Le moulage par injection est l'un des procédés de fabrication les plus courants aujourd'hui. Cette technique polyvalente permet de tout produire, des blocs de construction en plastique pour les jouets aux panneaux de carrosserie des automobiles.
Qu'est-ce que le moulage par injection ?
C'est simple, Le moulage par injection est un procédé de fabrication de pièces par injection d'un matériau fondu dans un moule. Le plastique fondu se refroidit ensuite et se solidifie pour prendre la forme du produit final..
Mais qu'est-ce que le moulage par injection et comment ce processus fonctionne-t-il ? Poursuivez votre lecture, en tant que professionnel moulage par injection de plastique Je vais vous aider à le découvrir.
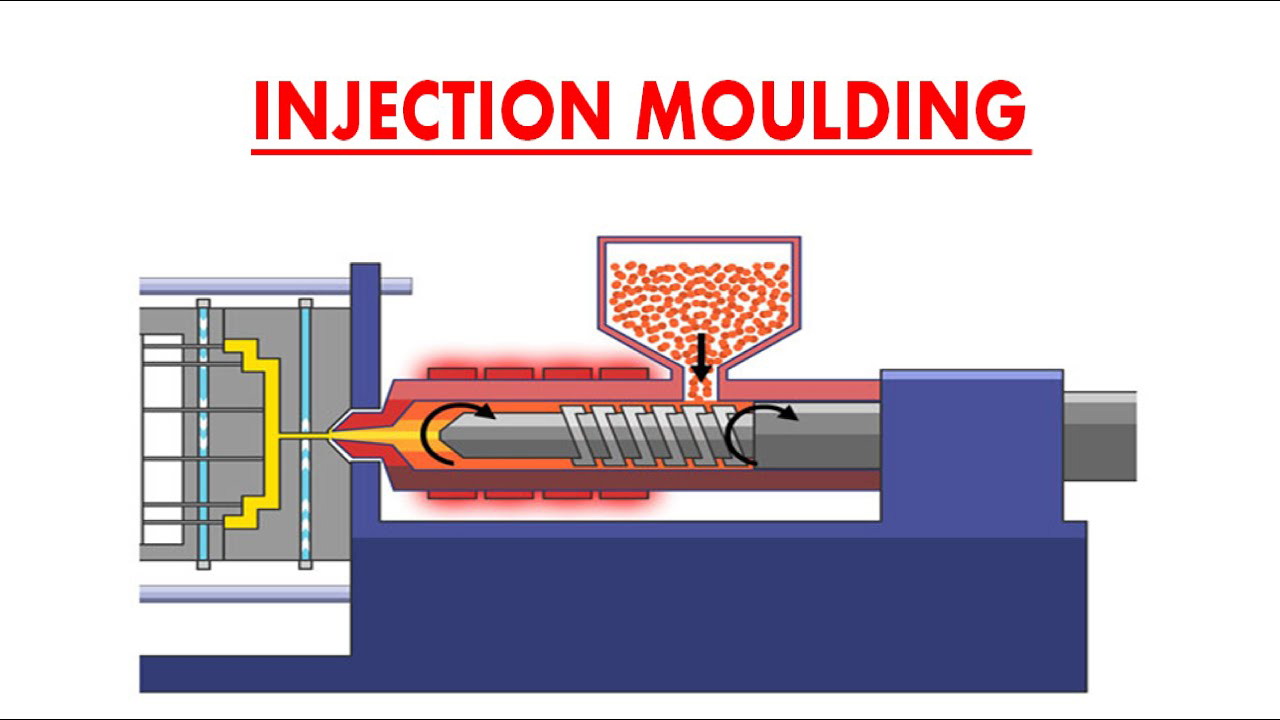
Comment fonctionne le moulage par injection ?
Le processus de moulage par injection peut être décomposé en plusieurs étapes clés :
1. Fabrication du moule
La première étape consiste à créer le moule d'injection proprement dit. Ce moule métallique en deux parties donne la forme que prendra le plastique fondu.
Les moules sont généralement usinés CNC en acier ou en aluminium. Les deux moitiés s'emboîtent pour former la forme de la pièce en plastique une fois qu'elles sont serrées dans la machine de moulage par injection.
