La pression dans l'empreinte est l'un des paramètres les plus importants à mesurer et à optimiser dans le moulage par injection. En tant qu'indicateur de la qualité des pièces, la compréhension et le contrôle de la pression dans l'empreinte permettent d'accélérer les cycles, de réduire les rebuts et de diminuer les coûts.
En tant que professionnel fabricant de moulage par injection de matières plastiquesJ'écris cet article pour parler de la pression dans l'empreinte dans le moulage par injection. Dans ce guide complet, vous apprendrez :
- Qu'est-ce que la pression de la cavité ?
- Pourquoi la pression dans l'empreinte est-elle si importante pour la qualité des pièces ?
- Comment la pression dans l'empreinte est corrélée à vos pièces moulées
- Conseils et bonnes pratiques pour optimiser la pression dans les cavités
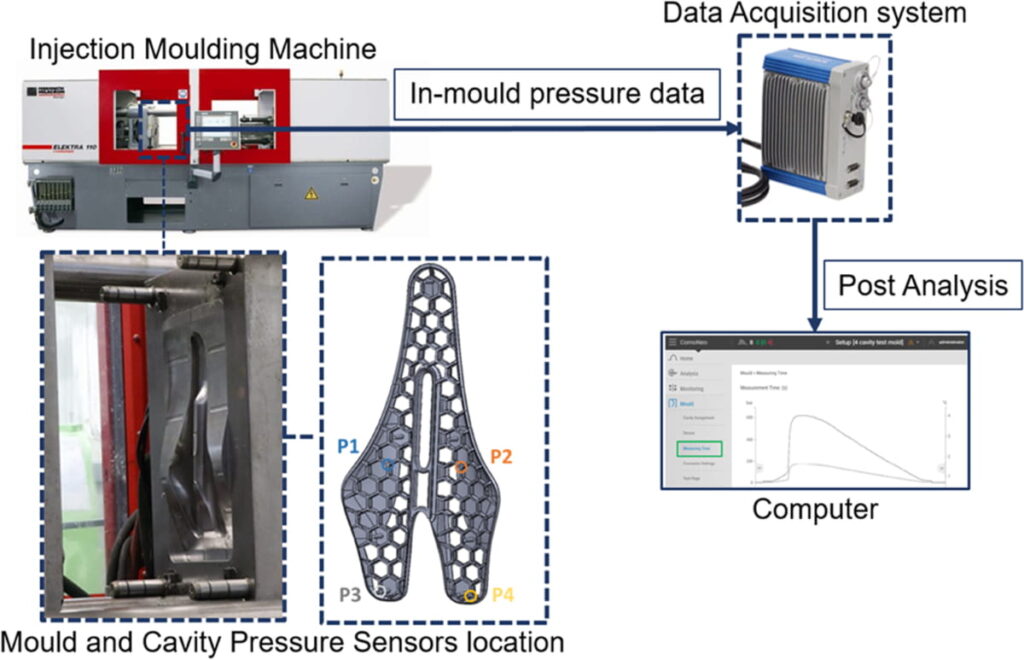
Qu'est-ce que la pression de l'empreinte dans le moulage par injection ?
Chaque moule à injection contient une ou plusieurs cavités remplies de plastique fondu qui forme chaque pièce. La pression exercée à l'intérieur de ces cavités est simplement appelée pression dans la cavité.
La pression dans la cavité évolue de manière dynamique tout au long du cycle de moulage, de l'injection à l'éjection en passant par le refroidissement. Cela en fait un paramètre incroyablement instructif sur ce qui se passe physiquement dans le plastique au fur et à mesure de la production des pièces.
Pression hydraulique, plastique et de cavité
Sur la plupart des machines de moulage par injection, vous verrez la pression hydraulique affichée sur l'écran de contrôle de l'opérateur, car elle est liée à la sortie de la pompe. Il ne s'agit cependant pas de la pression réelle à l'intérieur du cylindre ou du moule !
Pression plastiqueLa pression d'injection, également appelée pression spécifique, fait référence à la résistance physique du plastique fondu qui s'écoule à l'intérieur du cylindre et de la buse. Cette pression est amplifiée par la pointe de la buse et la carotte en fonction du taux d'intensification de la machine.
