Le moulage par injection est l'un des procédés de fabrication les plus populaires pour les pièces en plastique, des minuscules Legos aux pare-chocs de voiture et aux éléments du tableau de bord. Mais malgré la banalisation de cette technologie, nombreux sont ceux qui ne comprennent pas ce qui se passe une fois que le plastique fondu est injecté dans un moule.
L'un des comportements inhérents au plastique est qu'il se rétracte considérablement lorsqu'il refroidit. Ce rétrécissement n'est pas seulement un changement de dimensions, mais il peut également provoquer des contraintes internes qui conduisent à une augmentation des coûts de production. page de guerreUne déformation de la géométrie ou des dimensions d'une pièce.
La gestion et la réduction du retrait sont des aspects essentiels de la conception et de la fabrication de pièces plastiques complexes qui conservent des tolérances étroites tout au long de la durée de vie d'un produit. Dans ce guide, en tant que professionnel fabricant de moulage par injection de matières plastiquesJe vous expliquerai ce qui cause le retrait du moulage par injection, comment il peut être prédit et contrôlé, et quelles sont les stratégies pour réduire les défauts de vos pièces.
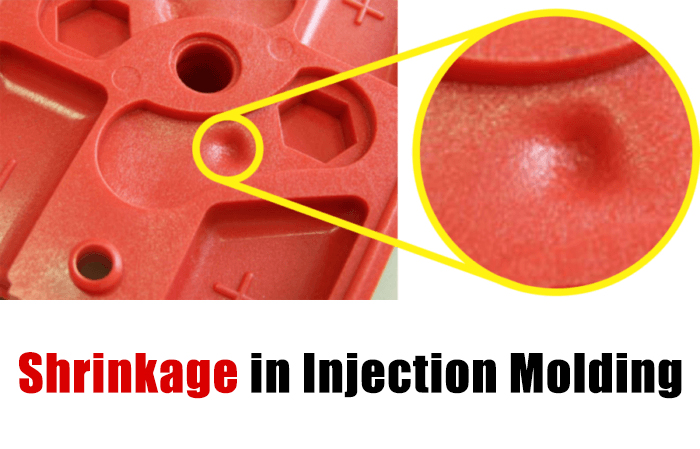
Qu'est-ce que le retrait dans le moulage par injection ?
Le retrait fait référence à la contraction d'un composant moulé en plastique lorsqu'il refroidit après avoir été injecté dans une machine de moulage par injection. En général, les polymères plastiques se contractent entre 2 et 4%, mais ce chiffre peut varier de 0,5% à 10% en fonction du plastique, des additifs de renforcement tels que les fibres de verre, et de détails tels que l'épaisseur de la paroi. Il est impossible d'éliminer complètement le retrait, il faut donc en tenir compte lors de la conception des pièces en plastique.
Dans les cas les plus extrêmes, le rétrécissement irrégulier appelé page de guerre peut déformer les pièces au point qu'elles ne s'ajustent plus dans les tolérances spécifiées. Mais le gauchissement peut apparaître de manière très subtile, sous la forme de légères courbures ou torsions invisibles à l'œil nu ; il est donc fondamental de gérer le retrait par des choix de conception et de traitement.
La dynamique du rétrécissement et son impact dépendent d'une combinaison de facteurs :
- Composition du polymère: La façon dont les molécules réagissent aux changements de température et de pression influence les tendances au rétrécissement directionnel. Les polymères amorphes tels que ABS ont des comportements plus uniformes alors que les plastiques semi-cristallins comme le PE et le PP ont des comportements anisotropes.
- Températures de fusion: Des températures de fusion plus élevées augmentent généralement le retrait en raison de l'expansion des chaînes de polymères.
- Températures des moisissures: Un refroidissement plus rapide augmente les contraintes internes. Les moules plus chauds permettent une plus grande relaxation des molécules avant la congélation.
- Distribution du poids moléculaire: Les polymères de poids élevé ont tendance à rétrécir davantage.
- Présence de produits de remplissage/renforcement: Les fibres limitent le rétrécissement le long de leur orientation. Les charges minérales réduisent le retrait global.
- Facteurs géométriques: Comme l'épaisseur de la paroi, les nervures, etc. Les zones plus épaisses se rétractent davantage que les zones plus fines, ce qui peut entraîner des distorsions.
Pourquoi le plastique rétrécit-il ?
Pour comprendre ce qui provoque le rétrécissement, il est important d'examiner d'abord ce qui arrive aux polymères au niveau moléculaire lorsqu'ils passent par le processus de moulage par injection.