2. Serrage
Ensuite, les deux moitiés du moule sont solidement serrées l'une contre l'autre par la machine de moulage par injection. Cette étape essentielle permet d'éviter que le plastique en fusion ne s'écoule entre les deux moitiés du moule lors de la phase d'injection à haute pression.
3. L'injection
Une fois le moule solidement fixé, le processus d'injection peut commencer. L'unité d'injection de la machine de moulage fait fondre les granulés de plastique en utilisant la chaleur et la pression. Elle force ensuite le plastique fondu à pénétrer dans le moule par l'intermédiaire de carottes et de glissières qui acheminent le matériau directement dans les cavités qui forment les pièces moulées.
4. Refroidissement et solidification
Au cours de cette étape, les canaux de refroidissement intégrés dans le moule métallique évacuent la chaleur du plastique fondu, ce qui le solidifie pour lui donner la forme finale de la pièce en plastique. Ce cycle de refroidissement dure généralement entre 15 secondes et une demi-minute avant l'ouverture du moule.
5. L'éjection
Une fois complètement refroidies, les deux moitiés du moule se séparent et des broches métalliques éjectent les pièces plastiques solides du noyau du moule, qui tombent dans un panier ou un convoyeur situé sous la presse d'injection.
Faire mousser, rincer, répéter ! Le moule se referme ensuite, prêt à recevoir la prochaine injection et à entamer un nouveau cycle de moulage.
Et c'est ainsi que vous avez créé une pièce en plastique moulée par injection. Hormis le coût initial de l'outillage du moule usiné, le coût par pièce du moulage par injection est très abordable, ce qui en fait la solution idéale pour les grandes séries.
Maintenant que nous avons abordé les principes de base, examinons quelques principes clés de conception du moulage par injection à suivre et les différents types de processus de moulage par injection.
Les bases de la conception du moulage par injection
La conception correcte des pièces pour le moulage par injection est essentielle pour une production de pièces en plastique sans défaut et rentable.
Voici quelques principes de conception fondamentaux à respecter :
Uniform Wall Stock - S'efforcer de maintenir une épaisseur uniforme dans la mesure du possible. Le passage brusque d'une paroi épaisse à une paroi mince rend les pièces sujettes à des défauts tels que des marques d'enfoncement ou un gauchissement.
Angles d'ébauche - Les surfaces verticales doivent être légèrement coniques pour améliorer l'aptitude au moulage et l'éjection. Un angle de dépouille minimal de 1 degré convient pour les applications générales (0,5 degré pour les broches).
Éviter les contre-dépouilles - Tout détail de surface ou toute géométrie empêchant l'ouverture droite du moule sans mécanisme de glissement augmentera les coûts.
Coins arrondis - Les angles vifs concentrent les tensions dans les pièces en plastique et accélèrent l'usure des moules. Il faut arrondir tous les bords pour améliorer la fluidité et la durabilité.
Renforcement des patrons - Agrandir les diamètres des bossages ou ajouter des goussets chaque fois qu'un filetage ou des fixations sont nécessaires pour la solidité.
Goupilles d'éjection - Placer les broches d'éjection sur les zones intérieures plates de la pièce, en évitant les surfaces extérieures très esthétiques.
Emplacement de la porte - Placer les points d'injection le long du plan de joint sans affecter les surfaces cosmétiques afin de minimiser les travaux de finition.
Types de moulage par injection
Outre le moulage par injection de thermoplastiques standard, il existe également des types de processus de moulage par injection spécialisés, notamment :
Moulage par insertion
Le moulage par insertion combine deux matériaux différents en insérant un composant préformé dans l'outil de moulage par injection avant d'injecter du plastique en fusion autour de lui.
Les inserts courants comprennent des composants métalliques tels que des inserts filetés en laiton permettant de mouler des points de fixation ou d'autres pièces plus performantes.
Moulage à tirs multiples
Le moulage par injection multi-coups permet de produire des pièces en plastique à l'aide de deux ou plusieurs matériaux différents superposés par étapes. Chaque injection de matière a lieu à différents stades du cycle de moulage par injection.
