Les défauts d'ébrasement peuvent sérieusement compromettre la qualité des pièces moulées par injection. Ces stries et décolorations de la surface nuisent non seulement à l'esthétique, mais compromettent également la résistance. Comment se débarrasser de l'évasement dans le moulage par injection ?
En tant que professionnel fabricant de moulage par injection de matières plastiquesJ'ai moi-même lutté contre les défauts d'évasement. Et je peux vous dire que, même si c'est délicat, il est possible d'éliminer l'évasement grâce à un dépannage approprié et à des ajustements de processus.
Dans ce guide complet, je vous présenterai les différentes causes de l'évasement et des solutions éprouvées pour l'éliminer définitivement.
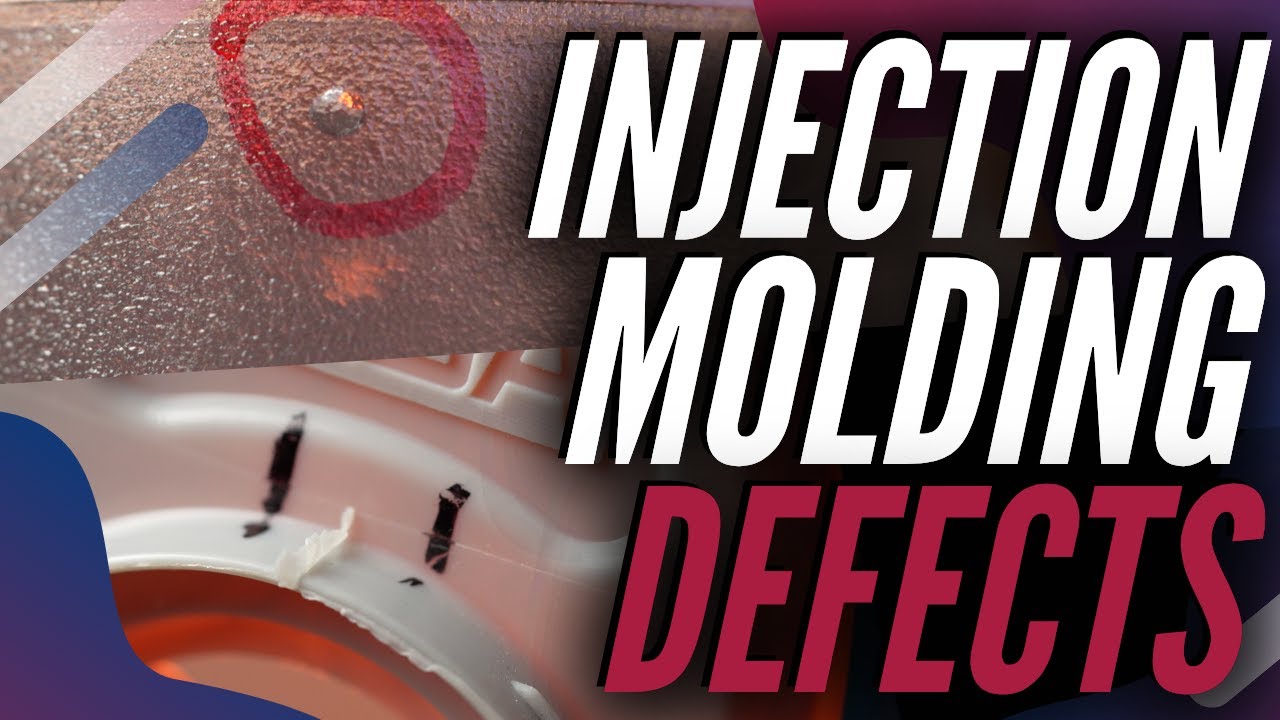
Quelles sont les causes de l'évasement dans le moulage par injection ?
Avant de se lancer dans la recherche de solutions, il est important de comprendre ce qui se cache derrière ces traces argentées gênantes.
Les défauts d'évasement se produisent lorsque de minuscules bulles de gaz sont entraînées le long de la surface au fur et à mesure que la cavité du moule se remplit. Le plus souvent, l'humidité absorbée par la résine plastique est à l'origine de l'évasement.
Lorsque les granulés sont chauffés dans le tonneau, cette humidité se transforme en vapeur. Les bulles de vapeur migrent vers la surface lorsque le moule se remplit, ce qui provoque ces défauts striés.