Comportement moléculaire des matières plastiques
Les matières plastiques contiennent de longues chaînes moléculaires d'unités répétées liées entre elles, appelées polymères. Le comportement de ces chaînes - l'ordre dans lequel elles s'agglutinent - détermine si un matériau est amorphe ou semi-cristallin.
Polymères amorphes ont une structure enroulée de manière aléatoire sans aucune organisation répétitive entre les chaînes. Lorsqu'ils sont chauffés, les polymères amorphes forment un liquide fluide, les molécules s'écartant les unes des autres. Le refroidissement permet aux chaînes enchevêtrées de se rapprocher, de se rétrécir et de se solidifier sur place, mais jamais de s'organiser en structures ordonnées.
Plastiques amorphes courants :
- Acrylonitrile butadiène styrène (ABS)
- Polycarbonate (PC)
- Polystyrène (PS)
Plastiques semi-cristallins contiennent des zones où les chaînes moléculaires se rassemblent pour former des régions cristallines ordonnées, tandis que d'autres zones restent amorphes.
Lorsqu'elles sont chauffées, les zones cristallines fondent dans les régions amorphes, mais les molécules continuent à pointer dans les mêmes directions. Lors du refroidissement, les structures cristallines ordonnées se reforment, attirant les molécules dans un volume plus petit - c'est de là que vient le retrait.
Plastiques semi-cristallins courants :
- Polyéthylène (PE)
- Polypropylène (PP)
- Nylon (PA)
Le haut degré d'alignement moléculaire des matériaux semi-cristallins entraîne un retrait perpendiculaire à l'écoulement, tandis que les polymères amorphes se rétractent dans le sens de l'écoulement.
Comment le processus de moulage provoque-t-il le rétrécissement ?
Pour en revenir au moulage par injection, comment les conditions de la machine et du moule conduisent-elles au rétrécissement ?
Lorsque le plastique entre dans un tonneau chauffé, les forces de cisaillement brisent les régions cristallines tandis que le chauffage permet aux chaînes moléculaires de s'étendre, augmentant ainsi le volume libre.
Ensuite, le polymère fondu est poussé à haute pression et à grande vitesse dans une cavité de moule relativement plus froide qui limite le mouvement perpendiculaire à la direction de l'écoulement. Les molécules s'alignent dans le sens de l'écoulement comme des spaghettis dans une buse.
Dans le cas des plastiques semi-cristallins, lorsque la température baisse, des structures ordonnées commencent à se former à nouveau. Les molécules qui se réalignent ont moins de volume libre, ce qui les incite à se resserrer et à rétrécir le plastique.
En outre, des contraintes résiduelles se développent entre le noyau plus chaud et les régions de surface plus froides, retenues par les parois rigides du moule. Les pièces essaieront de relâcher ces contraintes en continuant à refroidir après avoir été éjectées du moule, ce qui risque de provoquer un gauchissement.
Où se produit le rétrécissement ?
La majeure partie du retrait se produit pendant le refroidissement à l'intérieur du moule, bien qu'une plus petite quantité puisse se produire après l'éjection lorsque la température se stabilise complètement.
Le retrait après moulage dépend de plusieurs facteurs :
- Conditions de traitement telles que la vitesse d'injection, la pression et la température
- La rapidité avec laquelle les couches superficielles se solidifient et limitent les mouvements moléculaires
- Niveau des contraintes résiduelles
Par exemple, avec les plastiques amorphes comme le PC et l'ABS, le retrait est plus important à l'extérieur du moule, car les sections intérieures restent fondues plus longtemps, ce qui permet la relaxation des chaînes de polymères. Ou encore, les pièces très fines se solidifient plus rapidement et génèrent moins de contraintes internes.
Prévision et mesure des taux de rétraction
Chaque matière plastique se rétracte différemment dans diverses conditions. La première étape pour comprendre comment une pièce peut se déformer consiste donc à déterminer avec précision les taux de rétrécissement.
Le retrait est mesuré en pourcentage de variation des dimensions de la pièce moulée par injection par rapport au moule en acier à outils : Retrait (%) = (Dimension du moule - Dimension de la pièce) / Dimension du moule x 100
La plupart des fabricants de résines plastiques fournissent des données sur le retrait dans les fiches techniques des matériaux, mais l'idéal est de procéder à des essais en fonction de vos paramètres de production exacts. Les valeurs de retrait typiques se situent entre :
- Polymères amorphes: 0.3-0.7%
- Plastiques semi-cristallins: Autour de 2%
N'oubliez pas que les détails de la transformation influencent le retrait d'un plastique donné. Les modifications de la vitesse d'injection, de la température, de la pression et autres peuvent toutes avoir un impact sur le taux de rétrécissement.
