La décompression, également connue sous le nom de "suckback", est un paramètre important du moulage par injection qui permet de soulager la pression à la fin du processus d'injection. En tant que professionnel fabricant de moulage par injection de matières plastiquesC'est pourquoi je partage avec vous cet aperçu détaillé de ce qu'est la décompression, de son importance et de son impact sur le processus de moulage par injection.
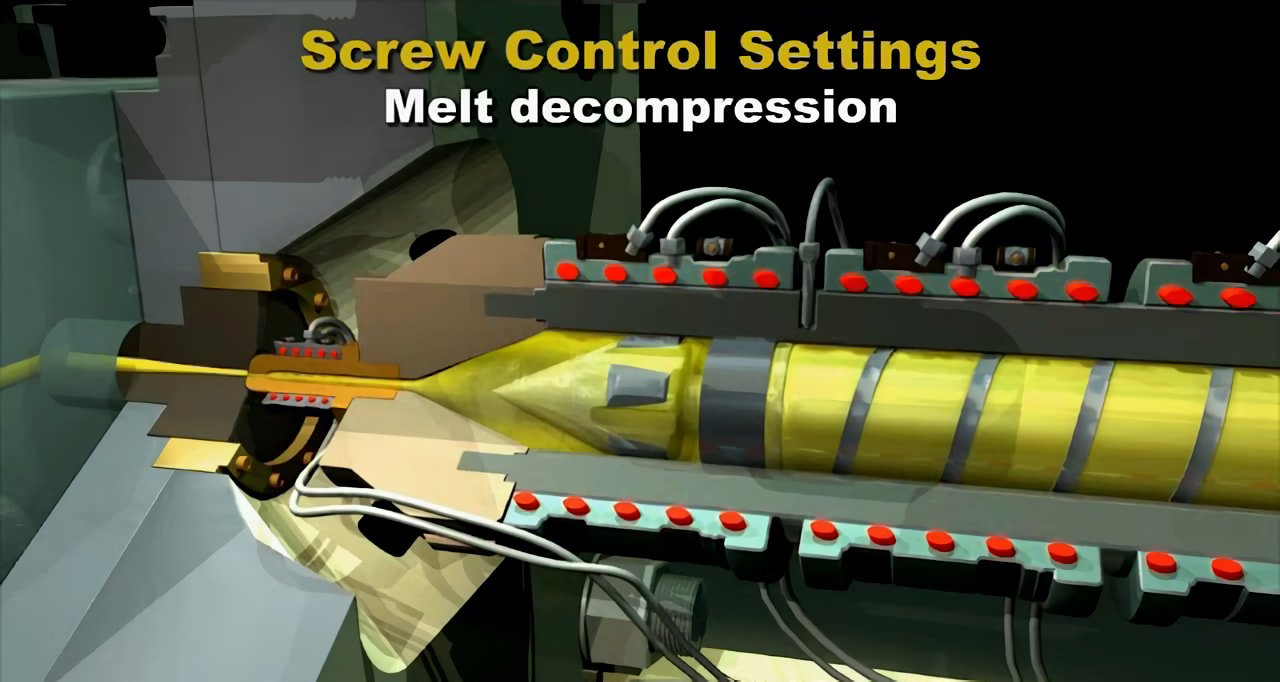
Qu'est-ce que la décompression dans le moulage par injection ?
La décompression, ou suckback, consiste à rétracter légèrement la vis à la fin du processus d'injection pour relâcher la pression devant la pointe de la vis. Pour ce faire, la vis est ramenée linéairement sur une petite distance, généralement de l'ordre de 0,1 pouce ou de quelques millimètres.
La décompression est essentielle pour relâcher la pression accumulée dans le canon juste avant les phases de tassement et de maintien. Elle crée un petit espace entre la pointe de la vis et le coussin qui se trouve devant elle. Lorsque la vis tourne pour doser le matériau en vue du tir suivant, cet espace se remplit d'abord avant que la pression ne s'accumule à nouveau pour forcer la vis à reculer.
Ce qui se passe pendant la décompression
La décompression est un mouvement contrôlé au cours duquel la vis se rétracte partiellement ou est "aspirée" dans le cylindre. Ce mouvement se produit après que la vis a fini d'injecter le plastique dans la cavité du moule.
La vis peut se rétracter de quelques millimètres seulement. Mais ce petit mouvement a une grande utilité : il soulage la pression qui s'est accumulée devant la pointe de la vis.
