Moulage par injection Le moulage par injection est un procédé de fabrication courant utilisé pour produire des pièces en plastique à grande échelle. Il est essentiel de bien concevoir les pièces pour le moulage par injection afin d'éviter les défauts, de contrôler les coûts et d'obtenir l'apparence et les performances souhaitées. Ce guide de conception complet présente les considérations clés concernant la géométrie des pièces, la sélection des matériaux, l'outillage et les opérations secondaires afin d'optimiser les composants moulés par injection.
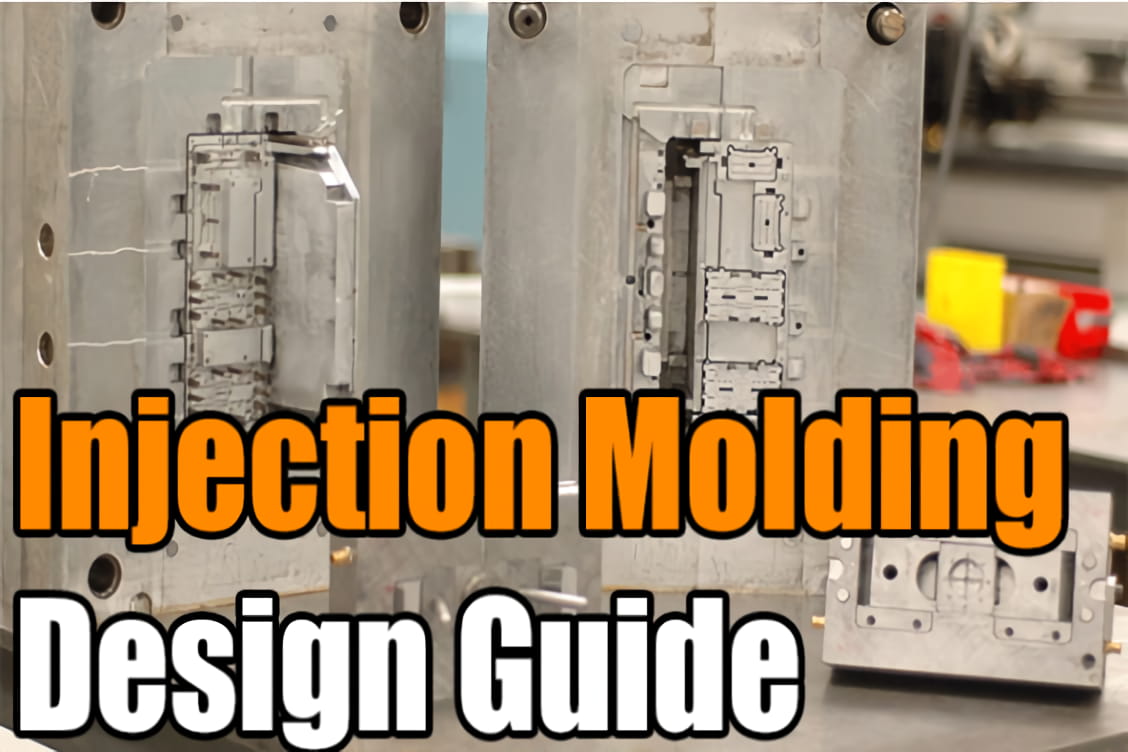
Guide de conception du moulage par injection
Éléments critiques de la conception
Plusieurs éléments critiques doivent être pris en compte lors de la conception de pièces pour le moulage par injection :
Lignes de séparation
Le plan de joint est l'endroit où les deux moitiés d'un moule d'injection se rencontrent pour éjecter la pièce refroidie et solidifiée. Les plans de joint seront toujours visibles sur les pièces finies, dans une certaine mesure, en fonction de l'emplacement, des angles de dépouille autorisés et des finitions de surface. Un placement stratégique des plans de joint peut contribuer à minimiser leur visibilité.
Sous-coupes
Les contre-dépouilles sont des géométries de pièces qui dépassent ou provoquent une interférence telle que la pièce ne peut pas être éjectée proprement d'un simple moule d'injection en deux parties. Les exemples les plus courants sont les trous transversaux, les filetages et les crochets d'encliquetage. Les contre-dépouilles augmentent la complexité et les coûts de l'outillage. Dans la mesure du possible, les pièces doivent être conçues de manière à éviter les contre-dépouilles en utilisant des techniques telles que les angles de dépouille ou les caractéristiques de remodelage. Les contre-dépouilles inévitables peuvent être compensées par l'utilisation de noyaux à action latérale et d'autres inserts.
Angles d'ébauche
Les angles de dépouille sont essentiels sur toutes les faces verticales d'une pièce pour réduire les frottements et permettre une éjection propre du moule. Un angle de dépouille minimal de 1 à 2 degrés est recommandé pour la plupart des caractéristiques, un angle plus important étant nécessaire pour les géométries plus hautes ou les finitions de surface texturées.