Comment les logiciels de simulation prédisent les taux de rétrécissement
Des logiciels de simulation spécialisés peuvent modéliser le processus de moulage par injection pour une conception de pièce plastique spécifique afin de prévoir des comportements tels que le retrait. Ils fonctionnent en reproduisant numériquement des facteurs tels que :
- Propriétés rhéologiques du plastique
- Performances de la machine de moulage
- Températures, vitesses, pressions
- Géométrie de la pièce
Les ingénieurs peuvent ainsi visualiser les tendances au rétrécissement et les risques de gauchissement de leur conception. Ils peuvent ainsi procéder à des ajustements avant de s'engager dans un outillage de moulage coûteux.
La simulation permet également de déterminer le meilleur compromis entre les propriétés nécessaires à la fonctionnalité et les défauts de distorsion dus au retrait. Les changements peuvent impliquer une modification de la géométrie, de l'emplacement des points d'injection, voire des opérations secondaires.
Comment contrôler le retrait du moulage par injection ?
Il est pratiquement impossible d'éliminer complètement le retrait des plastiques. Toutefois, grâce à des décisions intentionnelles en matière de conception et de processus, il est possible de le minimiser suffisamment pour fabriquer des pièces fonctionnelles et robustes sur le plan dimensionnel.
Stratégies de réduction de la rétraction du plastique
Voici quelques stratégies de bonnes pratiques utilisées pour réduire les défauts de rétraction :
1. Bien équilibrer le remplissage, l'emballage et le refroidissement
Remplissage trop rapide - Favorise l'alignement des molécules et risque de provoquer un retrait anisotrope.
Emballage inadéquat - Les sections internes de la pièce s'effondrent de manière imprévisible une fois éjectées.
Refroidissement trop rapide - Provoque un rétrécissement variable entre les zones épaisses et minces, ce qui entraîne un gauchissement.
2. Augmentation de la température du moule
Permet la relaxation des chaînes de polymères avant la solidification complète, réduisant ainsi les contraintes internes. La température idéale se situe souvent entre 30 et 50 °C en dessous de la température de fusion.
3. Utilisation de systèmes à canaux chauds
Les canaux chauds maintiennent les carottes et les canaux en fusion, éliminant ainsi les bouchons froids, ce qui réduit la longueur du flux et permet d'optimiser les sections des pièces.
4. Ajout de fibres de verre
A environ 30% de coupure en poids, les fibres empêchent la rétraction en fournissant un renforcement. Bien qu'elles réduisent la résistance aux chocs.
5. Inclure un système d'évacuation des moisissures adéquat
L'aération empêche l'air d'être piégé dans la cavité pendant le remplissage, ce qui favorise un remplissage complet pour un retrait uniforme.
6. Utilisation du moulage par injection assistée par gaz
Du gaz comprimé est injecté dans la cavité, poussant le matériau contre les parois, ce qui améliore la reproduction et la précision des dimensions. La pression entraîne la rétraction dans de petits canaux creux prévus à cet effet.
7. Suremballage des zones à forte rétraction
En règle générale, les zones situées dans le sens inverse du flux subissent un rétrécissement plus important car les molécules se détendent. Ce phénomène peut être compensé par un tassement intentionnellement plus important.
Règles de conception pour minimiser les rétrécissements irréguliers
La conception de géométries de pièces appropriées contribue énormément à la stabilité, car le plastique se contracte lors du refroidissement. Voici quelques lignes directrices de conception qui permettent de réduire le retrait inégal :
- L'épaisseur totale de la paroi doit être aussi faible que possible pour assurer une résistance adéquate. Les zones épaisses subissent un retrait plus important que les zones minces.
- La variation de l'épaisseur de la paroi d'une pièce à l'autre est limitée, ce qui permet d'obtenir des sections uniformes. Les changements soudains provoquent une rétraction préférentielle qui déforme les zones plus minces.
- Y compris des angles de tirage appropriés sur les parois verticales, permettant une contraction uniforme lors de l'éjection et évitant le collage.
- Positionner les lignes de soudage et de fusion à l'écart des zones d'apparence ou de tolérance élevées. Ces zones sont intrinsèquement sujettes à un retrait irrégulier.
- L'utilisation de nervures ou de structures d'appui avec des détails de profilés minces uniquement lorsque cela est nécessaire permet de gérer l'encombrement. Les nervures permettent de limiter les contractions différentielles sur des parois plus grandes, mais ajoutent une masse supplémentaire si cela n'est pas nécessaire.