous avez d'autres questions, n'hésitez pas à m'en faire part dans les commentaires. Il se peut que je rédige un contenu complémentaire si l'intérêt est suffisant !