Le moulage par injection de l'acrylique est le processus de mise en forme du plastique acrylique par injection dans un moule. Il permet de façonner l'acrylique en produits tels que des lentilles, des écrans et des panneaux. En tant que professionnel moulage par injection d'acrylique Je vais vous expliquer étape par étape tout le processus d'injection de l'acrylique.
Le processus de moulage par injection de l'acrylique commence par la conception d'un moule pour créer la pièce souhaitée. Les granulés d'acrylique sont ensuite séchés, chargés dans la machine d'injection et injectés dans le moule. Après refroidissement et durcissement, la pièce en acrylique est éjectée et peut subir d'autres étapes de finition.
Poursuivez votre lecture, je vais vous présenter chaque étape de la moulage par injection d'acrylique pour vous aider à comprendre exactement comment il fonctionne.
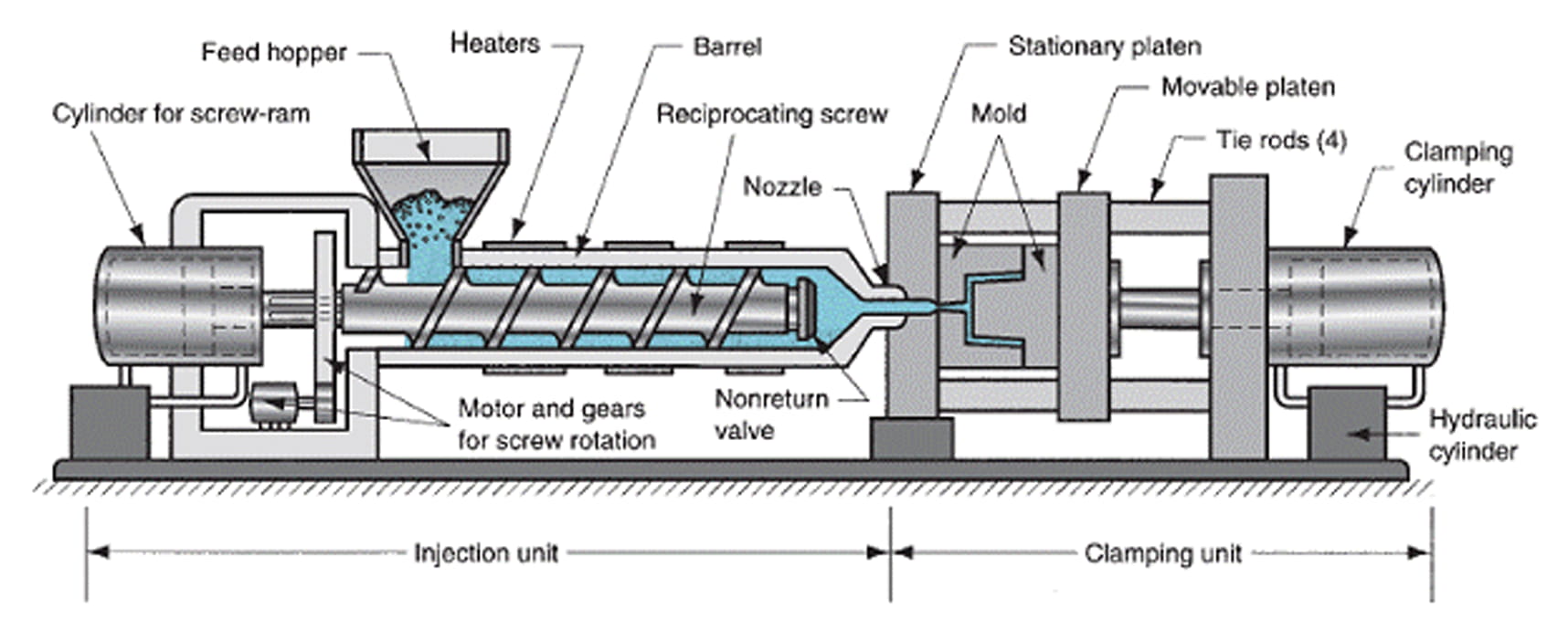
Processus de moulage par injection de l'acrylique
Étape 1 : Conception du moule
La première étape consiste à créer le moule d'injection pour former les pièces en acrylique. Le moule se compose de deux moitiés - la moitié de la cavité et la moitié du noyau - qui se rejoignent pour former l'espace intérieur du moule. L'acrylique prend cette forme une fois injecté.