Sans décompression, la haute pression resterait piégée.
Le soulagement de cette pression a plusieurs fonctions :
- Il permet aux machines dotées de buses ouvertes d'éviter la formation de gouttes ou de fuites de matériau.
- Il améliore l'homogénéité de la taille de la grenaille et de la plastification.
- Cela peut aider le clapet de non-retour à se fermer complètement
- Il peut réduire l'usure des composants tels que l'anneau de contrôle.
Dans la suite de ce guide, nous étudierons les spécificités de l'impact de la décompression sur les processus de moulage par injection. Tout d'abord, voyons pourquoi la gestion de la pression est si cruciale dans le moulage par injection.
Pourquoi contrôler la pression avec la décompression ?
Le contrôle de la pression est une tâche difficile mais essentielle dans le domaine du moulage par injection. Une pression trop élevée entraîne des problèmes tels que le clignotement, les tirs courts et les défauts des pièces. Une pression trop faible entraîne un remplissage incomplet.
La décompression permet aux transformateurs de mieux contrôler la pression à un moment clé - lorsque l'injection se termine et que l'emballage/le maintien commence.
La décompression permet d'éviter d'appliquer une pression de gonflage à une situation de surpression. Cela permet d'éviter des problèmes tels que
- Clignotement dû à une pression excessive
- Blocage prématuré de la vanne bloquant l'écoulement
- Dommages causés aux composants par les pics de pression
- Des tailles d'injection incohérentes dues à des fuites au niveau du clapet anti-retour
Une décompression bien réglée permet également de conserver une pression suffisante pour vider complètement les pièces.
Pour obtenir une décompression optimale, il faut trouver le bon équilibre entre le soulagement de la pression excessive et le maintien d'une pression suffisante pour le pliage.
Décompression et autres types de contrôle de la pression
Outre la décompression, les machines de moulage par injection disposent d'autres moyens de gérer la pression :
- Pression d'emballage - Une pression plus faible est appliquée après le remplissage pour tasser la cavité du moule.
- Injection en deux étapes - Passage d'une pression d'injection élevée à une pression plus faible à un point donné
- Fermeture des buses - Valves pour bloquer la buse et contenir la pression
La décompression va de pair avec ces autres contrôles de pression. Par exemple, une décompression bien programmée permet une transition en douceur de la pression d'injection à la pression de remplissage.
De plus, la suppression de la pression résiduelle peut éliminer la nécessité de fermer les buses dans de nombreux processus de moulage.
Quelle est l'ampleur de la décompression nécessaire ?
Il n'existe pas de règle universelle concernant la décompression (distance de rétraction) à appliquer. Les exigences dépendent de facteurs tels que
- Buse de la machine - Ouverture ou fermeture
- Viscosité des matériaux et caractéristiques de congélation
- Pression d'injection réelle utilisée
- Pression de garnissage souhaitée
- Vérifier la conception et l'état de l'anneau
Comme point de départ, de nombreux transformateurs utilisent une distance de décompression égale à 1,5 fois la course de l'anneau de contrôle. Mais ne vous fiez pas uniquement aux règles empiriques.
Le réglage de la décompression est essentiel pour optimiser le contrôle de la pression. Nous examinerons les procédures de réglage plus en détail dans un instant.
Terminologie de la décompression
Comme la plupart des processus de fabrication, le moulage par injection possède son propre langage. Voici quelques termes clés relatifs à la décompression :
- Retour de bâton - Un autre terme pour la décompression, basé sur le fait que la vis est "réaspirée" dans le canon.
- Contrôle de la bave - Empêcher les fuites de matériaux à partir des embouts ouverts lors de la décompression
- Coussin - La petite quantité de plastique qui reste devant la vis après la décompression
Le coussin agit comme un ressort pour transmettre la pression dans les phases d'emballage et de maintien. La taille et la consistance du coussin sont essentielles pour une production uniforme.
Pourquoi utiliser la décompression ? Avantages et inconvénients
Examinons maintenant quelques-uns des principaux avantages que la décompression apporte au moulage par injection :
Prévenir les fuites de matériaux
Sur les machines dont les buses sont ouvertes, la décompression empêche la matière de s'écouler ou de s'accumuler pendant la transition entre l'injection et l'emballage.
Cette fonction remplace les buses à obturation mécanique. En évitant les obturateurs, on élimine leur entretien et le risque de fuites ou de gel.
