Les lignes d'écoulement sont un défaut courant qui peut survenir au cours du processus de moulage par injection. Ces lignes visibles à la surface d'une pièce en plastique sont principalement d'ordre esthétique, mais elles peuvent néanmoins poser des problèmes. Quelles sont donc les causes exactes des lignes d'écoulement ?
Dans ce guide complet, en tant que professionnel fabricant de moulage par injectionDans cet article, j'aborderai les principaux facteurs qui contribuent aux lignes d'écoulement dans le moulage par injection. En comprenant ce qui se cache derrière ces défauts, vous pourrez prendre des mesures pour les éviter.
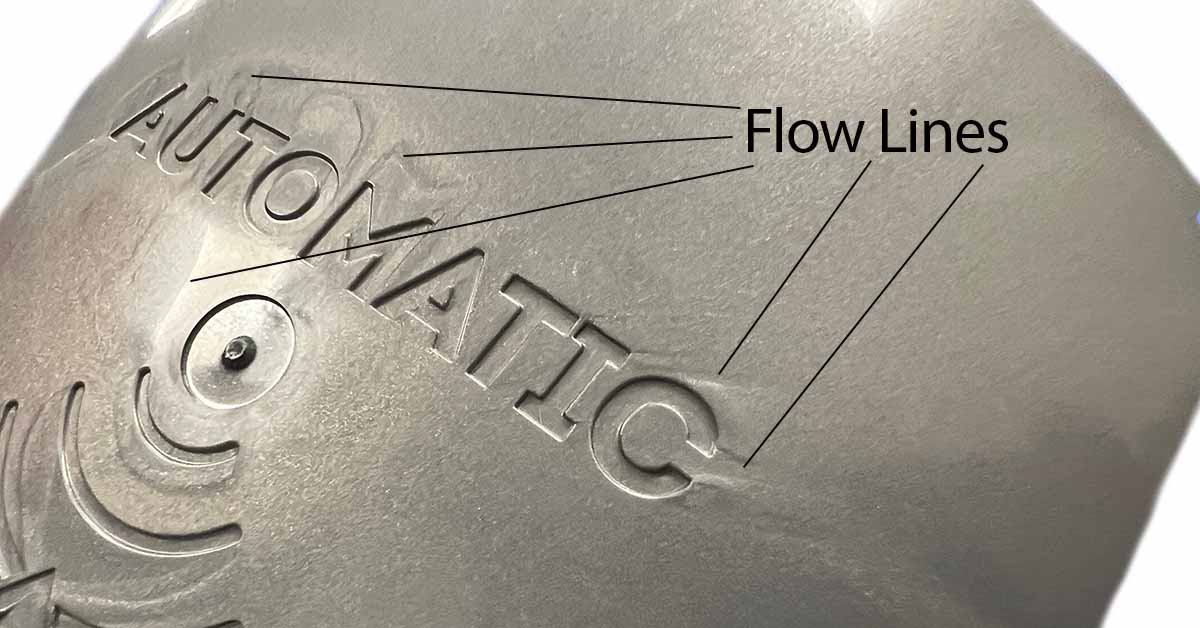
Que sont les lignes d'écoulement dans le moulage par injection ?
Avant de se pencher sur les causes, examinons brièvement ce que sont les conduites d'écoulement.
Les lignes d'écoulement apparaissent sur une pièce en plastique moulée par injection sous la forme de lignes, de stries ou de motifs visibles à la surface. Elles indiquent un écoulement irrégulier lorsque le plastique en fusion entre dans la cavité du moule et la remplit.
Souvent, les lignes d'écoulement se présentent comme suit :
- Lignes ondulées
- Répétition de motifs circulaires
- Traces décolorées sur la partie plastique
Bien que les lignes d'écoulement n'affectent pas directement la résistance ou la fonction de la pièce finie, elles constituent une imperfection. Pour les pièces visuelles soumises à des exigences esthétiques strictes, les lignes d'écoulement peuvent entraîner le rejet des pièces.
Dans l'ensemble, les lignes d'écoulement sont dues à des différences dans la manière dont les sections de plastique fondu se refroidissent et se solidifient dans le moule. Lorsque le refroidissement est inégal, des lignes visibles apparaissent à l'endroit où les flux se rejoignent.
Examinons maintenant les raisons pour lesquelles ce refroidissement et cet écoulement inégaux peuvent se produire pendant le moulage par injection.
Quelles sont les causes des lignes d'écoulement dans le moulage par injection ?
Il y a quatre catégories principales qui conduisent à la formation de lignes d'écoulement dans les pièces plastiques moulées :
- La machine de moulage par injection
- Le moule lui-même
- Le matériau plastique
- L'opérateur de la machine
Des problèmes dans l'un ou l'autre de ces domaines peuvent perturber la manière dont le plastique fondu s'écoule dans la cavité du moule. Lorsque l'écoulement est perturbé, certaines sections se refroidissent à des vitesses différentes, ce qui provoque des lignes d'écoulement.
Réglages et paramètres de la machine
La machine de moulage par injection elle-même joue un rôle important dans la fluidité et l'homogénéité de l'écoulement du plastique. Si l'un des paramètres clés n'est pas respecté, des lignes d'écoulement peuvent commencer à se former.
Faible pression d'injection - Si la pression n'est pas suffisante pour pousser le plastique fondu dans le moule, l'emballage et l'écoulement du matériau ne seront pas uniformes. Une faible pression permet aux sections du flux de se refroidir à des vitesses différentes.