Épaisseur de la paroi
Une épaisseur de paroi uniforme sur l'ensemble d'une pièce est optimale pour faciliter le flux des matériaux, réduire les risques de gauchissement, minimiser les temps de cycle et diminuer les coûts. Les spécifications typiques d'épaisseur de paroi vont de 0,060 à 0,180 pouces en fonction du matériau utilisé. Des transitions graduelles doivent relier toutes les sections dont l'épaisseur de paroi varie.
Rayons et angles
Les angles vifs concentrent les contraintes et provoquent des défaillances précoces des pièces. Des congés et des rayons généreux doivent être appliqués à tous les angles intérieurs et extérieurs dans la mesure du possible afin de maintenir la résistance.
Considérations sur la conception avancée
Outre les exigences de base en matière de géométrie et de dépouille, les caractéristiques suivantes offrent des fonctionnalités supplémentaires pour les pièces et requièrent une plus grande attention lors de la conception :
Patrons
Les bossages servent de points de fixation pour les inserts ou les vis autotaraudeuses. De fines nervures ou goussets doivent, dans la mesure du possible, relier les bossages aux parois principales afin d'améliorer la stabilité et d'éviter les marques d'enfoncement dues au rétrécissement du matériau.
Côtes
Les nervures renforcent les pièces sans augmenter l'épaisseur de la paroi. Les nervures doivent être conçues en fonction des limites d'épaisseur de la paroi et comporter des congés à leur base afin d'éviter les concentrations de contraintes.
Snap Fits
Les ajustements rapides permettent d'assembler des pièces moulées par injection sans fixations. Comme pour les autres saillies par rapport à la géométrie de la paroi nominale, la dépouille est essentielle sur les parois verticales à encliquetage pour permettre le démoulage. L'épaisseur par rapport à la paroi nominale et l'emplacement nécessitent une analyse supplémentaire lors de la conception des crochets ou des cantilevers d'ajustement rapide.
Charnières vivantes
Les charnières vivantes servent de connexions fines et flexibles entre des segments en plastique rigide. La sélection des matériaux est essentielle, avec polypropylène et le polyéthylène sont des choix courants pour les produits de consommation. L'épaisseur des charnières, les limites de longueur et l'inclusion d'épaulements influencent la durabilité au cours des cycles de vie prévus.
Considérations matérielles
Le choix du matériau influence l'aspect de la pièce, les exigences de performance, les options d'outillage et les processus de fabrication requis. Parmi les principales alternatives en matière de plastique, citons
- Polypropylène (PP) - Résine bon marché avec une bonne résistance chimique, souvent utilisée pour les produits de consommation et la tuyauterie.
- Acrylonitrile Butadiène Styrène (ABS) - Choix courant lorsqu'une résistance et une ductilité supérieures à celles du PP sont nécessaires. Utilisé dans les boîtiers pour l'automobile et l'électronique
- Polycarbonate - Option optiquement claire de haute résistance lorsque la résistance aux chocs et la stabilité dimensionnelle sont essentielles
- Polyamide (Nylon) - Préféré pour les pièces mécaniques nécessitant une résistance, une fatigue et une résistance à l'usure plus élevées.
Finitions de surface
Différents aspects et sensations esthétiques peuvent être obtenus sur les surfaces des pièces moulées par injection en fonction du prétraitement du moule et des textures transférées. Les alternatives courantes selon les normes SPI sont les suivantes
- SPI-A2 - Finition brillante, semblable à un miroir, obtenue grâce à un polissage au diamant moulé.
- SPI-B1 - Finition mate et satinée obtenue en utilisant du papier de verre à 600 grains sur le moule.
- Texture du moule - Finitions personnalisées en forme de grain appliquées à l'aide de moules de sablage médiatique
Opérations secondaires
Les étapes postérieures au moulage, telles que l'assemblage, l'étiquetage, l'impression, le soudage ou l'usinage, permettent d'étendre la fonctionnalité de la pièce en fonction des besoins :
- Tampographie - Méthode pour ajouter des logos, des étiquettes et des graphiques en couleur sur des surfaces courbes moulées par injection
- Soudage par ultrasons - Fusionne des composants moulés séparés en induisant des vibrations à haute fréquence.
- Usinage CNC - Permet d'obtenir des caractéristiques de plus grande précision difficiles à intégrer directement dans les conceptions moulées
Liste de contrôle rapide pour la conception
Lors de la finalisation de la conception des pièces moulées par injection, la liste de contrôle suivante couvre les éléments clés à examiner :
- Epaisseur de paroi uniforme de 0,060 à 0,180 pouces
- Angle de dépouille minimal de 1 degré appliqué à toutes les faces verticales
- Rayons de tous les angles intérieurs et extérieurs
- Ajout de côtes de soutien aux boss isolés
- Goussets reliant les nervures projetées aux parois nominales
- Inspection de la porte, de la goupille d'éjection et de l'emplacement des orifices d'aération
- Élimination des contre-dépouilles dans la mesure du possible
- Finition de surface standard SPI spécifiée
La prise en compte correcte de ces considérations critiques en matière de conception permettra d'obtenir des pièces aux dimensions exactes, avec des défauts de fabrication et des coûts moindres. N'hésitez pas à nous contacter si vous avez des questions sur l'optimisation de votre prochain composant ou assemblage moulé par injection.