Enfin, la pression dans l'empreinte représente la pression en temps réel à l'intérieur des cavités du moule. Elle est inférieure à la pression du plastique en raison des pertes dans le système de coulée.
Pour un contrôle et une répétabilité réels du processus, la pression dans l'empreinte est la valeur optimale que les mouleurs par injection doivent surveiller.
Pourquoi la pression de la cavité est-elle si importante ?
La mesure et l'analyse de la pression dans les cavités offrent des avantages considérables :
- Corrélation directe avec la qualité des pièces
- Amélioration de la stabilité du processus
- Une configuration et une optimisation plus rapides
- Réduction des coûts de mise au rebut et d'essai
Essentiellement, le suivi des courbes précises de pression dans l'empreinte vous permet de "voir" à l'intérieur du moule. La visualisation qu'il fournit revient à avoir radiographie Les lunettes sont allumées, ce qui permet d'isoler facilement les défauts de moulage et d'ajuster les paramètres en conséquence.
La pression des cavités est l'"empreinte digitale" des pièces de qualité
Au fur et à mesure que les pièces se remplissent, se tassent et se refroidissent dans le moule, les variations de la pression dans l'empreinte sont directement liées aux dimensions finales, à l'aspect, à la résistance et aux performances du produit.
Certaines valeurs peuvent indiquer si la pression est trop élevée ou trop basse, si la viscosité n'est pas optimale ou si d'autres défauts tels que les coups courts, les bavures, les coulures et les déformations sont présents.
En surveillant ces tendances, la pression dans l'empreinte devient l'"empreinte digitale" d'une pièce de bonne qualité. Tant que la courbe reste dans les limites définies du processus, vous pouvez confirmer que les pièces répondent aux spécifications.
Installation plus rapide et optimisation des processus
La mise en place d'un processus stable de moulage par injection nécessite généralement de nombreux essais de production pour tester des combinaisons de températures, de pressions, de vitesses et de temps.
Le contrôle en temps réel de la pression dans l'empreinte accélère la validation en montrant immédiatement l'impact des ajustements. Il facilite également l'équilibrage des systèmes à canaux chauds, car il permet de déterminer avec précision l'uniformité de la pression.
À long terme, l'optimisation de la pression dans l'empreinte minimise les variations d'une pièce à l'autre et d'un lot à l'autre. Cela réduit la nécessité d'une revalidation et d'inspections dimensionnelles coûteuses.
Comment mesurer et analyser la pression de la cavité, étape par étape
Maintenant que vous comprenez pourquoi la pression dans la cavité est si précieuse, voyons comment la mesurer et utiliser les données.
Voici un aperçu des meilleures pratiques pour la mise en œuvre de capteurs de pression dans les cavités et de systèmes de surveillance :
Étape 1 : Installer les capteurs à des emplacements optimaux
Des capteurs piézoélectriques ou à jauge de contrainte sont montés directement à l'intérieur de la cavité du moule pour capturer les données de pression.
L'emplacement des capteurs dépend de la géométrie de la pièce, du nombre de cavités et des points d'injection. À l'aide d'un logiciel de simulation, déterminez les positions qui fournissent une représentation globale précise de la pression de la cavité.
Prêtez attention à :
- Portes et emplacements de fin de remplissage
- Zones avec des coupes transversales épaisses et minces
- Zones sujettes à des défauts tels que des coups courts ou des marques d'enfoncement
L'intégration correcte des capteurs nécessite des trous de vis ou des encoches à l'intérieur de l'acier de la cavité, ainsi que des fentes ou des rainures pour l'acheminement des câbles à l'extérieur du moule.
Étape 2 : Connexion au dispositif d'acquisition de données
Des transmetteurs avec ou sans fil relient les capteurs à l'intérieur du moule à un dispositif central d'acquisition de données. Ce dernier enregistre les mesures de pression et de température de manière dynamique tout au long du cycle de moulage.
