Les bulles sont l'un des défauts les plus courants dans le moulage par injection de plastique. Elles ont un impact négatif sur l'apparence et les performances des pièces. Mais qu'est-ce qui cause exactement les bulles ?
Dans ce guide complet, en tant que professionnel fabricant de moulage par injection de matières plastiquesDans le cadre de cette étude, nous explorerons les différentes causes profondes des bulles, depuis les problèmes liés aux matériaux, aux machines et aux moules jusqu'aux paramètres du processus. En comprenant ce qui se cache derrière ces défauts, vous pourrez prendre des mesures préventives et correctives ciblées pour une production sans faille.
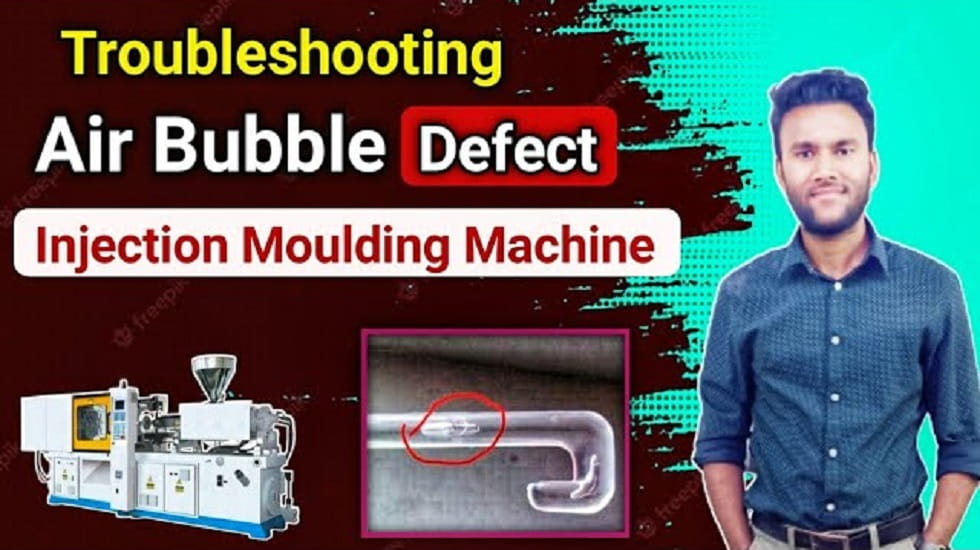
Quelles sont les causes des bulles dans le moulage par injection de plastique : Principales sources
Les bulles apparaissent lorsque des gaz sont encapsulés dans le plastique pendant le moulage. Examinons les causes typiques de l'emprisonnement des gaz :
Séchage insuffisant
De nombreuses résines absorbent facilement l'humidité ambiante. Des matériaux tels que le nylon, le polycarbonate et le PET peuvent contenir une quantité importante d'humidité s'ils ne sont pas correctement séchés au préalable. Sous la chaleur du tonneau, cette humidité se transforme en vapeur, provoquant des bulles dans le flux de matière fondue. Un séchage complet est essentiel pour éviter la formation de bulles.
Ingestion d'air
Même avec le séchage, des poches d'air peuvent encore s'infiltrer dans la manipulation de la résine. Le transport sous vide après le séchage minimise l'introduction d'air dans les granulés. Un versement soigneux et un bon entretien permettent également d'éviter la contamination.
Écoulement turbulent
Une vitesse d'injection excessive provoque un écoulement turbulent et non laminaire de la matière fondue. Ce mouvement chaotique entraîne de l'air dans le polymère, créant ainsi des microbulles. Un écoulement laminaire plus lent empêche le piégeage des gaz.
Dégradation des matériaux
Le fait de conserver la résine dans le fût pendant des périodes prolongées la dégrade en raison d'une exposition excessive à la chaleur. La viscosité réduite du plastique dégradé permet aux sous-produits gazeux de se mélanger, ce qui provoque des bulles.
Mauvaise ventilation
Une conception inadéquate de la ventilation du moule ne permet pas à l'air emprisonné d'évacuer la cavité pendant le remplissage. Sans issue, les gaz n'ont d'autre choix que de rester encapsulés sous forme de bulles.
Congélation prématurée
Des températures de moule plus froides accélèrent le taux de congélation du front d'écoulement avant que les gaz ne s'échappent complètement. La solidification plus rapide emprisonne les bulles à l'intérieur, empêchant toute fuite.
En identifiant les facteurs qui constituent des bulles dans votre application, vous pouvez mettre en place des contre-mesures ciblées. Ensuite, nous allons explorer les moyens éprouvés de traiter chacun d'entre eux.
