Le maintien de la pression est un aspect essentiel, mais souvent mal compris, du processus de moulage par injection. En tant que professionnel fabricant de moulage par injection de matières plastiquesJe suis ici pour démystifier ce paramètre crucial et expliquer exactement l'impact de la pression de maintien sur vos pièces moulées.
Commençons par le début : qu'est-ce que la pression de retenue ?
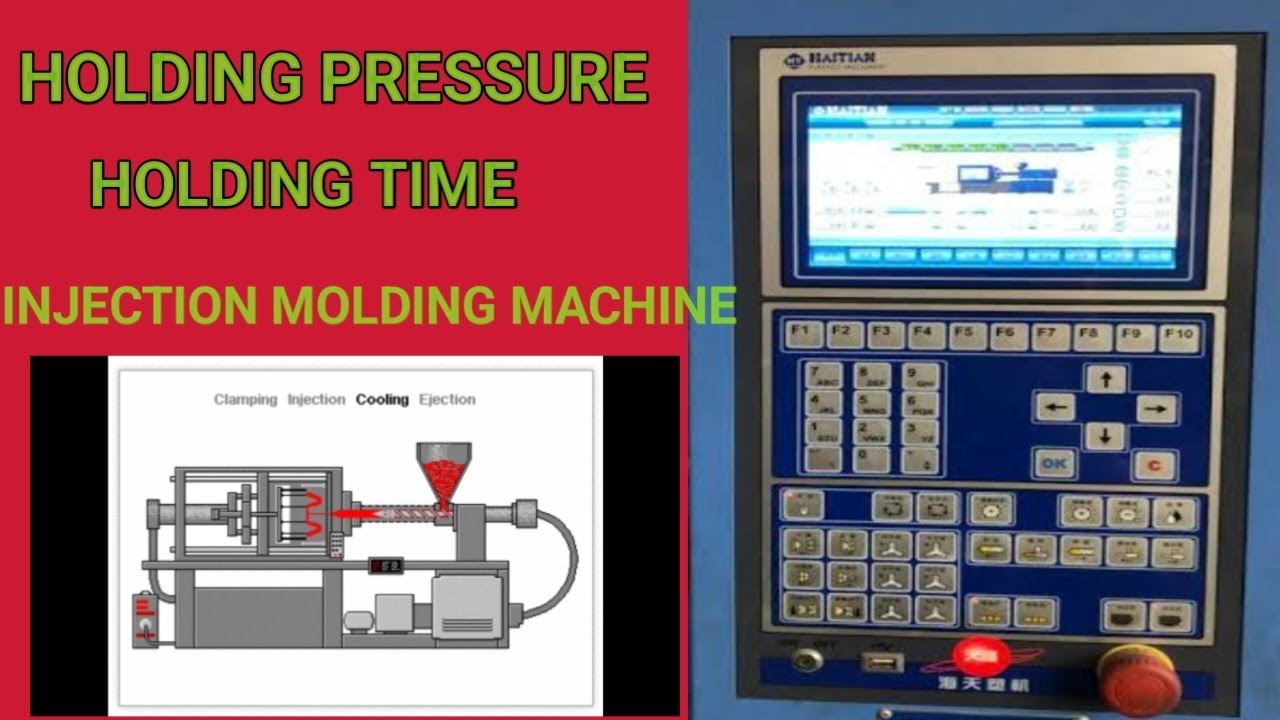
Définition de la pression de maintien
En bref, pression de maintien est la pression maintenue sur le plastique fondu après le remplissage de la cavité du moule pendant le moulage par injection. Elle se situe généralement autour de 70-80% de la pression d'injection maximale.
L'objectif du maintien de la pression est double :
- Compenser le retrait du matériau lors du refroidissement et de la solidification de la pièce
- Tasser le moule et exercer une force suffisante pour que les derniers 5-10% de la cavité se remplissent.
Le plastique fondu se rétracte en refroidissant. Sans pression de maintien, ce rétrécissement aspirerait le surplus de matière des canaux et des portes vers le canon, ce qui vous donnerait des pièces de faible diamètre.
En maintenant la pression sur la vis, le moule est alimenté en matériau supplémentaire pour tenir compte de ce retrait. Le résultat ? Des pièces entièrement emballées.
