Qu'est-ce qu'un portillon dans le moulage par injection ?
Une porte de moulage par injection est une petite ouverture qui permet au plastique fondu de pénétrer dans la cavité du moule au cours du processus de moulage par injection. Le portillon contrôle le flux et la direction du plastique lorsqu'il passe du système de coulée dans la cavité pour former la pièce souhaitée.
Il est essentiel de bien choisir et placer les portes pour obtenir un remplissage complet et uniforme du moule, minimiser les défauts et produire des pièces plastiques cohérentes et de haute qualité. Dans ce guide du débutant, en tant que professionnel, vous trouverez des informations sur la sélection et le placement des portes. fabricant de moulage par injectionJe vous expliquerai tout ce que vous devez savoir sur les vannes de moulage par injection, y compris les différents types de vannes, les considérations relatives à l'emplacement des vannes, le dégazage manuel ou automatique, et bien plus encore.
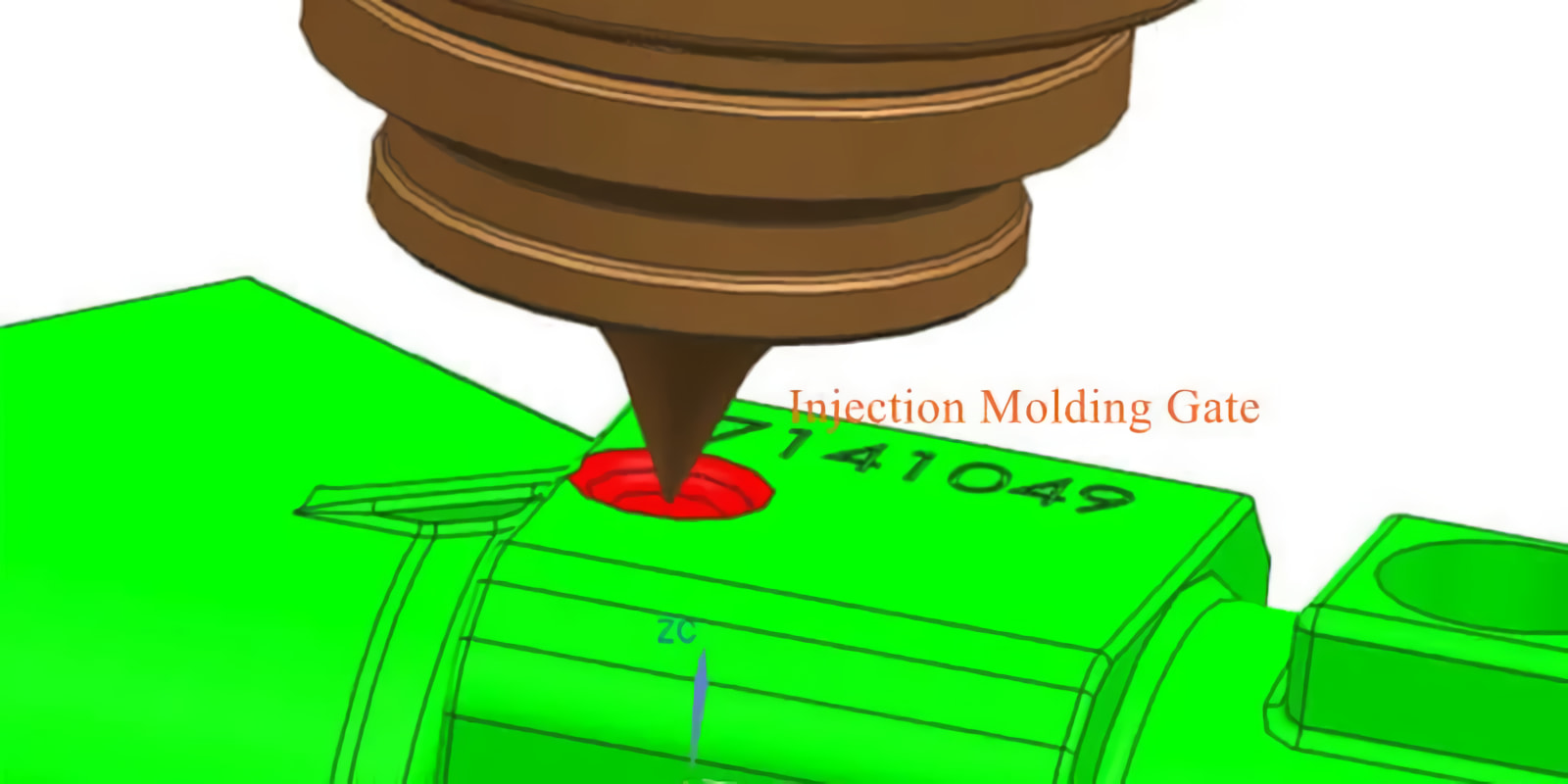
L'importance de la conception des portes dans le moulage par injection
Lorsque le plastique fondu pénètre dans la cavité du moule par la porte lors du moulage par injection, il commence à refroidir rapidement et à se solidifier pour prendre la forme du moule. La taille de l'opercule est généralement limitée pour faciliter la séparation du système de coulée de la pièce finie.
Cependant, si la porte est trop petite, elle peut causer de nombreux problèmes :
- Remplissage incomplet du moule - La porte ne permet pas un flux de matériau suffisant pour remplir complètement la cavité.
- Des temps de cycle plus longs - Des portes plus petites augmentent le cisaillement et frictionralentissant le taux de remplissage
- Défauts de pièces - Des taux de cisaillement élevés à travers la grille peuvent dégrader le matériau et produire des défauts.