Outre l'humidité, l'évasement peut également être dû à.. :
Causes liées à la chaleur
Des températures excessives du canon peuvent surchauffer le plastique, libérant des gaz qui provoquent un évasement. Une contre-pression trop élevée peut également entraîner une surchauffe.
Les temps de séjour prolongés dans la vis sont un autre coupable, la matière restant trop longtemps dans le tonneau avant d'être remplie.
Causes liées au cisaillement
Les vitesses de rotation élevées des vis génèrent une chaleur de cisaillement qui dégrade le plastique en gaz. Les petites portes peuvent également provoquer un cisaillement.
Les obstructions de la porte, comme les bavures de l'extrémité de la buse, perturbent le flux, tout comme les détails internes du moule, tels que les angles aigus.
Contamination
Le plastique broyé ou d'autres contaminants introduisent des éléments volatils ou de l'humidité dans la résine.
Questions matérielles
Les matériaux hygroscopiques tels que Nylon et PC absorbent facilement l'humidité ambiante. Un séchage insuffisant transforme l'eau en vapeur.
L'utilisation excessive d'agents gonflants ou d'additifs chargés d'humidité peut également libérer des gaz.
Par conséquent, toute source de contamination, de substances volatiles ou de gaz dans la résine ou le moule peut être libérée sous forme de bulles qui marquent la surface, c'est-à-dire qu'elles s'étalent.
Comment se débarrasser de l'évasement dans le moulage par injection
Maintenant que vous savez ce qui se cache derrière ces traînées argentées gênantes, passons à l'élimination des défauts d'éjection de vos composants moulés par injection.
Étape 1 : Inspecter les pièces pour détecter les modèles de défauts
Dans un premier temps, vérifiez soigneusement si vos pièces moulées présentent les caractéristiques suivantes des motifs dans les défauts de l'ébrasement.
- Si les marques apparaissent de manière aléatoire sur l'ensemble du territoire, l'humidité est probablement le coupable.
- Les défauts se situent principalement au niveau des points d'entrée cisaillement.
- Des marques constantes indiquent une à base de moule problème d'écoulement du lubrifiant dans les poussoirs.
Il convient donc d'être très attentif à la manière et à l'endroit exacts où l'éjection se manifeste avant de se lancer dans la recherche de solutions. Le modèle de défaut guidera les solutions appropriées.
Étape 2 : S'attaquer aux causes liées à l'humidité
L'humidité étant la cause la plus fréquente de l'évasement, nous allons suivre un processus systématique pour y remédier :
A. Vérifier les matériaux hygroscopiques
Examinez les types de matériaux et les fiches techniques pour voir si des résines sont hygroscopiques, comme le nylon ou le PC. Même de petites quantités d'humidité dans ces matériaux peuvent provoquer un évasement important.
B. Vérifier la température et le temps de séchage
Vérifier la température et la durée de séchage par rapport aux recommandations du fournisseur de résine. Par exemple, les nylons ont besoin de 8 heures à 180°F. Ne faites aucune supposition.
C. Inspecter les sécheurs
Vérifier physiquement que les conduites d'alimentation en air sont chaudes et que les retours d'air sont chauds. Utilisez des sondes pour confirmer que les températures correspondent aux points de consigne. Des sécheurs défectueux sont synonymes de plastique mouillé !
D. Ajuster les débits
Si l'on utilise des séchoirs de taille insuffisante, les matériaux risquent de ne pas passer suffisamment de temps à l'intérieur pour sécher complètement. Augmenter le temps de séchage en réduisant le débit.
E. Chargeurs de drains
L'humidité peut se réabsorber dans le plastique refroidi qui repose dans les chargeurs. Il faut toujours égoutter les portions initiales avant le moulage à partir d'une charge de séchoir donnée.
Suivez cette méthodologie pour exclure ou traiter systématiquement les causes liées à l'humidité. Cette méthode permet de résoudre la plupart des problèmes d'évasement.
Étape 3 : S'attaquer à l'évasement dû à la chaleur
Si l'humidité n'est définitivement pas en cause, une chaleur excessive est le prochain suspect probable. Voici comment résoudre les problèmes d'évasement thermique :
A. Comparer les temps de fonte
Vérifier les températures de fusion enregistrées par rapport aux directives du fournisseur de matériaux. Si elle est trop élevée, abaisser progressivement la température du tonneau et tester à nouveau les pièces.