Les concepteurs de moules utilisent la technologie 3D CAD pour modéliser avec précision les moules d'injection. Les géométries et les caractéristiques complexes peuvent être conçues en détail et converties en code d'usinage pour l'atelier de moulage. Les trous, les inserts, les textures et autres spécifications sont également pris en compte à ce stade précoce.
Il est essentiel de bien concevoir le moule. Des portes, des évents et des angles de dépouille intelligents garantissent un écoulement correct de l'acrylique et un résultat final de qualité. Un mouliste expérimenté tiendra compte de ces nuances lors de la fabrication de l'outil de production final.
Étape 2 : Préparation du matériau acrylique
Sous sa forme brute, l'acrylique se présente sous la forme de billes ou de pastilles translucides qui ressemblent à du sucre cristallisé. Les fabricants conservent la résine acrylique au sec dans un environnement climatisé afin de maintenir un taux d'humidité adéquat. Trop d'humidité crée des bulles et d'autres défauts une fois injectée dans le moule.
Certaines résines acryliques sont hygroscopiques. C'est pourquoi les fabricants chargent le matériau à partir d'une trémie de séchage contenant des lits de dessiccation. Des sécheurs chauffants réchauffent ensuite l'acrylique à plus de 200°F pour éliminer l'humidité résiduelle avant le moulage.
L'acrylique séché s'écoule dans des bacs de déversement en attendant l'injection. Certaines machines de moulage par injection sont même équipées de sécheurs de résine intégrés afin de simplifier le système d'acheminement des matériaux.
Processus de séchage de l'acrylique
Il est essentiel que la résine acrylique reste parfaitement sèche avant le moulage par injection. Toute trace d'humidité se transforme en vapeur instantanée lorsque le plastique chaud pénètre dans le moule.
Même les pièces les plus précises présentent de petites fissures, des bulles et des défauts visuels lorsqu'elles sont exposées à l'humidité. Pas de quoi en faire un fromage !
Étape 3 : Serrer le moule
Pour lancer la production, un opérateur fixe le moule d'injection dans la presse. Des vérins hydrauliques appliquent des tonnes de pression pour fermer solidement les moitiés du noyau et de la cavité. Cela empêche le plastique fondu sous pression de fuir lorsqu'il est injecté à grande vitesse.
La pression de la pince doit vaincre les forces collectives qui tentent d'écarter les deux moitiés du moule pendant l'injection. Les barres d'attache augmentent la solidité entre les plateaux.
Étape 4 : Injection de l'acrylique
Une fois le moule solidement fixé, l'acrylique en fusion s'écoule du cylindre d'injection et se déverse dans la carotte. Le système de canaux dirige la résine chaude dans chaque crevasse de la cavité de l'outil pour remplir complètement l'espace vide.
Les presses à vis introduisent des granulés solides dans le cylindre et utilisent des chauffages électriques et de l'énergie mécanique pour liquéfier le plastique. La pression d'injection dépasse la pression de la cavité du moule, ce qui provoque une poussée vers l'avant.
Emballer et conserver
Pour éviter une solidification précoce, une plus grande quantité de résine est injectée après le remplissage de la cavité. Cela permet de tasser de l'acrylique fondu supplémentaire et d'appliquer une pression de maintien jusqu'à ce que la porte se fige.
Les pièces conservent leur forme et subissent moins de déformations grâce à cette étape de conditionnement secondaire. Elle laisse plus de temps à la résine chaude pour prendre sa forme définitive avant de refroidir les êtres.
Étape 5 : Refroidissement et durcissement
Après l'emballage, de l'eau réfrigérée circule dans les ports à l'intérieur de l'outil pour solidifier le plastique acrylique surchauffé. Le routage complexe des canaux cible stratégiquement les points chauds pour accélérer le refroidissement.
Les broches d'éjection s'étendent légèrement pour rétracter le plastique des surfaces du noyau. Cela empêche les pièces de coller une fois qu'elles sont prêtes à être poussées hors du moule.
Les temps de refroidissement varient en fonction de l'épaisseur de la paroi. Le plastique épais retient la chaleur plus longtemps que les sections transversales plus fines. Les moules les plus récents utilisent des canaux conformes pour accélérer le refroidissement et raccourcir les temps de cycle.
Étape 6 : Éjection des pièces en acrylique
Pour éjecter manuellement un composant acrylique durci :
- La force de serrage se relâche, ce qui permet de séparer les deux moitiés du moule d'injection.
- À l'aide de tiges de guidage, la plaque d'éjection avance vers l'avant pour pousser les pièces hors de la cavité de l'outil.
- Des bras robotisés ou des ouvriers saisissent les produits finis à l'extérieur de la presse à mouler.