Améliorer la régularité des tirs
Une décompression bien réglée optimise la taille et la forme du coussin. Cela améliore la régularité d'un coup à l'autre.
En revanche, une décompression inadéquate permet au matériau de revenir de manière irrégulière vers la vis. Cela érode le coussin et entraîne une variation de la taille de la grenaille.
Réduire l'usure
La décompression atténue la pression qui tente de forcer l'ouverture du clapet de non-retour pendant l'injection. Cela réduit le broyage et l'usure.
Une pression plus faible lors de la fermeture de la vanne diminue également les charges sur les composants tels que l'embout de la vis, la bague de contrôle et la buse de pulvérisation.
Sur de longues séries de production, la diminution de l'usure permet d'économiser de l'argent sur la maintenance, les réparations et les temps d'arrêt.
Améliorer le contrôle des processus
Une bonne décompression est la clé d'une gestion totale de la pression. La maîtrise de ce paramètre permet aux transformateurs de mieux contrôler le remplissage, l'emballage et la qualité des pièces.
Cependant, une décompression incorrecte peut nuire à la cohérence et à la qualité des pièces :
- Une décompression excessive permet l'ingestion d'air, ce qui entraîne des défauts.
- Une décompression insuffisante entraîne clapet anti-retour fuites et variations des coussins
Cette imprévisibilité sabote même les meilleures tentatives de contrôle scientifique du processus de moulage.
Comment et quand décompresser
Maintenant que nous avons abordé l'importance cruciale de la décompression, examinons comment et quand elle se produit dans le cycle de moulage par injection.
Il existe deux options pour initier la décompression :
Basé sur le temps
La première approche, purement temporelle, démarre la décompression lorsque le temps d'injection atteint un point de consigne.
Une séquence typique est la suivante :
- La phase d'injection remplit la cavité du moule
- L'injection se termine lorsque la pression dans la cavité ou la position de la vis atteint le seuil.
- La temporisation permet de geler la porte
- La décompression rétracte la vis pour réduire la pression
Baser la décompression uniquement sur le temps manque de précision. On risque de se rétracter trop tôt avant que la porte ne se referme ou trop tard pour permettre un reflux.
Basé sur la position avec récupération de la vis
Les contrôleurs modernes lient directement la décompression à la position de la vis. Cette approche permet de décompresser pendant la récupération de la vis après avoir détecté que la vis atteint une cible.
Voici une séquence typique :
- La phase de remplissage injecte le matériau jusqu'à ce que la vis atteigne la position programmée.
- Commutation de la pression sur le capteur de cavité
- La vis se rétablit pour rattraper le point de consigne de la position
- La décompression s'active au niveau de l'interrupteur de limite de récupération
- La vis tourne pour reconstruire le coussin
Cette technique permet d'éviter les retours d'eau tout en garantissant une pression suffisante pour remplir le moule.
La récupération des vis basée sur la position pour la décompression est précise et sensible aux variations de chaque tir. Le processus est ainsi optimisé et maîtrisé.
Réglage des paramètres de décompression
Comme pour la plupart des paramètres de moulage par injection, un réglage correct de la décompression nécessite des essais et des analyses :
Étape 1 : Situation de référence sans décompression
Tout d'abord, arrêtez la décompression et établissez les conditions de base. Prenez note des indicateurs clés :
- Cohérence du poids du projectile
- Variation de la qualité des pièces
- Clignotement ou marques dues à des pointes de pression
- Bave de la buse
Étape 2 : Commencer doucement
Activez à nouveau la décompression en commençant par des réglages prudents. Par exemple :
- Distance : 1 mm
- Temporisation : 50 ms
Étape 3 : Collecte de données
Prendre des mesures sur la durée d'un échantillon (par exemple, des contrôles horaires sur une période de 8 heures) :
- Moyenne et étendue de la taille des tirs
- Mesures de la pression de la cavité et de la buse
- Journal de production indiquant les défauts
Étape 4 : Ajustement et nouveau test
Augmenter progressivement les paramètres de décompression tout en évaluant les effets :
- Essayer une distance de rétraction plus élevée
- Réglage de la temporisation vers l'avant ou vers l'arrière
- Saisir les valeurs directement ou par pourcentage
Après chaque modification, répétez l'échantillonnage et l'analyse des données avant de procéder au changement suivant.
