Want to know how to make a plastic cap?
You’re looking at a massive industry. Millions of plastic caps are manufactured every single day across the globe.
And here’s the deal:
The process is more complex than most people realize. But once you understand the fundamentals, it all makes sense.
In this guide, as a professional custom plastic cap manufacturer, I’ll break down everything you need to know about plastic cap manufacturing. From the materials and methods to quality control and finishing touches.
Plongeons dans le vif du sujet.
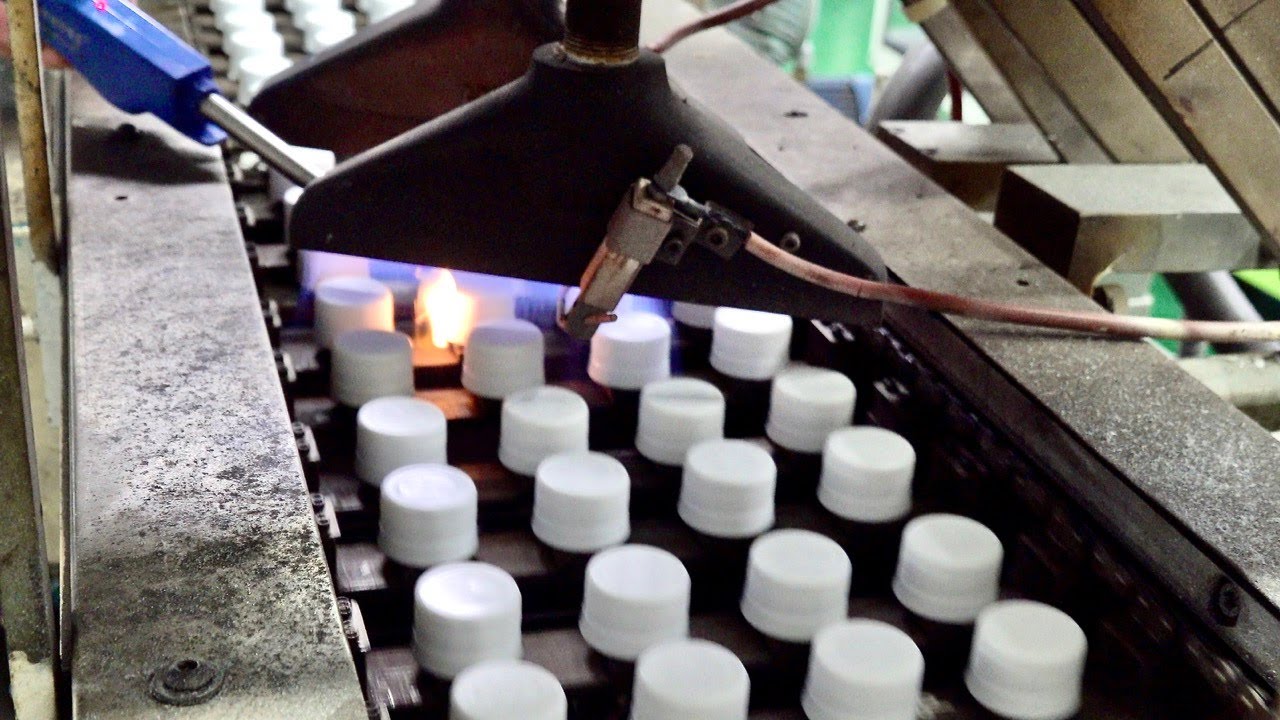
What You’ll Learn in This Guide
Before we get into the nitty-gritty, here’s what I’ll cover:
- The two main manufacturing methods (injection molding and compression molding)
- Which plastics work best for bottle caps
- Step-by-step manufacturing process
- Quality control essentials
- Considérations relatives aux coûts
- DIY alternatives for small-scale production
Sound good? Let’s start with the basics.
The Two Main Methods for Manufacturing Plastic Caps
When it comes to making plastic bottle caps, manufacturers use two primary methods:
- Moulage par injection
- Compression molding
Most modern facilities use injection molding. Why? It’s faster, more precise, and perfect for high-volume production.
But compression molding still has its place, especially for specific cap types.
Let me break down each method.
Injection Molding: The Industry Standard
Injection molding dominates the plastic cap industry. And for good reason.
Here’s how it works:
First, plastic pellets get heated in a barrel until they melt. Then, this molten plastic gets injected into a mold cavity under extreme pressure.
The mold shape determines your final cap design. Cool the mold, and boom – you’ve got a finished cap.
The entire process takes seconds. That’s why manufacturers can produce thousands of caps per hour.
