Le moulage par injection de plastique est un processus de fabrication complexe qui comporte de nombreuses variables. Pour produire des pièces de haute qualité, vous avez besoin d'un moule précis capable de produire des pièces cohérentes à plusieurs reprises. C'est là que l'analyse des flux entre en jeu.
L'analyse de l'écoulement du moule simule la manière dont le plastique fondu s'écoule dans le moule au cours du processus d'injection. Cette analyse prédictive permet de découvrir les défauts potentiels et les possibilités d'optimisation.avant couper n'importe quel acier.
Vous pouvez ainsi perfectionner la conception du moule, choisir la résine idéale, optimiser le système de canaux et équilibrer les taux de remplissage entre les cavités. Cela permet d'accélérer les temps de cycle, de réduire les taux de rebut et de passer en douceur à la production à grande échelle. En tant que professionnel fabricant de moulage par injection de matières plastiquesDans cet article, j'aborderai tous les aspects de l'analyse des flux pour le moulage par injection de plastique.
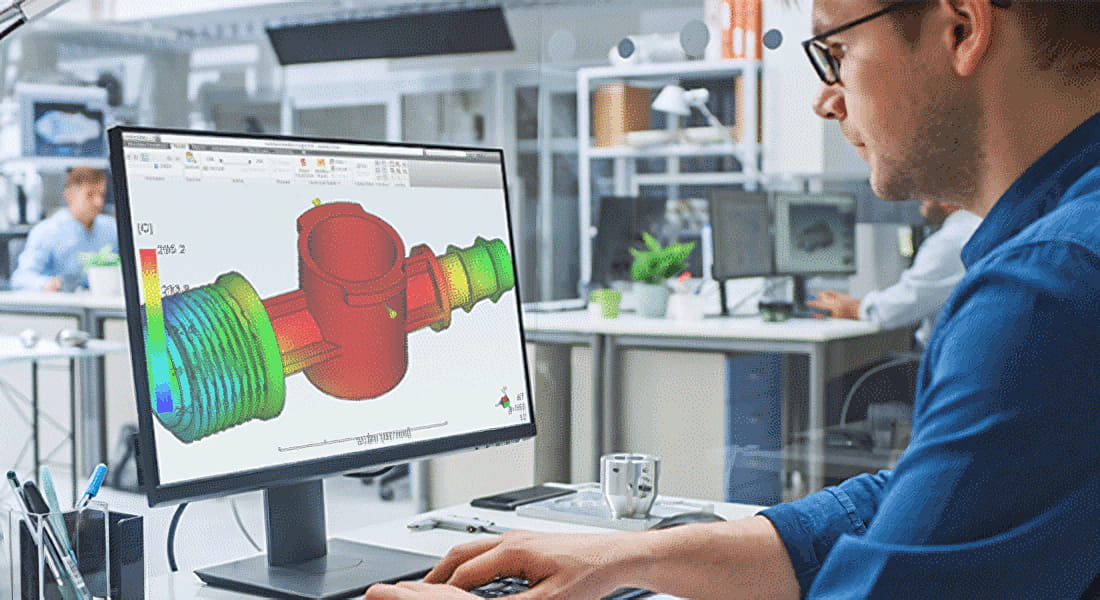
Comment fonctionne l'analyse de l'écoulement des moules ?
Le logiciel d'analyse de l'écoulement des moules importe vos CAD et reproduit numériquement le processus de moulage par injection. Des solveurs FEA spécialisés simulent l'écoulement de la résine dans le moule de refroidissement, en cartographiant des variables telles que la pression, la température, le taux de cisaillement, l'orientation des fibres, etc. dans l'espace et dans le temps.
Le logiciel produit des visualisations codées en couleur qui mettent en évidence les problèmes potentiels tels que les lignes de soudure, les pièges à air, les hésitations et les coups courts. En identifiant les problèmes à l'avance, les ingénieurs peuvent modifier la conception, la sélection des matériaux, les paramètres du processus et l'outillage avant même d'usiner une plaque.
Voici un aperçu général des avantages de la simulation :
Optimiser la conception des pièces
Les simulations FEED prédisent avec précision les défauts courants tels que le gauchissement, les marques d'enfoncement et les défauts de surface. En modifiant les géométries problématiques dès le début, vous pouvez optimiser la conception pour obtenir des performances de moulage.
L'analyse vérifie également les variations d'épaisseur des parois, détecte les angles de dépouille trop agressifs et valide les détails des inserts tels que les trous filetés, le texte et les embossages. Cela permet de réduire l'usure des outils et les opérations de post-moulage.
Choisir le meilleur matériau
Grâce à une base de données de plus de 6 000 matériaux, l'analyse permet de sélectionner la résine et la qualité optimales en fonction des exigences de performance et de moulabilité. Les compromis entre la facilité d'écoulement, le retrait et les propriétés mécaniques deviennent évidents.
Vous pouvez également connaître l'orientation des fibres de verre pour les polymères renforcés. L'orientation a un impact direct sur la résistance et peut être réglée à l'aide de guides de flux et de modifications de la géométrie.
Remplissage équilibré entre les cavités
La simulation de remplissage montre l'emplacement précis du front d'écoulement à des intervalles de temps déterminés, en identifiant le moment où chaque cavité se remplit. Les résultats révèlent les hésitations, les lignes de soudure et les pièges à air à éliminer.