Étape 5 : Trouver le bon point
Tracez les tendances jusqu'à ce que les taux de défauts atteignent un seuil acceptable et que d'autres mesures critiques, comme le poids de la grenaille, affichent une variation minimale.
Soyez méthodique lorsque vous évaluez le rapport risque/récompense d'une augmentation de la distance ou du temps de décompression.
Les réglages optimaux alignent parfaitement la décompression pour soulager l'excès de pression tout en maintenant les exigences de la phase d'emballage, tir après tir.
Obtenir de l'aide pour la décompression
Étant donné que de nombreuses variables influent sur l'optimisation de la décompression, l'obtention d'une aide peut accélérer la mise en place. Les options sont les suivantes :
- Fournisseurs de matériaux - Les fabricants fournissent des guides de traitement détaillés pour leurs résines, y compris des recommandations de décompression.
- Manuels des machines - La plupart des manuels de presse donnent des distances de décompression de base pour commencer à régler.
- Fabricants de moules - Les entreprises qui conçoivent et construisent votre moule ont l'expertise nécessaire pour régler la décompression en fonction de la conception de leur outillage et du plastique que vous avez choisi.
- Logiciel de simulation - Des programmes avancés modélisent désormais l'impact des changements de paramètres tels que le moment de la décompression et la distance. Leurs prédictions constituent une excellente base de départ.
- Experts en moulage scientifique - Les spécialistes du moulage par injection et les intégrateurs de systèmes de contrôle avancés apportent des connaissances pratiques approfondies pour maîtriser rapidement les méthodes de décompression à appliquer à votre application. Profitez de leur expertise plutôt que de partir de zéro.
Bien que le réglage de la décompression repose sur des indicateurs de précision et des méthodes de réglage systématiques, il faut également faire appel à ses sens lors des essais. Écoutez les changements dans le son de la machine lorsque la décompression est plus ou moins forte. Sentez les changements subtils dans les vibrations. L'apport de toutes vos facultés vous aide à guider votre analyse.
La maîtrise de la décompression - et du contrôle de la pression en général - est un défi qui en vaut la peine. Le moulage par injection relève autant de l'art que de la science. Développez une intuition basée sur l'expérience pour faire passer votre contrôle scientifique du processus au niveau supérieur.
Applications adaptées à la décompression
L'ajout de la décompression améliore les processus de moulage par injection à bien des égards. Mais certaines situations présentent des avantages particuliers :
1. Élimination de la bave de buse
Les machines de moulage à buse ouverte risquent de provoquer des fuites de matière sans décompression. Une aspiration bien calibrée contenant de la matière fondue à la place des fermetures de buses empêche la formation de gouttes en milieu de cycle.
2. Moules pour canaux chauds
La décompression libère la pression résiduelle de manière préventive. Cela permet de protéger les composants délicats des canaux chauds contre l'exposition à des charges de pointe excessives lorsque les vannes se ferment.
3. Moulage de précision
Le micromoulage et d'autres procédés exigeant une constance d'un coup à l'autre dépendent de la formation d'un coussin stable. La décompression permet d'accorder le coussin juste ce qu'il faut pour assurer la répétabilité.
4. Moulage scientifique
Les méthodes d'analyse et de contrôle avancées exigent une gestion totale de la pression. La décompression est le chaînon manquant pour une véritable maîtrise des étapes de remplissage, d'emballage et de maintien.
5. Validation des contrôles
Le réglage de la décompression met à rude épreuve les ensembles de capteurs sophistiqués et les algorithmes adaptatifs à la volée. Si les modèles de processus sont capables de gérer ce paramètre, la confiance dans leurs recommandations est maximale.
Pour toute application recherchant une cohérence et une capacité maximales, il est indispensable d'apprendre à tirer parti de la décompression. Commencez dès aujourd'hui à en récolter les fruits grâce aux conseils ci-dessus. Poursuivez votre chemin vers une précision et une perfection toujours plus grandes !
En résumé
En résumé, la décompression (ou aspiration) rétracte la vis pour libérer la pression emprisonnée après que l'injection a rempli la cavité du moule. La gestion de cette transition de pression permet d'éviter les défauts tout en assurant le conditionnement complet des pièces.
Le réglage de la distance et du moment de la décompression est nuancé mais vital pour améliorer la régularité. La maîtrise de cette technique permet d'atteindre de nouveaux niveaux de contrôle scientifique et de moulage de précision.