But here’s what makes injection molding special:
Précision. You can create complex thread designs and tamper-evident features with incredible accuracy.
Repeatability. Every cap comes out virtually identical. No variations in dimension, shape, or finish.
Cost efficiency. Once you’ve invested in the molds, the per-unit cost drops dramatically.
Compression Molding: The Alternative Approach
Compression molding works differently.
Instead of injecting molten plastic, you place a pre-measured amount of material directly into an open mold. Then you apply heat and pressure to form the cap.
This method works great for:
- Thermoset plastics
- Caps with unique material requirements
- Lower volume production runs
The downside? It’s slower than injection molding. And achieving consistent thread quality can be challenging.
Material Selection: Choosing the Right Plastic
Not all plastics are created equal. Especially when it comes to bottle caps.
The most common materials include:
PEHD (polyéthylène haute densité)
HDPE is the workhorse of the cap industry. You’ll find it on milk jugs, detergent bottles, and countless other containers.
Why HDPE rocks:
- Excellente résistance chimique
- Durable and impact-resistant
- Fully recyclable
- Rentabilité
The only downside? HDPE caps can be too soft for some applications.
Polypropylène (PP)
PP takes things up a notch. It’s harder than HDPE, making it perfect for caps that need extra durability.
You’ll see PP caps on:
- Soda bottles
- Medicine containers
- Emballage alimentaire
Pro tip: PP works especially well when you need caps that can withstand repeated opening and closing.
LDPE (Low-Density Polyethylene)
LDPE brings flexibility to the table. It’s softer than both HDPE and PP.
This makes it ideal for:
- Squeeze bottle caps
- Dispensing closures
- Caps that need to flex without breaking
PET (Polyethylene Terephthalate)
PET isn’t as common for caps, but it has its place. It’s crystal clear and incredibly strong.
Perfect for:
- Premium packaging
- Caps where appearance matters
- Applications requiring transparency
How to Make a Plastic Cap: Step-by-Step Process
Now let’s walk through exactly how plastic caps are made using injection molding.
Step 1: Material Preparation
Everything starts with plastic pellets. These tiny beads of plastic arrive at the factory in massive bags or containers.
Mais voilà :
The pellets need to be absolutely dry. Even tiny amounts of moisture can ruin the final product.
Manufacturers use specialized dryers to remove every trace of water. This process can take 2-4 hours depending on the material.
Step 2: Melting and Injection
Next, the dried pellets enter the injection molding machine’s hopper.
A rotating screw pushes them forward while heating elements melt the plastic. The temperature varies by material:
- HDPE: 180-220°C
- PP: 200-250°C
- LDPE: 160-200°C
Once melted, the plastic gets injected into the mold under pressures reaching 20,000 PSI.
That’s serious pressure. It ensures the plastic fills every tiny detail of the mold, including those crucial screw threads.
Step 3: Cooling and Solidification
This is where patience pays off.
The mold contains cooling channels filled with water or oil. These channels maintain precise temperatures while the plastic solidifies.
Cooling time depends on:
- Cap thickness
- Material type
- Température du moule
Typical cooling times range from 10-30 seconds.
Step 4: Ejection and Finishing
Once cooled, the mold opens and ejector pins push out the finished caps.
But we’re not done yet.
Many caps fall from the mold still connected to runners (the channels that delivered the molten plastic). These need to be trimmed.
Some caps also require additional finishing:
- Printing or embossing
- Liner insertion
- Assembly of multi-part closures
Thread Design: The Secret to a Perfect Seal
Voici une chose dont la plupart des gens ne se rendent pas compte :
Thread design makes or breaks a bottle cap.
The threads need to match perfectly between the cap and bottle neck. Too loose? Your product leaks. Too tight? Consumers can’t open it.
Thread specifications follow ASTM D2911 standards. This includes:
- Thread pitch (distance between threads)
- Thread depth
- Number of thread starts
- Thread profile angle
Most bottle caps use continuous thread (CT) designs. The designation looks like this: “28-410”
Où ?
- 28 = neck diameter in millimeters
- 410 = thread configuration
Getting this right requires precision tooling and careful mold design.
Quality Control: Ensuring Every Cap Meets Standards
Quality control in cap manufacturing isn’t optional. It’s essential.
Here’s what manufacturers check:
Précision dimensionnelle
Every measurement matters. Quality teams use precision instruments to verify:
- Overall diameter
- Height
- Thread dimensions
- Wall thickness
Even tiny variations can cause problems down the line.
Leak Testing
Nobody wants a leaky bottle. That’s why caps undergo rigorous leak testing.