Comment prévenir les bulles : Des solutions pour chaque cause fondamentale
En comprenant clairement ce qui cause les bulles, nous pouvons maintenant appliquer des solutions sur mesure pour un moulage par injection impeccable :
Séchage complet des matériaux
Plastiques susceptibles d'absorber l'humidité, tels que Nylon et le PET doivent être séchés jusqu'à une teneur inférieure à 0,2% avant d'être moulés, généralement à l'aide de sécheurs à dessiccation. Cela permet d'éviter les bulles de vapeur.
Manipulation soigneuse de la résine
Après le séchage, utilisez des transporteurs sous vide fermés pour transporter les granulés. Éviter les déplacements et les versements à l'air libre qui permettent l'ingestion d'air. Une manipulation délicate permet de maintenir le matériau exempt de bulles.
Vitesse d'injection conservatrice
Les profils d'écoulement plus lents et laminaires évitent les turbulences et le piégeage de l'air. Les vitesses d'injection cibles doivent être basées sur la viscosité et les caractéristiques d'écoulement de chaque matériau.
Surveillance étroite de la taille des tirs
L'adaptation du volume d'injection à la géométrie de la pièce permet d'éviter une exposition prolongée à la chaleur qui peut dégrader le plastique. Combinée à une contre-pression suffisante, elle permet également d'obtenir un amortissement adéquat.
Améliorer la conception des évents
La profondeur, le diamètre, l'emplacement et l'angle appropriés des évents facilitent l'évacuation de l'air de la cavité pendant le remplissage. Les évents à vide améliorent encore le dégagement des bulles.
Permettre une température suffisante pour les moules
Dans les limites autorisées, l'utilisation de moules plus chauds permet de conserver la fluidité des matériaux plus longtemps, ce qui laisse le temps aux gaz de s'évacuer complètement avant de geler.
Plutôt que de régler les problèmes a posteriori, cette approche proactive s'attaque aux causes profondes pour une prévention permanente. Voyons maintenant comment ces solutions s'appliquent à travers une étude de cas réelle.
Étude de cas : Élimination des bulles dans les pièces transparentes
Pour obtenir une clarté optique parfaite dans les visières moulées, un fabricant d'appareils médicaux a dû faire face à des bulles sporadiques près des sections incurvées. En s'attaquant méthodiquement aux causes profondes, les bulles ont finalement été éliminées.
Étape 1 : Séchage complet
Malgré l'utilisation de PC, une résine hygroscopique, aucun séchage spécifique n'a été mis en œuvre au préalable. Un séchoir à roue déshydratant réglé à 250°F pendant au moins 4 heures a systématiquement séché les pièces sous 0,1% d'humidité.
Étape 2 : Réglage de la dynamique des flux
Des vitesses d'injection élevées ont provoqué des turbulences au milieu du remplissage, car l'unique petite vanne ne pouvait pas suivre. L'abaissement de la vitesse a permis un écoulement laminaire, tandis qu'une deuxième porte a équilibré le remplissage.
Étape 3 : Augmenter la capacité de ventilation
À l'origine, il n'existait que deux petits évents pour la grande zone incurvée de 14 pouces. L'ajout d'évents plus larges a permis aux gaz de s'échapper.
En combinant les changements de matériaux, de moules et de processus conformément aux principes fondamentaux décrits précédemment, on a pu produire des pièces sans défaut et sans bulles en grandes quantités.
En s'attaquant aux causes distinctes de ses bulles à l'aide de solutions sur mesure, ce fabricant a obtenu une clarté de précision répondant à des normes médicales strictes. La clé était d'identifier et de rectifier correctement les causes profondes.
Préparer une stratégie de prévention
Si les correctifs apportés après la production ont un certain effet, la prévention permanente des bulles nécessite une approche en amont :
- Vérifier les protocoles de préséchage optimaux pour chaque matériau
- Manipuler les résines avec précaution pour éviter l'ingestion d'air.
- Établir des taux de remplissage d'injection prudents
- Contrôler étroitement le volume des tirs
- Amélioration de la ventilation pour une évacuation optimale de l'air
- Laisser suffisamment de chaleur au moule pour le temps d'aération
Plutôt que de s'attaquer aux symptômes de manière réactive, cette philosophie proactive arrête les bulles à la source pour une fabrication sans faille et résiliente. Quelques petits ajustements suffisent à faire une grande différence !
Associée à un contrôle rigoureux des processus et à un moulage scientifique, l'absence de bulles devient une référence réalisable, ce qui permet d'obtenir une qualité de surface parfaite et une intégrité structurelle optimale.
En adoptant une vision éclairée et fondée sur les causes profondes des défauts de bulles, les transformateurs de matières plastiques peuvent passer de la lutte contre les bulles à leur élimination pure et simple grâce à des pratiques optimales fondamentales. Le résultat est une performance et une esthétique maximales.