Je ne sais pas ce qu'il en est pour vous, mais je pense que quelques images sont nécessaires. Voici ce qui se passe pendant les phases du moulage par injection :
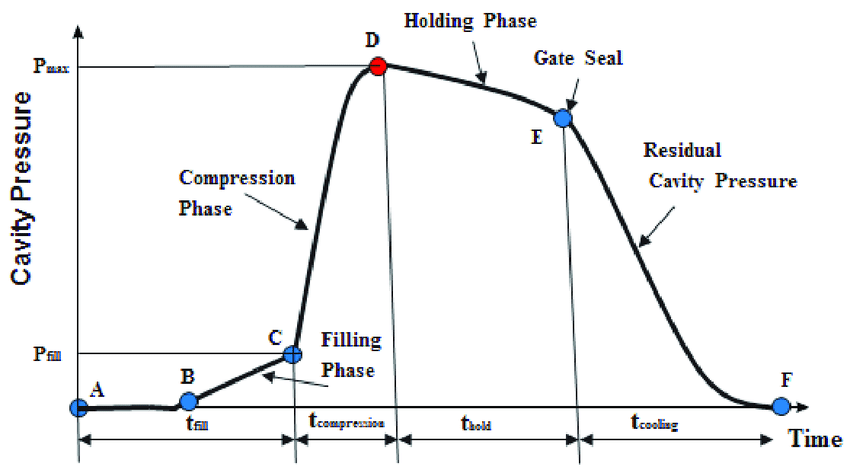
- Phase 1 - Remplissage : La pression d'injection remplit ~95% de la cavité du moule.
- Phase 2 - Mise en place : la pression de maintien permet d'extraire la dernière partie de la cavité.
- Phase 3 - Refroidissement : La pression diminue au fur et à mesure que la pièce se solidifie
Les valeurs de pression réelles pendant le maintien dépendent du matériau. Par exemple :
- Polyamide (PA) pression de maintien - 50% de la pression d'injection
- Polyoxyméthylène (POM) pression de maintien - 80% de la pression d'injection
- Pression de maintien du polypropylène (PP) / polyéthylène (PE) - 30-50% de la pression d'injection
Mais quelle que soit la résine, la pression de maintien est toujours inférieure à la pression d'injection afin d'éviter les bavures et autres défauts.
Maintenant que vous avez compris les principes fondamentaux, voyons pourquoi il est important d'ajuster la pression de retenue.
L'importance du maintien de la pression
En un mot : la qualité.
Une pression de maintien adéquate élimine les défauts des pièces, tels que les coups courts, le rétrécissement et les vides internes. Jetez un coup d'œil :
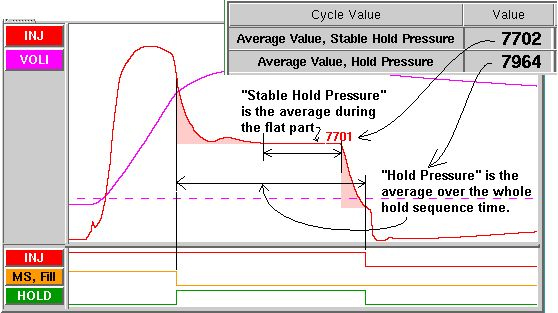
Par ailleurs, une pression de maintien insuffisante entraîne :
- Marques d'évier
- Les pages de guerre
- Lignes de soudure
- Incohérence dimensionnelle
Une pression de maintien excessive entraîne des problèmes tels que
- Flash
- Contrainte résiduelle
- Fard à joues
Pas de quoi en faire un fromage.
En réglant votre pression de maintien au niveau optimal, vous pouvez éviter tous ces défauts et produire des pièces de qualité constante, lot après lot.
Laissez-moi vous montrer ce que je veux dire.
Réglage de la pression de maintien pour la qualité des pièces
Le réglage de la pression de maintien relève plus de l'art que de la science. Mais voici une méthode fiable pour trouver le point idéal :
Étape 1 : Commencez par une pression de maintien de base d'environ 65-75% de la pression d'injection maximale.
Étape 2 : Augmenter progressivement la pression de maintien à chaque tir. Inspecter les pièces pour détecter les défauts visuels entre les tirs.
Étape 3 : Cessez d'augmenter la pression de maintien lorsque l'opercule présente les premiers signes de rougissement ou de clignotement.
Étape 4 : Réduire la pression de maintien de ~5% à partir du point de rougissement/flash. Il s'agit de la pression de maintien optimale.
Dans l'idéal, vous obtiendrez un processus qui remplit complètement le moule sans rougir la porte ou introduire des contraintes résiduelles.
Bien entendu, ne modifiez pas la pression de maintien à l'aveuglette. Faites attention à ses effets sur la qualité des pièces à chaque incrément :
- Si la pression est trop faible, il faut s'attendre à des tirs courts et à des coulées.
- A proximité de la pression optimale, les pièces doivent se remplir complètement sans défaut.
- Au-dessus de la pression optimale, le rougissement de la porte et le flash apparaissent
Ajustez votre processus en conséquence.
Et voilà qui conclut ce cours accéléré sur le maintien de la pression ! Faites-moi savoir si vous avez d'autres sujets sur le moulage par injection que vous aimeriez que j'aborde. Je vis pour ce genre de choses !