Les marques d'évier sont un défaut courant du moulage par injection qui entraîne des surfaces inégales et une esthétique médiocre. En tant que professionnel fabricant de moulage par injection de matières plastiquesJ'ai travaillé avec des fabricants qui se sont heurtés à des problèmes d'évidement. En optimisant la sélection des matériaux, les paramètres du processus, la conception de l'outillage et la géométrie des pièces, vous pouvez éviter complètement les coulures.
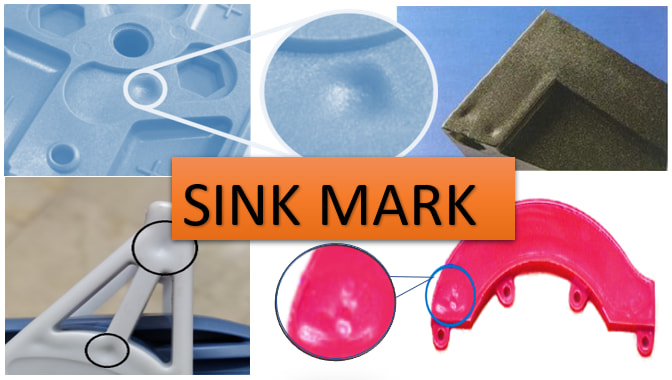
Quelles sont les causes des marques de coulure dans le moulage par injection ?
Avant de se pencher sur les solutions, il est important de se pencher sur les causes des marques d'évier. Comment éviter les marques d'enfoncement dans le moulage par injection ? Les retombées se produisent lorsque les sections épaisses refroidissent plus lentement que les sections fines. En se contractant, le plastique chaud des parties plus épaisses s'éloigne de la couche extérieure rigide en contact avec la surface du moule. Cette contraction forme une dépression visible sur l'extérieur de la pièce, connue sous le nom de marque d'enfoncement.
Plusieurs facteurs contribuent au refroidissement différentiel et à la formation de puits :
Pression d'emballage insuffisante
Si la pression de tassement n'est pas suffisante, le plastique chaud ne peut pas tasser complètement les éléments épais. Le matériau se rétracte en refroidissant, au lieu de rester poussé contre le moule. L'augmentation de la pression de tassement entraîne une plus grande quantité de résine dans les sections épaisses afin d'éviter les vides.
Basses températures de fusion
Si la température de fusion du plastique est trop basse, les zones épaisses résisteront à l'écoulement et auront plus de difficultés à se remplir. L'augmentation de la température améliore l'écoulement, de sorte que toutes les zones peuvent être remplies. Bien entendu, les températures ne doivent pas dépasser les limites de dégradation, ni même s'en approcher.
Géométrie épaisse
Naturellement, les sections plus épaisses se refroidissent plus lentement car elles retiennent la chaleur plus longtemps que les parois minces. En optimisant la conception des pièces, vous pouvez éliminer les variations drastiques d'épaisseur et favoriser une solidification homogène.
Mauvaise ventilation
L'air emprisonné provoque un remplissage inégal car le matériau se déplace dans les poches au lieu de remplir entièrement les sections. Une ventilation efficace donne à l'air un endroit où aller pour que la résine puisse se remplir entièrement.
Questions relatives à l'emplacement et à la taille des barrières
Une porte mal placée restreint le flux vers les parties les plus éloignées de la cavité. Les petites portes limitent également le flux de matériau, ce qui peut laisser des zones épaisses partiellement remplies.
Comment éviter les marques de coulure lors du moulage par injection
Maintenant que nous comprenons ce qui cause les marques d'enfoncement, explorons les moyens éprouvés de les éviter en modifiant les matériaux, les paramètres du processus, l'outillage et la géométrie de la pièce.
Choisir des matériaux à faible retrait
Comment éviter les marques d'enfoncement dans le moulage par injection ? Commencez par sélectionner une résine plastique présentant des propriétés de rétrécissement minimales. Les résines amorphes telles que ABSLe PMMA et le SAN rétrécissent moins que les matériaux semi-cristallins. Lorsque la résistance le permet, les plastiques amorphes permettent d'éviter les retassures dès le départ. Au-delà du type de résine, les matériaux chargés de verre rétrécissent beaucoup moins que les variétés non chargées.
Optimiser les paramètres du processus
Pendant le moulage, l'ajustement des paramètres clés permet d'éloigner le processus des puits :
- Température : Vérifier que les températures de la cuve et du moule sont conformes aux recommandations pour la résine. Augmenter la température du tonneau pour améliorer l'écoulement dans les sections épaisses. Baisser la température du moule pour accélérer le refroidissement.
- Pression : Augmenter la pression d'emballage pour forcer le matériau supplémentaire dans les sections lourdes, en compensant le rétrécissement. Prolonger le temps d'emballage pour permettre un emballage complet.
- Refroidissement : Allonger les intervalles de refroidissement avant l'éjection afin d'éviter un retrait prématuré lorsque les sections internes restent chaudes.
Améliorer la conception des outils
Des modifications subtiles des composants de l'outillage ont un impact significatif sur la formation de l'enfoncement :
- Ventilation : Ajoutez des évents pour que l'air puisse s'échapper au fur et à mesure que le matériau s'écoule. Cela permet d'éviter que l'air ne soit emprisonné et que le remplissage ne soit pas uniforme.
- Lignes de refroidissement : Un refroidissement supplémentaire à proximité des zones d'évier attendues évacue la chaleur afin d'éviter que le matériau ne reste chaud. Favorise un refroidissement uniforme.
- Portes : Rediriger les portes vers les zones plus épaisses afin que le flux soit direct. Il peut être nécessaire d'ajouter des vannes à une pièce à plusieurs vannes.
Optimiser la géométrie des pièces
Enfin, il convient d'adapter la conception des pièces afin de minimiser les pertes :
Comment éviter les marques d'enfoncement dans le moulage par injection ?
- Éliminer les changements et les variations drastiques d'épaisseur. Maintenir les murs à peu près de même épaisseur.
- Ajoutez progressivement de l'épaisseur avec des angles ébauchés plutôt qu'avec des coins/projections tranchants.
- Réduire les éléments épais tels que les nervures et les goussets. Ne pas dépasser une épaisseur de 50-60% de la paroi.
- Le carottage des sections lourdes permet d'éliminer la masse et d'éviter un rétrécissement important.
Conclusion
Si l'on n'y prend pas garde, les marques d'enfoncement nuisent à l'aspect et aux performances de la pièce. En examinant les causes profondes, nous pouvons nous attaquer aux coulures de moulage par injection en sélectionnant intelligemment les matériaux, en optimisant les paramètres du processus, en améliorant l'outillage et en repensant la conception des pièces. L'idéal est de s'y intéresser dès le stade de la conception afin d'éviter les maux de tête liés à l'ajustement des pièces et des moules après coup. En faisant preuve de diligence sur ces fronts, vous pouvez éliminer les défauts d'enfoncement de l'équation.
Comment éviter les marques d'enfoncement dans le moulage par injection ? Un contrôle minutieux des matériaux, des paramètres de moulage, des facteurs d'outillage et de la géométrie permet d'éviter les coulures et d'obtenir des produits finis sans défaut et résistants. Quelles stratégies avez-vous utilisées pour lutter avec succès contre les marques d'enfoncement ? Vos commentaires sont les bienvenus !