Faible température de la buse - La buse transfère la chaleur dans le plastique juste avant qu'il n'entre dans le moule. S'il n'est pas assez chaud, les problèmes de refroidissement commencent immédiatement lorsque la matière fondue atteint le moule.
Vitesse d'injection lente - Une vitesse d'injection trop lente donne au plastique fondu plus de temps pour commencer à refroidir de manière non uniforme avant de remplir le moule. Cette variabilité de la température entraîne des problèmes d'écoulement.
Temps de cycle courts - Si le cycle global ou le temps de refroidissement est trop rapide, le plastique dans le tonneau risque de ne pas atteindre la température de fusion optimale avant d'être injecté.
Questions relatives à la conception des moules
Les défauts de conception des moules sont un autre facteur important de défaillance des lignes d'écoulement. Même de minuscules nuances telles que les évents, les vannes et la géométrie peuvent perturber l'écoulement :
Ventilation inadéquate - L'air emprisonné provoque des blocages et une résistance à l'écoulement. Lorsque les bouches d'aération ne remplissent pas correctement leur fonction, le remplissage et le refroidissement sont inégaux.
Petits portails/coulisses - Les vannes restreintes et les glissières minces entravent le flux, ce qui permet le refroidissement avant que le plastique n'atteigne les cavités du moule.
Géométrie complexe - Les arêtes vives ou les nervures agissent comme des barrières qui modifient radicalement la direction de l'écoulement. Les changements brusques favorisent un refroidissement non uniforme.
Epaisseur de paroi variable - Les sections minces se refroidissent plus rapidement que les sections épaisses. Lorsque le plastique fondu passe des zones épaisses aux sections minces, la différence de température entraîne des problèmes d'écoulement.
Facteurs matériels
Croyez-le ou non, la résine plastique elle-même peut également jouer un rôle dans la formation de la ligne d'écoulement :
Faible débit de matière fondue - Les matériaux très visqueux et à écoulement lent ont tendance à se refroidir à des intervalles différents. Cela provoque des lignes visibles là où les flux se rencontrent.
Manque de lubrifiant - Une quantité insuffisante de lubrifiant empêche l'écoulement des matières plastiques qui traversent des sections étroites plus longues. Une plus grande restriction permet des variations de refroidissement.
Influence de l'opérateur
Si les systèmes automatisés permettent de l'éviter, l'erreur humaine ne doit pas être sous-estimée :
Des temps de cycle incohérents - Si un opérateur ne parvient pas à maintenir la même séquence temporelle, des paramètres tels que la température fluctuent. Des conditions incohérentes d'un cycle à l'autre entraînent des problèmes de refroidissement.
Mauvais entretien - Le fait de ne pas éliminer les bavures ou les obstructions dans les composants du moule augmente la résistance à l'écoulement. Les accumulations contribuent à un remplissage et à un refroidissement inégaux.
Comment éviter les lignes d'écoulement dans les pièces moulées par injection ?
Heureusement, une fois que l'on sait à quoi s'attendre, il existe des moyens de lutter contre les lignes d'écoulement. Les modifications apportées aux machines, aux moules, aux matériaux et à la formation des opérateurs contribuent à réduire les risques de défauts d'écoulement.
Voici quelques exemples de moyens mis en œuvre par les fabricants de matières plastiques pour éviter les lignes d'écoulement :
- Optimiser la pression, la température et la vitesse d'injection
- Utiliser des systèmes d'évacuation des moisissures et des barrières appropriés
- Choisir des matières plastiques ayant des propriétés d'écoulement appropriées
- Conception d'une géométrie et d'une épaisseur de paroi uniformes
- Automatiser les réglages du processus et la durée du cycle
- Effectuer l'entretien préventif des moules
Bien qu'il soit difficile d'éliminer complètement les lignes d'écoulement, la première étape consiste à identifier pourquoi et où elles se produisent. L'ajustement de l'équipement et la vigilance permettent de réduire considérablement les défauts d'écoulement.
Une analyse minutieuse des réglages de la machine, de la viscosité du matériau, des composants du moule et le respect des procédures de qualité favorisent un écoulement fluide et régulier du plastique dans les moules d'injection. Cette régularité réduit les possibilités de refroidissement non uniforme des sections.
Le bilan
Les lignes d'écoulement se produisent lorsque la séquence complexe du moulage par injection est déséquilibrée. Comprendre les zones de problèmes potentiels permet de remettre les choses sur la bonne voie.
La bonne nouvelle, c'est que les conduites d'écoulement compromettent rarement la résistance des pièces si elles restent esthétiques. Mais en restant vigilant avec votre moulage par injection Le contrôle des processus et la conception des moules permettent d'éviter la mise au rebut de pièces en plastique coûteuses en raison de défauts essentiellement esthétiques.
Maintenant que vous savez pourquoi les perturbations du flux se produisent, vous pouvez vous concentrer sur les points faibles du système. En prenant des mesures stratégiques pour favoriser un écoulement uniforme du plastique, vous réduisez les risques de voir des sections refroidir à des vitesses différentes pendant le moulage par injection.
Quelle est votre expérience en matière de défauts de la ligne d'écoulement ? Vous avez d'autres conseils pour assurer la fluidité et la cohérence du flux de moulage par injection ? Faites-le moi savoir dans la section des commentaires ci-dessous !