L'équilibrage des systèmes de glissières et de la disposition des commandes garantit un remplissage simultané. Cela permet d'éviter le suremballage et de minimiser les besoins en force de serrage.
Optimiser les canaux de refroidissement
L'analyse fournit des tracés de température sur le cycle de moulage, quantifiant l'accumulation de chaleur interne et superficielle. Les ingénieurs optimisent alors l'emplacement de la ligne de refroidissement et le matériau utilisé pour éviter les points chauds et limiter les temps de cycle.
Valider les paramètres du processus
Enfin, l'analyse permet d'optimiser le temps de remplissage, la pression d'injection, la température de fusion et les profils d'emballage. Les fonctions automatisées de conception d'expériences (DOE) rationalisent l'optimisation.
Les 6 principaux avantages de la simulation de l'écoulement des moules
Au-delà d'une présentation générale, voici six avantages tangibles à faire de l'analyse de l'écoulement des moules un élément standard de votre processus de moulage par injection :
1. Réduire les itérations de fabrication
Les prototypes physiques entraînent des coûts et des délais importants. En simulant numériquement le processus de moulage, vous évitez des séries d'essais et d'erreurs dans la mise au point des outils.
Cela permet de réduire le temps de développement total de plusieurs semaines, voire de plusieurs mois. L'analyse des flux minimise les cycles de fabrication afin d'obtenir des outils robustes et à haut rendement dès la première fois.
2. Réduire les délais de mise sur le marché
Une mise sur le marché plus rapide des produits offre un avantage concurrentiel évident. L'accélération des calendriers de mise sur le marché dépend de l'efficacité du processus de développement des pièces en plastique.
L'analyse du flux des moules réduit le cycle conception → fabrication → test pour livrer plus rapidement des outils fiables. La suppression des conjectures permet d'éviter un cycle prolongé de construction, de moulage, d'essai des pièces, d'identification des problèmes et de répétition. Cet effet de cascade vous permet de réduire considérablement les délais de mise sur le marché.
3. Réduction des coûts de production
Les rebuts et les retouches réduisent les marges bénéficiaires. L'adaptation des outils et des processus en vue de réduire les défauts permet de réaliser d'importantes économies par pièce, qui se multiplient au fil de la production en série.
L'analyse des flux permet d'éviter de nombreux défauts courants et coûteux dans le domaine du moulage par injection, tels que les coups courts, les bavures, les marques d'enfoncement et le gauchissement. Cela permet d'améliorer la capacité du processus et de réduire les coûts de fabrication.
4. Garantir des rendements élevés
Un moule d'injection qui ne se remplit pas de manière régulière est source de graves problèmes. Si seule une partie des cavités se remplit à chaque cycle, vous gaspillez de la matière, de l'énergie et du temps à purger les mauvaises pièces.
L'analyse en amont permet d'égaliser les taux de remplissage sur l'ensemble de l'outil, ce qui garantit des cavités pleines et maximise le rendement de la production.
5. Mieux comprendre la conception
La simulation numérique offre une visibilité unique sur le processus de moulage, impossible à obtenir par la seule expérimentation. L'observation des fronts d'écoulement remplissant les cavités, le suivi des changements de température des matériaux et la visualisation de l'orientation des fibres permettent d'obtenir des informations précieuses sur la conception.
Les ingénieurs utilisent ces informations améliorées pour optimiser le dessin, le découpage, la mise en page et les performances des matériaux.
6. Évaluer les compromis de conception
Chaque décision de conception implique des compromis. Changer la résine, modifier l'épaisseur d'une paroi ou la géométrie entraîne de multiples répercussions sur les performances.
La simulation fournit les données permettant d'évaluer les compromis associés lors de la modification de la conception du moule, des conditions de traitement ou de la sélection des matériaux.
Quand faut-il procéder à une analyse des flux de moulage ?
Bien qu'il soit possible de mouler des pièces par injection sans analyse préalable, il est conseillé d'intégrer la simulation dès le début du processus de développement :
- Moules à cavités multiples
- Géométries complexes
- Spécifications à tolérances serrées
- Utilisation de nouvelles résines
En fait, il s'agit de simuler tout projet présentant des coûts élevés ou des incertitudes. L'identification à l'avance des défauts potentiels à l'aide de l'analyse du flux des moules permet d'atténuer les risques et d'économiser beaucoup de temps et d'argent.
À emporter
L'analyse du flux des moules offre une visibilité unique sur le processus de moulage par injection. La simulation avancée prédit avec précision la manière dont la résine s'écoulera dans les moules complexes, ce qui permet de détecter rapidement les défauts et de présenter des possibilités d'optimisation.
Cela permet de réduire les rebuts, de diminuer les exigences en matière de serrage, d'équilibrer le remplissage, de concevoir des outils robustes et, en fin de compte, de réduire les délais de mise sur le marché. Plutôt que de couper de l'acier et d'espérer le meilleur, la simulation fournit les données nécessaires à la conception de la qualité.
En intégrant l'analyse en amont et en validant numériquement la fabricabilité des pièces, vous rationalisez le développement, réduisez les coûts et accélérez la mise sur le marché de produits moulés par injection robustes.