Injection molding is a popular manufacturing technique widely used to create high-volume plastic parts with complex designs and specifications. But how exactly does this process work? As a professional plastic injection molding manufacturer, I will help you to find it out.
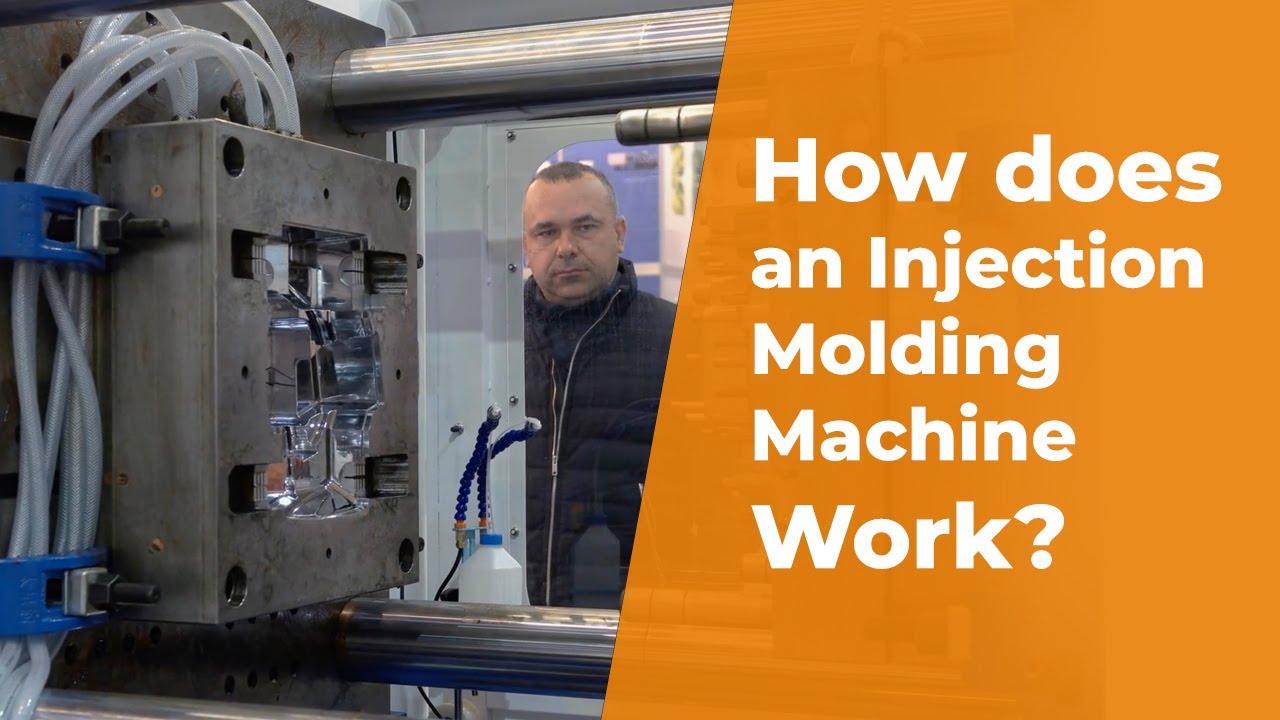
What is injection molding?
Injection molding is a manufacturing method for producing plastic parts through a cyclic process. Pre-weighed plastic material in granular form is melted and injected under high pressure into a metal mold to give it the desired shape. Once the molten plastic solidifies and cools inside the mold, the end product is a net-shaped thermoplastic part that meets design specifications.
The high-precision tooling used is called an injection mold – it gives the plastic its unique shape and must be designed specifically for each product. The mold consists of two main parts – cavity and core, along with components like cooling lines, ejector pins, etc. When closed together under pressure, they form the mold cavity into which molten plastic is injected during the molding process.
Understanding the injection molding process
The injection molding process can be broken down into four fundamental steps:
- Clamping
- Injection
- Cooling
- Ejection
Step 1: Clamping
During clamping, the mold halves are securely closed by the clamping unit to prevent leakage of material when the molten plastic is injected at high pressure.
Hydraulic, mechanical or hydraulic-mechanical clamping systems provide the needed force to keep the mold securely shut until the molten plastic inside has cooled down and solidified fully. Sufficient clamping tonnage ensures tight closure along the parting lines of the mold tool.
Step 2: Injection
With the mold shut and ready, the injection phase begins. Here, the desired type of plastic material usually in pelletized form is gravity fed from a hopper into the injection molding machine’s heated barrel.
Inside the barrel sits a long screw that turns to melt, mix and gather the plastic, thanks to conductive and mechanical heating induced by its rotation. The molten plastic then gets injected at high pressure through the nozzle and into mold gates, runners and cavities until all spaces are filled.
The speed and pressure need to be adequately maintained during the injection stroke to ensure all empty spaces inside the mold (sprues, runners, cavities, etc.) get filled without getting clogged.