Pour les formes plus simples avec des moules à tirage direct, les systèmes d'éjection automatique sont les plus efficaces. Ils dégagent instantanément les pièces de chaque face de l'outil sans nécessiter de travail manuel.
Étapes de finition supplémentaires
Après l'éjection de base, les pièces en acrylique subissent souvent des processus de post-moulage supplémentaires :
- Découper le surplus de plastique
- Poncer ou polir les marques de l'outil d'accouplement
- Polir les surfaces à la flamme et à la vapeur
- Appliquer des revêtements durs pour une meilleure protection
- Coller les assemblages par adhésif ou par soudage
Ce travail de finition améliore l'aspect cosmétique et prépare les composants acryliques pour l'expédition ou le processus de fabrication suivant.
Le processus de moulage par injection de l'acrylique se poursuit au fur et à mesure que les composants supplémentaires sont surmoulés, que les étiquettes adhèrent, que le matériel est monté et que les essais finaux valident la qualité de la pièce.
Applications du moulage par injection d'acrylique
Transparent ou coloré, le plastique acrylique offre une grande souplesse de production grâce aux techniques de moulage par injection. Examinons quelques applications courantes.
Phares et feux arrière automatiques
Les constructeurs automobiles moulent des phares et des feux arrière personnalisés en acrylique. Ce matériau résiste à des années d'abus de la route sans se dégrader sous l'effet de l'exposition aux UV.
Les phares comportent des réflecteurs complexes qui nécessitent des capacités de moulage par injection de précision. Le plastique acrylique crée également des lentilles optiques idéales pour diffuser les faisceaux lumineux là où c'est nécessaire.
Glace synthétique
Il est possible de mouler par injection des qualités spécialisées d'acrylique pour imiter l'apparence et les propriétés de frottement de la glace. Les patinoires synthétiques permettent de faire face au coût élevé du maintien de la glace traditionnelle à l'état solide.
Les sites de curling, de patinage artistique et de hockey restent opérationnels toute l'année grâce à l'acrylique injecté. Ce matériau convient également aux manifestations temporaires sur glace qui ne disposent pas d'une infrastructure de réfrigération permanente.
Écrans LCD
Les écrans plats s'appuient sur des fenêtres de visualisation en acrylique et des tubes optiques pour une clarté d'affichage éclatante. Les moulistes fabriquent avec précision un plastique ultra clair et sans défaut pour faire passer la lumière à travers les différentes couches de l'écran LCD.
Des techniciens qualifiés polissent les lignes de séparation moulées après le démoulage. Cette opération permet d'éliminer les imperfections avant de prendre en sandwich d'autres composants électroniques entre les vitres formées.
FAQ sur le processus de moulage par injection de l'acrylique
Voici les réponses aux questions les plus courantes concernant le processus de moulage par injection de l'acrylique :
Quelles sont les machines utilisées ?
Les presses à injection standard traitent thermiquement les composés acryliques pour les applications de moulage. Les machines vont des petites machines verticales aux plus grandes configurations horizontales avec des tonnes de force de serrage.
L'acrylique injecté fonctionne également avec des presses à injection de métal. Ces machines spécialisées acceptent des mélanges de métaux en poudre en plus des résines traditionnelles.
Pouvez-vous mouler par injection tous les types d'acrylique ?
Oui, les qualités telles que l'acrylique extrudé, l'acrylique coulé en cellule et l'acrylique coulé en continu sont toutes moulées par injection avec succès. Les fabricants adaptent les routines de refroidissement, les taux de remplissage, la température du moule et d'autres paramètres pour traiter les différentes formulations acryliques.
Pourquoi plastifier l'acrylique ?
Sous forme de granulés bruts, l'acrylique ne s'écoule pas et ne remplit pas les détails complexes des pièces. La plastification transforme la résine acrylique rigide en un fluide fluide. Cela permet une pénétration complète du moule avant que le refroidissement ne redonne à l'acrylique une forme solide.
En chauffant l'acrylique entre 240°C et 320°C, on fait fondre le matériau pour obtenir une viscosité d'injection adéquate. L'acrylique ne se décomposera pas chimiquement avant d'avoir dépassé 380°C, ce qui est bien supérieur aux températures de moulage standard.
Conclusion
Comprendre l'ensemble processus de moulage par injection de l'acrylique vous permet de planifier un lancement de produit qui utilise efficacement ce matériau plastique transparent.
Faire appel au bon partenaire de moulage par injection permet d'éviter les retards de fabrication et les erreurs d'itération coûteuses. Leur expérience fera la différence lors de la qualification du moule acrylique.