Inversement, des portillons trop grands permettent au système de coulée de rester en fusion trop longtemps après la solidification de la pièce. Cela empêche la porte de geler, ce qui peut également entraîner des défauts.
La conception des vannes a un impact direct sur le processus de moulage par injection. Le choix de la bonne taille, de la bonne forme et du bon emplacement est crucial pour des temps de cycle rapides, des coûts réduits et des pièces de qualité.
Types de portes de moulage par injection
Il existe de nombreux types d'opercules utilisés dans le moulage par injection. Parmi les variétés d'obturateurs les plus courantes, citons
Portes de bordure
Les portillons de bord, le type de portillon le plus fréquemment utilisé, sont placés le long du périmètre d'une pièce au niveau de la ligne de séparation du moule. Ils laissent une marque visible mais permettent une séparation facile de la pièce après le moulage.
Meilleures utilisations : Les portes de bord fonctionnent bien pour les pièces plates ou modérément épaisses et sont couramment utilisées avec des moules à plusieurs cavités.
Portes Hot Tip
Utilisés exclusivement sur les moules à canaux chauds, les portillons à pointe chaude délivrent de la résine fondue directement sur la pièce à une température constante. Ils laissent un petit défaut en relief sur la surface supérieure des pièces.
Meilleures utilisations : Les pièces de forme ronde, bombée ou conique bénéficient du modèle de remplissage concentrique d'un portillon à pointe chaude.
Portes à goupilles
Variété peu commune d'obturateurs situés du côté de la broche d'éjection du moule (à l'opposé du plan de joint). Les portillons se cisaillent proprement, ne laissant pratiquement aucun vestige sur la surface de la pièce finie.
Meilleures utilisations : Les portillons à broches permettent un dégraissage automatique tout en éliminant les marques de portillon sur les surfaces cosmétiques.
Portes sous-marines (tunnels)
Dotés d'un canal angulaire et conique, les portillons sous-marins remplissent la cavité du moule par le dessous du plan de joint, ce qui permet de dissimuler les marques de portillon.
Meilleures utilisations : Les portes sous-marines permettent de masquer les imperfections de la porte et sont utiles pour les petits moules à forte cavitation.
Où doivent se situer les barrières ?
Bien que les types de portillons diffèrent considérablement, leur emplacement est également important pour la fabrication de composants moulés par injection.
Voici quelques bonnes pratiques que tous les concepteurs de moules devraient suivre :
- Dans la mesure du possible, placer le portillon dans la partie la plus épaisse de la pièce.
- Tenir les portes éloignées des broches d'éjection, des noyaux et des glissières afin d'éviter les interruptions de flux.
- Prévoir un espace suffisant pour les opérations d'enlèvement de la porte
- Utiliser plusieurs vannes pour améliorer l'équilibre des flux et des pressions
Un mauvais positionnement des portes peut avoir un impact négatif sur la qualité des pièces, allonger les temps de cycle et augmenter les coûts de production. L'emplacement judicieux des portes est un aspect essentiel de la conception d'un moule.
Retrait manuel ou automatique des barrières
Comme nous l'avons vu précédemment, les portillons doivent être retirés des pièces plastiques finies après le moulage par injection. Ce processus secondaire est connu sous le nom de dégainage.
Les opérations de dégraissage entrent généralement dans l'une des deux catégories suivantes :
Dégradation manuelle
Forme la plus élémentaire d'enlèvement d'une porte, le dégraissage manuel repose sur un opérateur qui coupe, rogne, brise ou tord les portes des pièces moulées. Bien qu'universelle, cette méthode augmente les coûts de main-d'œuvre et peut endommager des composants fragiles.
Meilleur pour : Prototypage, outillage de pont, grandes portes, ou exigences personnalisées en matière d'habillage
Dégradation automatique
Pour les applications à forte production, le dégainage automatique détache les portes pendant l'ouverture du moule ou l'éjection de la pièce. Les robots manipulent ensuite les pièces finies pour les opérations en aval. La suppression de l'intervention humaine permet d'accélérer les cycles et de réduire les coûts.
Meilleur pour : Production en grande quantité, moules à cavités multiples, petites portes
Comprendre comment les portes seront retirées permet d'optimiser la conception des moules et des pièces. Le choix entre dégazage manuel et dégazage automatique influe sur l'efficacité du cycle, les besoins en main-d'œuvre et la qualité globale des pièces.
Conclusion
Nous espérons que ce guide du débutant vous a permis d'acquérir de solides connaissances de base sur les portes de moulage par injection.
Récapitulons rapidement :
- Les vannes contrôlent l'écoulement du plastique fondu des glissières dans les cavités du moule.
- Le dimensionnement correct de la porte permet d'éviter les coups courts tout en permettant un remplissage complet de la cavité.
- Parmi les variétés de vannes les plus courantes, on peut citer : les vannes de bord, les vannes à pointe chaude, les vannes à broche et les vannes sous-marines.
- L'emplacement de la porte influe sur les schémas de remplissage, l'efficacité du cycle, la cosmétique
- Le dégraissage des pièces peut être effectué manuellement ou automatiquement, avec des compromis pour chaque méthode.
Armé de ces connaissances, vous pouvez faire des choix éclairés pour votre prochain composant moulé par injection ou votre prochaine conception de moule. Comme toujours, le fait de s'appuyer sur un partenaire de fabrication expérimenté permet d'éviter les faux pas lors de l'utilisation de ce processus précis.
Quel aspect de la conception des portails n'est pas encore clair ? Faites-moi part de vos commentaires dans la section ci-dessous !