Souvent utilisées pour combiner différents polymères plastiques ou couleurs, les techniques de tir multiple permettent de créer des poignées et des finitions durables, douces au toucher ou ergonomiques.
Surmoulage
Semblable au moulage par injection multiple, le surmoulage relie deux matériaux différents en une seule pièce en plastique, combinant souvent une base en plastique rigide recouverte d'un matériau souple caoutchouté.
Cette technique de surmoulage permet aux pièces d'être à la fois rigides et résistantes aux chocs, ce qui la rend populaire pour les poignées d'outils et de produits de consommation.
Matériaux de moulage par injection
Les ingénieurs peuvent choisir parmi des milliers de matières plastiques pour un moulage par injection adapté aux exigences de l'application.
La plupart d'entre eux se répartissent en deux catégories principales :
Polymères thermoplastiques - Les thermoplastiques, le type le plus courant, comprennent des matériaux tels que acryliqueABS, nylon, polyéthylène et polypropylène. Les thermoplastiques fondent lorsqu'ils sont chauffés et se solidifient lorsqu'ils sont refroidis.
Polymères thermodurcissables - Les thermodurcissables utilisent la chaleur ou des réactions chimiques pour se solidifier et prendre leur forme définitive. Les matériaux thermodurcis les plus courants sont l'époxy, le silicone, le polyuréthane, la résine de polyester et le caoutchouc vulcanisé. Ils ne peuvent pas fondre et se remodeler après la formation initiale.
Au-delà des polymères de base, il existe de nombreuses options de matériaux avancés pour le moulage par injection, notamment :
- Composites - Matériaux renforcés par des fibres ou des particules pour une résistance/rigidité accrue
- Plastiques haute température - Peut résister à des températures supérieures à 500°F pour les applications automobiles
- Polymères conducteurs - Dissipation de l'électricité statique et blindage électromagnétique
- Biopolymères - Matériaux plastiques écologiques à base de plantes
Le choix du matériau optimal qui répond aux exigences en matière de propriétés mécaniques, de température, de compatibilité chimique, de cosmétique et d'autres performances est une première étape essentielle pour obtenir des pièces moulées par injection de qualité.
Principaux avantages du moulage par injection
Maintenant que vous connaissez les bases du processus de moulage par injection, récapitulons quelques-uns des principaux avantages qui en font la méthode de production de masse la plus populaire au monde :
Faible coût - Le prix des pièces de grand volume obtenues par moulage par injection est très abordable.
Vitesses de production élevées - Les cycles de moulage permettent de produire des pièces en quelques secondes
Flexibilité de la conception - Il est possible de réaliser des géométries complexes avec des tolérances serrées
Polyvalence des matériaux - Des milliers d'options de matériaux plastiques pour répondre aux spécifications
Consolidation de l'assemblée - Les pièces peuvent intégrer plusieurs composants et matériel de fixation
Il est clair que pour les industries manufacturières, des dispositifs médicaux aux biens de consommation en passant par l'automobile, le moulage par injection offre une solution efficace, polyvalente et compétitive en termes de coûts pour la production de pièces en plastique.
Conclusion
J'espère que ce guide du débutant vous a fourni des explications utiles sur le moulage par injection. Les étapes de base du processus de moulage par injection sont relativement simples, mais la maîtrise de la conception des pièces en plastique et l'optimisation de la production s'acquièrent au fil des années d'expérience dans le domaine du moulage.
Si vous souhaitez faire fabriquer des pièces en plastique sur mesure, le moulage par injection est l'option la plus viable pour des volumes supérieurs à 1 000 unités. En dessous de cette quantité, l'usinage CNC ou l'impression 3D peuvent s'avérer plus rentables.
Pour résumer, le moulage par injection offre une souplesse de conception, une précision et une valeur inégalées pour la production de composants en plastique à grande échelle. Il mérite à juste titre le titre de cheval de bataille de la production de masse dans le monde entier et dans d'innombrables secteurs.
Avez-vous déjà utilisé le moulage par injection ou débutez-vous ? Je serais curieux d'entendre vos expériences ou vos questions dans les commentaires ci-dessous !