Step 3: Cooling
During cooling, the molten plastic material gradually solidifies into the desired finished shape by dissipating heat through cooling channels in the mold. This cooling period is necessary before opening the mold plates to reveal the end plastic part.
Water or oil-based liquids are circulated through cooling lines surrounding each cavity to help remove heat from the hot molten plastic inside it. The cooling setup needs proper tuning to ensure sufficient cooling without freezing or deforming the components.
Step 4: Ejection
In the final step, once adequately cooled down, the mold opens and gets separated into cavity and core sides using ejector pins. This lets the completely solidified plastic parts get ejected out conveniently.
Any residual plastic left in the mold runners known as runners is also removed from the tooling in this step. The finished injection molded parts can have some finishing appearance defects, so post processing like trimming by CNC may be needed.
And the cyclic process begins again starting from the clamping phase!
How injection molding machines work
Sophisticated injection molding machines are needed to execute this fundamental process precisely and repeatedly for mass manufacture of plastic components.
Such dedicated units have three main sections:
- Clamping unit
Houses mold holding platens to keep mold tooling closed and aligned before/ during injection.
- Injection unit
Melts plastic resin and injects molten polymer into cavities through high temperature and pressure.
- Mold
Shaped tooling kept between platens having impression of part’s negative relief details.
Advanced programmable process controllers finely control various processing parameters like heating, screw RPM, hydraulics, etc. This allows tuning characteristics like plasticizing rate, shot sizes, injection profiles and pressures precisely.
Such automation makes injection molding highly repeatable for mass production while maintaining strict quality control of complex precision plastic parts.
Common materials used
While several materials work for injection molding, some common ones include ABS, acrylic, nylon, polycarbonate and polypropylene. Each has unique properties that make it suitable for certain applications.
ABS – Acrylonitrile Butadiene Styrene has high impact strength combined with toughness, rigidity and thermal stability. Appliances, automotive interiors and consumer products extensively use ABS injection molding.
Polycarbonate – With unmatched transparency and heat/impact resistance polycarbonate suits applications needing such resilience. From bulletproof glass panels to medical supplies and CDs rely on molded polycarbonate parts.
Nylon – From excellent strength-to-weight ratio to natural lubricity, abrasion resistance and chemical inertness make nylon a frequent choice for molding. Gears, cams, bearings, specialty plumbing/automotive fixtures often get made via nylon injection molding.
And many more – PBT, POM, acrylic PMMA, HDPE, LDPE, PP, PS, PPS, PEEK, etc.
Key design considerations
Several critical design rules need consideration to make injection moldable parts manufacturable with efficiency:
Consistent wall thickness – Varying wall thickness leads to uneven shrinkage causing warpage and sink marks. Maintaining near uniform thickness yields consistent cooling.
Generous radiused corners – Sharp 90-degree corners negatively impact material flow. Large fillets improve fill while ensuring adequate strength.
Draft on vertical faces – Even marginal draft facilitates part ejection after the injection molding process without deforming part surfaces.
Unrestricted core pulls – Side cores, slides need their movement axis to permit clean retractions without obstruction.
Such design considerations lead to faster cycles, dimensional stability concerns reduction and longer mold/ component lifespan through reduced wear and tear.
FAQs
How are plastic pellets melted during injection molding?
Inside the injection molding machine barrel, plastic pellets feed into the rotating screw. Through conductive heating from the metal barrel and its shearing actions, the plastic resin gradually softens, melts and accumulates in front of the non-return valve as a shot.
What provides the pressure during injection molding?
Accumulated molten plastic in front of the screw gets forced into the mold cavity through hydraulic injection pressure acting on the screw coupled with non-return valve closure. This allows molten plastic injection without backflow.
Why is cooling time critical for injection molding?
Adequate cooling time ensures proper solidification of injected molten plastic held inside mold cavities before opening the tool. Insufficient cooling causes permanent deformation on ejection due to residual material softness.
How many types of injection molding exist today?
Several variants of injection molding cater to specialty niche applications – multi-material molding, over-molding, insert molding, gas-assisted molding are some continually evolving techniques.
The future of injection molding
While already a versatile technique for polymer processing, injection molding continues to evolve in sophistication. With advancing automation, machines get increasingly precise exceeding tight tolerances holding consistency across million-part runs. By incorporating sensors and interconnected data systems, smart networks optimize crucial processing parameters in real-time. Leveraging such self-refining injection molding 4.0 ecosystems will push part dimensional accuracies into nanometer regime!
Conclusion
So in summary, injection molding forms the backbone for mass manufacture of precision plastic parts across various sectors. This cyclic manufacturing method relies on sophisticated mold tooling into which molten thermoplastics inject under high pressure. Upon cooling and solidification, complex plastic parts eject out completing the molding process.
With stringent processing controls and adherence to design considerations high consistency across huge volumes, precision and automation get achieved in injection molding. This versatile, high-performance manufacturing technique thus keeps gaining relevance making improved products accessible globally!