Choisissez un matériel capable de répondre aux besoins :
- Nombre de canaux de capteurs
- Vitesse d'échantillonnage et volume de données
- Intégration avec d'autres capteurs tels que la température de fusion ou de moulage
- Compatibilité des logiciels d'analyse des résultats
Étape 3 : Interprétation de la courbe de pression de la cavité
Grâce aux données quantitatives en temps réel, les opérateurs peuvent identifier la phase de moulage spécifique où des problèmes surviennent en fonction des changements dans la forme de la courbe de pression :
Phase d'injection : Un pic de pression indique un remplissage initial du moule. Une chute prématurée peut laisser présager des tirs courts.
Phase de transition : Les pics de pression atteignant la valeur optimale prédéterminée correspondent au remplissage du moule 100%. Des valeurs inférieures indiquent un remplissage incomplet.
Phase d'emballage/de maintien : La pression doit rester suffisamment élevée tout au long de la solidification pour obtenir la résistance et l'aspect requis de la pièce. Une chute prématurée indique des déficiences du matériau ou de la machine.
L'idéal est de tracer les données de plusieurs cycles les unes au-dessus des autres pour visualiser la stabilité. Essayez d'obtenir une fenêtre de processus étroite où la pression dans la cavité reste reproductible d'un cycle à l'autre.
Conseils et bonnes pratiques pour optimiser la pression dans la cavité
Le respect constant des objectifs de pression dans l'empreinte permet de réduire le nombre de pièces mises au rebut et d'accélérer les temps de cycle. Voici quelques conseils pour améliorer le contrôle :
1. Déterminer les cibles optimales
Chaque combinaison de moule et de matériau a des objectifs de pression optimale qui lui sont propres. Pour commencer, prenez en compte les recommandations du fabricant, mais affinez-les en fonction de la corrélation avec les résultats de l'inspection du premier article.
2. Améliorer l'intégration des capteurs
Si les valeurs de pression fluctuent de manière erratique d'un cycle à l'autre, il se peut que les capteurs soient installés de manière non optimale. Vérifier à nouveau l'emplacement des capteurs et le cheminement des câbles.
3. Ajuster la vitesse d'injection
Une injection plus rapide augmente de façon exponentielle la pression dans la cavité, tandis qu'une injection plus lente permet d'élargir la fenêtre de traitement. Ajustez les profils de vitesse pour stabiliser la pression.
4. Modifier la température du moule
Les moules plus froids facilitent le remplissage des cavités, tandis que les moules plus chauds réduisent la viscosité et les pertes de pression. Optimisez la température du moule pour atteindre vos objectifs.
5. Emplacement du portillon d'aiguillage
Les grandes longueurs d'écoulement causent plus de pertes de pression que les vannes directes. Envisager de déplacer les vannes plus près des zones problématiques du moule.
6. Augmenter la taille de la machine
Sur les petites machines, la pression d'injection maximale peut ne pas atteindre les niveaux nécessaires pour un remplissage complet. Passer à un tonnage de pinces plus important.
Conclusion - Pourquoi la pression de la cavité est-elle importante pour la qualité des pièces ?
Comprendre ce qui se passe à l'intérieur du moule est essentiel pour les entreprises qui cherchent à optimiser leurs processus de moulage par injection et à réduire les coûts de fabrication.
En tant qu'indicateur le plus direct des conditions dans lesquelles chaque pièce est créée, le temps réel mesure de la pression dans la cavité offre une valeur inégalée.
Grâce à un logiciel d'analyse couplé à une sélection et à un placement appropriés des capteurs, les courbes de pression de la cavité permettent de prendre des décisions plus judicieuses :
- Identifier les problèmes de stabilité à l'origine des défauts
- Accélérer les DOE et l'optimisation des processus
- Validation des processus documentaires pour les normes ISO ou les réglementations médicales
- Trier automatiquement les bonnes et les mauvaises pièces
En exploitant ces données facilement accessibles, votre équipe obtient des informations précieuses sur l'état physique du plastique et libère des efficacités de production pour tous les produits moulés par injection.
Quels sont les aspects de la pression dans la cavité qui vous ont le plus surpris ou que vous avez appris pour la première fois ? Faites-moi savoir dans les commentaires ce que vous avez trouvé de précieux dans ce guide ou si vous avez des questions supplémentaires !