Common methods include:
- Pressure testing
- Vacuum testing
- Dye penetration tests
Material Testing
Manufacturers regularly test material properties:
- Tensile strength
- Impact resistance
- Chemical compatibility
- UV resistance
Visual Inspection
Automated vision systems check for:
- Color consistency
- Surface defects
- Contamination
- Proper forming
Mold Design: Where Engineering Meets Art
The mold is where the magic happens. And designing one requires serious engineering chops.
Modern cap molds feature:
- Multiple cavities (8-96 caps per cycle)
- Specialized core designs for threads
- Hot runner systems for efficiency
- Precise cooling channels
Here’s the kicker:
A single mold can cost $50,000 to $500,000. But it’ll produce millions of caps over its lifetime.
For threaded caps, the mold design gets extra complex. Some caps simply strip off the core. Others require unscrewing mechanisms that rotate the cap off the threads.
Considérations sur les coûts
Parlons argent.
The cost to manufacture plastic caps depends on several factors:
Material costs: Raw plastic pellets typically run $0.50-$2.00 per pound. A pound might produce 100-500 caps depending on size.
Mold investment: As mentioned, molds are expensive. But spread that cost over millions of caps, and it becomes manageable.
Temps machine: Injection molding machines range from $50-$500 per hour to operate.
Travail: Modern facilities are highly automated, keeping labor costs low.
Volume: This is the big one. High volumes dramatically reduce per-unit costs.
Bottom line? At scale, plastic caps can cost just pennies to produce.
Embossing and Customization
Want your brand on every cap? Embossing makes it happen.
The beauty of injection molding? You can add incredible detail directly to the mold. No secondary operations needed.
Common embossing includes:
- Company logos
- Opening instructions
- Recycling symbols
- Date codes
Pro tip: Embossed features last forever. Unlike printed labels that wear off, embossing is permanent.
Environmental Considerations
Here’s something the industry is working hard to improve:
Sustainability.
Most plastic caps are recyclable. But they often use different plastics than the bottles they seal. This complicates recycling.
The solution? Design for recycling from the start:
- Use compatible materials
- Make caps that stay attached after opening
- Clearly mark recycling codes
- Minimize material usage
Some manufacturers now use recycled plastics in their caps. It’s a growing trend that helps close the loop.
DIY and Small-Scale Alternatives
What if you need just a few caps? Industrial injection molding doesn’t make sense.
Here are some alternatives:
Impression 3D: Great for prototypes and small batches. Modern printers can create functional caps with decent thread quality.
Silicone Molding: Create your own molds and cast caps using two-part resins.
Modified Existing Caps: Sometimes the simplest solution is adapting commercially available caps for your needs.
For example, I’ve seen makers drill holes in standard caps and add silicone seals for specialized applications. Not pretty, but it works.
Advanced Manufacturing Techniques
The industry keeps evolving. Here are some cutting-edge developments:
Moulage multi-matériaux: Combining hard and soft plastics in a single cap.
Étiquetage dans le moule: Adding labels during the molding process.
Smart caps: Integrating RFID chips or sensors directly into caps.
Bio-based plastics: Using renewable materials instead of petroleum-based plastics.
Common Challenges and Solutions
Manufacturing plastic caps isn’t always smooth sailing. Here are common issues and fixes:
Marques d'évier: Caused by uneven cooling. Solution: Optimize cooling channels and cycle times.
Coups courts: When plastic doesn’t fill the mold completely. Solution: Increase injection pressure or temperature.
Flash: Excess plastic at mold seams. Solution: Ensure proper mold alignment and clamping pressure.
Déformation: Caps that aren’t flat. Solution: Balance cooling and reduce internal stresses.
The Future of Cap Manufacturing
Where’s the industry headed?
Automatisation: Robots handling everything from material feeding to quality inspection.
Durabilité: More recycled content and biodegradable options.
Personnalisation: Small-batch production becoming more economical.
Integration: Caps with built-in functionality like tamper evidence and child resistance.
Principaux enseignements
Let’s wrap this up.
How to make a plastic cap depends on your needs:
- For high-volume production, injection molding is king
- Material selection matters – choose based on your application
- Thread design requires precision engineering
- Quality control is non-negotiable
- Costs drop dramatically with volume
Whether you’re looking to manufacture millions of caps or just understand the process, these fundamentals apply.
The plastic cap industry might seem simple on the surface. But dive deeper, and you’ll find a world of engineering excellence and continuous innovation.
That tiny cap on your water bottle? It represents decades of manufacturing evolution and expertise.
Pretty cool when you think about it.