B. Réduire les pressions dorsales
Une contre-pression excessive risque de provoquer une surchauffe et une dégradation des résines. Diminuer progressivement la contre-pression jusqu'à l'élimination de l'évasement.
C. Températures inférieures de la zone d'alimentation
Des zones d'alimentation plus froides réduisent le temps de séjour de la résine dans le tonneau chaud, minimisant ainsi la dégradation due à une exposition prolongée à la chaleur.
D. Récupération des vis à retardement
Si les temps de refroidissement sont longs, retardez la rotation de la vis pour terminer la récupération juste avant l'ouverture du moule. Cela permet d'éviter la surchauffe des résidus.
En s'attaquant méthodiquement aux facteurs liés à la chaleur, on résoudra de nombreux problèmes d'évasement qui subsistent.
Étape 4 : Traiter les causes liées au cisaillement
Si le chauffage et l'humidité ne sont pas des facteurs déterminants, il est probable que le cisaillement de la chaleur soit à l'origine des difficultés de la série d'argent. Voici quelques conseils pour contrer le cisaillement :
A. Vis inférieure RPM
Les vitesses de vis élevées génèrent une chaleur de cisaillement excessive qui dégrade le plastique. Diminuer progressivement la vitesse de rotation jusqu'à ce que l'évasement disparaisse.
B. Élargissement des portails
Les vannes sous-dimensionnées provoquent un cisaillement du matériau. Élargir les vannes ou utiliser des vannes à ventilateur pour minimiser l'échauffement par cisaillement.
C. Injection lente
Le moyen le plus rapide de résoudre le problème du cisaillement de la grille est de ralentir la vitesse d'injection. Cela donne à la résine plus de temps pour s'écouler.
D. Éliminer les obstacles
Vérifier que les embouts des buses et les canaux de ventilation des moules ne présentent pas de débris ou de bavures susceptibles de perturber l'écoulement de la matière fondue.
En dernier recours, le traitement des causes de cisaillement doit permettre de remédier aux défauts d'ébrasement résiduels qui n'ont pas été résolus par d'autres solutions.
Étape 5 : Traiter les facteurs de contamination
Si l'évasement persiste après avoir traité les problèmes de chaleur, d'humidité et de cisaillement, la contamination peut être le coupable sournois. Voici comment s'attaquer au plastique et aux moules contaminés :
A. Éliminer le rebroyage
Si du plastique rebroyé ou recyclé est utilisé, il faut le purger et l'exclure à des fins d'essai. Les contaminants présents dans la résine réutilisée sont souvent à l'origine de l'évasement.
B. Augmenter la purge
Purger abondamment avec des composés spéciaux pour nettoyer complètement la vis, le canon, la buse et les canaux chauds des débris ou des huiles, cires et contaminants accumulés.
C. Nettoyer les moules
Démonter les moules et nettoyer méticuleusement toute accumulation de lubrifiants, d'antirouille ou d'autres matières étrangères sur les surfaces des cavités à l'aide de solvants appropriés.
Le traitement approfondi de la contamination ne laisse aucune place à l'oubli dans votre lutte contre les parasites.
Conclusion
Et voilà, une feuille de route complète pour traiter de manière décisive ces défauts d'ébrasement !
L'essentiel est de travailler méthodiquement sur les facteurs les plus probables, en commençant par les problèmes d'humidité les plus courants et en abordant progressivement la chaleur, le cisaillement et la contamination.
Bien que cela puisse sembler décourageant, une attention et un dévouement appropriés à chaque étape produiront en fin de compte d'énormes dividendes sous la forme de surfaces magnifiques et sans éraflures. Grâce à ce plan de bataille, vous n'aurez plus à vous soucier des traces d'argent.
Les connaissances permettant non seulement de s'attaquer aux défauts, mais aussi de les prévenir à l'avenir, sont ce qui transforme les mouleurs par injection de techniciens en véritables experts. J'espère que ce guide vous a permis d'ajouter une arme supplémentaire à votre arsenal de qualité des processus !
Maintenant, allez de l'avant et ne craignez pas les ennemis de l'évasion ! Vos pièces attendent d'être à nouveau impeccables et parfaites.